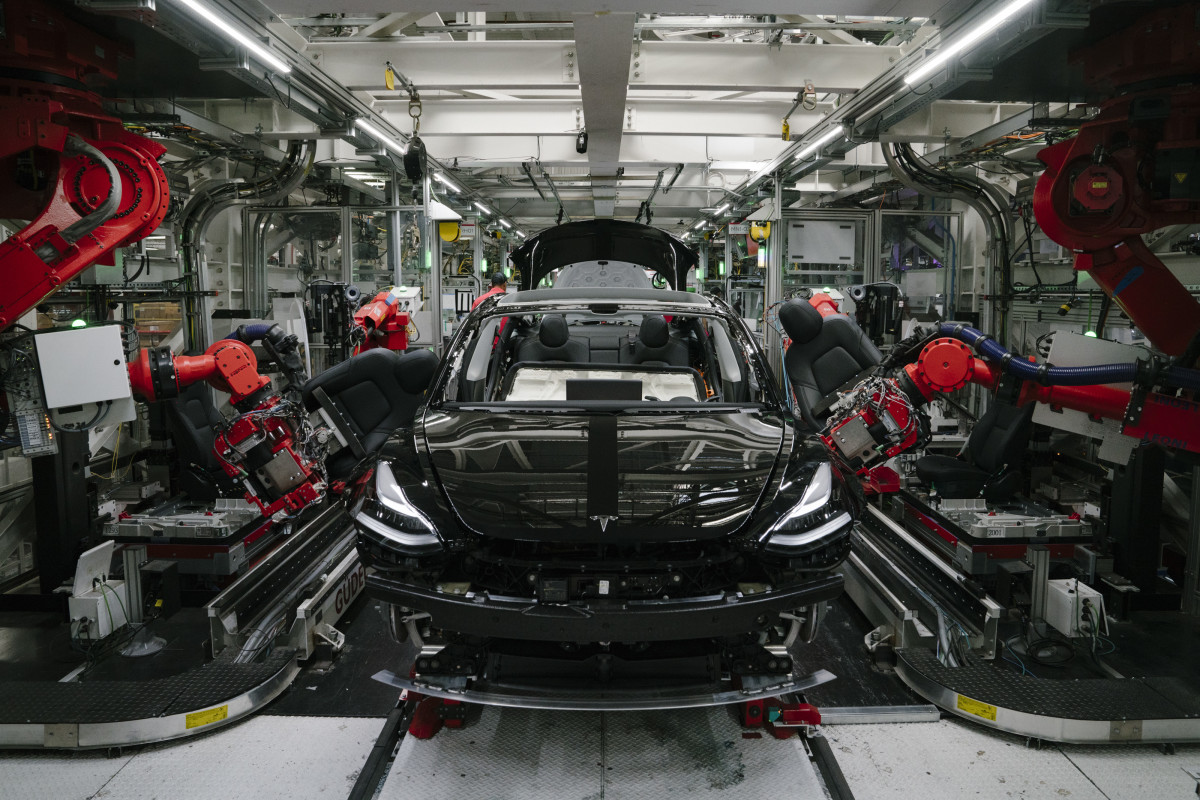
Against the backdrop of an apparent softening in the electric vehicle demand curve, Toyota TM said last month that fully electric vehicles are just not ready yet for mass adoption. The carmaker for years has been touting the value of hybrids, which serve as an important stepping stone to total electrification without the range anxiety that comes part-in-parcel with fully electric cars.
The focus on hybrids, however, doesn't mean that Toyota isn't interested in dominating the EV sector as well. The Japanese automaker, which in 2022 became the world's top-selling carmaker for the third year running, has been claiming big wins in battery tech innovation for months.
Last week, the company announced an $8 billion investment in a U.S.-based battery plant. Still, the company's standard production method is likely not up to scratch when compared to EV leader Tesla TSLA.
Related: Toyota has an important warning for electric vehicle enthusiasts
Tesla pioneered a production method called "gigacasting," something the company has been leveraging since 2020. Where traditional car manufacturing involves the welding together of hundreds of separate parts, gigacasting creates high-pressure molds which can then be assembled much more quickly.
Shanghai's Gigafactory produces a car once every 40 seconds, the company said in July.
Other automakers, struggling to be competitive in EVs, while also chasing profitability, are already keen on the new technique. Volvo will soon start using casting to help produce its third generation of EVs. General Motors GM said this year that the automaker is planning to use new "giga press" machines for its fleet of vehicles.
And though Toyota admitted in September that it has a lot to learn from Tesla when it comes to EV production, the company said that it doesn't plan on copy-and-pasting Tesla's formula. Instead, Toyota plans to gradually integrate giga-casting into its production lines, without losing its existing, more traditional, methods of production.
Part of this two-pronged approach is inspired by concerns over ways to reduce potential repair costs. If the entire underside of a car is one continuous piece of metal, a repair to one piece of that part could be far more expensive than they currently are.
"To be honest, we are behind in gigacasting since we have yet to roll out a product," Kazuaki Shingo, Toyota's chief production officer told FT. "But we have done casting for a long time and ultimately we believe we can produce a product that will be cheaper, lighter and thinner with high performance."
Related: Toyota Seeks to Compete With Tesla Through Powerful New EV Technology
The company, which plans to sell 3.5 million fully electric cars every year from 2030 on, recently adjusted its fiscal year forecast, saying that it expects to sell 123,000 EVs, 137,000 plug-in hybrids and 3.5 million traditional hybrids. Tesla, by comparison, sold 435,000 vehicles in the third quarter of the year, below Street estimates.
"We don't actually think that our 10 million vehicles will immediately shift to gigacast," Shingo said, highlighting the company's intention to mix legacy production with gigacasting. This integration, executives told FT, will help push Toyota ahead of the competition.
The company's stock ticked up slightly Monday.
Get investment guidance from trusted portfolio managers without the management fees. Sign up for Action Alerts PLUS now.