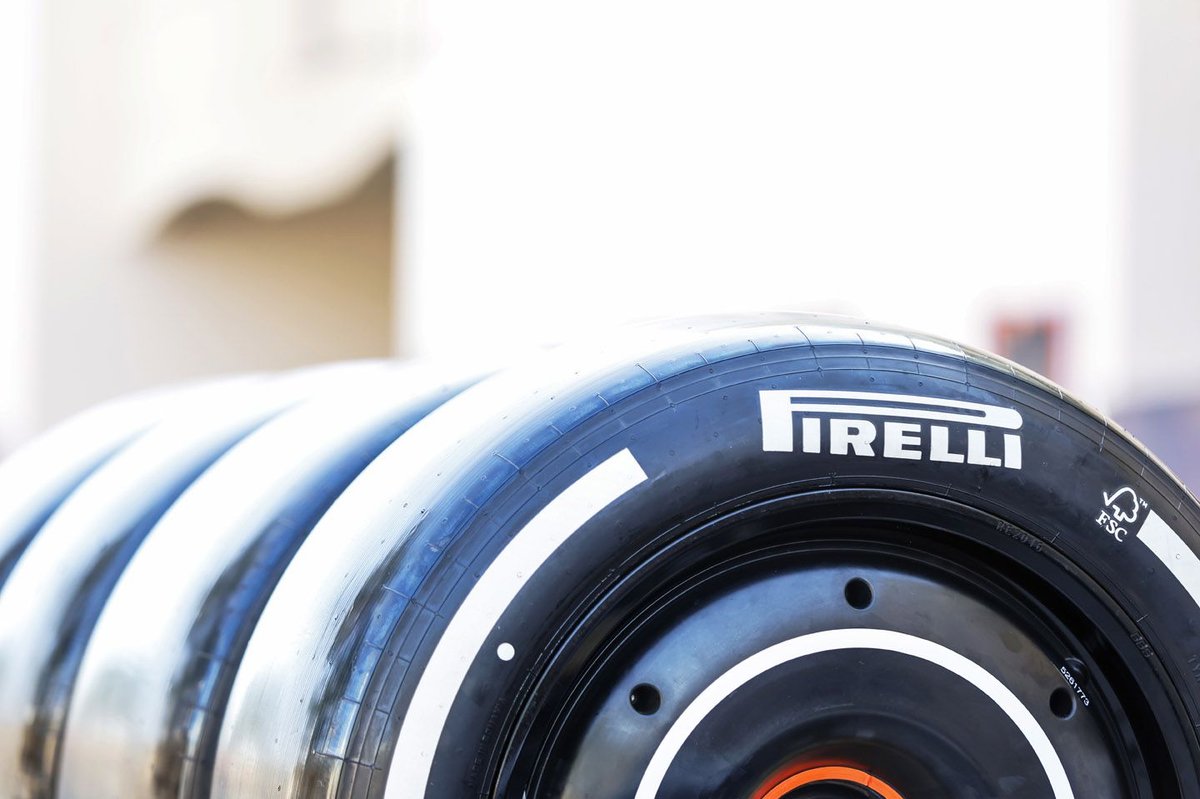
The topic was also a key element of the most recent F1 tyre tender process launched by the FIA, and which covered the 2025-'28 seasons.
However, long before it submitted its successful tender bid Pirelli had already established its sustainability credentials. Indeed, in November 2021 it became the first tyre company to receive a three-star certification under the FIA's Environmental Accreditation Programme.
"We got the FIA certification more than one year before the tender," says Pirelli director of motorsport Mario Isola.
"So we already started well before the tender to work around sustainability. And if we talk about sustainability in the company, we started with the first actions in this direction many years ago.
"For example, our factories use electricity from renewable sources, and that is not something you can do from one day to another. It is a long journey, and we have more plans for the future."
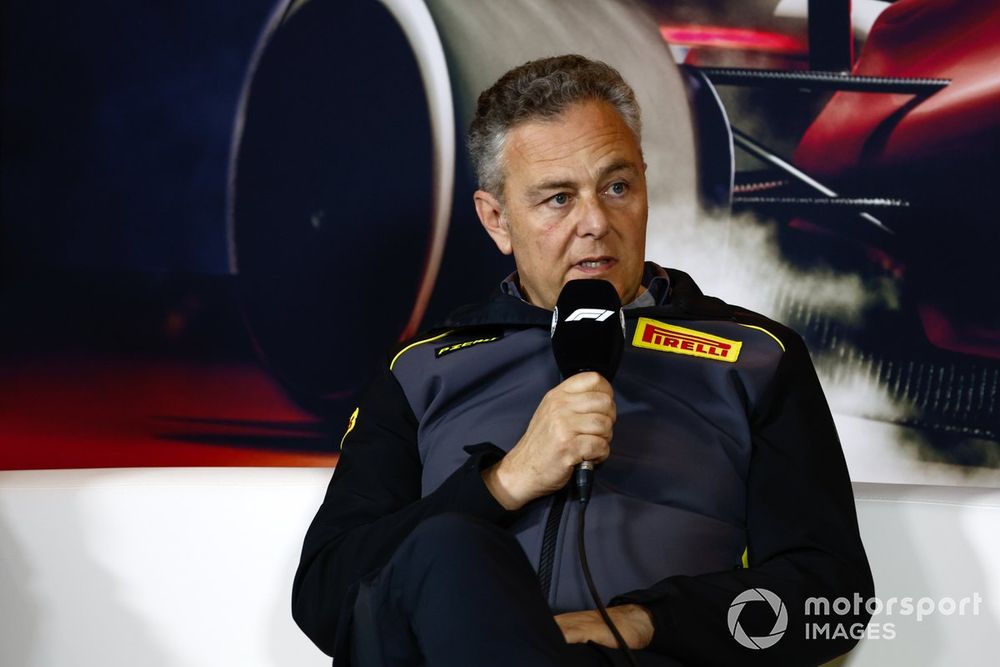
There are multiple aspects to Pirelli's F1 sustainability initiatives, and one of the key parameters involves the products that are used in manufacturing.
In parallel with its successful tender bid Pirelli achieved another important milestone when its 2024 F1 tyres were certified by the Forestry Stewardship Council.
"The FIA three-star is a certification that you have to fulfil some requirements for, and you get the certification," says Isola.
"However, the sustainability strategy for the company is something that is completely separate from the three-star.
"For example, there is no requirement to have an FSC tyre. It was our project to introduce an FSC-certified tyre in F1, because this is part of an activity we started with BMW in 2021, with a road tyre that was the first to be certified by the FSC.
"And as a natural extension of that we were also evaluating to use this certification for F1 tyres, and we were working in the direction to get this certification.
"It shows that we respect a number of conditions in all the life cycle of a tyre, from the rubber plantation, how we extracted the rubber from the trees, the respect of biodiversity, the respect of the local population, how we use this rubber.
"They follow all the life cycle of the tyre to the end of life, which is the way we recycle them."
Pirelli also pays close attention to the complex mix of ingredients used in the manufacture of its F1 tyres.
"That's part of a normal, let's say, upgrade of our materials," says Isola. "Obviously some ingredients that many years ago were permitted are now no longer permitted.
"It's probably something that is not visible, but every year, we test some prototypes and solutions that are replacing materials with new concepts that impact the environment less.
"Our health and safety department pays a lot of attention to that. And every year they give us targets to replace some materials with better ones, which we usually do, irrespective of new regulations and so on."
Each season Pirelli has to transport tens of thousands of tyres around the world, and a 24-race schedule, with the majority now taking place outside Europe, makes that a huge challenge. Reducing the carbon footprint associated with getting its tyres to circuits is a key target for the company.
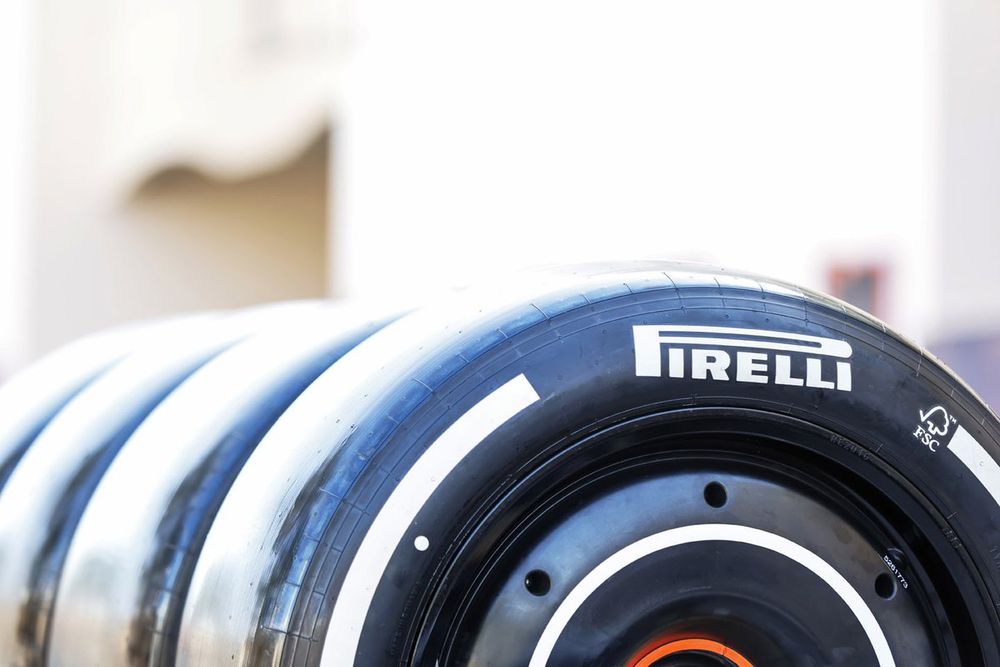
"If we talk about logistics, we transport the majority of our equipment and tyres – more than 90% - with sea freight," says Isola. "We reduced the air freight already many years ago.
"In Europe, our trailers are the latest Euro 6E standard. All the fleet is very new, and with the most efficient trucks."
Sometimes circumstances still force Pirelli to transport tyres by air, but that only occurs when it is absolutely necessary.
"It happens," says Isola. "This year we have been obliged to fly some tyres, because of the Red Sea freight situation, and unfortunately, it was not possible to reschedule the shipment in order to send the tyres at the right time for the first Asian races.
"Now the situation is more under control, and we've come back to a situation where we sea freight all the equipment."
Reducing the number of tyres that actually have to be manufactured and hence transported is an obvious way to address the carbon footprint.
In the past the wastage of unused wet tyres at the end of a dry race weekend was a frustrating issue.
While in Europe they could be transported to the following race by truck, still mounted on rims, that wasn't possible for flyaway events. Once dismounted, they were no longer usable, because of potential damage to their beads.
The solution pursued by Pirelli was to make changes that avoided such damage and meant that unused wet tyres could be dismounted, shipped without rims, and remounted at a later race weekend.
"That was an experiment last year," says Isola. "It's a regular procedure this year. Thanks to some modifications we made on the bead and on the fitting machines, we can now dismount the wet and intermediate tyres without damaging them, so we can re-use them.
"For example, at the beginning of the season we had dry races in Bahrain and Saudi Arabia, and those tyres have already been checked after dismounting them, and they are already on the way for a race in the second half of the season.
"So this batch of tyres goes to Austin or Mexico, and we don't have to manufacture new ones. Obviously, that has a positive impact – we save around 2-3000 tyres over the season, depending on the weather conditions.
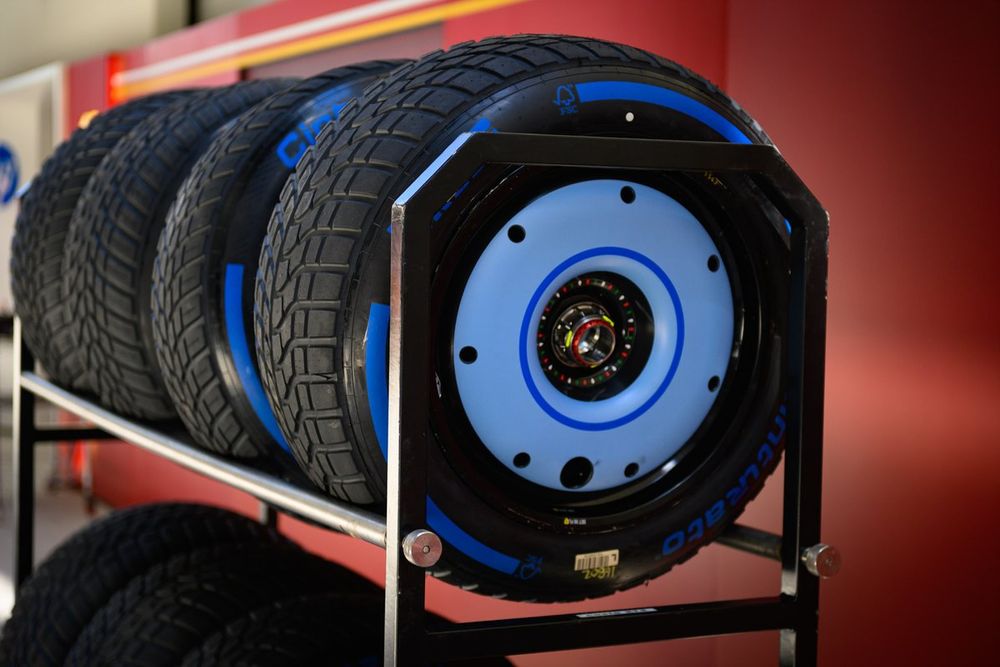
"It is complicated, because we have to follow the calendar, and our logistics department works hard in order to make an efficient schedule for these tyres to be re-used at another race."
Pirelli is always looking for ways to reduce the number of tyres required on a race weekend, and that includes potential rule changes, although it's never easy to convince the teams to cut back.
"Obviously, this has an impact on production and shipment," says Isola. "There was a plan last year with the alternative tyre allocation to reduce two sets of slick tyres per car per event. That was, in my opinion, quite a good plan.
"At the end of the year it was decided to abandon this idea for a number of reasons, but I believe that the topic of reducing the number of tyres that we use during a race weekend is still on the table for 2026.
"However, the teams don't like change, and for them it's better to have more tyres, because they have more possibilities for testing."
Less obvious than race weekend usage are the steps Pirelli has taken in terms of reducing the number of development tyres it produces for track testing, thanks to increasingly sophisticated simulation tools.
It can be compared to the way F1 teams use CFD to reduce the number of wing iterations that are actually manufactured and tried in the wind tunnel and on track.
"Virtualization is important for sustainability," says Isola. "Thanks to the virtual models that we have developed, especially with F1 and then extended to GT road tyres, we can accelerate development, but we can also cut the number of physical prototypes we produce.
"If we talk about developing the 18-inch F1 tyres, we tested 70 specifications of tyre virtually, and we tested 30 on-track.
"So clearly this has an impact on the number of physical prototypes you have to produce, and this has an impact on sustainability."
One initiative that has had a clear benefit in terms of power usage is the reduction in the use of blankets. They have already been removed from wet tyres, and intermediates are set to follow that route when FIA approval has been attained.
While plans to drop blankets for dry tyres have been put on hold following last year's testing programme it's worth noting that they now consume less electricity on a race weekend than they previously did.
"We worked to develop a dry tyre able to work without blankets," says Isola. "It's still a project that we have in mind. Removing the blankets is a good message, for sure.
"We already reduced the temperature and the time that tyres stay in the blankets, and this obviously reduces the electricity that is needed. If I make a comparison with 2019, back then we were heating tyres at 100C for three hours, and now it's 70C for two hours.
"We saved more than 50% of the electricity that we used in 2019, so there is this reduction. We are no longer heating the extreme wets, and the plan is also to remove the blankets as soon as we can on the intermediates."
What happens to F1 tyres after they have been used is another important issue, and one that Pirelli has addressed.
"In the past when we started with F1 we were burning tyres and producing energy," says Isola. "Now we send all the tyres back to UK, where we crush them, and we use this material as a secondary raw material to produce new applications, like plastic floors, like tarmac, and other applications. It is more efficient.
"We have plans for the future, and we are also testing some new processes to make it even more efficient. The final target is to use these materials again in tyres."
Pirelli has left no stone unturned in its quest to address sustainability, and that extends beyond the tyres themselves to all aspects of its race weekend operations.
"Several years ago we removed any single use plastic from our operation," says Isola. "And we have some parts of our team kit that are made with recycled material – for example, our shoes and luggage.
"And we are trying to extend this approach with any small detail that is affecting our operation. So sustainability is not a single action."