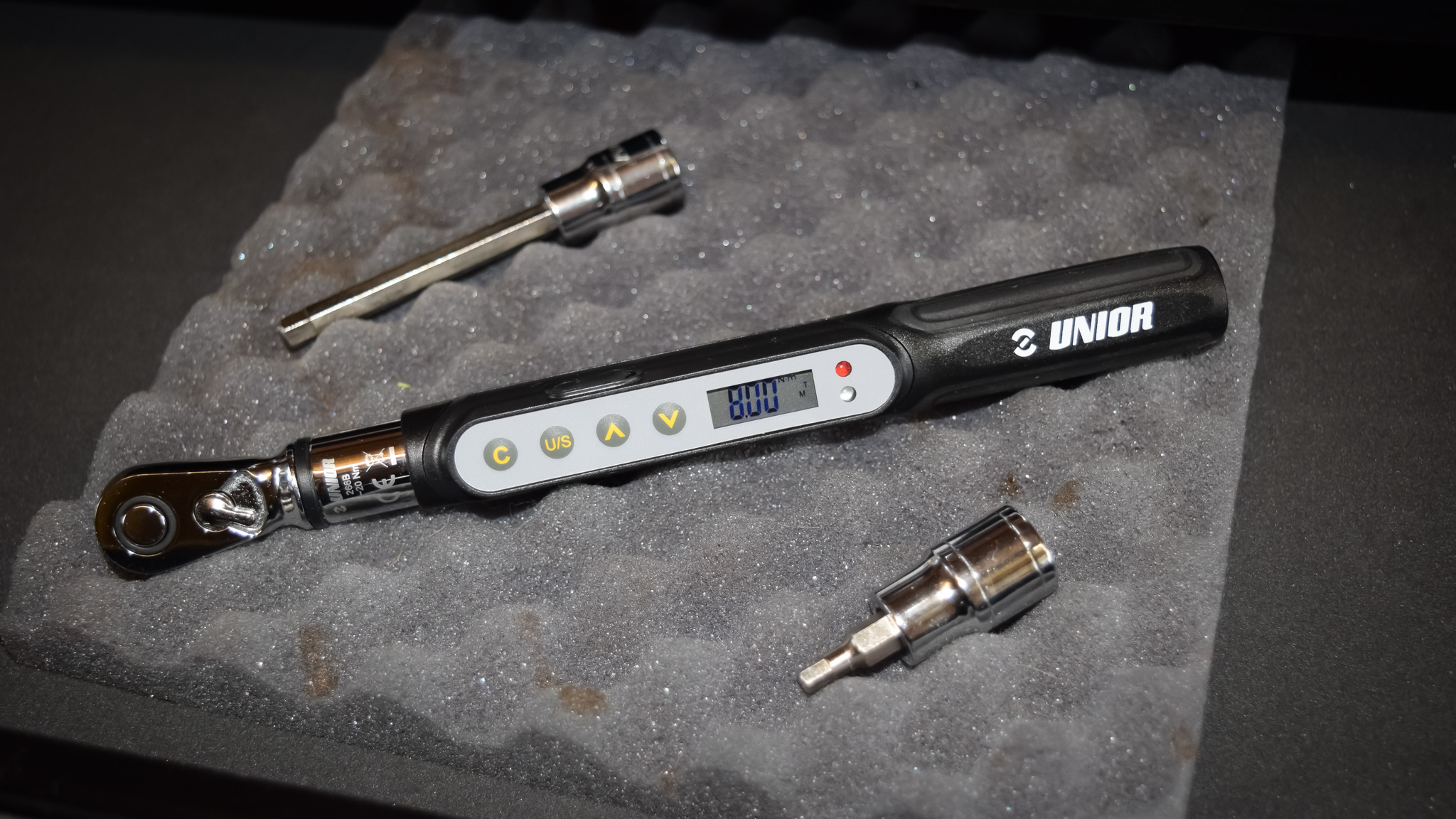
We hear about torque quite a lot in the cycling world these days. Bike mechanics will use torque wrenches daily to tighten bolts to spec. Before going any further 'torquing to spec' refers to tightening any fastener to the torque rating - or 'specification' - set by the manufacturer. Home mechanics are encouraged to purchase one of the best bike torque wrenches to help look after their equipment properly and minimise the chance of damage. Some of the best road bikes now even come with a torque wrench included to help owners hopefully get things right out of the box.
As a qualified mechanic, I have spent years torquing fasteners (a fastener is used to hold objects together, on a bike these will usually be threaded, with the thread used to secure components to one another i.e a screw or bolt) on bike components to spec and looking up and learning component torque ratings to ensure customers' bikes were maintained to spec and to minimise the risk of damage. Every day is a school day, as the saying goes, and I have always been interested in how things are done in other industries compared to the bike world when it comes to torque and torque wrenches. To that end, I've spoken with two professional bike mechanics, an aircraft technician and an automotive mechanic to see how things are done in their industries, in order to create an interesting comparison on working with torque. I had a few preconceived ideas that I wanted to ask them about, as well as questions the mechanic in me just wanted to know out of sheer curiosity.
One of these hunches is that even though torquing fasteners on bike components is widely regarded as good practice, it's not seen as essential and therefore isn't enforced as stringently compared to other sectors. This is possibly because bikes, in the overall scheme of things, are somehow seen as less serious when compared to cars or planes. The ramifications of a component failure on a bike, car or plane however can obviously all be catastrophic.
I will be pursuing some of these ideas in more depth in a future piece on torque where I will be speaking to several major torque wrench manufacturers to get a take directly from the horses' mouths.
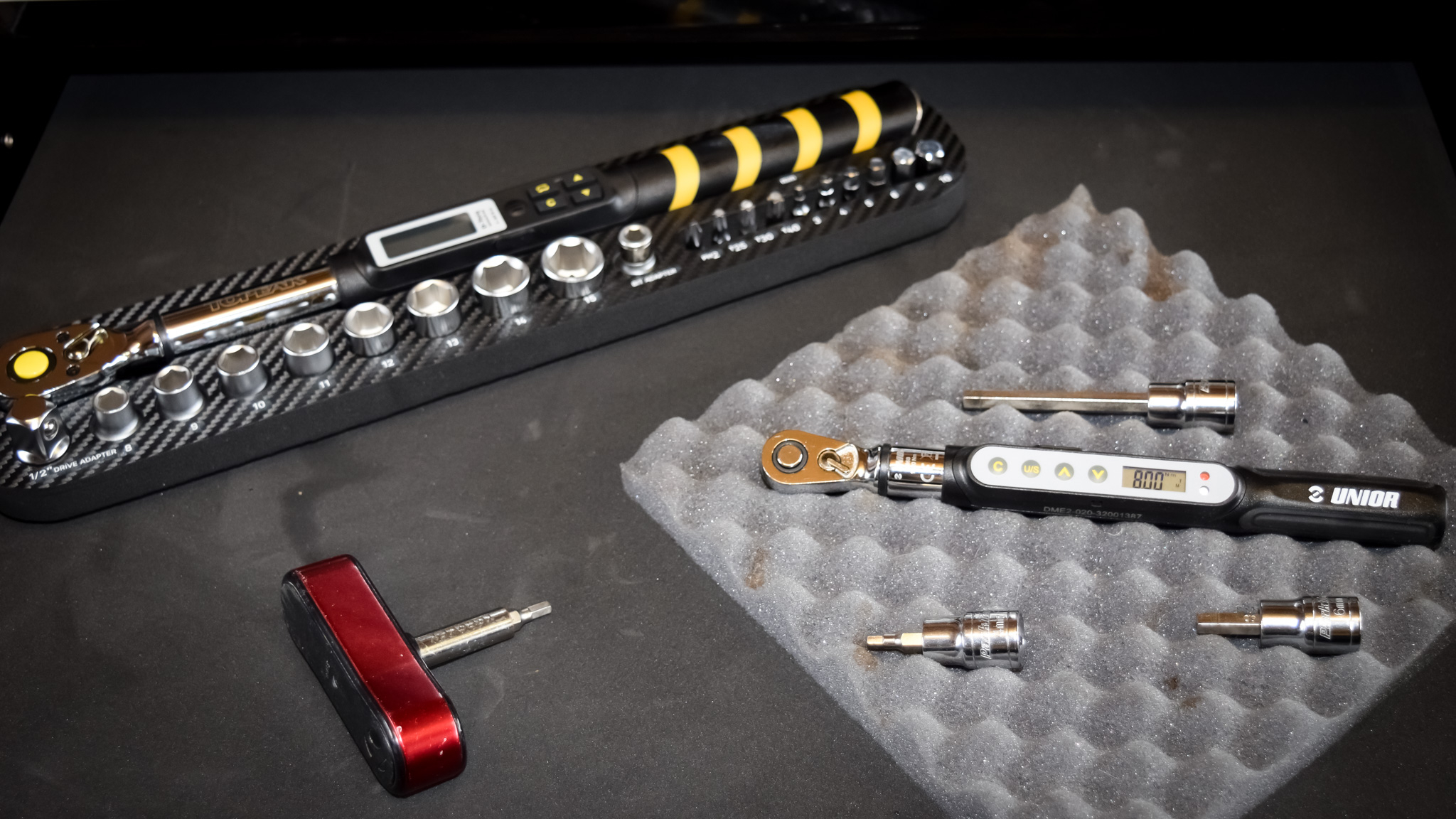
I spoke to Bahrain Victorious's head mechanic and head of technical operations Filip Tisma, as well as Richard Steels from Detail Bike Tech, a pro mechanic who has worked with the Great Britain Cycling Team and Ineos Grenadiers on Dan Bigham's Hour Record project. I also spoke to aircraft mechanical technician, Harry Shakespeare; and finally Christian Beyer, mechanic and owner of Chipp'wa Valley Motors, a general automotive repair shop located in Wisconsin, USA.
It was clear that there were some common themes running through the answers which is probably to be expected from professional mechanics who do this day in and day out for a living and who all work to a high standard. The responses also highlighted one or two interesting points the bike industry could maybe take something from.
The first thing I wanted to establish was the importance of torquing fasteners in each of the mechanic's roles. Beyer's response highlighted a great deal of importance attached to torquing fasteners correctly in his line of work.
"We have a policy of torquing nearly every fastener we touch. We even go as far as requiring all fasteners we touch to be marked with a paint marker once they have been sufficiently torqued. This level of attention to this small detail helps us know for sure that our work is completed to the highest standard with no guessing that could lead to failures down the line." he said.
I myself have often re-checked a bolt at the end of a job to ensure I had indeed torqued it to spec, I knew I had, I just wanted peace of mind by double-checking. Marking fasteners with a paint marker is a new concept to me, and could save time as well as provide peace of mind when working on bikes.
In response to the same question, aircraft technician Harry Shakespeare said "The importance of torque tightening on aircraft is to make sure fasteners are tightened to the correct level according to manufacturer's maintenance manuals.”
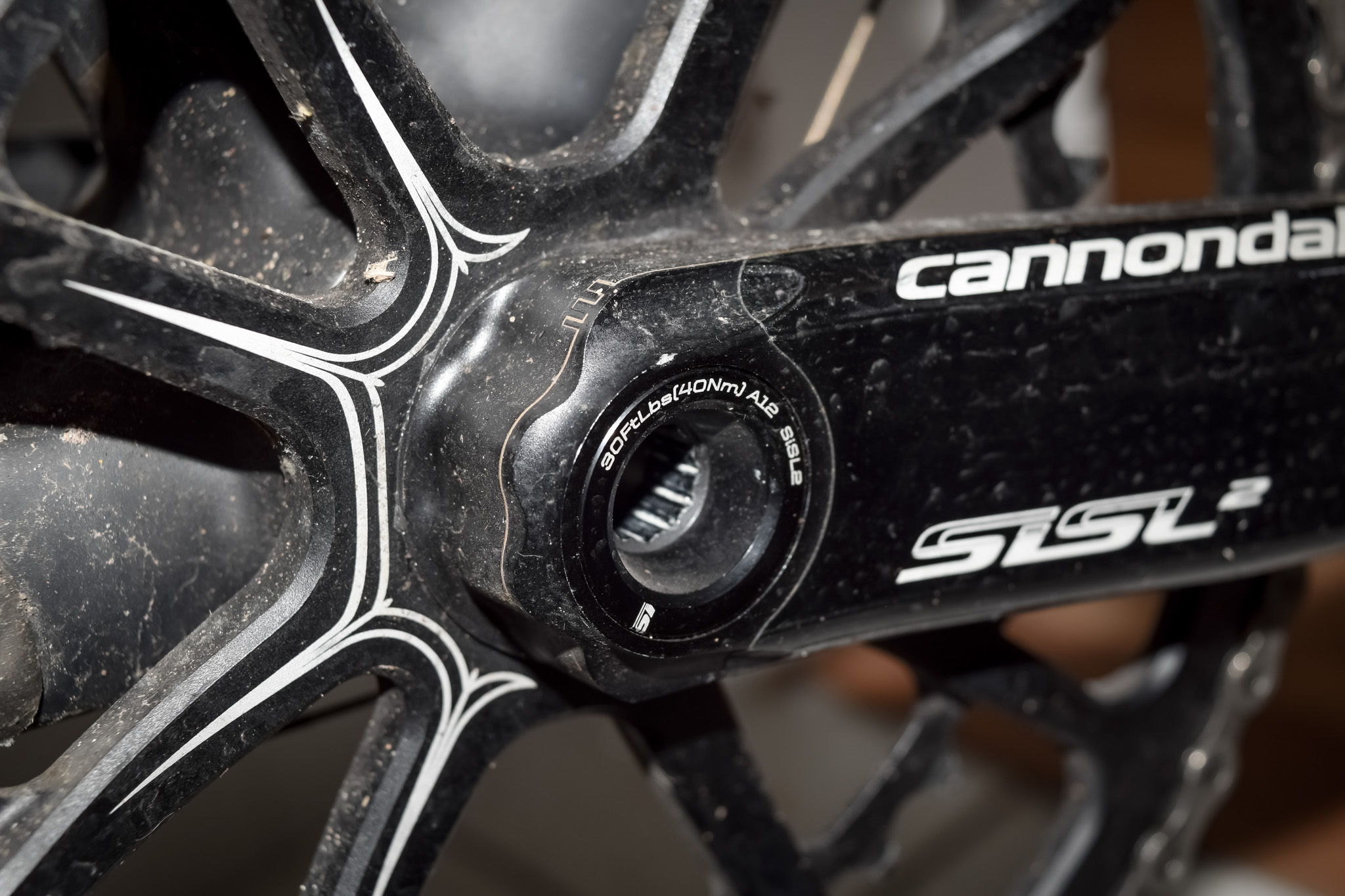
It's clear torquing fasteners correctly was critical to all of the mechanics, I also asked them if they used a system for logging torque checks and how this was carried out. Bike mechanics will log torque checks on bike PDI (pre-delivery inspection) sheets and service invoices, and mechanics carrying out bike fleet maintenance work will log service intervals, and by extension, torque checks too.
Shakespeare said: "We follow a maintenance manual which tells us to apply torques to different fasteners, but for critical components such as engine mounts and flight controls, we will have duplicate inspectors visually check they have been torqued correctly to avoid complacency."
Clearly, maintenance checks on aircraft are taken seriously and inspectors visually checking torque work show nothing is left to chance.
On the same point, Bahrain Victorius mechanic Filip Tisma said "All components have torque specs written on them, and the bikes are checked every day". Steels echoed this response by saying "I have a routine to check a bike before I take it out of the stand."
It's probably fair to assume that there is a significantly larger paper trail required with regard to aircraft maintenance than is perhaps needed in a bike workshop or shop service department. It's clear that the same level of thoroughness and professionalism is there, but the bike industry seems to require generally less stringent checks compared to the aviation industry.
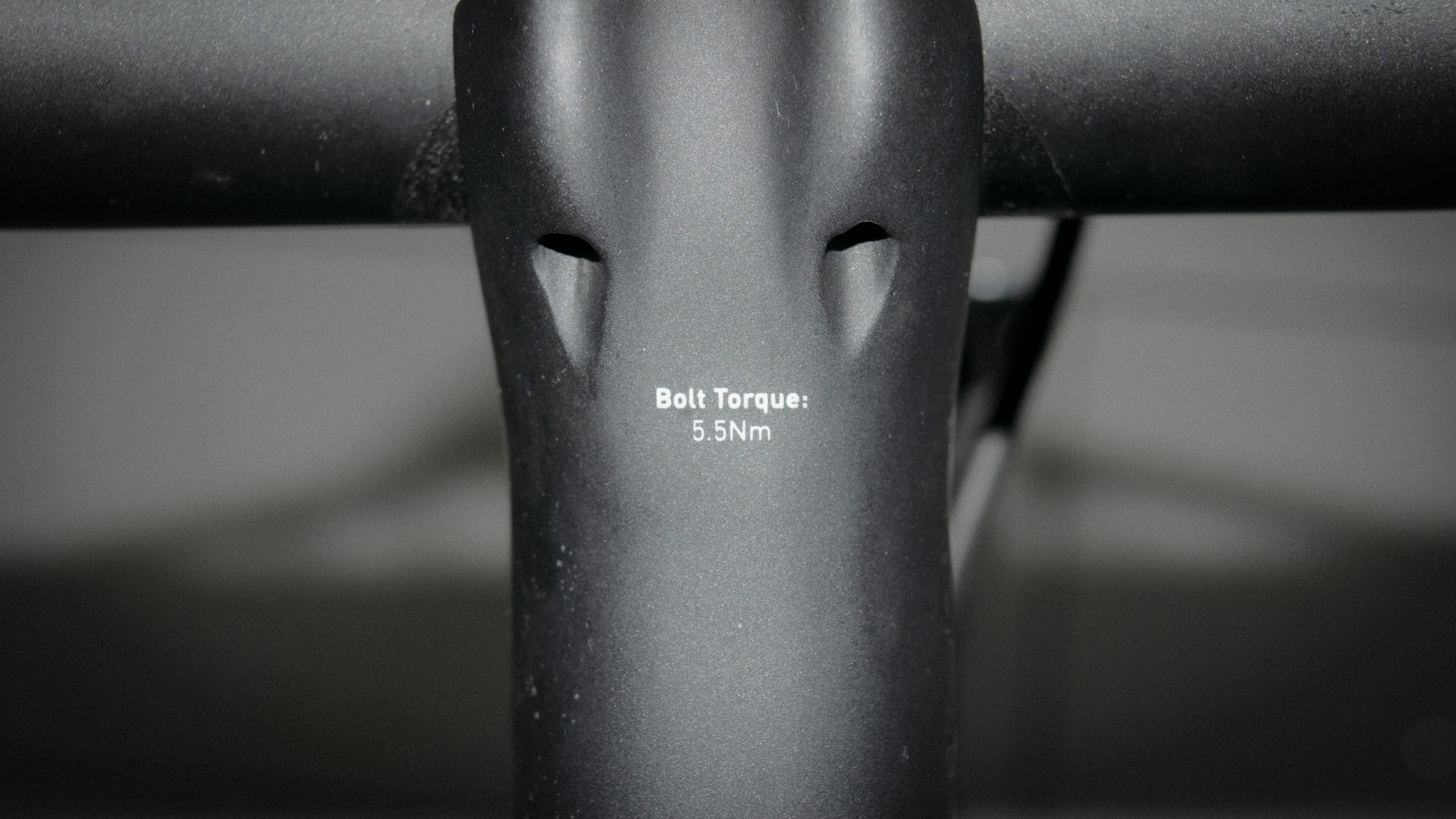
Mechanics generally take pride in their tools and usually amass their collections over a period of years. Bike shops tend to supply the majority of tools needed although mechanics will, of course, buy the specific tools they want or need. Interestingly, in other industries, mechanics can be expected to buy all of their own tools. Independant bike mechanics or ones running their own workshops will of course own their own tools as well.
In the same way that cyclists get excited about shiny bike components, mechanics appreciate a flash set of Allen keys or interesting tools. I asked the mechanics what brand(s) of torque wrench they used, and found there was a common and fairly unsurprising name being mentioned.
"I use Snap-on Techno-wrenches as my daily drivers, I have two which cover both ends of the torque scales. They are both digital and offer really accurate readings which I find critical for when I am doing suspension work or working on delicate components such as Darimo [who make some seriously exotic carbon fibre bike components] parts which use very low torque values." Steels said.
Snap-on tools are often the go-to for mechanics across various industries worldwide and the iconic logo is seen as something of a benchmark. Many of the tools are regarded as bulletproof and the warranty is often lifetime with no questions asked if it breaks.
Bahrain Victorious also chooses to use the American brand's tools with Tisma saying "We have a partnership with Snap-on and Bahco, who provide us with the highest quality tools every season."
Beyer also mentioned Snap-on equipment in his response. "We use numerous brands and sizes of torque wrenches, Snap-on, TDI, and Precision Torque are the brands we primarily use. The types of torque wrenches chosen to use vary based on application, but we have a selection of electronic, beam, split beam (click type), and dial type" he said.
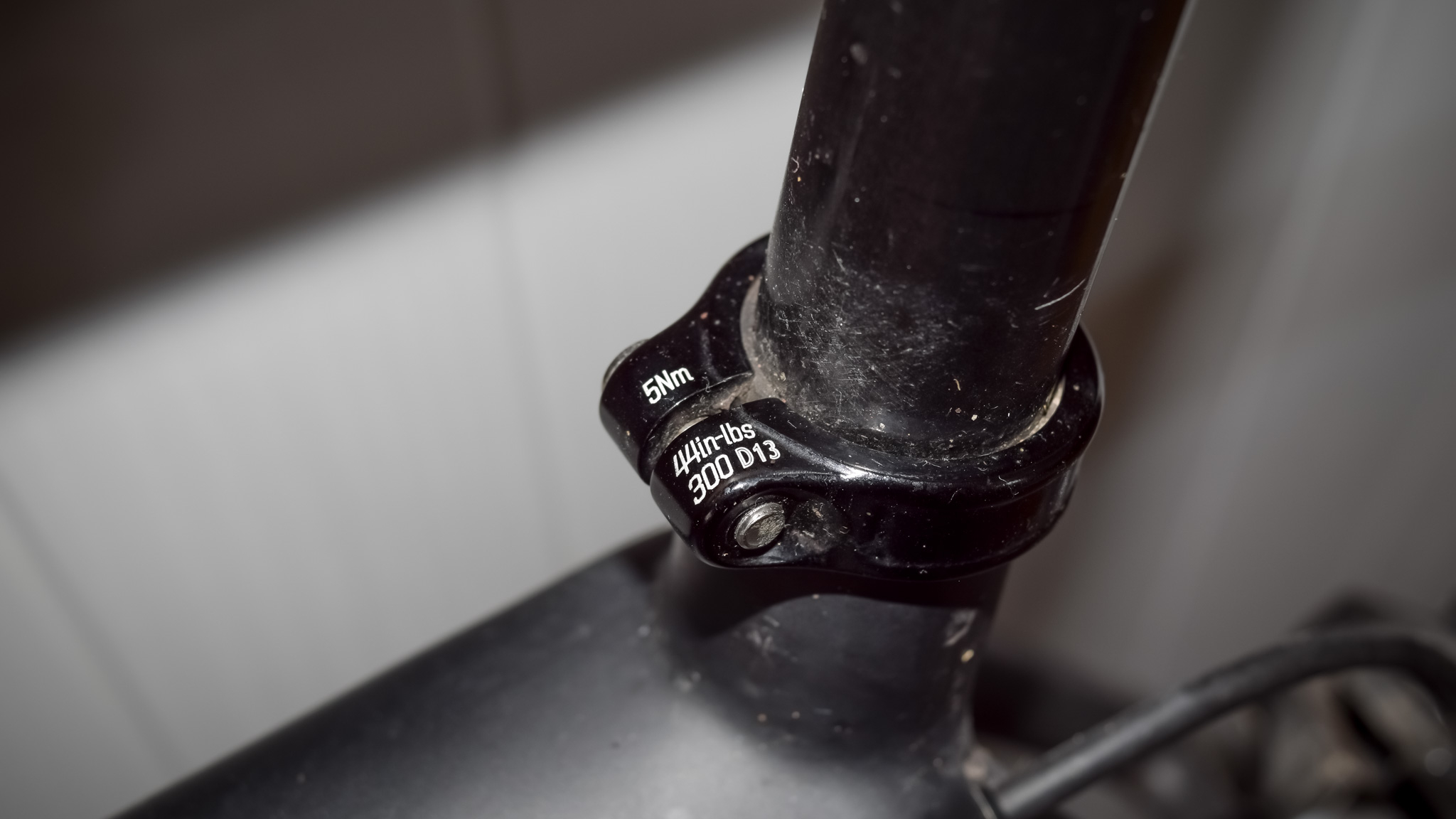
Torque wrench calibration is something we are going to be investigating in more detail in the coming months but yearly calibration checks are also featured in all of the mechanics' work.
"Our torque wrenches generally are calibrated once per year. We either send them out to their manufacturer for calibration or to a specialist that provides that service," Beyer said.
Tisma had a different answer and one that highlights the revolving door of WorldTour sponsorship partnerships. "We get new wrenches every year, so no calibration is needed for this period. However, if you are using them longer, calibration should be done."
Most manufacturers recommend torque wrench re-calibration yearly and offer this service themselves or through re-calibration specialists. An older, used and abused torque wrench may no longer be accurate and pose a risk, hence the need for re-calibration.
Steels said "Calibration is one thing I do at DBT. In fact, a couple of my daily drivers are on holiday at Snap-on being serviced now. I never did do this until four years ago when I began to see a few cranks coming loose after rides. I knew I had torqued them up but questioned my torque wrench calibration. Luckily when they came back they were all still accurate and didn’t need setting. I later discovered the crank manufacturer had some axle tolerance issues that was causing the loosening. Either way, it kicked me up the ass to annually get them calibrated to protect my back."
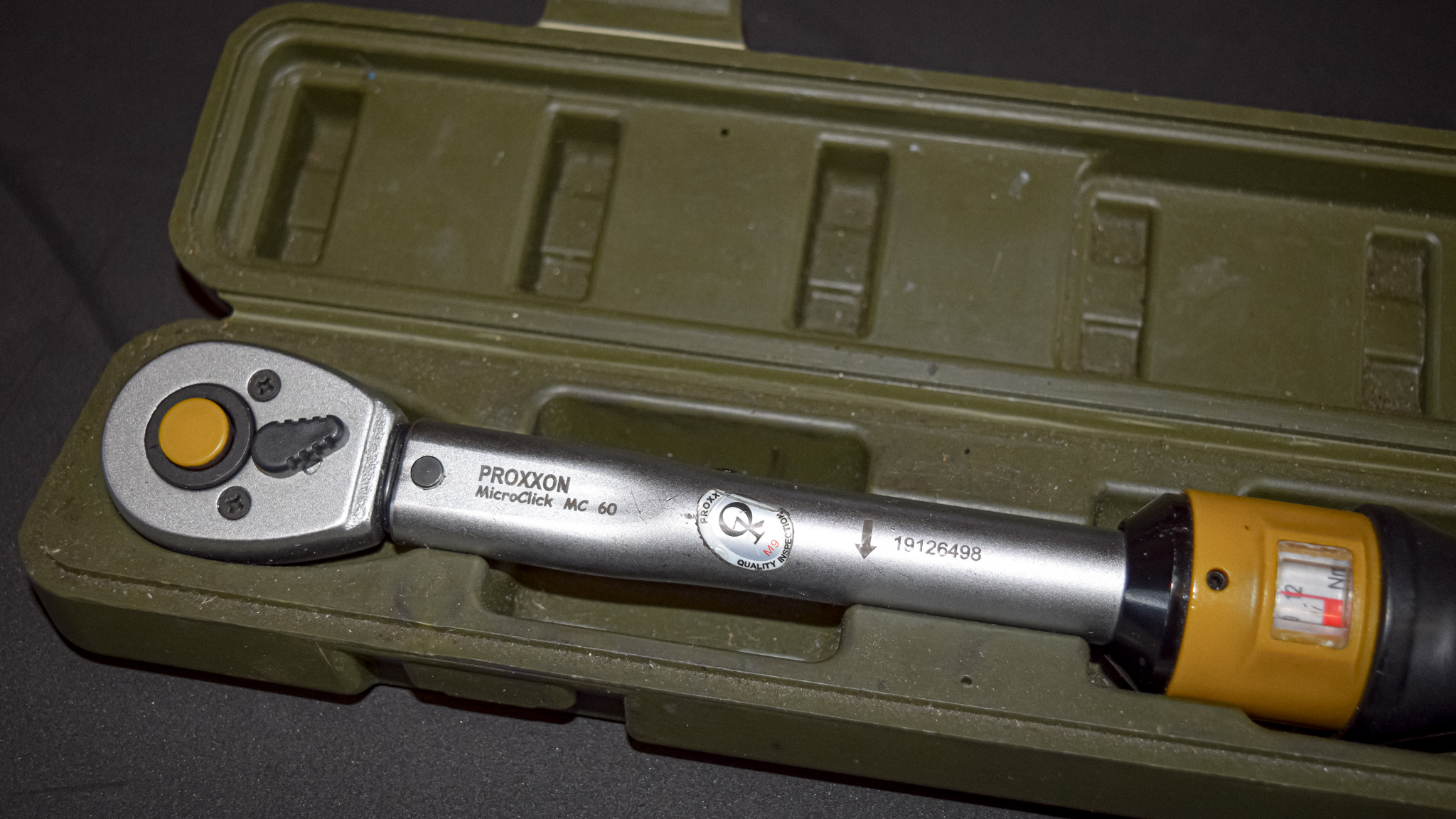
Out of pure curiosity, I wanted to know the highest torque rating the mechanics had to deal with. Fasteners in the bike world have pretty low torque ratings in the grand scheme of things, with cars and other industries seeing far bigger torque specs.
Bike mechanics Steels and Tisma had similar responses as you would expect.
"The cassette nut, it's tightened to 40-60 Nm, and I think that is the highest torque we do," Tisma said. Whilst Steels' highest number was similar "Hope Cranks, 70-75Nm." he explained.
As expected, Aircraft technician Shakespeare could go higher: "A350 engine mount bolts were torqued to 800 lbs-ft." There are several different ways of measuring torque but lbs-ft (not to be confused with ft-lbs) is about 1084nm. I've included newton meter conversions as it's the unit of measurement we see most of in the bike world and it makes things a little more relatable. Most of us will have something like 4-6nm ratings on our handlebar stems for example.
Being personally used to torquing crank bolts to around 40 Newton meters or so, I struggled to get my head around Beyer's answer, who wins this particular game of Top Trumps by a long way:
"The highest torque I personally have ever dealt with was about 26,000 ft-lbs. This was while I was employed by a Caterpillar dealer working on heavy equipment. The application for that level of torque was on a hydraulic cylinders rod nut that keeps the piston secured to the rod while travelling in the cylinders barrel."
This figure was far in excess of anything I was expecting and I believe converted to Newton Meters is about 35000nm.
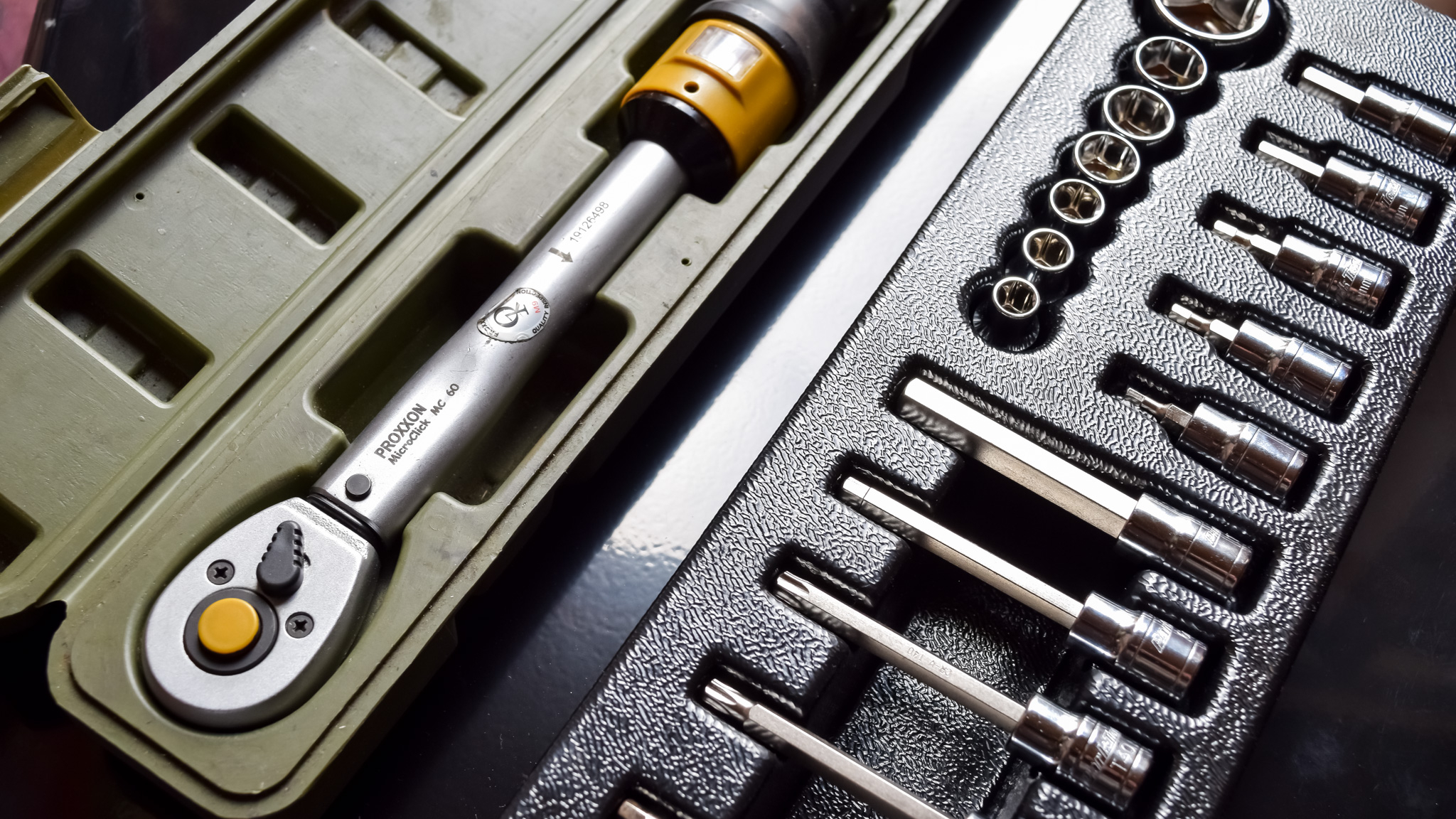
Regardless of the torque rating applied to fasteners, whether large or small, torquing them to the correct value is equally as important. Understanding what happens to a threaded fastener as it's torqued to a value helps us understand why we do it at all.
"Understanding how fasteners function helps to understand why correct torque is critical. Correct torquing of a fastener is actually stretching the fastener just enough to get the maximum clamping force from it," Beyer explained.
"Under torqued fasteners are bound to come loose under normal operating conditions due to vibrations. Over-torquing a fastener can stretch it beyond the material's elasticity. Immediately past that point of elasticity, the fastener loses its strength very very quickly."
Regardless of bolt size or torque rating, over-torquing can lead to failure and component damage, and under-torquing can lead to loosening and fasteners working free over time.
The largest takeaway from all the information and knowledge shared by the mechanics is that the reasons for torquing fasteners to spec remain the same and of equal importance regardless of whether it's to a rating of 5 Newton Meters or 35,000. Paying attention to torque ratings will provide a better, consistent standard of work and will help keep us all safe.
Thanks to all of the mechanics for their time and knowledge, and do look out for upcoming pieces on torque.