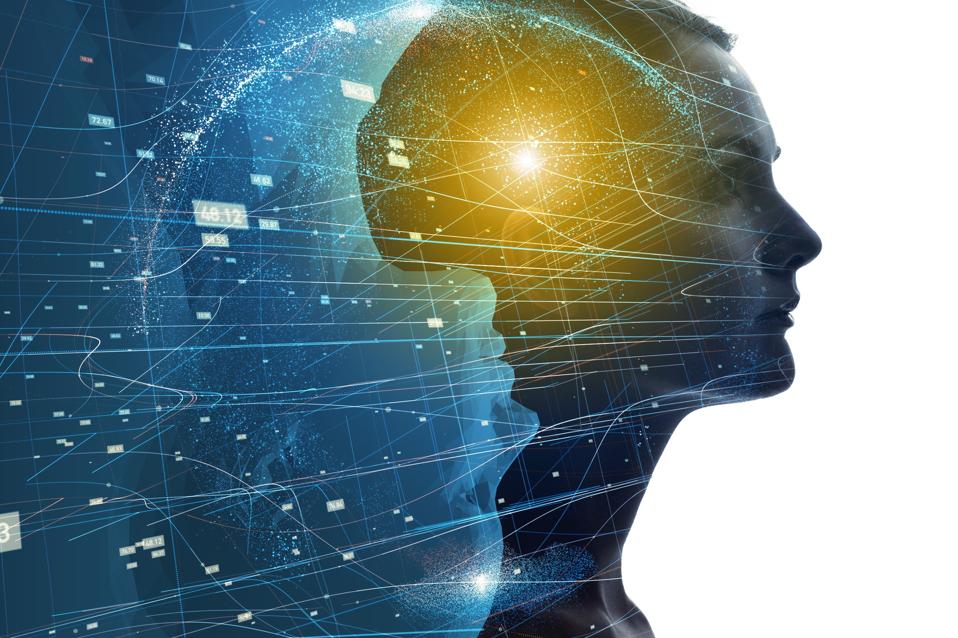
The rise of new competitive automotive companies and the recent pandemic are driving new and more agile development processes in automobile design and manufacturing. These new agile processes are also helping automobile companies acclimate to the semiconductor challenges brought on by global forces that hobbled automobile production in 2021 and into 2022. This article is based upon a recent white paper looking at changes in how automobiles are designed and built and why this will drive demand for digital storage and memory.
Auto companies adopting agile processes soonest, best and most effectively will be at a distinct, measurable competitive advantage for three reasons: 1) they use parts more in tune with mainstream semiconductor products; 2) they work faster, with more processes happening simultaneously; and 3) their earlier execution can lower costs and increase profitability.
With these changes and the requirement for more and more automotive electronics enabling advanced driving features, infotainment and the growth in production of electric vehicles, the demand for digital storage and memory is increasing. Indeed, the lines of supporting software code in automobiles already outstrips the amount of code in a fighter jet, laptops and social media sites, and is expected to continue to grow dramatically, as shown below.
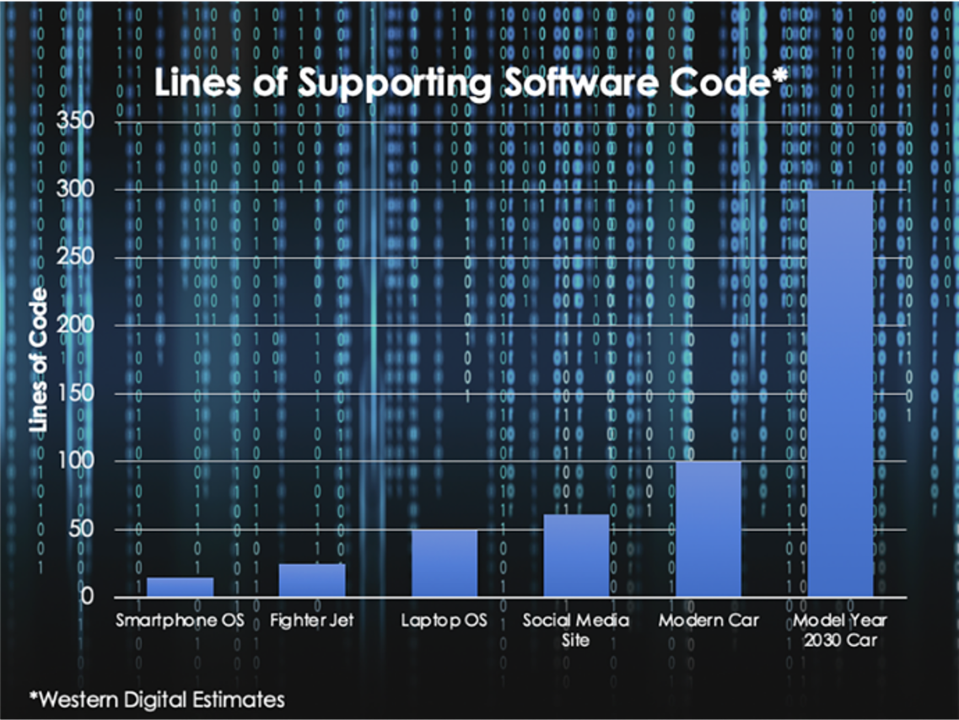
Traditional automotive companies have worked to reduce the development times for new cars for many years. With competitors increasingly using the fast development time of cutting-edge semiconductors as a model for automotive development, the pressure to reduce development time and implement new technologies into the automotive industry has accelerated.
There is a huge push to move to electrical vehicles (EVs) that will drive the electronic content in vehicles to much higher levels than in the past. EVs will require expected lifetimes similar to conventional cars and much greater than many mass-market consumer devices. This may require new hardware architectures that are modular, blade- or cartridge-based, allowing for upgrading hardware to enable longer overall vehicle life.
Moving some vehicle functions from strict hardware control to software control will be an important element to enable some replacement of hardware, including semiconductors, while maintaining vehicle functionality. This could provide more component sourcing flexibility and the avoidance of future automotive semiconductor shortages. Modularizing hardware upgrades will also help to keep vehicles up to date through their lifespan.
New design methodologies such as digital twins can allow some virtual vehicle testing and reduce the dependence upon physical product testing and allow moving to a more parallel design approach for automotive systems. This plus the move to more software-defined vehicle functions, modularized systems and a shift to semiconductor lithography processes that match those of mass production semiconductor products will help to speed the development of automobiles and provide a path towards the long lifetimes consumers expect from vehicle investments.
Among U.S. light vehicle production, memory ICs and sensors will be among the top seven highest volume automotive semiconductor categories with over one billion units used annually by 2030, according to S&P Global Mobility, formerly the automotive team at IHS Markit. It is estimated that, in 2020, seven percent of automotive semiconductor devices were memory and storage, according to a 2019 U.S. International Trade Commission Executive Briefing.
To store the information from these sensors and other electronic functions for AI processing and other uses, S&P Global Mobility forecasts a 28.4 percent cumulative annual growth rate (CAGR) in memory ICs (LPDDR, DRAM and NAND flash) in the 10-18nm segment, resulting in 1.2 billion memory ICs shipped in 2031 for U.S. light vehicle production.
But the solid-state storage favored in vehicles have characteristics that need to be considered in the design of automobiles, in order to enable a long life. Without planning ahead when vehicle systems are being designed, a car could end up wearing out the storage in an ADAS, or an eCockpit, or infotainment system, before the car’s life is over.
According to Russ Ruben, Director of Technical Segment Marketing at Western Digital, automotive designers need to “know…that the endurance of the storage device depends on the amount of data written (measured in terabytes) and varies based on the capacity of storage. Every device has a limit, so it is important to determine the data write requirements based on real system workloads over the lifetime of the vehicle.”
Ruben continues to say that, “Understanding the future workloads of software-based vehicles is becoming a bigger challenge for hardware engineers. They need to plan for unforeseen scenarios requiring more capacity for software updates as well as how the updated software will read and write to the storage devices.”
With cross-functional teams working together between the automotive design and the storage and memory providers, problems such as not enough storage capacity for future developments and storage wear out can be anticipated and avoided.
Leading semiconductor and storage companies are helping to bring new vehicles to market in a more efficient and effective manner. They are helping to optimize the industry’s success with innovations such digital twin technology that manage the vehicle over its lifecycle, right-sizing storage to match the lifetime of the car, and adopting more parallel workflows in testing and certification.