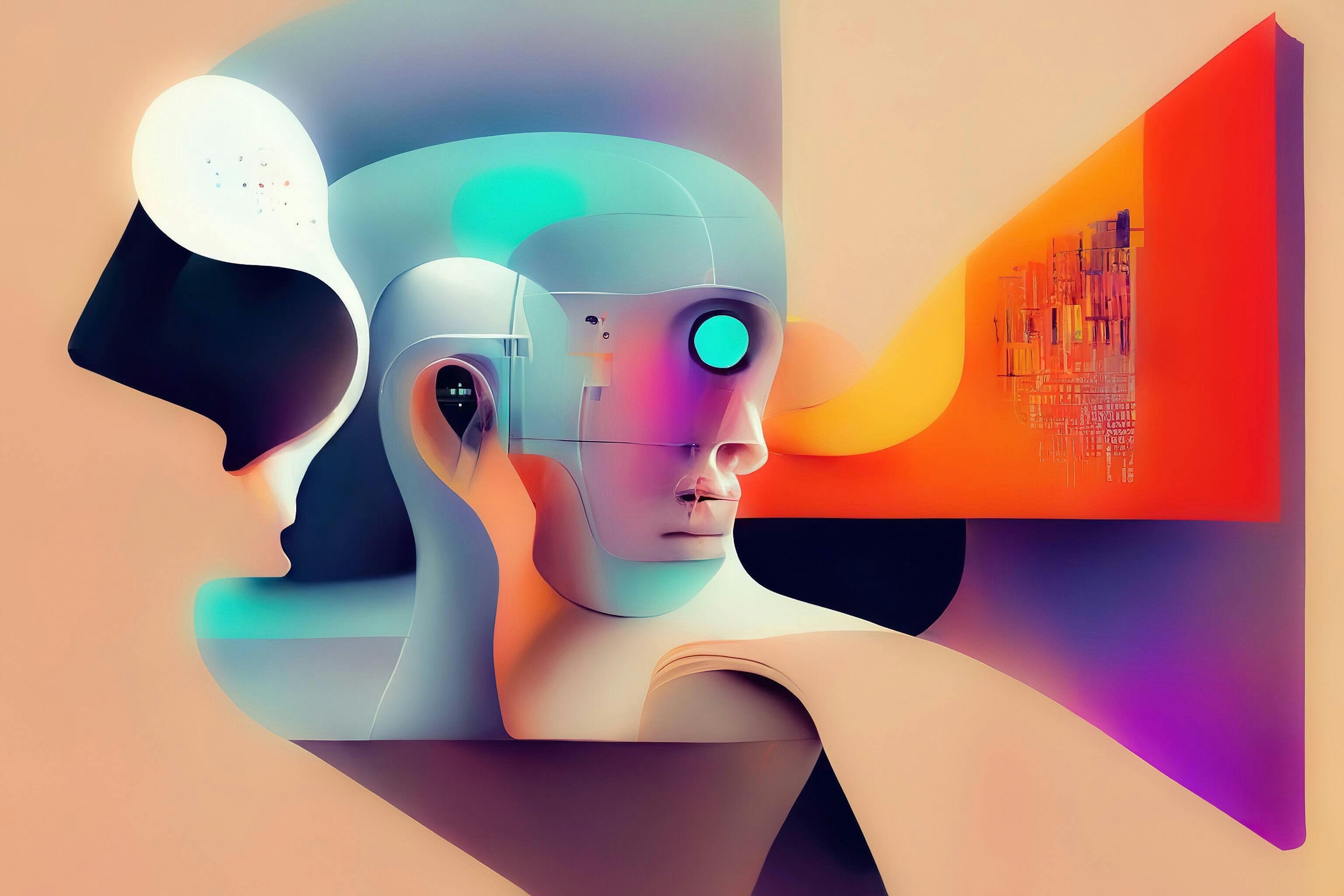
Imagine a film that can be stretched to reveal a hidden message or a bathing suit that shifts hue during laps. What about an armband that changes color based on muscle mass measurements?
While these gizmos may sound like the stuff of dreams, a team of engineers has repurposed a 19th-century photography technique to develop elastic materials that reflect different wavelengths when strained. Researchers have paved the way for producing these detailed, large-scale materials that feature “structural color” — meaning that the microscopic structure dictates the hue, as reported in a new paper.
What’s new — The idea of structural color is borrowed from nature. Outside of the wild, man-made pigments and dyes provide products with their signature shades. This distinction could soon change: In a study published in Nature Materials, scientists from the Massachusetts Institute of Technology (MIT) laid out the details for a manufacturing technique to produce structurally colored materials that could revolutionize product coatings and packaging, as well as wearable devices.
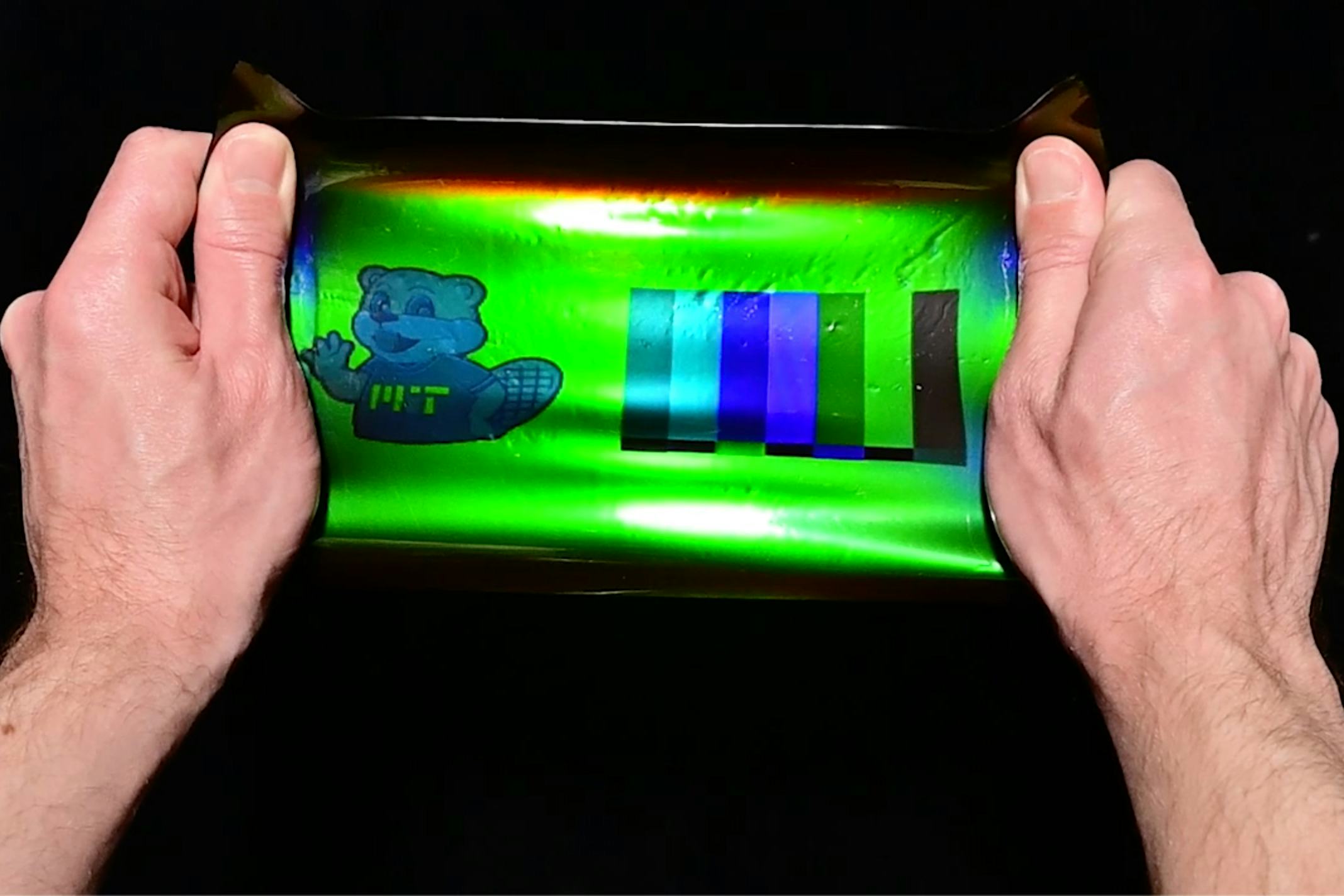
Co-author Mathias Kolle, an associate professor of mechanical engineering at MIT, looked at shiny creatures for inspiration. His team has studied how mollusk shells, butterfly wings, and other iridescent organisms reflect light via microscopic surface structures. These structures work somewhat like mini, colored mirrors, a feature that teams such as Kolle’s aim to recreate in the lab.
Previously, these structures were difficult to replicate. The team writes, “an approach that offers both [microscale control and scalability] remains elusive, despite several potential high-impact applications.”
The discovery — Holography, a technique that produces 3D images by superimposing two light beams onto a surface, offered a solution to this challenge.
“I realized what they do in holography is kind of the same thing that nature does with structural color,” says Benjamin Miller, a graduate student in MIT’s Department of Mechanical Engineering, in a press release.
So Miller and his colleagues took hints from holography and Lippmann photography, an early color photography method from the late 19th century. Ultimately, they applied Lippmann’s photography to modern holographic materials.
The researchers stuck elastic, transparent holographic film onto aluminum. They then projected images onto the film and created vivid reproductions of the original colors. To test their color-shifting theory, they stretched out the film and watched the hues transform as they reflected slightly different wavelengths. Red, for example, could appear blue when the material is strained.
Beyond textiles, the team is also looking into applications like color-changing bandages that could be used to monitor bandage pressure levels when treating conditions like venous ulcers and certain lymphatic disorders. Other possibilities dip into the realm of science fiction.
“Now that we’ve cleared this scaling hurdle, we can explore questions like: Can we use this material to make robotic skin that has a human-like sense of touch? And can we create touch-sensing devices for things like virtual augmented reality or medical training? It’s a big space we’re looking at now,” Miller says.
On the horizon ...
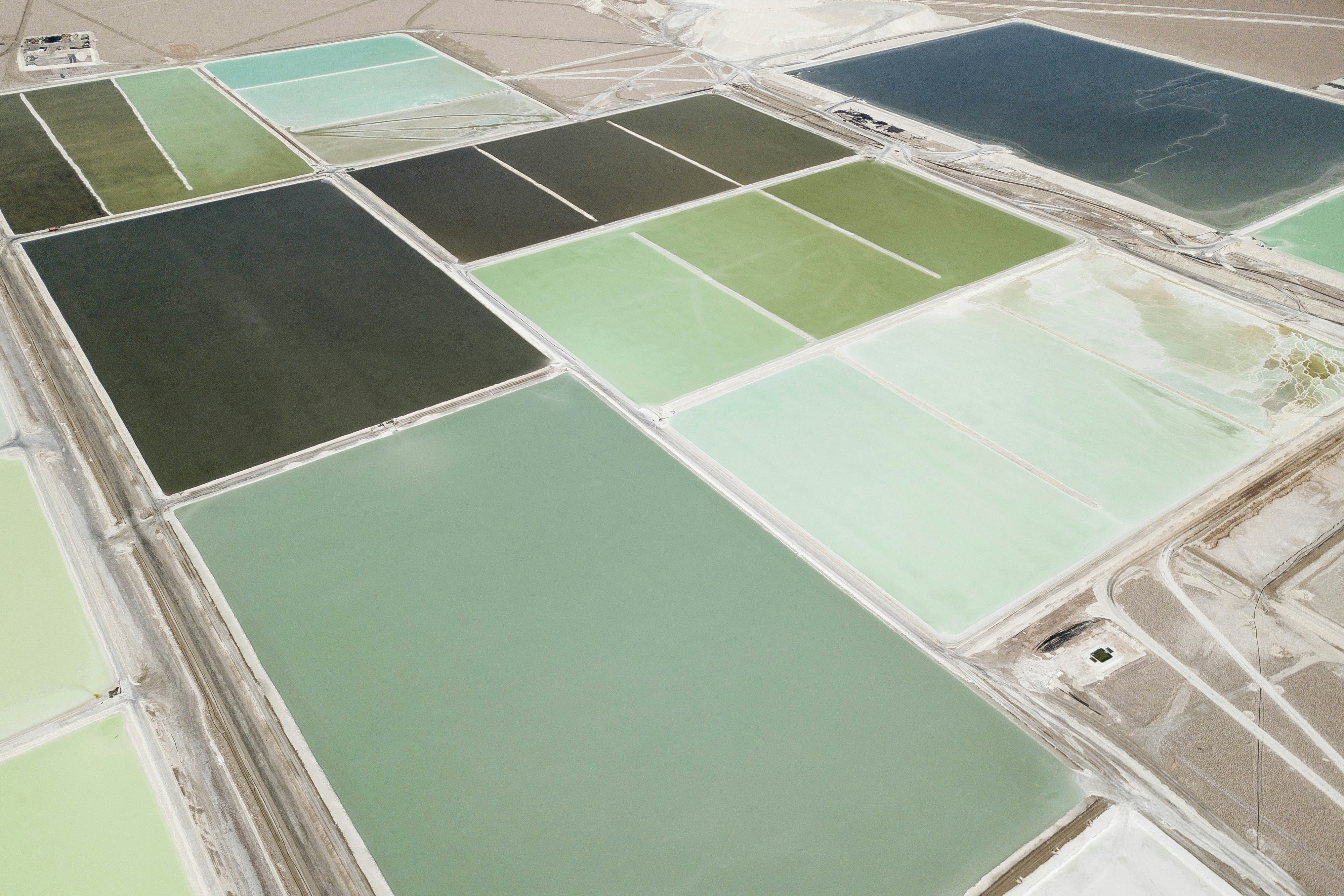
In today’s world, we increasingly rely on a tiny powerhouse to keep us online, on the road, and on top of our daily demands: The lithium-ion battery. By the end of the decade, we will need to magic up as much as 4 million metric tons of lithium carbonate equivalent (the stuff that goes into the batteries) to (literally and figuratively) keep the lights on — that’s many times the 500,000 metric tons used annually now. Lithium is already scarce. So that begs the question: Where will we get all the lithium we need?
As Inverse has previously reported, the answer may lie in wastewater from geothermal plants stationed in salt lakes like the Salton Sea in California. But to make that possible, you need to be able to harvest the lithium ions out of the brine — preferably with as little additional environmental damage as possible.
Thankfully, scientists are on the case: A team at the University of Chicago led by engineer Chong Liu explained to Inverse that one could use a technique called electrochemical intercalation in which an electrode is used to remove the ions from the water. That would negate the need to use chemicals to sort the lithium ions from the salty soup, which is the typical extraction method today.
One sticking point: Sodium ions. It’s hard to separate the lithium ions from the various other elements in the water, so a next-step innovation would be to find an electrode material that does an efficient job: “I hope these results will encourage others to study lithium extraction, especially to find better materials that can increase lithium selectivity,” Liu said. Extracting the “white gold” from wastewater could have a huge pay-off.
Read the full story to find out why.
Here’s what else we’re reading...
- An engineer who was fired by Google says its AI chatbot is “pretty racist.” Business Insider has the scoop.
- Meta shared information on 21 billion Facebook friendships to aid a research project on economic inequality, The Verge reports.
- If insects feel pain, should we rethink research ethics? Undark tackles this stinging question.
- The groundbreaking climate bill would provide nearly 400 billion for climate and energy projects. MIT Technology Review has the details.
- A California-based organization wants to use AI to help us communicate with animals. Not everyone is a fan, according to The Guardian.
Editor's note: On August 2, 2022 this post was updated to correct a photo caption.