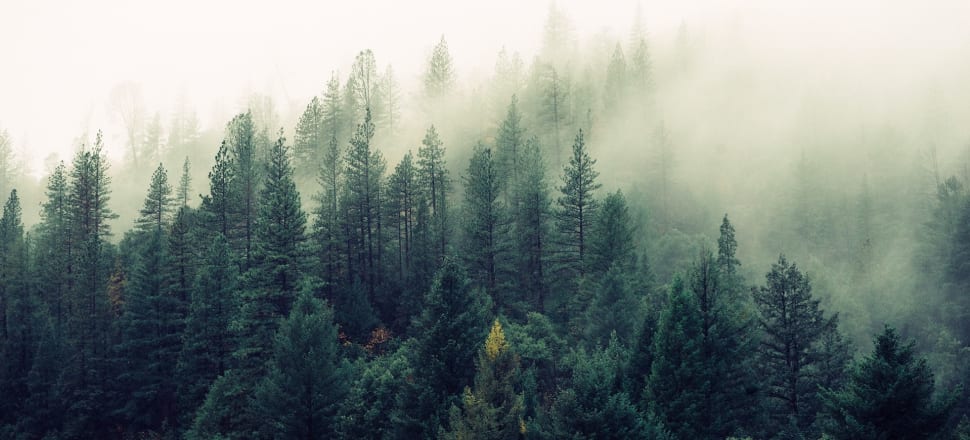
Futurity sees forestry waste as a promising source of high-value, sustainable chemicals.
Bio-refinery start-up Futurity is launching a $1.5 million commercialisation study into turning wood by-products into high-value chemicals.
The study will involve working to commercialise technology developed in Europe to turn lignin waste from Oji’s pulp and paper mills into replacements for traditionally fossil fuel-based materials used in automotive, electronics and construction.
Ministry for Primary Industries is putting in $600,000 from its Sustainable Food and Fibre Futures Fund towards the pilot, with Futurity, owned by co-founder and chairman Rupert Paterson’s venture capital firm Prospectors, putting up the remainder.
Chief executive Jacob Kohn said the enzyme technology it was looking to import from Finnish company MetGen Oy was currently operating at pilot scale rather than the commercialisation Futurity was looking to do.
READ MORE: * What $500m could do for climate and cost of living * Converting waste to environmentally conscious walls * ‘The more you know about waste, the less you sleep at night’
The tech works by breaking down the lignin into different sizes which are then separated with filtration units into three sizes with different properties.
“The real difference is that even a lot of what's going on in Europe at the moment is focused on domestic markets for consumption," said Kohn.
“We've got a unique opportunity in New Zealand because of our geographic location being in close proximity to Asia Pacific, that we can focus on those markets and collectively, APEC as the largest consumer of chemicals in the world.”
Target areas
A key market the business wants to zone in on is the phenolic resins used as glue in plywood, MDF and other engineered wood products as well as electronics, semiconductors and brake pads.
Another is the “polyol component” of polyurethane foams, which have applications in insulation, packaging, aviation and more.
The third key market is packaging, where Futurity's tech could replace petrochemical sizing agents in cardboard that provide water resistance and strength properties.
When the company started investigating markets over three years ago, it looked at 50 to 100 different potential applications before settling on the above targets after preliminary works.
“The reason we've landed on those is both because we've been able to demonstrate performance parity or advantages and we’ve also been able to demonstrate that we can either match the cost or provide a cost saver,” Kohn said.
Earlier works, which will stack up to $3.5m by the end of this year, had also looked at applications of cellulose, another building block of wood, but saw the most potential in lignin.
The company wants to revisit cellulose and hemicellulose down the line to enable it to utilise the whole tree.
Kohn said the value added to the input materials could be anywhere from 10 times to 50 times depending on the application.
The pilot study is expected to wrap up next year.
“At that point, we would hope to be in a position where we have some secured offtake with customers, and that's fundamental for us to justify progressing towards investment in the next stage.
“We've got very strong interest from customers and are highly engaged in the process of validating these products and working to identify where our markets are.
“But it's more about taking that from research and development and piloting into actual documentation of secured offtake that's bankable.”
The next stage is getting engineering and design work together to build a fully-fledged facility/facilities.
Carbon impact
Futurity is still working out carbon-saving calculations, but expects it to work out far better for the planet.
“Fundamentally it's biogenically sourced versus fossil, and it’s a biological process which is less intense than a lot of chemical pressure conversion technologies used to refine petrochemicals," Kohn said.
“It's also about the end-of-life infrastructure and with the appropriate end-of-life as utilised, it should have significant benefits from a carbon standpoint.”
The plant functions similarly to wine, beer or dairy production, requiring stainless steel tanks, filtration units, an energy supply, a laboratory and an office.
It has been designed as an engineering package that can be installed at mills such as Oji’s facilities in Kawarau and Kinleith to tap into the waste stream.