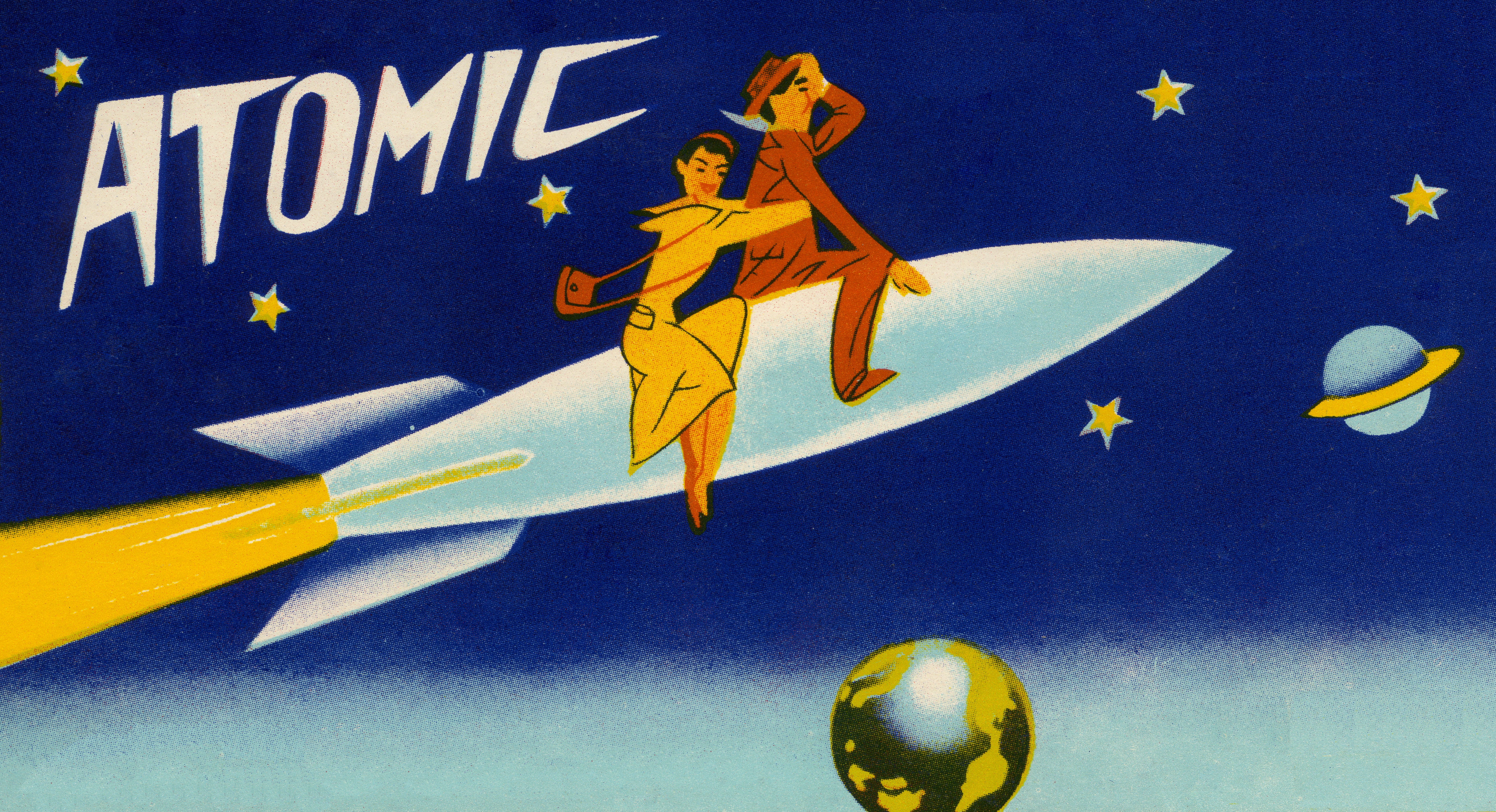
You may recall the old universal solvent problem: There’s an old problem in chemical solvents: a solvent that dissolves anything isn’t easy to bottle up. High-performance metallurgy faces a similar problem: You use heat to forge metal alloys to build powerful rocket engines and nuclear reactors, but these applications produce extreme amounts of heat that can degrade those alloys.
Finding ways to produce materials that can remain strong under extreme conditions is key to advancing power and propulsion technologies for both terrestrial and celestial use.
NASA researchers may have found a revolutionary method to do just that. By combining metal alloys with ceramic particles using 3D printing technology, they produced a new material that in one test proved more than 600 times as resistant to stress and heat than existing high-performance metal alloys.
The alloy, GRX-810, which is described in a new paper published Wednesday in the journal Nature, could find use in rocket nozzles and even nuclear fission or fusion reactors, and moreover, could signal an era of rapid advancement in materials science.
“It took us a while to convince ourselves that these results were real,” Tim Smith, a research materials engineer at NASA’s Glenn Research Center tells Inverse. “We understood then that, you know, something had changed, And we made an alloy that we were very excited about.”
Harder, hotter, and more resistant
GRX-810 is made primarily of nickel, cobalt, and chrome, but it is laced with nanoscale particles of a ceramic oxide called yttrium, yielding an “oxide-dispersion-strengthened” (ODS) alloy. It’s long been known that incorporating such materials into metal alloys can enhance their strength, ductility, and hardness.
“You even have better irradiation properties,” he says. “So applications that are higher radiation environments, fission or fusion reactors, things like that, will all benefit by having these oxides dispersed in it.”
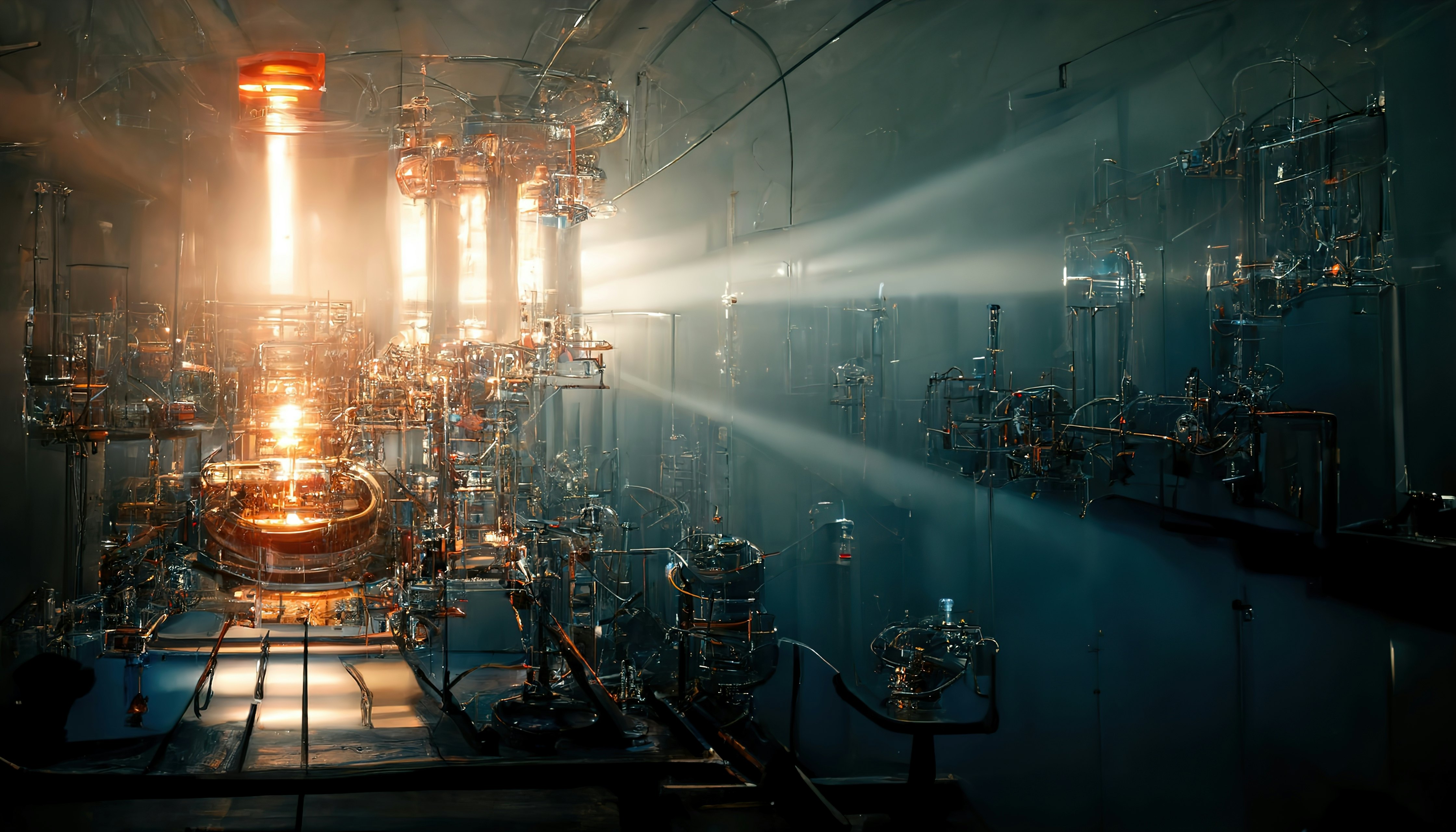
NASA and others explored alloys similar to GRX-810 in the past, according to Smith, but it was a combination of the specific elements and the use of additive manufacturing — 3D printing — that gave GRX-810 such outstanding properties compared to existing alloys.
The primary gauge of alloy strength used in the study is known as a “creep test.” This involves placing the test material in a high-temperature environment and then putting a static load, a weight or pressure, on the material and waiting to see how long it takes the material to break.
In the study, Smith and his colleagues tested GRX-810 against existing high-performance alloys in a creep test set at 2,000 degrees Fahrenheit with a load of up to 3,000 pounds per square inch. The best of those existing alloys lasted up to about 10 hours in the creep test. GRX-810 lasted 6,500 hours, “which is somewhere around eight, nine months,” he says.
Testing your metal
NASA researched creating ODS alloys all the way back in the 1970s and 1980s, according to Smith, but the manufacturing technologies of the time ran into fundamental challenges.
“If you melt metal, these ceramic oxide particles are a lot lighter and have a higher melting temperature. And so they immediately just float to the top of the molten metal,” he says. “So you can't just sprinkle some oxide into a metal and there you go.”
But 3D printing offers an alternative. What Smith and his colleagues realized is they could create a metallic powder made of nickel, cobalt, and chrome particles of just 10 to 45 micrometers in diameter, and then coat them with an even finer powder of yttrium oxide, particles of around 200 nanometers in diameter.
They then feed the coated powder into a powder bed 3D printer.
“What it does is it puts down a layer of that metal powder, and it hits that layer with a laser and consolidates that powder in a certain pattern that you want,” Smith says. Then the plate moves down a few microns, it spreads more powder, and you hit it again.”
In this way, a plate of GRX-810 can be built up over time, the metal alloy evenly laced with the oxides particles when examined with a scanning electron microscope. The resulting crystal structure of the alloy also closely matched computer modeling the research team used to identify the type of alloy and the crystal structure necessary for the properties they hoped to achieve, vindicating their design process as well as the manufacturing technique.
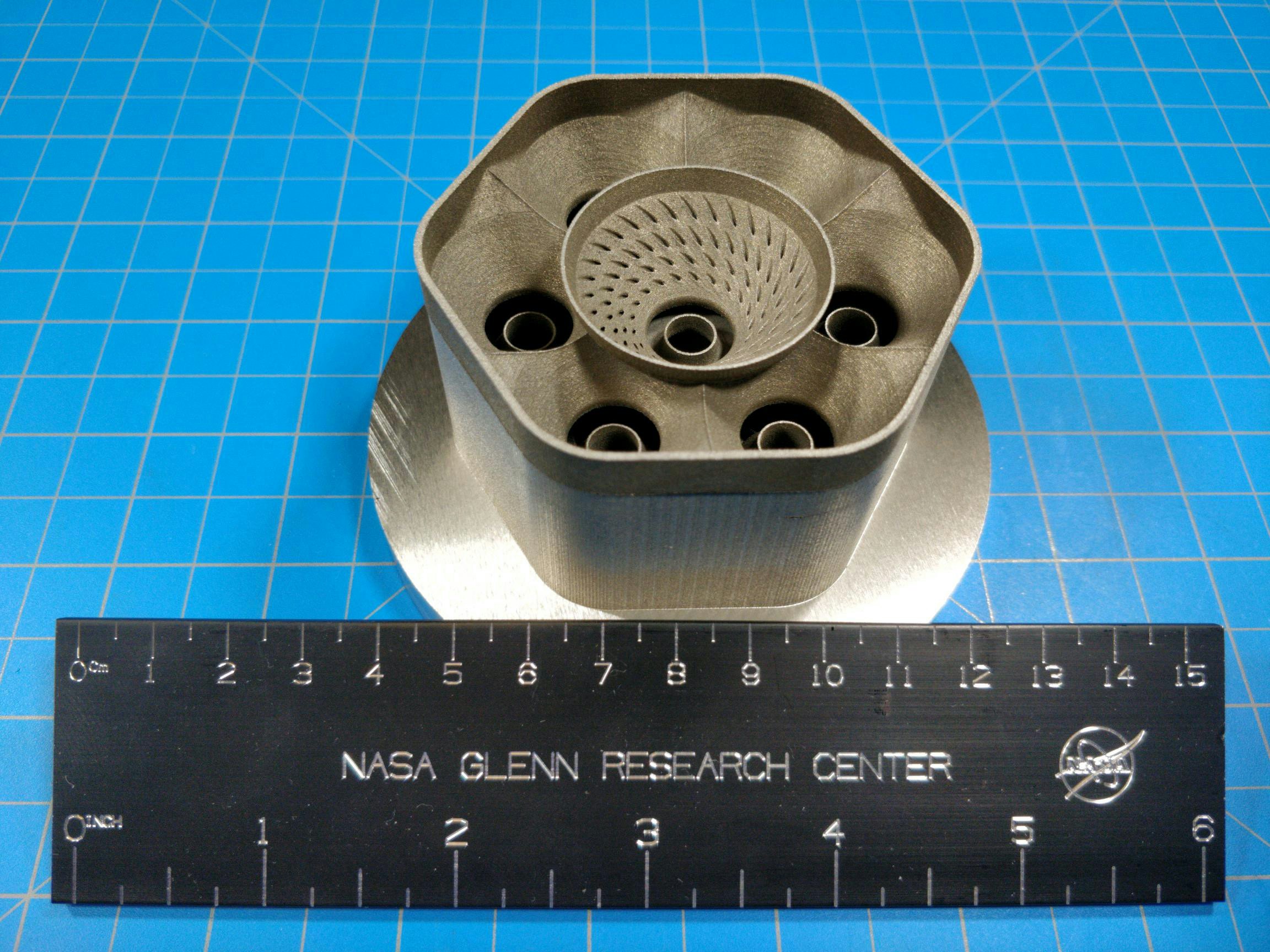
New materials and extreme environments
While it’s still early research, Smith believes GRX-810 can be 3D printed on larger machines to produce components that could replace existing materials in rocket engines and power sources.
“Things where you need to be able to survive really extreme environments under tough conditions for as long as possible,” he says. “GRX-810 is, I think, the perfect alloy for all those applications.”
That could be a boon for the work NASA is conducting along with DARPA to construct nuclear thermal rocket engines, which use a nuclear fission reactor rather than chemical combustion to produce thrust. Used in space, nuclear thermal rockets can be much more efficient than chemical rockets, and could power faster journeys to Mars and beyond. Crucially, the efficiency of a nuclear thernal rocket engine is directly related to how hot you can run the reactor.
Smith and his colleagues' next step is to continue studying the GRX-810 manufacturing process and learn how to scale it up so it can be introduced to industry as soon as possible. But in the long term, he’s very interested to see what other new materials can be created using the same techniques. GRX-810 may be only the beginning.
“Now there is a potential that we can start producing superior aluminum alloys, titanium alloys, copper alloys,” he says. “I'm excited to see what new properties can be made with it.”