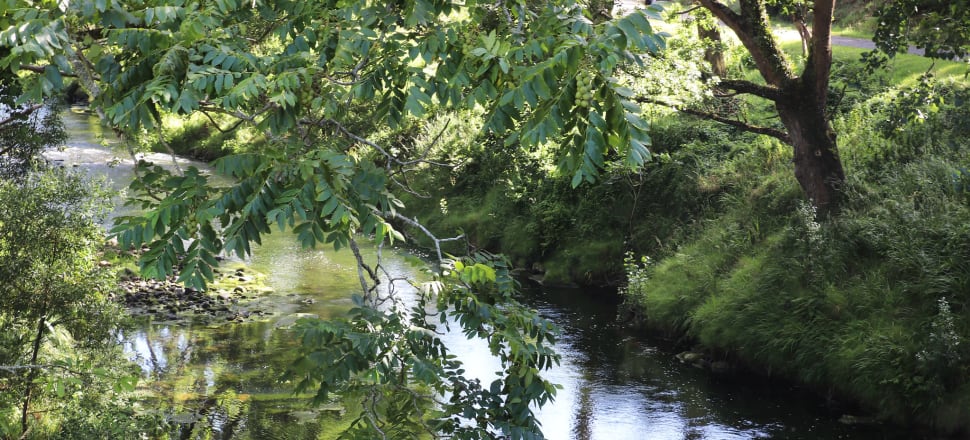
Wastewater, whether urban or from farms, may not look or smell good. But to University of Auckland researchers, it can be the source of agricultural gold.
Engineers at the University of Auckland are designing way to clean phosphorus from waste water and turn it into fertiliser - a process with both environmental and financial benefits
Wastewater, whether urban or from farms, may not look or smell good. But to University of Auckland researchers, it can be the source of agricultural gold – well, a whitish-goldish mineral called struvite, anyway.
Phosphorus-rich struvite not only makes a great slow-release fertiliser, recovering it from wastewater helps clean up our waterways.
Senior Lecturer Wei Yu and Research Fellow Bing Li of Chemical and Materials Engineering at the Faculty of Engineering have been researching phosphorus recovery for years.
They’re now ready to take the next step and pilot their process on a commercial scale. They say it will not only be good for the planet, it will also make financial sense.
Phosphorus is essential to all life forms. However, it’s associated with major problems.
While a little phosphorus helps plants grow, too much is terrible for waterways. Plants only take up so much phosphorus. The rest, along with other nutrients in fertiliser, such as nitrogen, runs off when it rains and makes its way to lakes, rivers and the ocean.
Nutrient pollution can cause huge algal blooms, which reduce light and oxygen in water bodies and result in the mass death of fish and other life. Algal blooms can be toxic, which makes water dangerous for swimming and for consumption not only by humans but also by other animals such as birds and dogs.
Fertiliser runoff is an especially big problem in New Zealand. “New Zealand has an average phosphate fertilizer application rate two to three times higher than Europe and 1.5 times to two higher than Australia, resulting in over 80 percent of phosphorus being lost to the environment,” says Li. “Two-thirds of our rivers have a problem with phosphorus and half our monitored lakes have poor or very poor water quality.”
New Zealand is a major purchaser of phosphate from the Western Sahara, where sales of the mineral are helping to fund a bloody war.
Another problem is that phosphorus is a non-renewable resource, meaning the world could run out of mineable phosphate.
New Zealand has few phosphate rock reserves, so it imports by far most of its supply. It’s the only major purchaser of phosphate from Western Sahara – where sales of the mineral are helping fund a bloody war.
Despite the lack of phosphate in New Zealand, there is potentially a rich source of phosphorus here – human and animal waste.
It’s long been known that manure can make effective fertiliser. The problem is, spreading manure or on fields can result in the introduction of harmful bacteria and contaminants such as heavy metals. What’s more, compared to chemical fertilisers, manure-based fertiliser runs off far more easily.
Extracting pure phosphorus from wastewater isn’t easy. Struvite, however, forms readily – so much so that wastewater treatment plants have to fight struvite build-up.
Struvite is rich in nitrogen, phosphorus and magnesium, all of which are necessary to help plants grow. Using struvite as fertiliser isn’t a new idea and has been proven effective. In fact, struvite is in some ways superior to chemical fertiliser, because it dissolves slowly. This slow release prevents excessive nutrient runoff and may lower costs to farmers because it doesn’t have to be applied as often.
Smarter and better
Yu and Li aren’t the only scientists working to extract struvite from wastewater with the objective of reusing it as fertiliser. However, they believe they’ve come up with a better process. “Although there are several industrialised struvite recovery units in Europe and Canada, the low product efficiency and high operating cost make their economic payback weak,” says Yu. “The cost of current processes significantly limits application at full scale. Also, few of the people working on struvite precipitation focus on the quality of the recovered struvite.”
In developing their process, Yu and Li have put product quality, process efficiency and process economics at the centre of their work. “Our research is to use process systems engineering knowledge to address these concerns,” says Yu. “With our colleague Brent Young, we use computer-aided models to design, control and optimise the process.”
Precipitating struvite from urban or agricultural wastewater is a little like cooking, says Li, who is now an assistant professor at Tsinghua University in China in addition to continuing work with Yu.
“If you’re cooking, you might add some salt and use a fork to stir it. It’s like that. For struvite precipitation, you start with wastewater as the feed stock and you add magnesium. You control the pH and the amount of magnesium, then you stir for 15 to 30 minutes under the right conditions, and you will struvite crystals. You can separate them from the wastewater just using sedimentation.”
Admittedly, it’s not always quite that simple. If the concentration of phosphorus isn’t high enough, the process doesn’t work. That’s why the researchers developed a phosphorus absorption process to increase the concentration of the influent so it can be sent through the crystallisation process. This process enables them to treat water with a lower phosphorus concentration than existing units can.
Another process the researchers have developed minimises impurities such as heavy metals. Because heavy metal precipitate begins to form earlier than struvite, the step-by-step precipitation of heavy metals and struvite is possible. “The wastewater is fed into a pH adjusting tank for heavy metal precipitation, followed by a settlement tank for separation,” says Yu. “The pH is then adjusted for struvite precipitation and sedimentation. Our results prove that this type of pH adjustment can significantly reduce the co-precipitation of copper and zinc.”
“If you don’t have phosphorus, you don’t have food, and if you have too much phosphorus, you don’t have clean water. That’s why we’re doing this.” - Bing Li, University of Auckland research fellow
Yu and Li have optimised their process to keep costs low. The equipment required is inexpensive, with the largest tank required only about half a metre long and wide, with a height of about two metres. The magnesium and calcium needed to make it work can be obtained from seawater or, in China, from ash. The cost of recovering phosphorus from wastewater treatment plants is already the same as the cost of simply removing it. In fact, using their process as part of overall wastewater treatment would end up costing about the same as current wastewater treatment does now, says Li.
“Also, if you compare the cost of producing fertiliser, the cost is around 80 cents U.S. per kilo to produce elemental phosphorus, but for phosphorus recovery, it’s 30 cents. That means it’s more than a 100 percent cost reduction to recover phosphorus rather than produce it.”
The researchers are currently working on building a pilot plant in China. Though not yet assembled due to Covid-19 restrictions there, they anticipate it will soon be able to treat two to three tonnes of wastewater a day. The resulting clean struvite pellets can be sold as fertiliser, which is one way of making the process financially sustainable, even profitable.
The other possible revenue stream could come from the widely used systems where polluters have to pay to pollute. If water pollution can be reduced at the source – say, a livestock operation – the business could save money by paying for the struvite recovery process rather than the emission fees. Governments might also be willing to subsidise the process because it would contribute to the goal of reducing water pollution, says Yu.
If all goes well with the pilot plant in China, Yu and Li say their technology will be ready to commercialise internationally within a few years. First, though, the researchers are looking for support and partners to build a pilot in New Zealand. Livestock farmers interested in reducing water pollution could be partners, as could fertiliser companies. Yu and Li are also looking for government support because their work could help meet environmental goals.
“Phosphorus is needed by everyone – animals, plants, human beings,” says Li. “If you don’t have phosphorus, you don’t have food, and if you have too much phosphorus, you don’t have clean water. That’s why we’re doing this.”