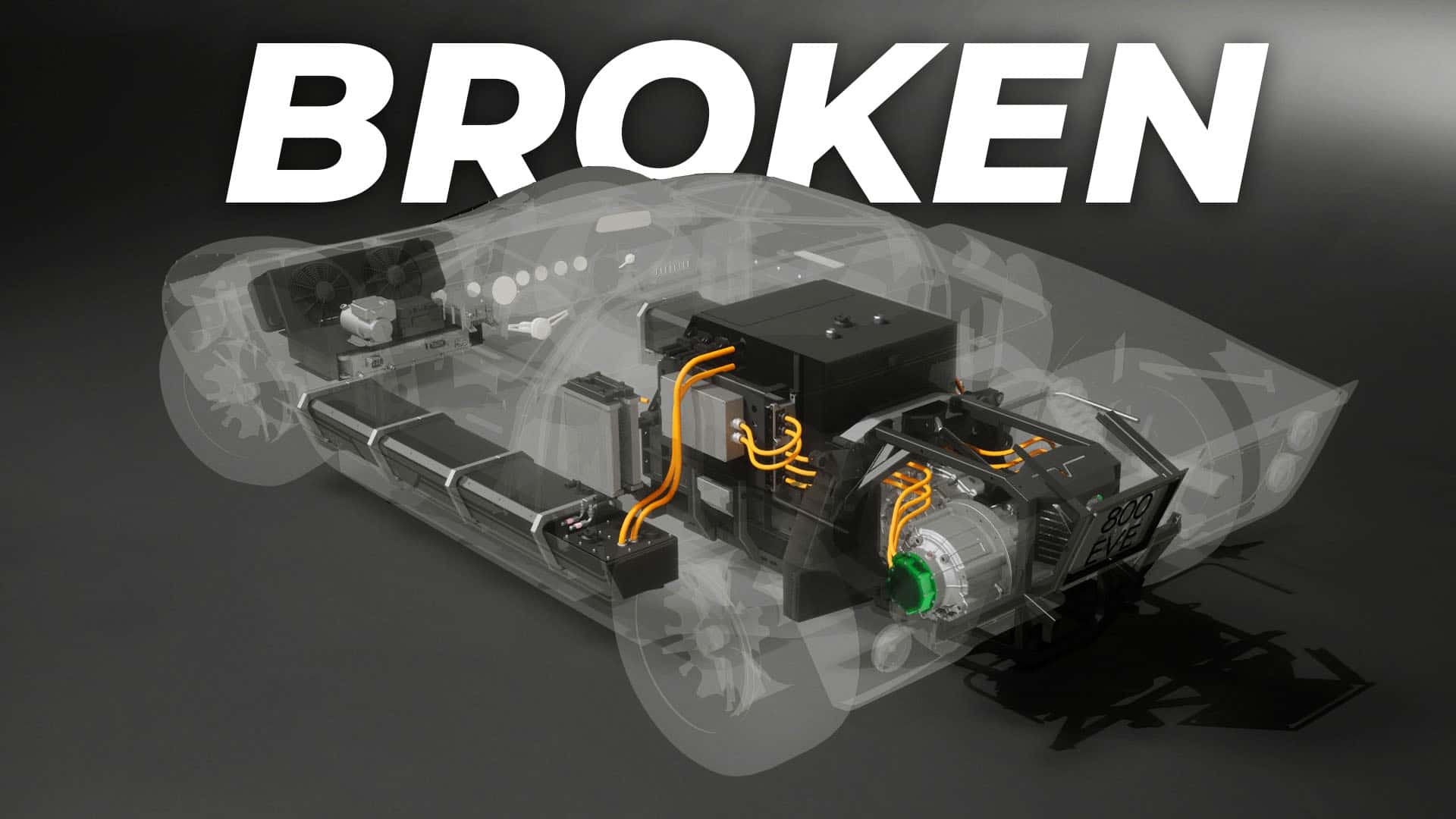
Eric Kriss was one of America’s early electric-vehicle tinkerers. During the EV swap's Wild West era in the late 2000s, Kriss sourced battery cells from an alleged Chinese hybrid-electric submarine surplus, and swapped the components into his 1969 Saab Sonnet and 1955 Porsche 356 Speedster.
“This was early days, 2008, 2009,” Kriss told me. “[The Chinese Navy] couldn’t use as many [cells] as [its suppliers] were making, so they allowed these companies to export.” It’s a far cry from 2024, when mainstream automakers are building massive factories stateside to produce millions of automotive-grade cells.
Removing a combustion engine in favor of an electric drivetrain was difficult way back then and it still is today. Even with a growing swath of off-the-shelf parts intended for automobiles, the amount of money and brainpower required to complete a clean electric build is immense. As such, shops are forced to demand top dollar for their creations, and hobbyists face a landscape where the fundamentals of EV swaps are ever-changing.
An industry-wide push toward EVs with more range, creature comforts, and fast charging has led to increased costs, curb weights, and complexity. That means many enthusiasts—including people like Kriss who favored light, simple vehicles for this very reason—are left with few affordable options to power their projects.
Kriss’s niche – swapping electric motors into light, simple old sports cars – is the sort that makes a lot of sense for hobbyists. His machines use a small quantity of air-cooled batteries stacked up in the hood and trunk of their respective donor cars. The final energy capacity isn’t extreme, but neither is the power necessary to propel the cars. For reference, his 356 had a post-conversion curb weight of just 2,009 lbs. With the mainstream development of increasingly lightweight and energy-dense cells, it’s plausible Kriss's simple concept could be taken much further. EV buyers on showroom floors, however, aren't after simplicity.
Far from those scruffy early days, many EV swaps are no longer hobby-tier projects driven by sheer excitement and curiosity. Rather, a preponderance of expensive, boutique EV shops dominate the scene. They cater only to a monied, environmentally conscious few.
Professional Conversions
ECD Automotive Design of Florida builds high-end ICE- and EV-swapped vintage British cars. The newest electric drivetrain ECD offers is refined, easy to use, and chugs electrons from public DC fast chargers like Electrify America’s. The builder’s electric E-Types start at $299,995.
ECD’s Owner, Elliot Humble, doesn’t mince words about the complexity of his cars.
“I don't think our [latest setup] is really for the average mechanic at home,” Humble says. It takes a team of professionals to integrate and tune the drivetrain for use by an average driver, to the point where each car is basically a one-off.
“At the moment, for your normal home mechanic, I would throw in an LS3.”
ECD’s first-gen system used old Tesla Model S battery modules and a Tesla motor, which are widely available. Humble thinks this kind of setup would be possible to put together at home and indeed many do. However, sourcing these parts is expensive and rarely straightforward.

That’s not to mention the danger of working with high-voltage electricity, which ECD technicians were trained to mitigate.
“It was pretty intimidating,” Humble said of the foray into EV building. “I was never a big fan of standing there [and] making the final connection to the battery.”
ECD is therefore very careful about its electric builds, which require patience, a clear mind, and a steady hand.

To address the added weight typical of such conversions, ECD sticks to cars that were heavy to begin with. Humble’s company only EV swaps Series III versions of the Jaguar E-Type, for instance, removing their massive, emissions-choked iron-block V12s in favor of a 42.0-kilowatt hour battery, 400-volt inverter, and a gear-reduced motor. The swapped cars often end up lighter, and with a superior weight distribution than stock. ECD’s vintage Land Rover Defender conversions, meanwhile, make the already heavy truck only slightly heavier – around the weight of an extra passenger.
Other companies and individuals are more ambitious, though, putting electric drivetrains into vintage lightweights. Kriss’s builds worked nicely because his classics didn’t require much energy to move, and the lithium-iron-phosphate batteries he utilized don’t necessarily require a complex management system to avoid catastrophic thermal runaway, unlike other lithium chemistries. The forklift-sourced inverters Kriss found were simple, relatively low voltage, and reasonably inexpensive.
Despite the mishmash of components, the dynamic capabilities and straight-line performance of these cars are considerably increased, perhaps to levels they weren’t suited for.
“You get these things up above 90, 95 miles per hour and the front starts to lift up… the steering gets very light, and you kind of wonder what the hell you’re doing,” Kriss laughed.
Despite the sketchy handling characteristics found beyond the cars’ performance envelope, Kriss’s creations even have a reasonable range of around 150 miles. Not bad for batteries supposedly meant for submarines.
Few take this bare-bones approach anymore. The light car, small-battery formula falls apart once things like heat, air conditioning, and other amenities begin skimming battery power.
Some view that hurdle as a tantalizing challenge.
Everrati, a UK company, recently created an electric Porsche 911 RSR reproduction, built from the bones of a less-desirable narrow-body automatic model. Despite not being a legitimate example of the one-of-51 air-cooled RSRs, the project is controversial.
“We would never touch an original RSR,” Everrati’s CEO, Justin Lunny, told Motor1. He also thinks that converting ”kind of unloved” vehicles to electric power might give them a new appeal.
The company is launching a “certain type of Jaguar” this year that was never a favorite among enthusiasts. He wouldn't say which car or why it’s less desirable, but from his perspective, it could “open up a whole new era” for some vehicles, especially those that were originally unreliable or underpowered.
Needless to say though, the company’s builds are still breathtakingly pricey.
“It’s not for everybody. It’s cost-prohibitive for most people, actually.” Lunny describes his products as aimed at the “ultra-wealthy.”
Wrenched Beyond Recognition
High price isn’t the only downside to converting your classic to an EV. All permanent-magnet-motor-based electric vehicles – by far the most common today – have the same horsepower and torque curve, just at various magnitudes. In other words, they behave identically when you put your foot down. This has led to accusations that post-conversion cars aren’t really the same vehicle in spirit. More or less, they’re a faceless EV cosplaying as a vintage car.
Lunny understands this criticism.
“We don’t just buy a motor or a battery. We have our own entire control architectures… we can tune that car to feel pretty much like it should,” he says. Lunny cites his company’s Land Rover conversions as an example.
“Our Series 2A Land Rovers, the originals did 0-60 miles per hour in about 24 seconds. We’ve intentionally got it down, but only to about 13.” He says accelerating any faster would be uncharacteristic of the car in its original form. He also thinks that if Land Rover could have achieved that type of performance in-period, it probably would have.
“For us, it’s all about being appropriate.”
The work that companies like ECD and Everrati are doing is impressive. Everrati builds bespoke battery packs for each of its vehicles from raw cells supplied directly by massive companies like CALB. It even produces custom drive units with bespoke gear reductions and motors straight from mainstream automotive suppliers, which is almost unheard of in the EV restomod space.
Each vehicle receives a unique solution to the packaging problems it presents. Cars like the company’s GT40 reproduction are fitted with banks of batteries in the sills next to the driver and passenger. Packs like this in a custom form factor are not easy to pull off, and it’s the result of painstaking effort from engineers who were formerly employed by the likes of McLaren, Rimac, Bentley, and Lotus.
That’s the shame with EV powertrain swaps as they sit. The work these restomod companies do with EVs is not only very impressive, but extremely interesting. The cost means that only a wealthy few can enjoy them.
Individual Struggles
This revelation discouraged Eric Kriss to the point where he sold the two cars he converted to electric power. When he started, EV swaps were something skilled hobbyists could do at a cost comparable to a regular engine swap (although with considerably more trouble). It didn’t matter if his vehicles went without a heater or traction control, Kriss never planned to sell them en masse. Once electric cars went mainstream, though, the excitement gradually left him.
“I began to feel that the fun part of doing this yourself was getting harder and harder and much more expensive,” Kriss said, noting that the creative, innovative work that was once shared freely within a close-knit community of tinkerers was now being done inside companies like Tesla, behind closed doors.
A curiosity that could’ve birthed the next hot-rodding scene was cut down in its infancy. And while the conversion community today isn’t dead, it’s in a tough spot, stuck in a rut that requires high costs, high levels of expertise, or both to escape.
Adam Grosser, a tech entrepreneur and electrical engineer, recently converted a Series III Jaguar E-Type to electric, like ECD does. His immense skill and adequate funding for the project – it was built as a gift for a wealthy friend – made the endeavor possible. Grosser humorously calls the entire project “a very ill-considered decision,” citing its eventual cost and extreme complexity. “All in, there’s probably $200,000 worth of hard costs in this car,” which includes restoring the Jaguar to better than factory condition.
Even with the costs aside, Grosser doesn’t think refined and daily-drivable EV swaps are within the reach of an average home mechanic or enthusiast. Details like powering lower voltage accessories, making brakes work without a source of manifold vacuum, and limiting torque to protect what remains of the factory drivetrain are tough issues to crack. That’s also just the tip of the iceberg.
“I don’t think this is for the faint of heart. I really don’t.” Grosser tells Motor1. “Do I think this will get easier? I do.” By nature of the problem, though, it’s hard to know when that will happen.
He also doesn’t think EV swaps should be the new default. “I’m building a new ‘69 Camaro for myself,” Grosser says. “Everybody is like ‘Oh, is it gonna be electric?’ No.”
Cars like the ‘74 E-Type he converted had “the worst of everything,” so swapping out the anemic and heavy V-12 for batteries and motors was hardly a crime. The car even ended up 35 pounds lighter than it was before, echoing ECD’s results.
However, Grosser thinks many classic cars need to stay true to their original forms.
“For this Camaro? I’m putting in a Gen V LT1 [V8] and a Tremec six-speed. An electric conversion just doesn’t make any sense to me there.”
Hobbyists Grind On
At a surface level, it seems not much work is being done to develop electric drivetrains outside of OEMs. The opposite is true, but avoiding the high costs of off-the-shelf components requires an extreme level of expertise.
Without an inverter, a practical electric vehicle cannot function. The inverter turns DC current from the battery into three-phase AC, which most electric motors use to spin. Think of it like a carburetor or fuel injection system in a combustion-engined car, a critical component in the process of turning raw, potential energy into motion. Designing these devices is extremely difficult, and the few options oriented toward amateurs are expensive as complete units. Only a select few brilliant tinkerers have been able to design open-source inverters or create devices that interface with existing hardware.
One such tinkerer is Benjamin Vedder, an engineer whose VESC line of devices is relatively easy to use out of the box. They are also relatively cheap (most under $500) when built by third-party companies. They only operate at 100 volts or less, though, which makes them effectively unsuitable for full-sized EVs, which typically operate between 400 volts and 1000 volts.
The OpenInverter project, created by a very bright team of engineers led by Johannes Hübner, is the closest thing to an affordable aftermarket inverter for hobbyists. It piggybacks existing traction hardware from automakers to create an open-source high-voltage device without breaking the bank.
Like many others interested in electric vehicles, Hübner found DIY options limited. He attempted to design his own inverters from scratch – he has a background designing high-power solar inverters –but found the better option was the comparatively simple task of creating a control board that plugs right into the existing hardware of vehicles like the Nissan Leaf, BMW i3, or Tesla's S and X models.
However, Hübner’s control boards are not complete devices intended for your average home mechanic. The boards cost less than $400, but you must source an inverter, learn how electric motors are controlled, and solder some components yourself. That’s not to mention the peripheral knowledge required, such as the understanding of CAN, which is essential to completing most refined EV projects.
A video made by one of Hübner’s colleagues, Damien Maguire, details the process of setting up one OpenInverter device on a Tesla Model S/X small drive unit. It takes nearly an hour and a half just to cover the basics.
Hübner wants to make his creations more user-friendly and easier to set up, but he’s limited by the supply of used inverters and his own free time. Short of starting a full-fledged inverter manufacturing operation, open-sourcing is his best option.
Other "fancy" companies, which Hübner did not explicitly mention by name, even use his technology in the products they sell as their own. Not only does that hint at the challenges associated with ground-up inverter design, but at the rarified quality of the knowledge he and his associates possess.
Like others, Hübner doesn’t gloss over the associated dangers, either. Working with the amount of power needed to propel a car means he’s seen “pieces of [solid] aluminum get vaporized.” High-voltage electricity must be treated with respect, something that’s often incompatible with the kind of rough-and-ready budget builds many are interested in.
The Bottom Line
The very nature of EVs makes them difficult to sort for home mechanics and experienced tinkerers alike. Power in an EV isn’t just a liquid fuel that has to be sent somewhere and burned. The battery pack, charger, inverter, and motor are all individual systems that require high levels of expertise to understand, integrate, and use effectively. An error installing any of these individual sub-assemblies often means destroying them, or severely damaging them beyond repair.
Off-the-shelf parts to make an electric swap a breeze simply don't exist at a reasonable price. And the best entities to develop and sell these systems – the automakers – are too wrapped up in their own EV rollouts to produce plug-and-play kits at a reasonable volume and cost for enthusiasts.
With no big players stepping up, it’s down to dedicated engineers like Hübner and his colleagues, or high-end builders like ECD and Everrati to pass the torch. While electric versions of 911s, Mini Coopers, and Jaguars may sound appealing and provocative, they aren't anywhere close to mainstream. The everyday enthusiast is losing the battle for the electric project car; The EV swap needs a hero.
Photo Credit: Eric Kriss, Everrati, ECD Automotive Design, Johannes Hübner