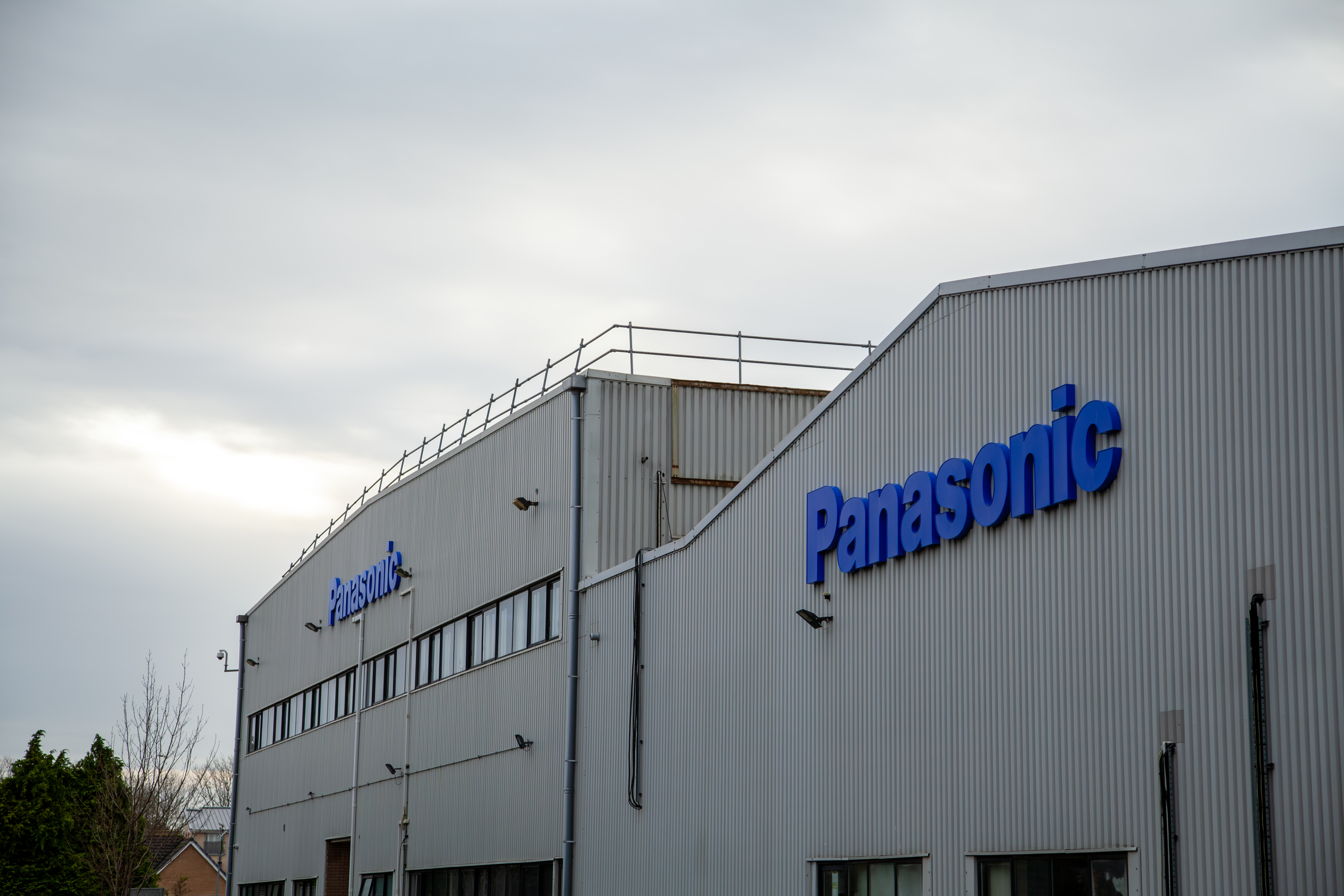
TechRadar Pro was recently invited to the 50th anniversary of Panasonic’s Cardiff factory, where the company revealed a new leap forward for sustainability.
By retrofitting the site with pioneering hydrogen cell technology, Panasonic has built a fully self-sufficient production line.
Panasonic’s microwave oven assembly factory on the outskirts of Cardiff has been running since 1976, and is now being fitted with state-of-the-art hydrogen fuel cells, dubbed Panasonic HX, powered by green hydrogen, solar PV, and battery storage - just in time for its 50th birthday.
The first of its kind in Europe
“This is very much a beacon project for us and as far as we're aware, we are the only ones really with such an initiative with hydrogen fuel cells in using it with our proprietary EMS system,” Managing Director Robert Blowers told TechRadar Pro.
The technology is only currently in use in Japan, where Panasonic has already invested over £100 million into renewable energy projects. The project in Cardiff was a £20 million venture, and comes with significant education investment for the 400 employees already working on-site.
“I think that this facility could be used as a very strong education conduit, not necessarily just (for) today and business leaders today, but (for) the next generation. Panasonic has a very ambitious green impact target, so by 2030 all 250 global plants are planned to be net zero,” noted Blowers.
Production at the plant is set to be much greener, with electricity sourced renewably, from both in-house solar energy and from UK produced hydrogen.
The introduction of Panasonic HX is part of wider commitments by the company to sustainable and green energy, and one it hopes will be introduced in manufacturing sites around the world.

Ultra-efficient
The plant is powered by solar panels and green hydrogen, which is obtained through the process of the electrolysis of water. The key to this is the process is entirely powered by renewable energy, so is non-polluting and is the cleanest form of hydrogen.
Panasonic’s 21 5KW fuel cells have a 95% energy efficiency rate when converting green hydrogen into electricity and heat energy.
Efficiency is the name of the game all round, as the heat generated by the hydrogen cells, as a by-product of the electricity production, will be used to heat spaces and domestic hot water - and with the onsite electricity production, the factory will benefit from a more reliable electricity supply.
Why Wales?
If you’re raising your eyebrows at the thought of solar panels in Wales, you’re not alone. But Cardiff’s volatile climate is a feature, not a bug - "If you can succeed in Wales, you can succeed anywhere in the world," joked Hiroshi Suzuki, the new Japanese Ambassador to the UK.
There are a few reasons Panasonic chose Cardiff, Blowers adds. There’s an image of sustainability that is tied to new contemporary buildings, so the transformation of a 50 year old site into a beacon of green energy is helping Panasonic create a framework for others to follow.
South Wales is also home to a ‘green hydrogen cluster’, meaning the hydrogen can be sourced from a local partner, minimising the carbon footprint of transportation. There’s a ‘movement’ in the UK and Europe, Blowers says, that values sustainability, an appetite for renewables that makes Cardiff the perfect fit.
Building a ‘hydrogen society’
Whilst this is only a proof of concept so far, Panasonic is so confident in the tech, that it already has plans to retrofit a similar site in Germany, and is scouting for potential partners in Europe.
As well as its commitment to renewables, Panasonic is working towards reducing its CO2 emissions from its operations to ‘virtually Net Zero by 2030’, and aims to contribute a total of 110 million tonnes of its own emission impact through reduction and avoidance of CO2 emissions.
“This decentralised approach to energy demand management increases the company’s energy resilience in a volatile market. By integrating an energy management system and storage batteries, the factory will be able to scale its energy needs when ramping up productions, for example,” the company said.
Construction for this Energy Management System (EMS) started in August, and the proof of concept is already in operation, so although it’s not ready for a full-scale roll out, it can be adopted quickly.
Could this be the future of sustainable manufacturing? Panasonic certainly seems hopeful. CEO Masahiro Shinada hopes the site will be seen as a ‘birthplace of innovation’, and that Panasonic can lead the way in building a ‘hydrogen society’ and laying a foundation for a decarbonised future.
“So by 2050 we want to help society reduce 300 million tonnes of carbon emissions through new and existing technologies," Blowers concludes. "Now that's not only about building a group of concepts here, that's about educating the next generation of business leaders and the next generation of students in sustainable technologies. So I think that's an area where it's very exciting honestly speaking from a developmental point of view.”
You might also like
- Check out our pick of the best endpoint protection software
- Many UK workers still aren't using AI at work
- Take a look at our best malware removal software choices