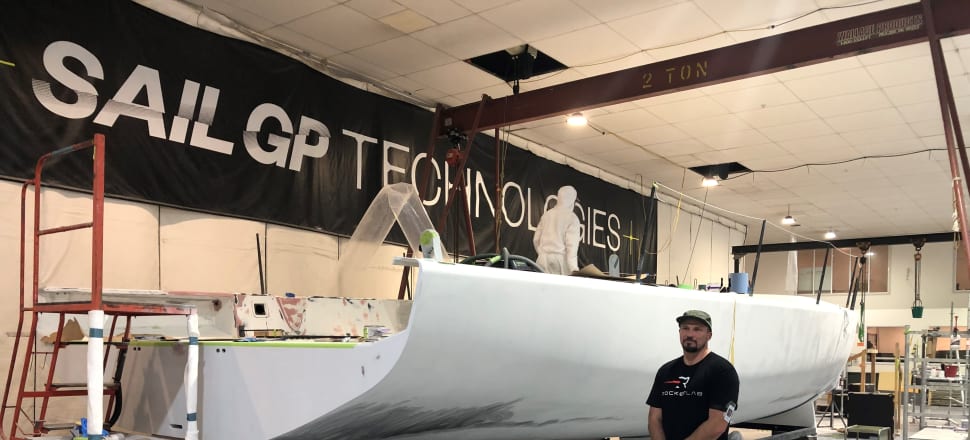
It used to make high-performance boats that went like rockets, but now Warkworth's big manufacturer is switching to actual rockets
Garry Clark has made war ships, superyachts, hovercraft, and sonar domes.
Only last week he and his workmates were building hi-tech racing boats.
Now, in a simple shed inside a shed in the same Warkworth factory north of Auckland, the leading hand composite technician is building a rocket.
"Rocket Lab taking over? Best thing that can happen to us, it's fantastic news," says Clark. "It's long-term employment, you've got exciting projects to work on, it's perfect."
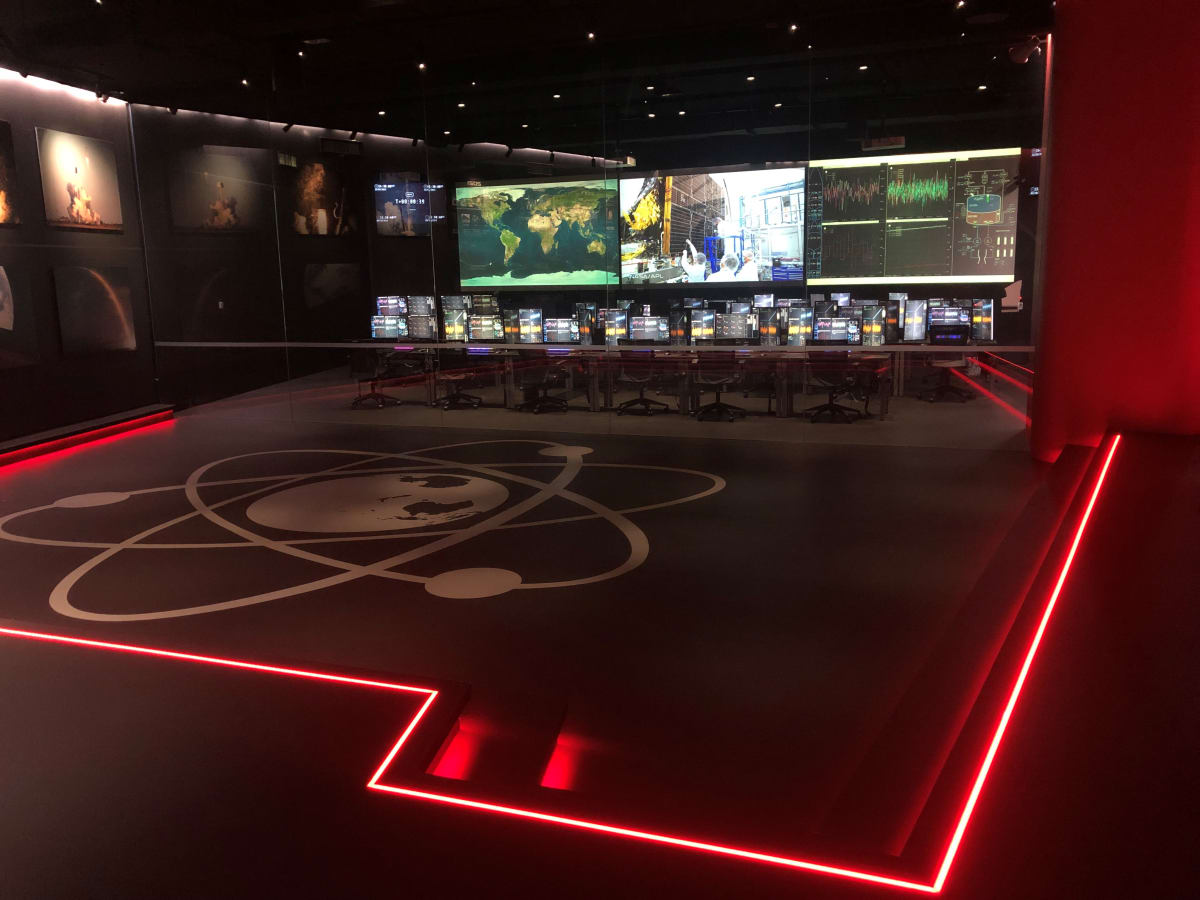
It's all come about after Sir Russell Coutts sold his SailGP Technologies racing boat manufacturing complex to Rocket Lab, shifting his operation to the northern hemisphere to be closer to the racing events.
With the complex comes all the hi-tech composite machinery – and more than 50 workers with specialised skills in building with carbon composites.
The Detail takes a tour of the 6,500 square metre site in Warkworth as it makes the speedy transition from boat building to rocket building, and we go inside Rocket Lab's Auckland plant to see how they make and fit tens of thousands of components to a rocket.
Both the hi-tech, high-performance industries use these super strong but ultra light carbon composites. The two firms already had a relationship as the Warkworth factory was making some carbon composite materials for Rocket Lab before the deal.
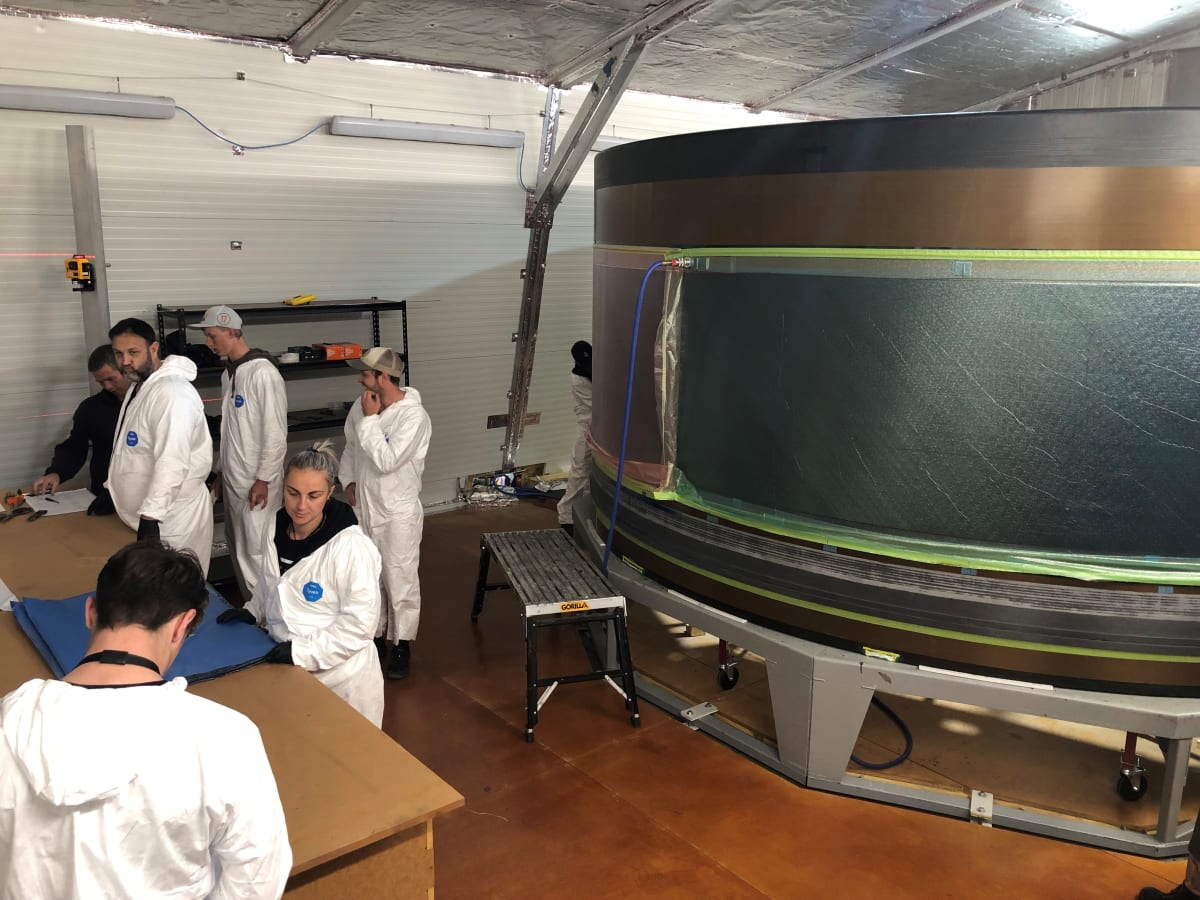
Ben Malcolm, who is in charge of the carbon composite production for the new big rocket Neutron, says being able to retain SailGP's skilled staff has helped the team – and hopefully helped the community too.
"This is the next level, this is the next step," says Malcolm. "No one can deny that the scale of the vehicle, the scale of what we're trying to achieve here, is pretty up there with anything that's been done in the industry in New Zealand."
At the Warkworth plant, a large SailGP banner is draped on the wall next to the last boat being built there – and there are other remnants of the marine industry.
"There's a lot to be said about keeping the Kiwi boatyard," says Malcolm, who helped build Team New Zealand boats before joining Rocket Lab. "To be honest, that's at the heart of the composite structures at Rocket Lab.
"The same industry has fed our team so we've supported and also been supported by the composites industry and a lot of that is founded in the marine industry."
Most of the Warkworth team had worked on America's Cup boats, then SailGP's F50 catamarans, and are used to working to tight deadlines for yacht racing, Malcolm says. Their experience translates well to working on research and development of the Neutron, with its expected launch date just around the corner in 2024.
The factory floor in Warkworth is a stark contrast to Rocket Lab's security-conscious Auckland site, with its all-black reception area giving a view of the control room. The space is also lit by billboards telling the story of the company: started by Kiwi space entrepreneur Peter Beck in 2006, and now listed on the Nasdaq stock exchange in the US, employing 1,700 people here and in the States, and launching missions every month.
Behind it is a special room where visitors can watch their rockets taking off, if they're not at the New Zealand launch site at Mahia.
"It is quite an emotional time for some of them. We have had some of them working up to 15 years on something that takes a few minutes to get to space."
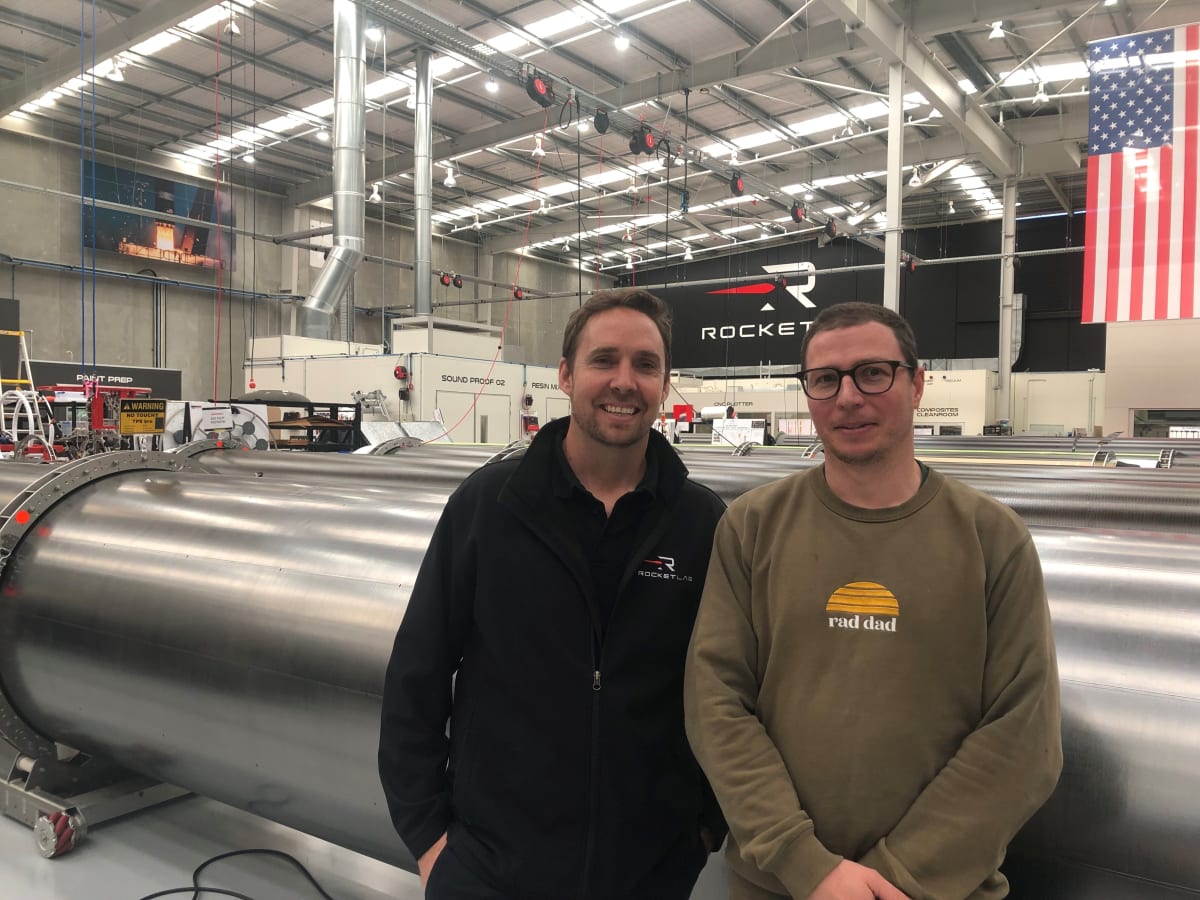
Two huge flags – one NZ and one US – hang over the thousands of rocket parts on the factory floor. So pristine and tightly managed is this space that even the tiniest tool has its place on a board and must be accounted for.
Several "vehicles" are on the production line for customers, who range from private businesses putting up satellites to take photos of Earth, to government agencies working on climate change research, to defence agencies.
Malcolm shows The Detail the finished rocket at the end of the production, but photos are banned.
"You're seeing nearly everything here," he says. "This is going to space, you're seeing the engine, you're seeing the batteries."
But an image can too easily wind up on the internet and get scrutinised.
"You have some very smart people out there who can reverse engineer this."
Check out how to listen to and follow The Detail here.
You can also stay up-to-date by liking us on Facebook or following us on Twitter.