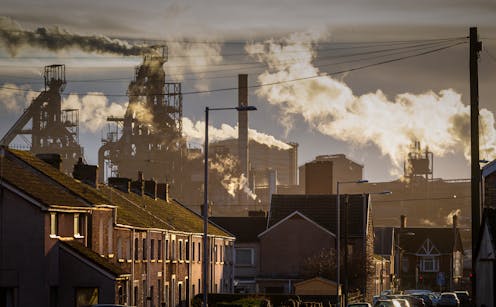
At first glance, a £500 million government investment into a critical industry looks like a move designed to inspire confidence. But the large sum will provide little comfort to the 2,500 people expected to lose their jobs as Tata Steel close the UK’s last blast furnace at Port Talbot in south Wales. And nor is it enough to guarantee the long-term future of British steel making.
But it will make it greener. The government money will be used to support a transition to electrically powered steel production, which will be more energy efficient and less carbon intensive.
Every 1,000kg of steel produced by a blast furnace results in the production of about 2,000kg of carbon dioxide. This falls to as little as 150kg from an electric furnace, meaning the change could reduce carbon emissions in Wales by up to 20%.
The new electric furnaces also require far fewer workers than traditional blast furnaces – hence the job cuts.
But the change is not as simple as it sounds. For the new furnaces will use an electric current to melt scrap steel or iron. They cannot produce what’s known as “virgin steel”, which is made from freshly mined iron ore.
Some say the electrically produced steel will not meet the most stringent safety and performance standards required for use in sectors like infrastructure or defence. Others argue that using recycled scrap steel is absolutely fine.
At the moment, the quality of the steel depends on the quality of the scrap steel being used, and certainly there needs to be more research done on how to get the best quality product.
But it will still be a significant challenge to build a recycling system to provide the necessary scrap steel. The UK produces around 10 million tonnes of scrap steel every year, but roughly 80% of it is exported. As domestic demand rises, diverting these scrap supplies will be crucial.
In Port Talbot, steel workers’ unions had another plan for the plant which involved a slower but more controlled transition that minimised job losses. The idea was to retain one blast furnace while introducing a smaller electrical furnace, and establish another operation known as a “direct reduced iron” (DRI) plant.
DRI, or “sponge iron” which can then be made into steel, is produced by reducing iron ore using gas, and if that gas is hydrogen it produces no carbon dioxide. Many countries, including Sweden, South Korea, Germany and the US are pushing ahead with hydrogen-based steel technology and steel plants. The UK must now decide if it will follow suit or risk being left behind in the evolving global steel landscape.
Hydrogen plan
These tensions underscore the broader challenges of industrial transition. The union plan would be more expensive and rely heavily on technologies still in development. But if it worked, it would offer the prospect of a more measured transition that protects jobs and enhances supply chain resilience.
However, it will require significant political will and collaboration between the government, Tata Steel, and unions to make this alternative feasible. As global steel overproduction (particularly from China) continues to affect pricing and profitability, short-term economics make such long-term collaborations very difficult.
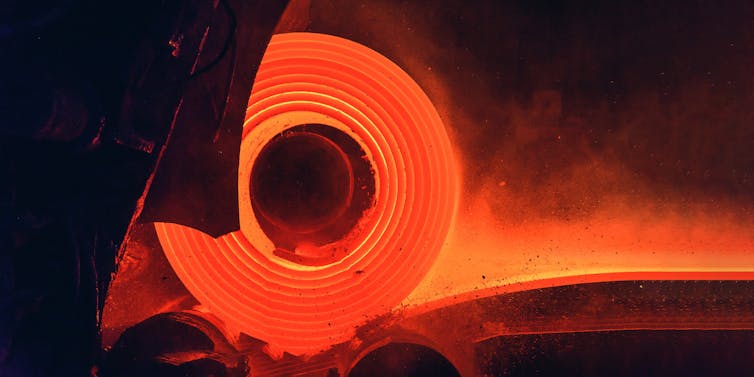
But for too long, the steel industry has pursued short-term operational fixes rather than embracing long-term change. For years, Tata has been able to enhance efficiency and reduce emissions from its blast furnaces, but these improvements fall well short of meeting genuine sustainability goals.
Meanwhile, the UK government (which said it was committed to making the UK a leader in clean steel production) claims that the deal in Port Talbot is is only part of a broader steel strategy.
Full details of that strategy are not expected until 2025. But it will need to address the fact the move to electric furnaces is a partial transition, and one which may not be enough to ensure the long-term competitiveness of UK steel making.
Done without careful planning, it could increase reliance on imported virgin steel and recycled scrap metal. It will also test the government’s commitment to “securonomics” which involves safeguarding the supply of key goods and services to the UK. If geopolitical rivals threaten the supply of steel, then would have a negative affect on new infrastructure investments and domestic manufacturing.
Ultimately, a genuine commitment to a national industrial strategy is a prerequisite for navigating this transition. Hydrogen will be a key part of any new steel story, but the UK is a long way from having a robust, scalable and affordable supply of green hydrogen. Again, in Europe, Sweden is leading the way.
Without significant investment and coordinated efforts to build the necessary systems for hydrogen production, storage and distribution, the steel industry’s shift to sustainable processes will be significantly delayed. But done well, over time, such a strategy could help secure the future of steel manufacturing and rebuild communities – and strengthen national resilience and competitiveness.

Phil Tomlinson receives funding from the Engineering and Physical Sciences Research Council (EPSRC) for Made Smarter Innovation: Centre for People-Led Digitalisation.
Michael Lewis receives funding from the EPSRC, ESRC and AHRC.
This article was originally published on The Conversation. Read the original article.