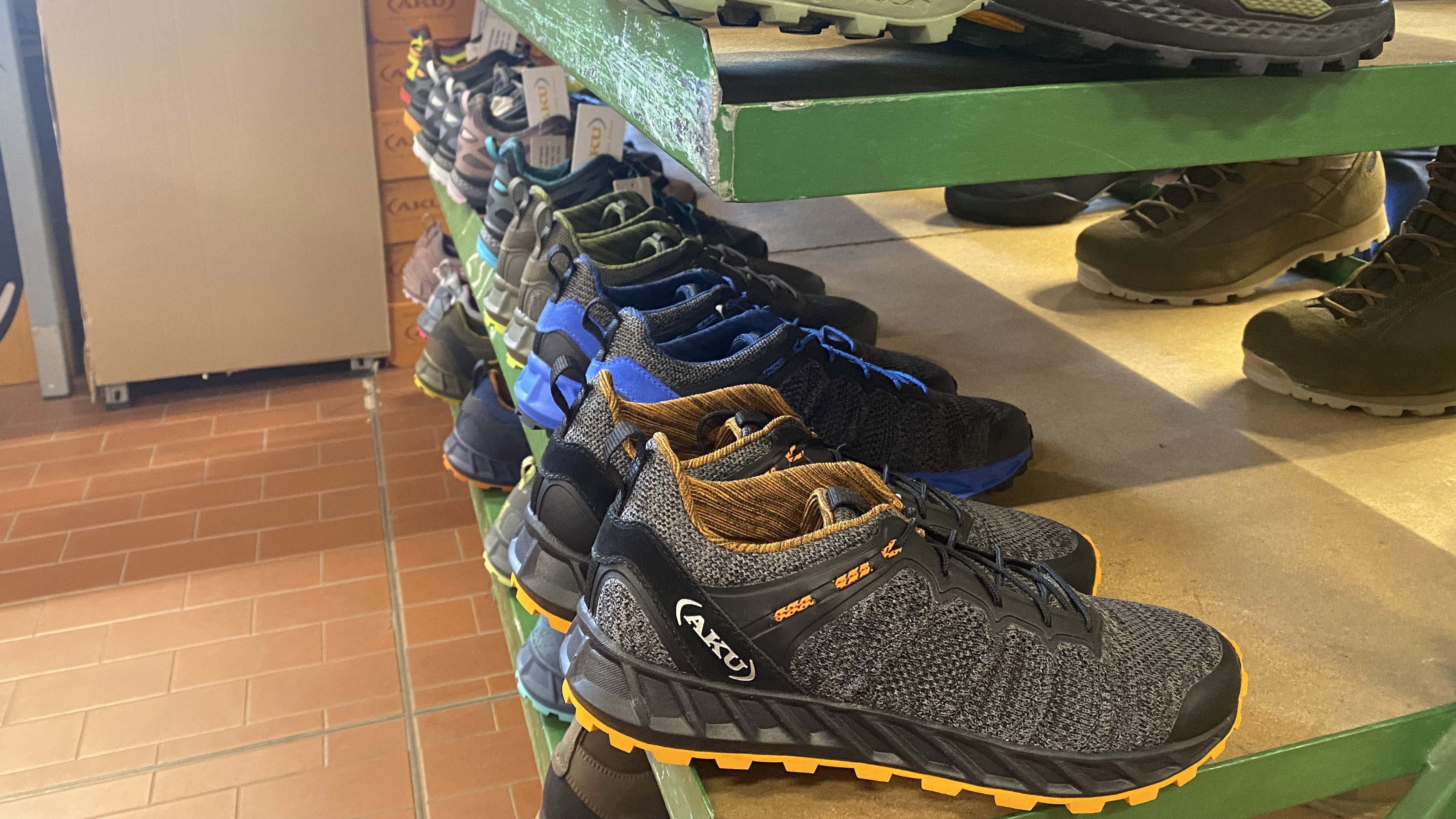
Montebelluna is an unassuming city between Venice and the magnificent Dolomites in the Italian province of Treviso. With layered, mountainous walls backed by snow-capped peaks to the north, and flat plains dominated by the wide Piave River and dotted with vineyards, it’s a fair setting, where we lay our scene. The region is rightly proud of its heritage and we have it to thank for prosecco, radicchio and tiramisù.
This part of northern Italy also is home to more than its fair share of premium hiking and mountaineering boot manufacturers. This family of close-knit brands includes the likes of Aku, Scarpa and Asolo. In conversation with Guilio Piccin, Aku’s Sustainability Manager, he told me that there’s little that’s private between these hiking boot heavyweights. News spreads fast across the prosperous region due to the shared network of tradespeople who supply the leather, laces and components.

So, there’s something of an open culture in the region, with only the most important trade secrets guarded closely. It was in this spirit that I was invited, along with several other writers, retailers and influencers, to spend a few days with master hiking boot manufacturer Aku. We explored the spectacular Pale di San Martino mountain range, tested the newest and most sustainable version of the classic Slope hiking boot, learned all about the brand’s vision for responsible manufacture, and were taken on an eye-opening tour of the Montebelluna factory.
It all starts with the last
At the heart of Aku’s HQ is a large conference table surrounded on three sides by walls lined with footwear, showcasing its current range of shoes and boots. There's everything from stylish ‘mountain inspired’ leisure wear to the Aurai, a highly technical winter mountaineering and ice climbing boot.
Guilio, our host for the day, talked us through Aku’s commitment to the responsible manufacture of boots where the environment is concerned. Aku has reviewed practices right across the company to ensure they are as sustainable as possible going forward, as well as pioneering more environmentally friendly designs in its footwear.
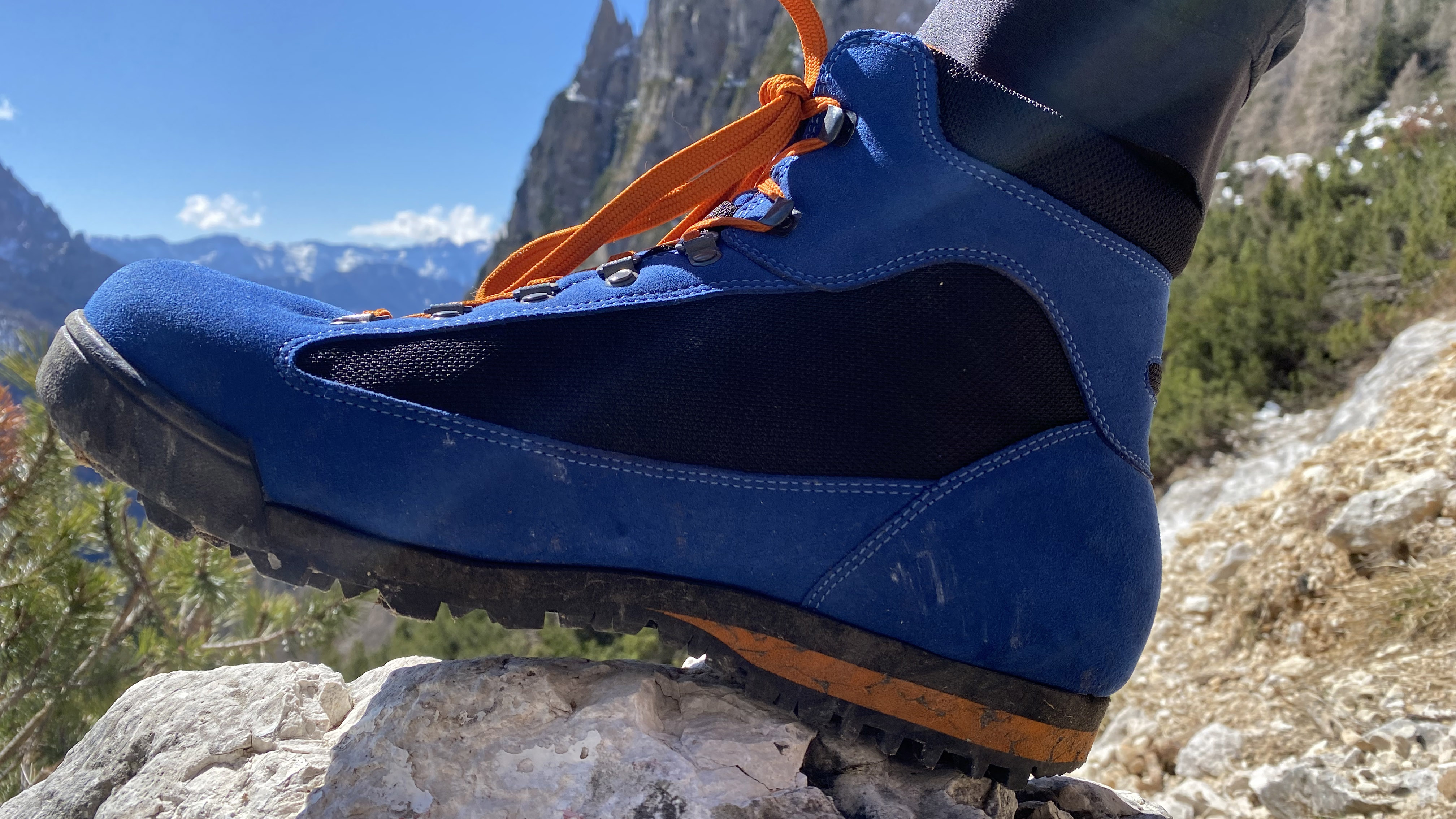
For example, the V-Light version of the classic Slope boot that we had tested in the mountains the day previous has a 100% recycled microfiber upper, a Gore-Tex lining laminated with 99% recycled yarns and recycled polyester laces. The upper is not only lighter than suede, it negates the need for leather, cutting the tie to the beef industry and the use of animal products. This is the reason for the ‘V’ in the name, as the shoe is ‘vegan-friendly’.
The Slope is one of Aku's most successful models, with over 30 years of popularity and a solid reputation as a quality hiking shoe. It shares the same last as much of Aku’s hiking footwear. The importance of a last can't be understated. So, what exactly is it?
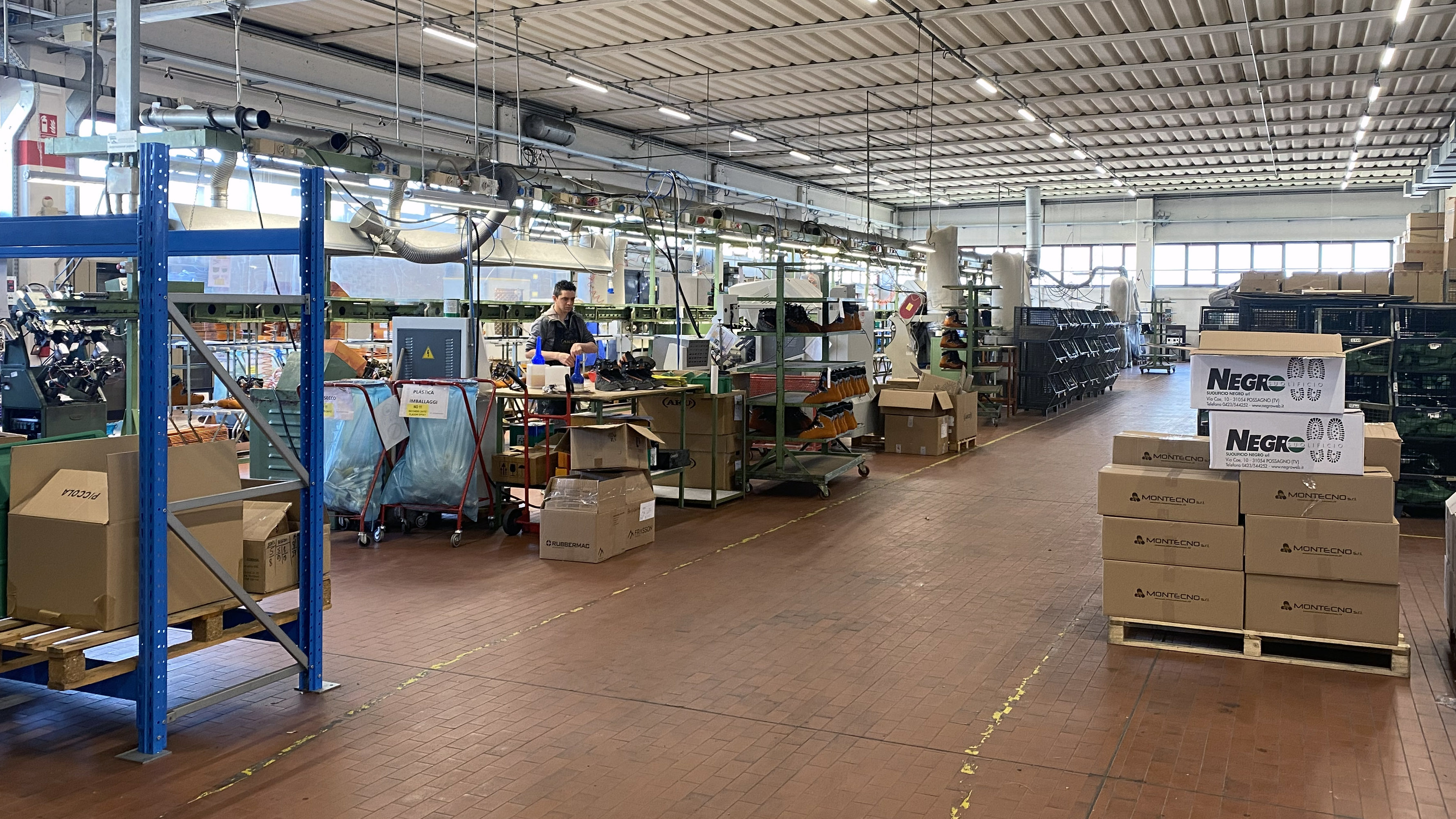
The last is the foot-shaped mold at the heart of the shoe, and forms the basis for the design process. The word is English in origin, coming from the Old English ‘least’, which means footprint. Just as no two feet are the same, every shoe manufacturer will have its own unique lasts, forming a large part of the character and, importantly, fit of its shoes. They’re typically made from hardwoods, cast iron, and high-density plastics.
Aku’s last, originally developed by founder Galliano Bordin, is the foundation for its ELICA natural stride system. With this, boots match the biomechanics of the foot to provide even weight distribution, stability, better arch support and a more natural hiking motion. Interestingly, Aku's last features opposite inclination between the forefoot and the heel for a dynamic stride. The video below explains this in more detail.
On the design floor
Upstairs, in a room full of colorful prototype boots that we were half-jokingly told were 'classified', a few of Aku’s leading designers sit dreaming up hiking shoes on their iMacs and scribbling new designs onto versions of the last. This is where the boots of the not-too-distance future are born, virtually and in prototype form. The walls are covered in schematic style graphics of Aku boots, while the bookshelves are full of tomes on boot design and the upcoming color trends to watch out for.
Once the design has been nailed down, the production begins, starting with the upper. Back on the factory floor, we are met with the people whose job it is to make sure the various design elements come together and fit onto the last. One glance at the computer software they use to do this reveals the many layers and components that go into a hiking or mountaineering boot. Complicated doesn’t begin to describe it and we’re getting a real appreciation for the intricacies involved.
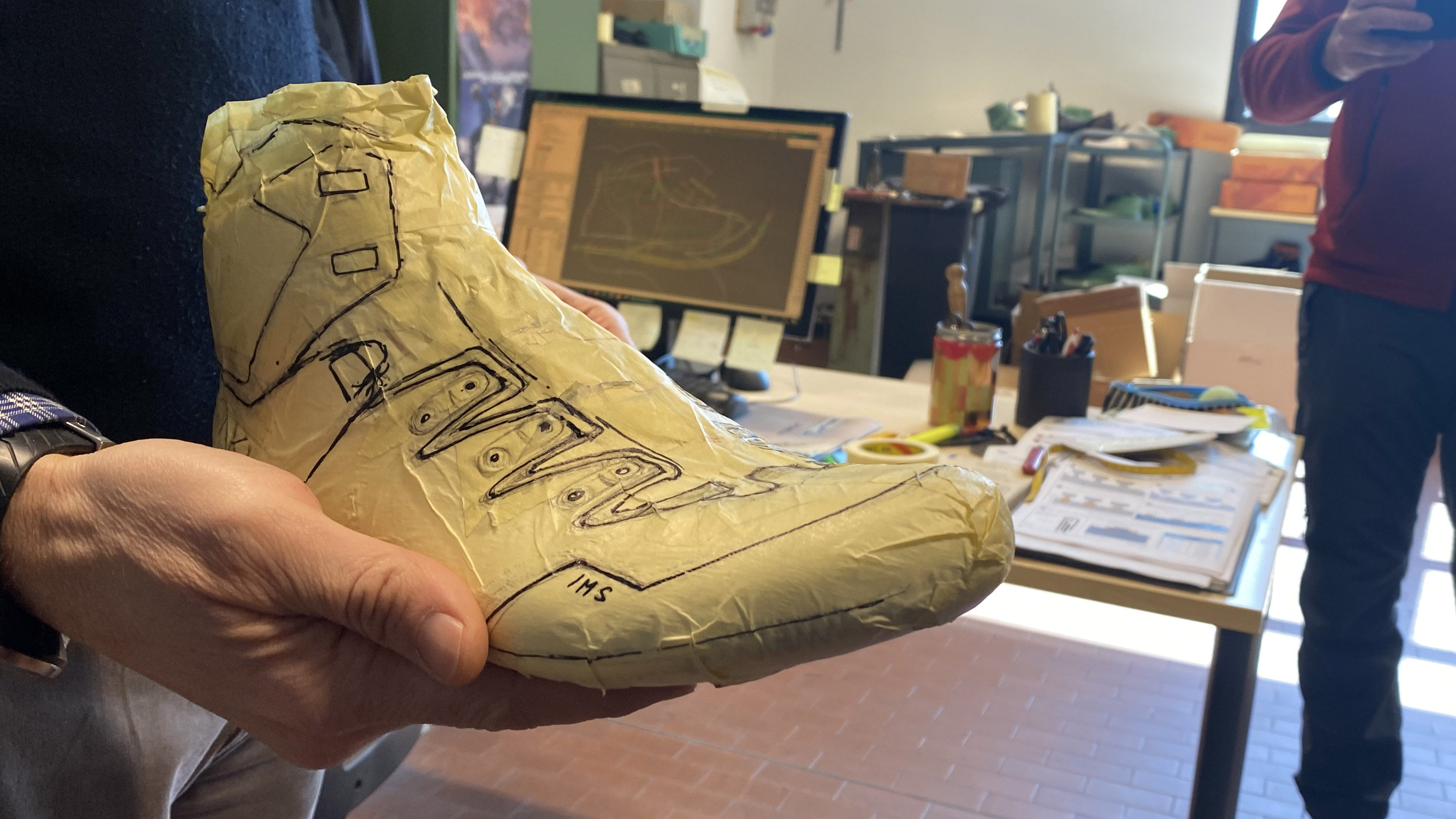
Upper cut
Measurements approved, it’s time for the various elements to be cut to size. The elements of the upper are mapped onto huge sheets of fabric, packed in closely together, so that they can be cut with minimal waste. It’s great that brand have clearly prioritised these kinds of practices and good for us to see everything Guilio was talking to us about earlier in action.

The Gore-y details
Next, we are treated to seeing how the inner lining of the boot is put together. This is a critical part of any waterproof hiking footwear, as it's where the Gore-Tex lining sits – the bit that keeps water out. The Gore-Tex layer is glued between two fabric layers, basically the meat in a sandwich. Aku’s patented Air8000 technology is used here, which involves applying the glue in a lattice, thus increasing breathability. Gore-Tex lab tests suggest this approach makes the bootie over 11 times more breathable.
A ‘bootie’ – the liner that sits inside a hiking shoe – is then carefully, yet efficiently, stitched into the correct shape on a sewing machine by a skilled factory worker. Of course, the stitched area couldn’t possibly be water-tight, so the bootie is then taken to an impressive machine that applies Gore-Tex tape over the top of the stitching.
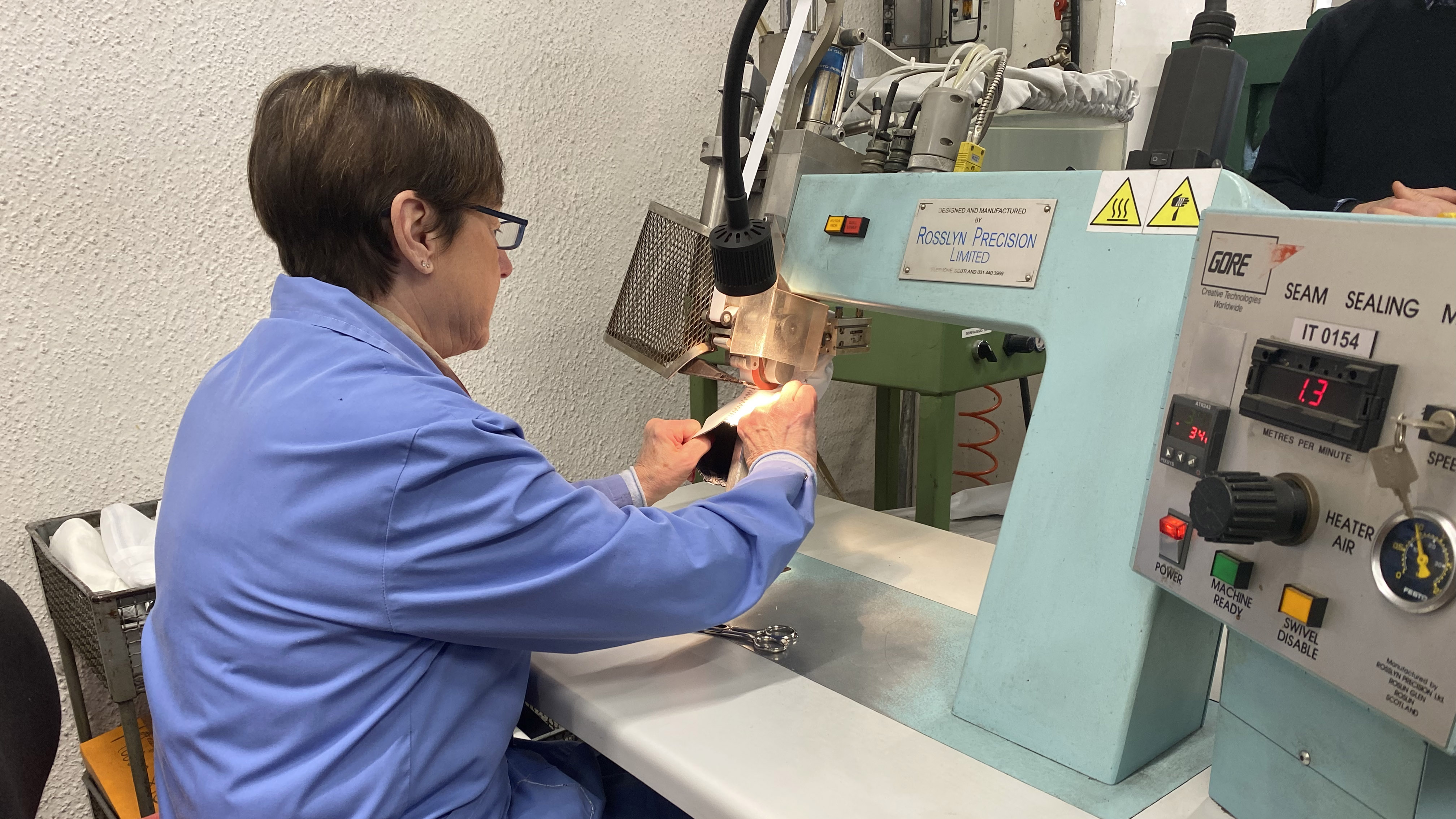
Tape applied and with a satisfied look on her face, the factory worker then takes us over to what at first glance looked like a fish tank, but is actually designed for some bootie dunking. Quality control is crucial at this stage, as it would be galling to get right to the end of a boot’s production only to find there was a leak in its inner bootie.
So, inflated with air like a balloon, the bootie is submerged to see whether it's compromised or whether it's OK to continue the journey along the production line. Hurrah! This one is indeed watertight. Had it not been, we’d have seen air bubbles rising from any weak spot in its lining.
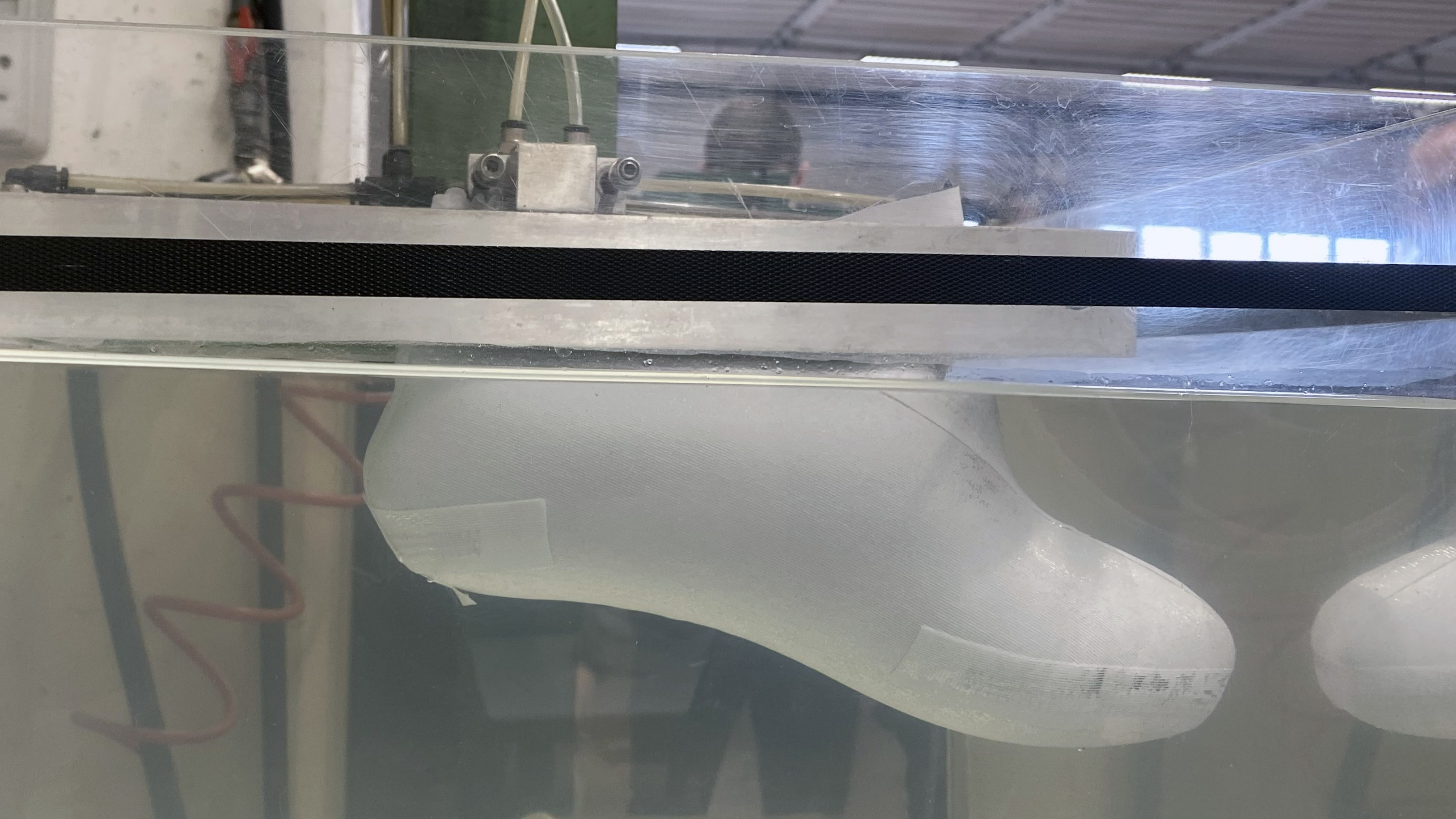
Craftspeople at work
One thing that really struck me about the whole process was the craftsmanship. Far from the automated car-style production line I had expected, there's loads of skilled, manual work on display. From the careful stitching together of the upper to the attachment of protective rubber rands and the Vibram outsole, it is done all by hand.
Sure, there are machines of varying levels of complexity used along the way for certain processes, but everything is operated by a person. There's never a moment where a boot was left to an automated fate. Every one is always under the watchful eyes of the craftspeople at work.
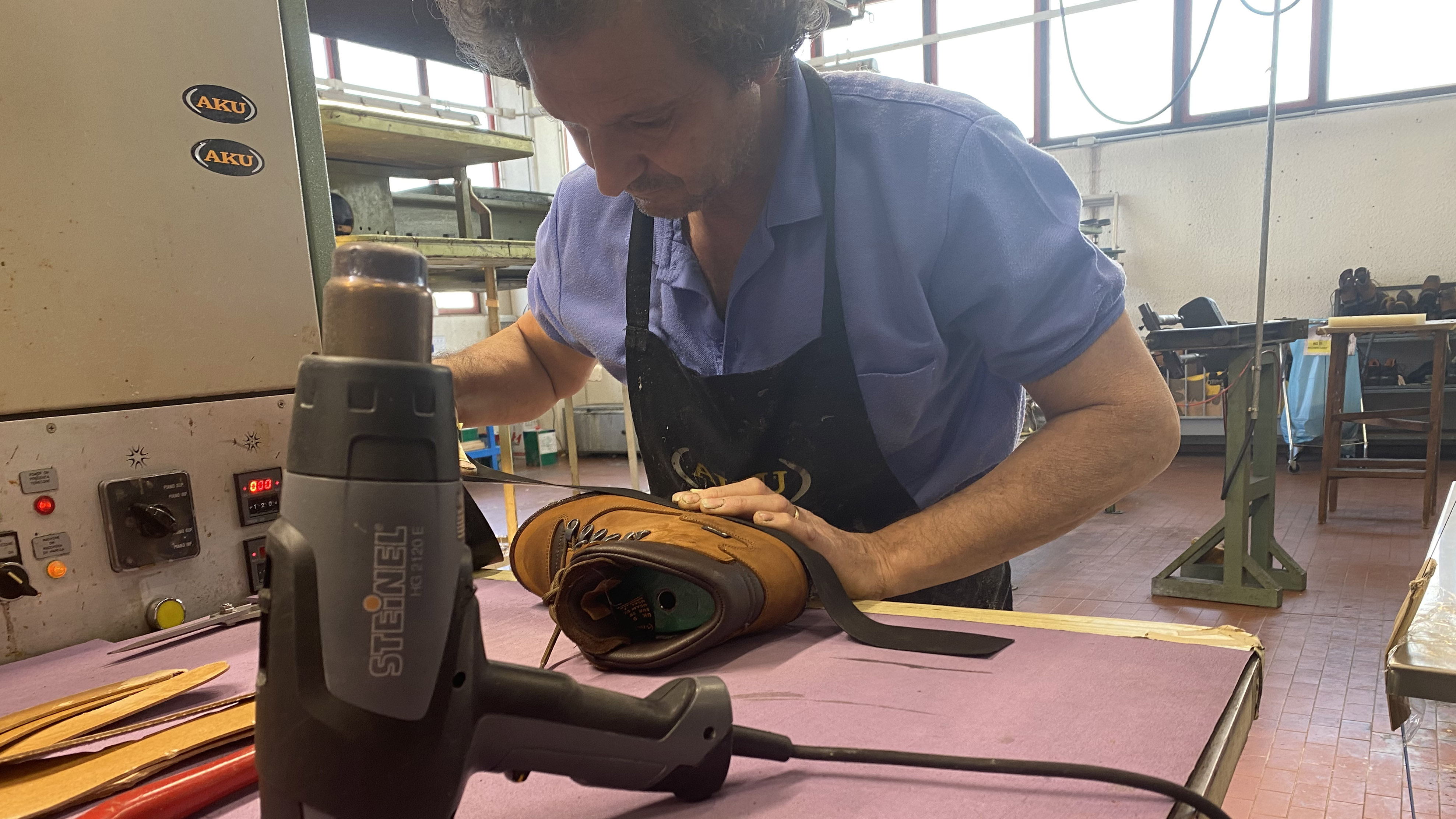
My personal favourite came next: a huge device that looked like what I’d expect if you opened up Optimus Prime’s torso to reveal all the mechanics within. With several dials, a couple of access keys dangling down and a big red and yellow emergency stop, it definitely looks the business. It's called the Challenger, and is a machine that is used to wrap the shoe's upper tight around the lasting board and two-density midsole before fusing them together.
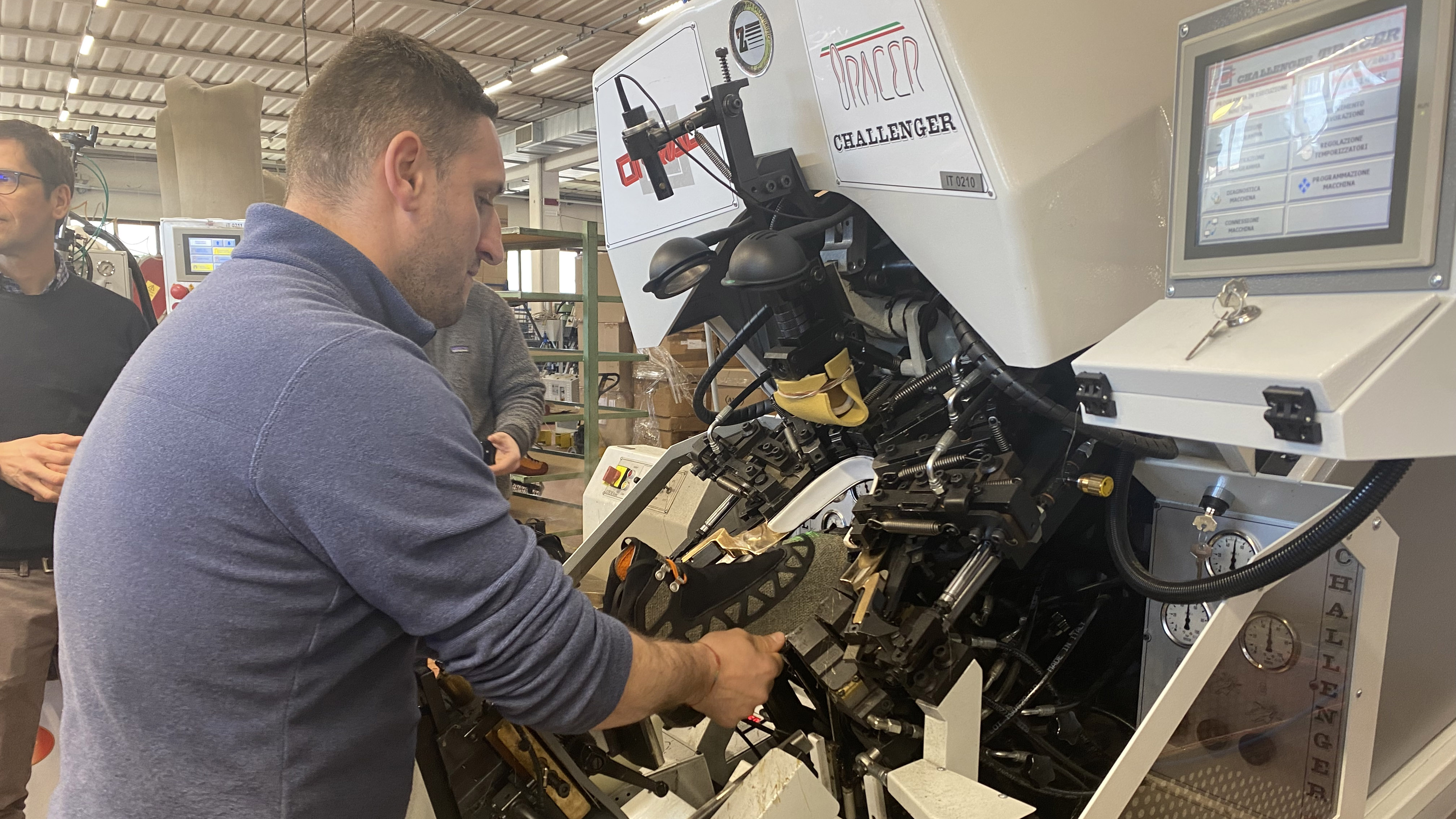
After this, the process of fusing the boot with its Vibram outsole and protective rubber rand is carefully completed, and the boot is pretty much ready for the trails.
An organic product as perfect as our feet
The tour of the factory had been a real eye opener. Looking at the completed boots at the far end of the production line, I now couldn’t believe how perfect they looked having seen the handcrafted way they had been put together. I’d always envisaged machines pumping out thousands of products identical products a day, whereas the reality was unique but masterfully finished products that numbered in the low hundreds per day.
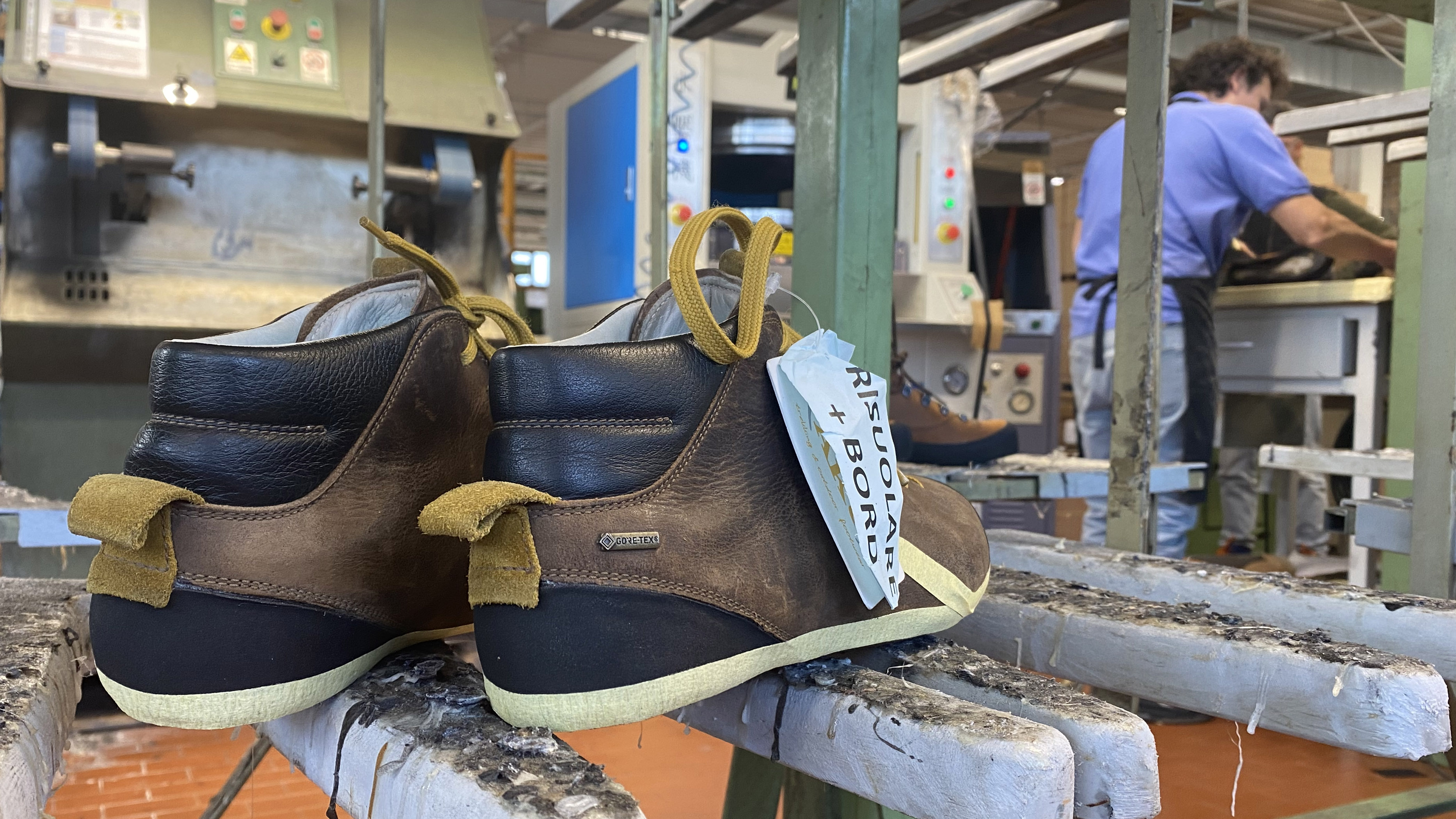
It’s given me an appreciation of how much of an art this kind of boot making is compared to clothing and gear that are, for the most part, based on symmetrical, mathematically simple foundations. The foot is an asymmetrical, organic shape and therefore, the design and manufacture of quality boots has to match this complexity, which is something difficult to attain unless overseen by craftspeople, such as those in the Aku factory. In this age of automation and artificial intelligence, it was a breath of fresh air.
- The best hiking shoes: lightweight footwear for spring adventures