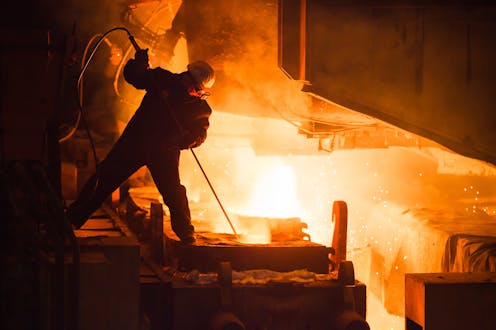
Steel is essential for making many of the technologies that will end fossil fuel combustion, including electric vehicles, wind turbines and solar panels. Unfortunately, to produce a lot of steel, manufacturers need to burn a lot of fossil fuel.
Steel production accounted for 2% of the UK’s emissions in 2019 and ranks second for energy consumption among the country’s heavy industries. Roughly two-thirds of this energy comes from coal.
The blast furnaces of steelworks burn a special type called coking coal (which is converted to a hard and porous fuel known as coke) at temperatures of up to 2,000°C, producing large amounts of carbon dioxide (CO₂) – around 1.8 tonnes for each tonne of steel. This method accounted for 82% of steel production in the UK in 2021, and 71% of all steel made worldwide that year.
While coal-based steelmaking can be decarbonised to an extent by capturing the CO₂, there has to be a suitable storage site nearby or sufficient demand for using that CO₂ in other industries. This is not the case for the blast furnaces in Port Talbot, Wales, which account for half of UK steel production.
Coking coal prices have more than doubled since the beginning of the pandemic and the invasion of Ukraine has disrupted supplies. In 2021, the UK imported 39% of its coking coal from Russia, with almost all of the rest coming from the US and Australia.
Another option is to use natural gas, another fossil fuel. But since 2020, gas prices have also risen considerably. These recent fuel cost hikes demand a reassessment of how steel is made.
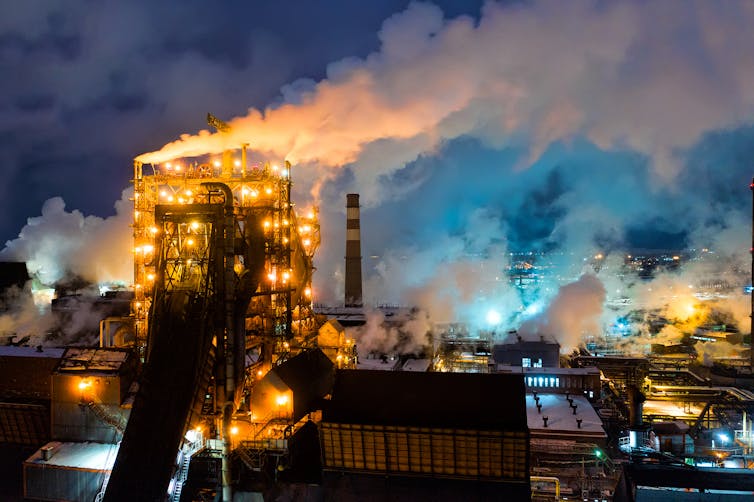
Steelmaking with green hydrogen (hydrogen that has been split from water using electricity generated by renewables or nuclear power) removes fossil fuels from the process altogether. As a result, it could be insulated from increases in fossil fuel prices and carbon taxes, all of which have made steelmaking with fossil fuels more expensive in recent years.
The UK steel industry is currently given a free allocation of emissions allowances, which significantly lowers the effective carbon price paid by steel producers. Our recent research shows that, if this exemption were phased out gradually, steelmaking with green hydrogen produced using wind and solar electricity would in fact be cheaper than all other options.
Green steel
Hydrogen can convert iron ore to a pure form known as sponge iron through a process known as direct reduction. This involves heating hydrogen to between 800 and 1,000°C which reacts with the oxygen in iron ore to leave pure iron and water vapour, with no carbon emissions. The sponge iron is then processed in an electric arc furnace to produce steel.
Electric arc furnaces can also recycle scrap metal, and while the UK has no direct reduction furnaces, it already has five electric arc furnaces that recycle scrap to provide 18% of the nation’s steel. If renewable electricity powered these furnaces and was used to generate the hydrogen that fuels the production of sponge iron, then total emissions from the steel industry could be zero.
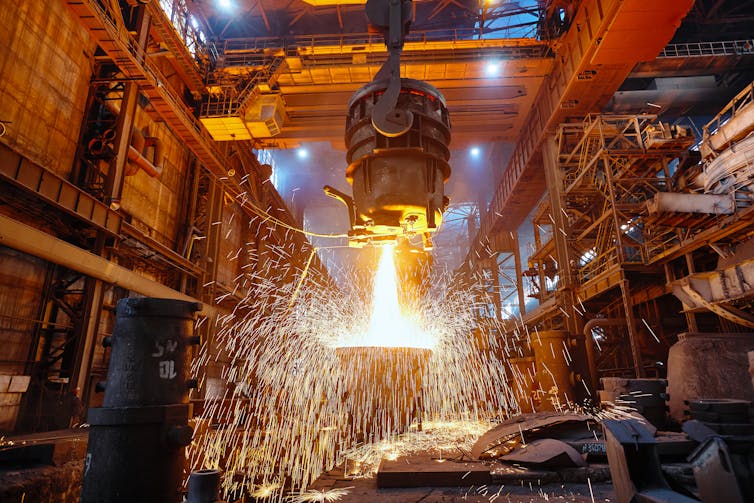
The EU and UK have both committed to ending imports of Russian coal in 2022, and large producers such as Tata Steel and ArcelorMittal have already stopped using Russian commodities in their supply chains.
While high gas and electricity prices are making some industries revert to burning coal, our findings show that green hydrogen offers a cheaper alternative to steelmakers. At recent fossil fuel prices, we estimate that direct reduction steelmaking with green hydrogen could be roughly 15% cheaper than the cheapest coal-based option (including carbon capture and storage) over a typical 25-year project lifetime.
Steelmaking with green hydrogen and electric arc furnaces uses lots of electricity. So, in a recent paper, we looked at reducing industrial electricity bills by removing green levies (which raise funds to spur the deployment of renewable technology and support vulnerable customers) and energy network maintenance costs and moving them to general taxation instead.
This would put the UK’s steel industry on an equal footing with France’s and Germany’s. We found that price parity could be achieved by increasing the average income tax bill by around 68p, rising to around £5.50 if UK steel production switched entirely to direct reduction with green hydrogen.
The UK government is considering exempting industries that consume a lot of energy from paying green levies. But soaring fossil fuel prices have hiked wholesale electricity costs so much that removing them and network maintenance fees will not significantly affect bills.
Instead, steelmakers and other heavy industries could access cheap renewable electricity directly in a green power pool.
The UK cannot afford to keep coal-based steelmaking in its decarbonisation strategy and must ensure the steel industry is ready to transition to using green hydrogen fuel instead.
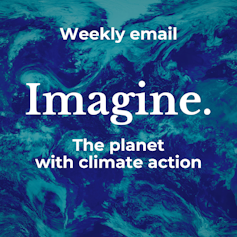
Don’t have time to read about climate change as much as you’d like?
Get a weekly roundup in your inbox instead. Every Wednesday, The Conversation’s environment editor writes Imagine, a short email that goes a little deeper into just one climate issue. Join the 10,000+ readers who’ve subscribed so far.

Clare Richardson-Barlow is a non-resident fellow at the National Bureau of Asian Research.
Andrew Pimm and Pepa Ambrosio-Albala do not work for, consult, own shares in or receive funding from any company or organisation that would benefit from this article, and have disclosed no relevant affiliations beyond their academic appointment.
This article was originally published on The Conversation. Read the original article.