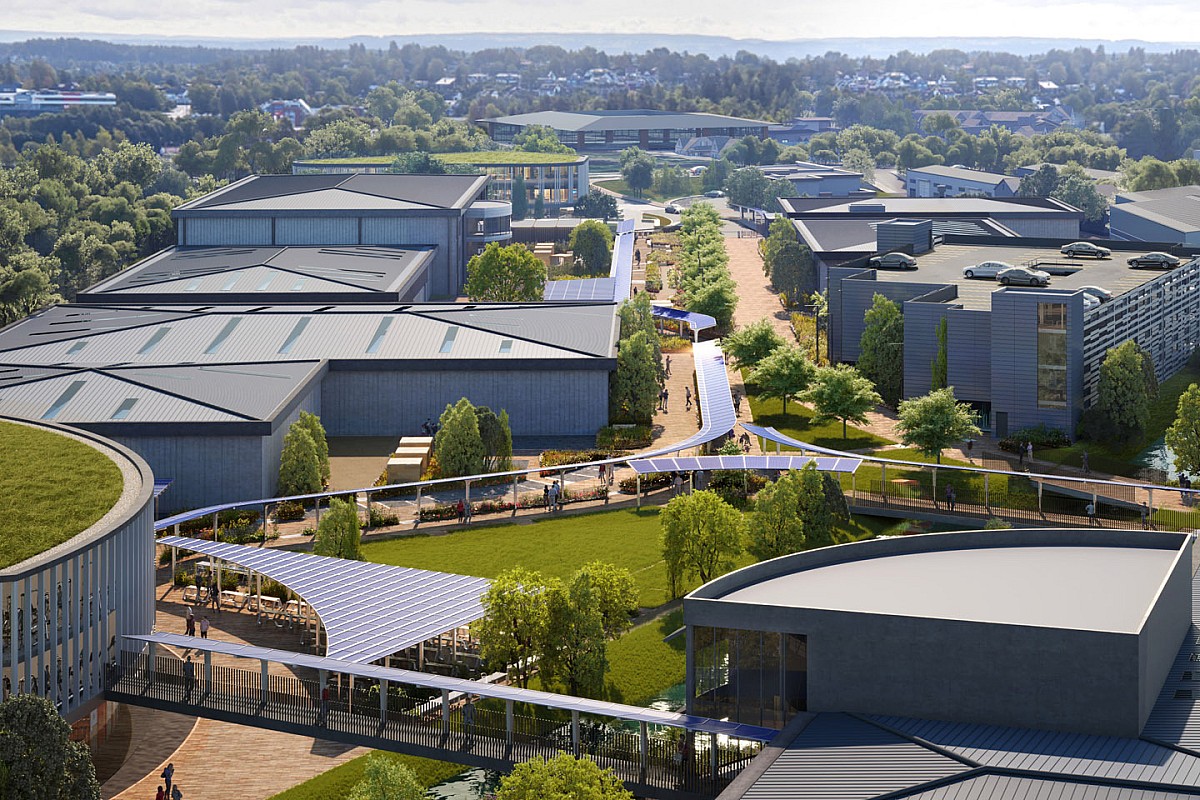
But, ahead of the Monaco Grand Prix where it unleashes a major upgrade to its W14, the German manufacturer has revealed plans for big changes to its Brackley-factory too.
As part of what has been a £70 million commitment to upgrading its facilities since 2017, Mercedes has given the green light to the biggest overhaul yet of its campus.
It plans to make it more pedestrian friendly, and there will be the construction of new marketing buildings, leisure facilities and restaurants to help improve the team’s working environment. It is hoped work will be finished by the end of 2025.
Team boss Toto Wolff says he does not just want the completed facility to be the best factory in F1; he wants it to be something that rivals the best even Silicon Valley can throw up.
“We are not orientating ourselves towards our competitors in our sport,” he told Autosport in an exclusive interview.
“We are orientating ourselves towards the best technology campuses that we know from the United States. That's the ambition.”
To the cynical, spending like this may seem to be quite frivolous – especially because, in the cost cap era of F1, teams need to be using every penny possible in making their car go quicker.
After all, with the current competitiveness of the grid, unlocking just one tenth of a second with a new development can be worth a couple of positions on a Saturday afternoon.
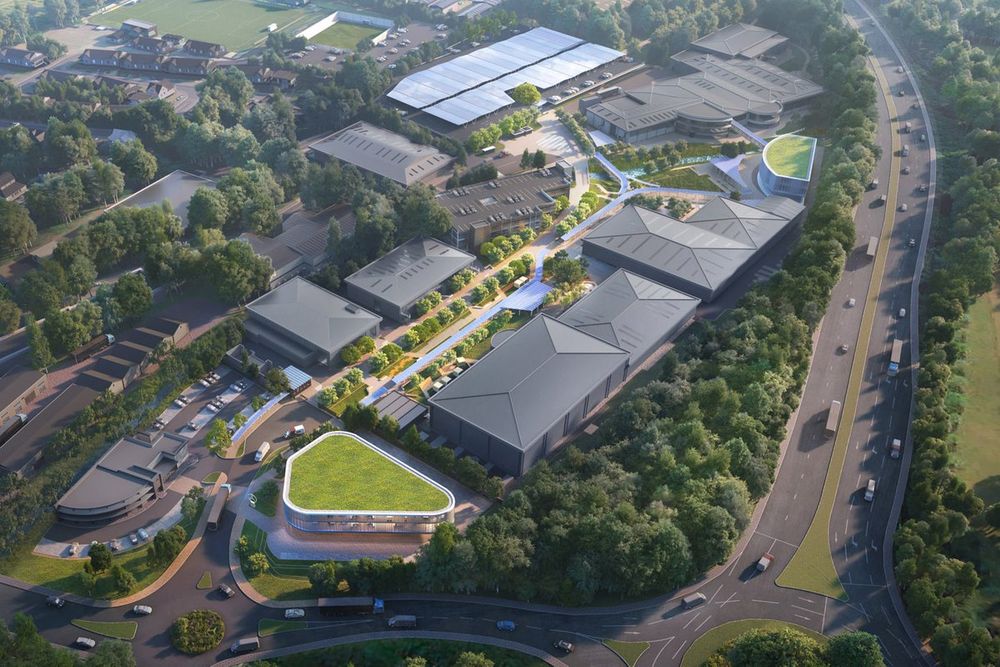
But what is important to understand about the motivation behind the Mercedes factory overhaul is that it is not about making its car quicker today; it is very much about ensuring it is faster tomorrow.
Wolff makes no bones of the fact that the motivation behind the changes at Brackley is about delivering somewhere and something where the top brains in F1 want to work.
As the implications of F1’s cost cap limits bite (and facility construction like the campus changes fall outside the scope of the rules), one thing teams have come to realise is that there is increased competition to attract the best staff – and also keep them.
Wolff says the design of the new campus has not been inspired as a means of showing off something beautiful to sponsors, nor grabbing attention to win any architecture awards.
Instead, there are practical reasons behind it – in that it will make Brackley a place where the top people want to work.
“You must never get carried away by the aesthetics of a campus,” he said. “When that becomes the main priority, you need to concentrate on what's best for the people.
“This is also a fight for talent retention and hiring; and being an attractive employer. Therefore, that shows our commitment, and that what we're doing is for all of our people. We want it to become a best-in-class technology campus.”
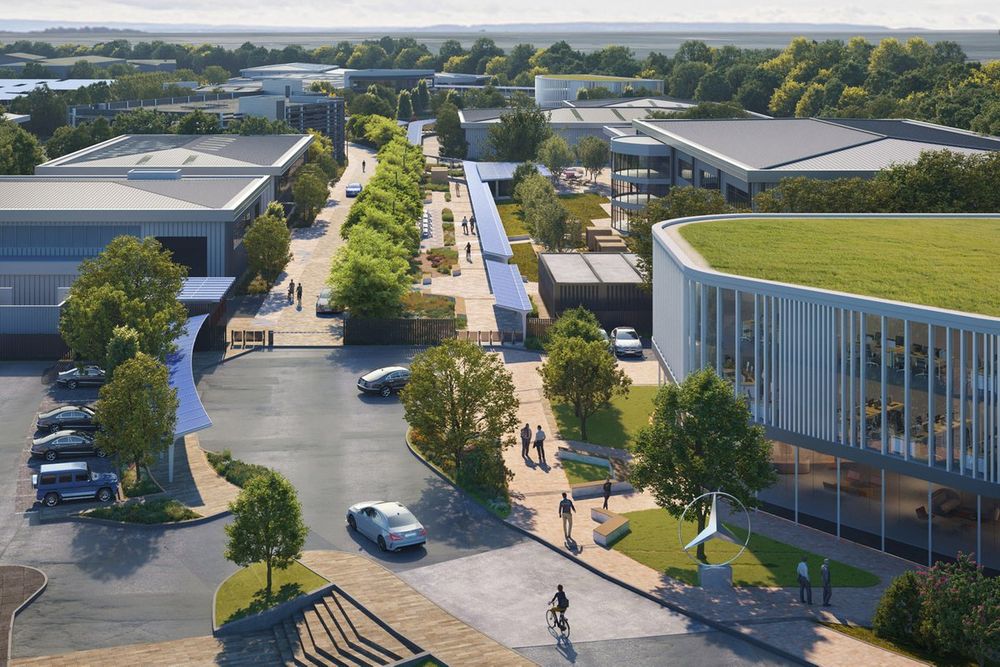
Delivering something that is a rival for what other industries are offering is also something that Wolff thinks is important, because the cost cap has changed the nature of F1 employment.
Whereas in the past, F1 proved so attractive to the best brains because wages were so high compared to other industries, that is no longer the case.
With salaries falling under the cost cap, teams have to balance making wages super attractive against the need to ensure as much of its spending per year can go on improving the car.
Blank cheques to sign the best talent are no longer possible, so teams have to look at other ways of encouraging top names to join – and that sometimes can mean winning them over from other industries.
“We need to attract and retain the best people,” said Wolff. “We've seen with the cost cap that sometimes we are limited in the possibilities of paying people the same as any other industries.
“There are areas where we're clearly not competitive anymore on the cost cap. And it's something we need to address also going forward; how important it is to have the best people here.
“Formula 1 was always an aspirational environment, not only for working in F1 per se but also being able to earn more than in other any engineering industry in the UK.”
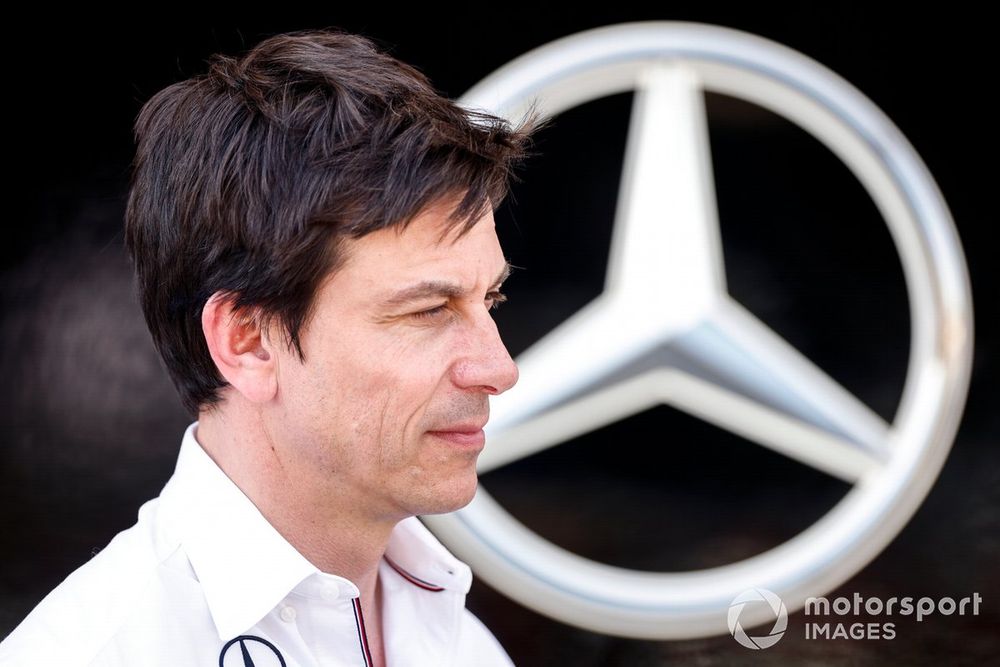
Off the back of it emerging that Mercedes has given a pay rise for staff in-line with inflation, which is currently around 10%, the team’s investment in staff is clear to see.
It is obvious then why Mercedes could not afford to sit back and not try to make its factory the best it can possibly be.
“The learning is coming from; how do we work today?” added Wolff.
“How are we creating an attractive workplace that provides you with an environment that is most inspiring, and that triggers creativity? How are we providing spaces that encourage you to work less from home and more from here?
“You can say that a gym doesn't make the car go quicker. But, if the gym makes people happier and enjoy where they work, that makes a car quicker.”
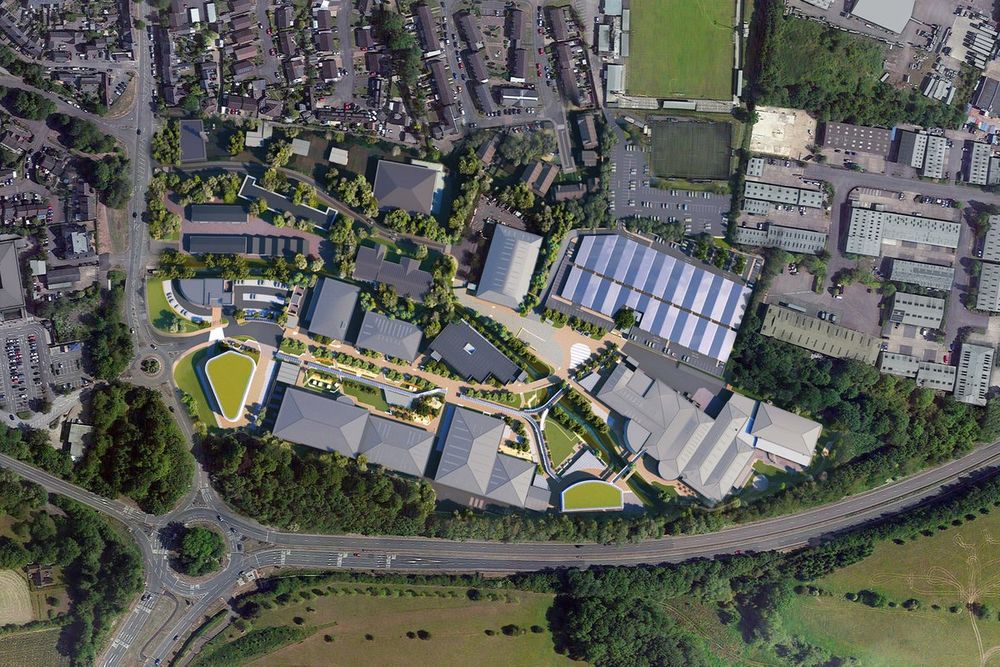