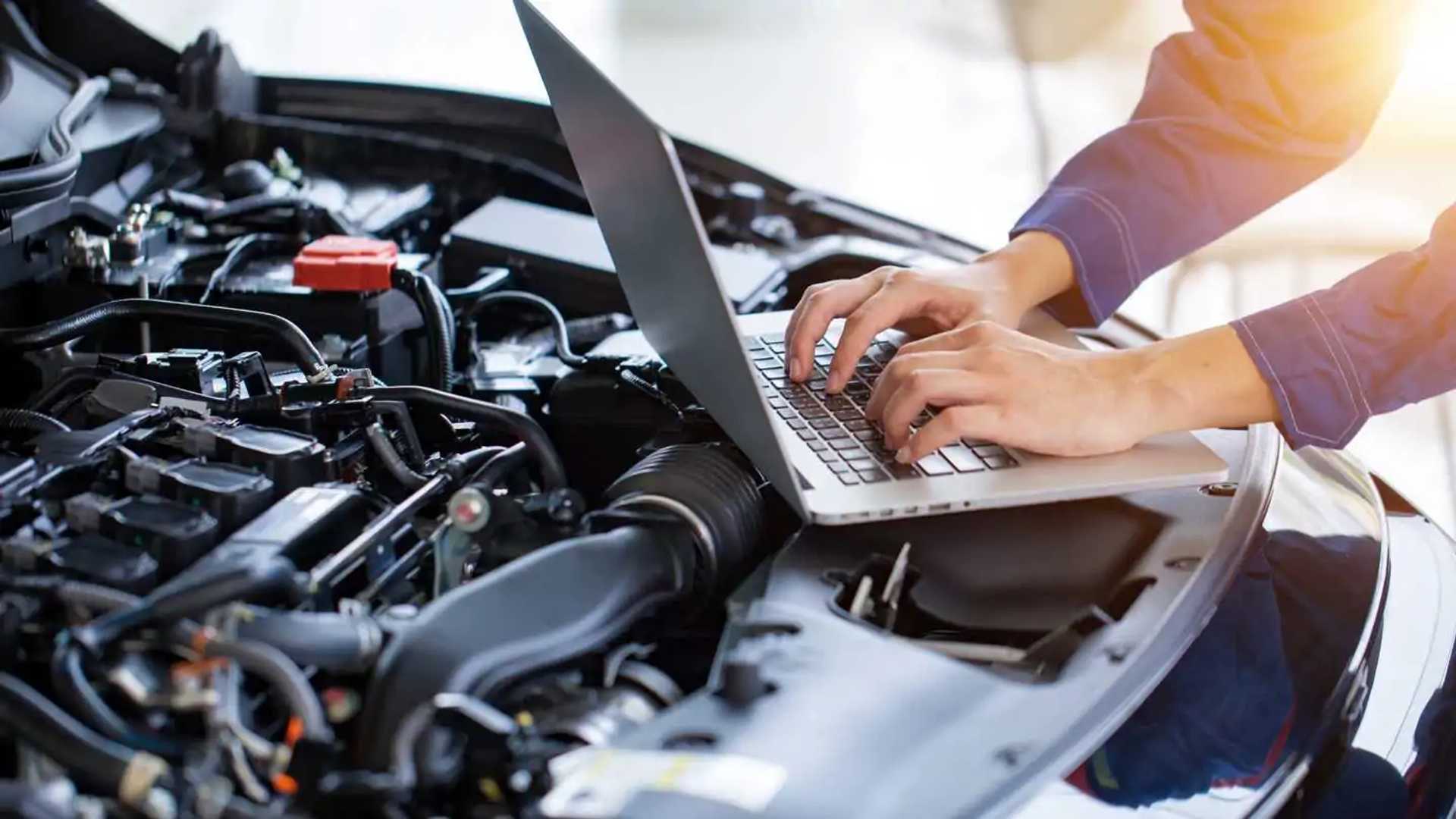
It's no secret that modern automobiles are more complex than ever. By default, that means modern automotive techs have a bevy of systems to inspect, diagnose, and repair when things go wrong. One might think plugging in a code scanner makes a mechanic's life carefree, but a new study reveals the opposite; mechanics suffer considerable stress. In fact, half want to quit the business completely.
That's the takeaway from a recent study by Wrenchway, which surveyed techs working in a variety of fields, including automotive and diesel repair. A small sample of techs in related fields such as auto body repair were included, and the study received feedback from students as well as shop managers. Wrenchway posed questions on subjects ranging from pay to time off, tool allowances, benefits, commute times, and career paths. The biggie was whether respondents had considered leaving the industry, to which a whopping 49 percent said yes.

Where does the dissatisfaction come from? According to the study, stress over pay is the leading factor. Physical and mental demands accounted for a smaller percent, followed by tool costs. Poor management, lack of respect, and benefits also factored. Digging deeper, the study found differences between automotive and diesel-focused techs. Sixty percent of auto techs think about quitting versus 45 percent in the diesel fold, but both point to pay-related stress as the predominant factor.
This brings us to the debate of hourly pay versus flat rate. In short, many shops pay employees a fixed rate per job, regardless of how long it takes. This is a sticking point according to the survey, which found 65 percent of techs would prefer either a straight hourly scale, or an hourly scale with production bonuses. Nineteen percent favored a flat-rate scale with a 40-hour guarantee, and just 10 percent said they wanted a flat rate.
Tool costs and training also factored. Techs generally have to pay for their own tools, and with such investments easily topping $10,000, the study says it limits young techs looking to get started in the industry. As for established professionals, keeping up with ever-changing vehicle systems requires considerable training. Some shops pay for that training, others don't. So this isn't a field where you get a job and simply get to work. Techs are largely responsible for investing their own cash into equipment and training.
The survey paints a rather bleak picture of a critical industry. We did some fact-checking on our own to see if anecdotal experience backs up the data, and unfortunately, it does. For starters, we found nobody at automaker dealerships willing to chat with us, be it managers or mechanics. The folks we did speak with are off-the-record, and they talk of tough times in this industry. A mechanic based in New Jersey with eight years on the job confirmed he's on the fence about leaving, pointing to pay and stress as big factors.
"I'm not super against salary pay," he told us in an interview. "It puts less stress on technicians and it also shows that there’s some sort of trust between the owner and the technician. That’s a problem; a lot of private shops and dealerships are like revolving doors for technicians. They go in, they’re there for six to eight months, and they’re gone, off to the next job."
This tech went on to say that if mechanics find ways to be more efficient on repairs, the flat rate is reduced, basically cutting their paycheck. But it doesn't work the other way. If something takes longer, the mechanic literally works for free.
"They’re making up these repair times and not taking into account locations, like the East Coast where rust is prevalent."
With regard to trust and respect, we spoke to a tool dealer in the Southeast who shared a similar story. Having visited repair shops and mechanics for 10 years in his job, he says it's all about how management treats their employees.
"I'd say the survey is pretty accurate, being 50/50 wanting to quit," he said. "I have one bad dealer that I visit, they had 50 techs a year and a half ago and now they're down to 20. Good techs are hard to come by, and places that respect them will pay them well to stay. This dealer charges $320 per hour on labor, but for 'b work' like brakes or oil changes, the techs basically make $20 an hour."
On the management side, we chatted with a small shop owner in southwest Michigan who confirmed that finding good techs is his biggest challenge.
"I heard from a teacher at a tech school recently, in a class of 50 students, only three or four actually go into their fields when they graduate," he said. "So I'm left with training young techs and finding out many don't want to work hard. Of the employees I have found in the last 10 months or so, more than half left and went into something completely different."
With automotive technology evolving on an almost daily basis, the study and our follow-up interviews suggest the world of auto repair needs to evolve, too. Do you have any mechanic stories to share? Jump into the comments; Let the world know what works and what doesn't in this vital industry.