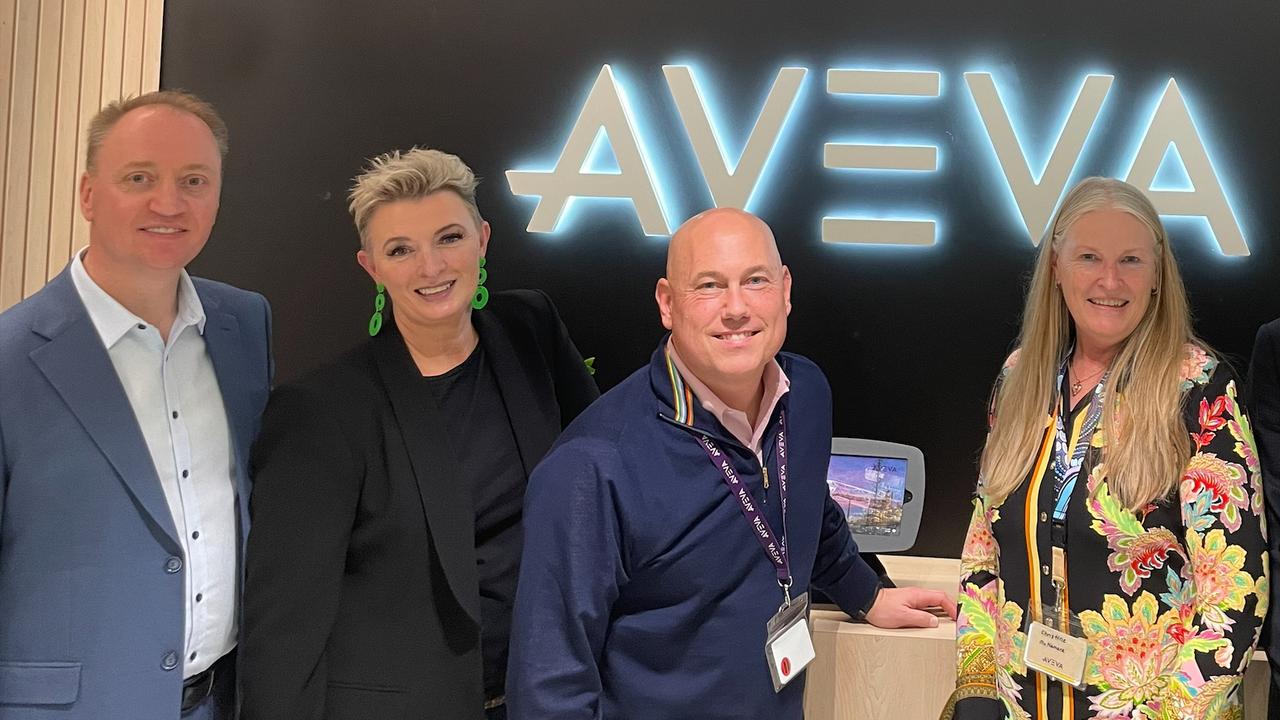
Calibrating settings for the perfect slice of bread, spotting water leaks in pipelines or learning to run a power plant while wearing a headset all depend on industrial intelligence.
Artificial intelligence and analytics can also be used to prevent blackouts by spotting potentially catastrophic problems in turbines or detecting methane plumes that would otherwise blow climate targets.
"If you're going to put a target out there, you need trusted data to back it up to prove you're achieving these targets," Aveva chief product officer Rob McGreevy told AAP during a visit to Australia.
"It can be used to solve sustainability problems. Effective use of water, gas, electricity is super important because industry is the largest consumer of these resources."
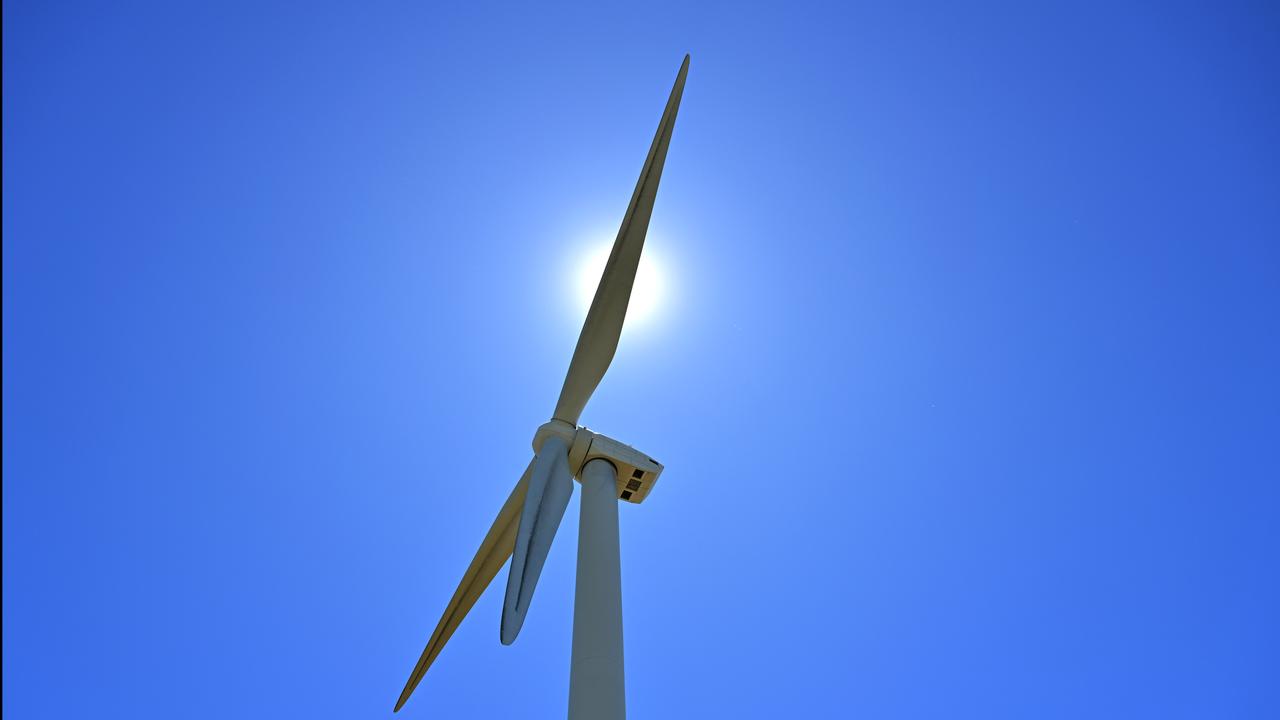
Companies are under pressure to provide more detailed reporting to meet regulatory, investor and consumer demands.
Working with some of Australia's largest companies, British information technology firm Aveva said a 30 per cent reduction in water use or halving power bills can also avoid hundreds of millions of dollars in costs.
"Profitability splits two ways - profitable for the planet and profitable for the company ... I don't think there's any shame in accommodating and winning both ways," he said.
"Nearly every manufacturer I see around the world has an interest in sustainability."
He said industrial engineering technology can spark improvements in quality on a baking production line or plasterboard factory by monitoring and adjusting to temperature and humidity.
People who have been doing jobs for a lifetime are heading for retirement and that expertise can be digitised and support the next generation of workers who already live in a virtual world and rely on chatbots.
"Gamification of of industrial training is going to become more popular in coming decades because the next generation are just different in how they explore and digest technology," Mr McGreevy said.
The concept of a "digital twin" - literally a digital model of an actual production line or power plant - is also taking hold for the design, maintenance and improvement of equipment.
When designing a soft drink bottling plant, for example, a smarter design can be achieved by feeding in tougher parameters for water use.
Once a machine or turbine is built, desktop industrial warriors can look at how fast it is operating and how much energy is it using or producing.
Previously "data blind", AGL Energy uses a system to reduce fuel consumption and emissions, which translates to savings of millions of dollars per year.
The electricity generator and retailer's real time data system guru David Bartolo centralised the group data from all operational sites.
It could connect to any one of their controllers, harvest every piece of real-time data and make it available to every person at AGL.
Monitoring trends in small hydro units located 700km away, one worker figured out why his machines were tripping and sent on-site subcontractors to the source of the problem.
An engineer built a display to capture how two solar farm sites were performing. Chemists set alarms to add years to the lives of boiler-cycle assets. Other users built screens to monitor generator temperatures.
Back in 2017, an outage that could have cost up to $70 million in damage was prevented when the team discovered they were mere days from a number of coils catching fire.
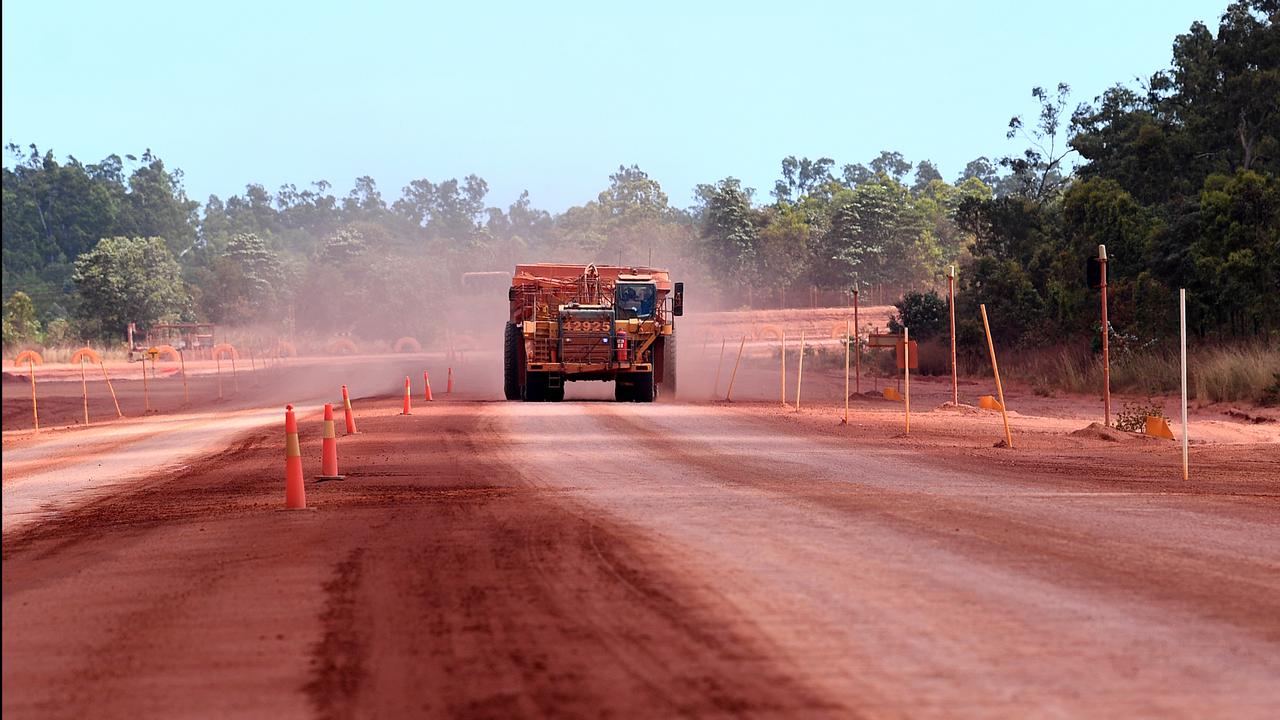
Australia's mining industry, already years ahead on operating equipment from control rooms hundreds of kilometres from sites, also has one of the world's most advanced communities of software developers.
Talison Lithium uses high-tech tools at the world's largest hard-rock lithium mine Greenbushes, located in Western Australia, to locate bottlenecks and make improvements in processing.
Its processing operations include a plant that produces lithium concentrates used in batteries and pharmaceuticals, and a plant that produces highly refined lithium for use in glass, ceramic, and metal alloys.
By identifying and analysing small downtime events that kept repeating, Talison said it could build up a clear view of daily and weekly performance and identify where they were losing production.
Rio Tinto, a leader in iron ore, copper and aluminium, is also a technology company and uses a dashboard or screen known as a human machine interface to control machinery.
At their most technologically advanced mine, Gudai-Darri in WA's remote Pilbara region, the entire truck fleet is directed by controllers sitting almost 1500km away in Perth.