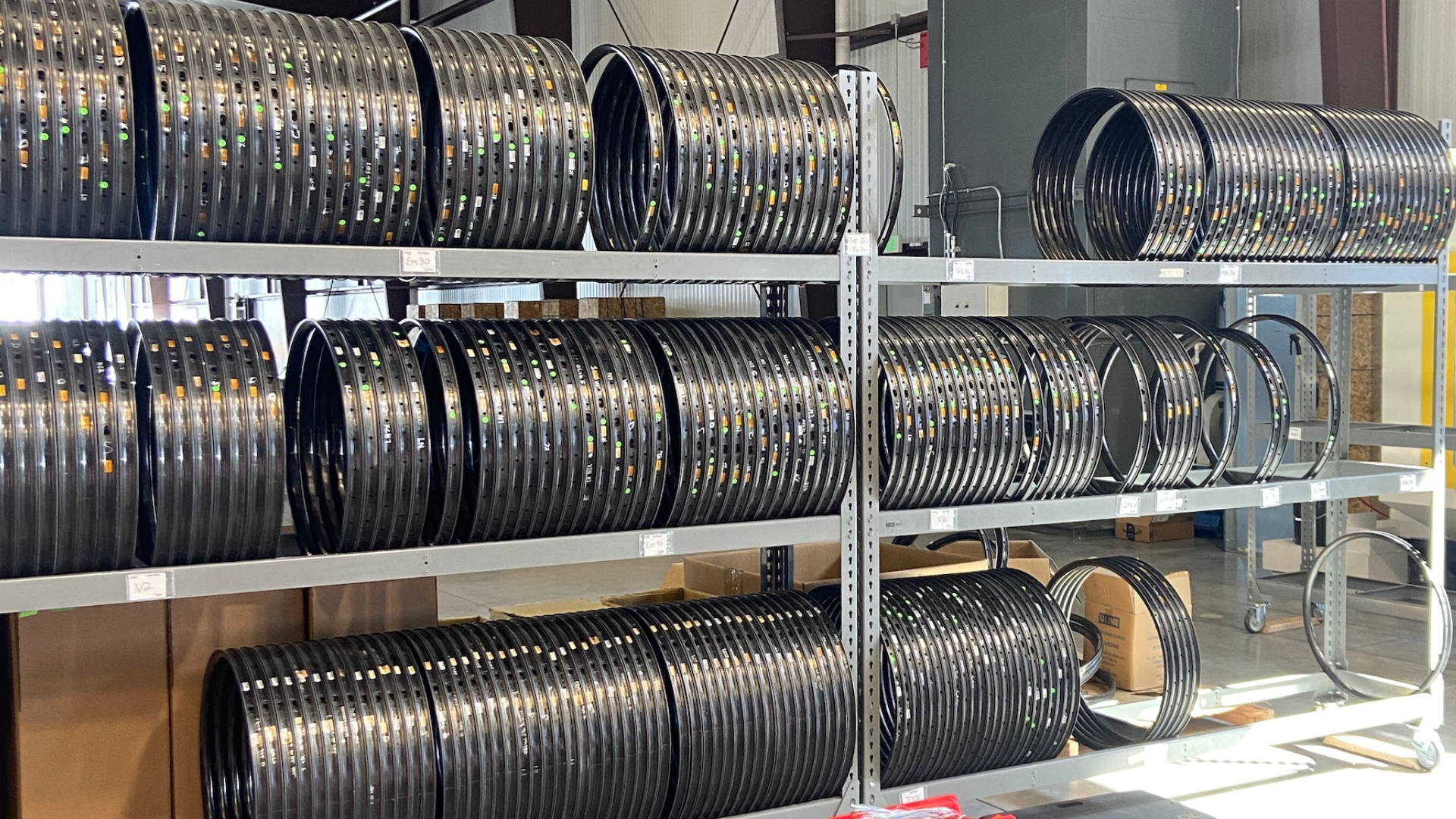
Two hours south of Salt Lake City lies the small town of Gunnison, Utah. Home to vast swaths of farmland and cattle pasture, Gunnison is also the headquarters of CSS Composites, the parent company of Forge + Bond, which designs and manufactures thermoplastic carbon fiber wheelsets.
CSS shares its campus with ACT Aerospace, a composites facility that has been manufacturing aerospace parts since 1985. The expertise, and the significant funding behind CSS, which uses novel thermoplastic composite techniques in place of more commonly used thermoset (epoxy-based) manufacturing, comes from the long and successful history and wealth of experience of ACT.
The campus comprises several large buildings and an impressive solar array; traditional composites manufacturing is highly energy intensive. Raw materials must be kept at very low temperatures prior to use so they don’t degrade, and the process of turning these materials into finished, usable parts takes immense amounts of heat and pressure, typically via large, submarine-esque autoclaves.
In contrast, the process CSS uses to make Forge + Bond rims requires far less energy. It’s also surprisingly clean, efficient and astonishingly fast: a wheel can go from raw materials to being ridden in less than two hours!
Cycling Weekly visited the CSS factory to see this process from start to finish.
Inside the CSS Factory
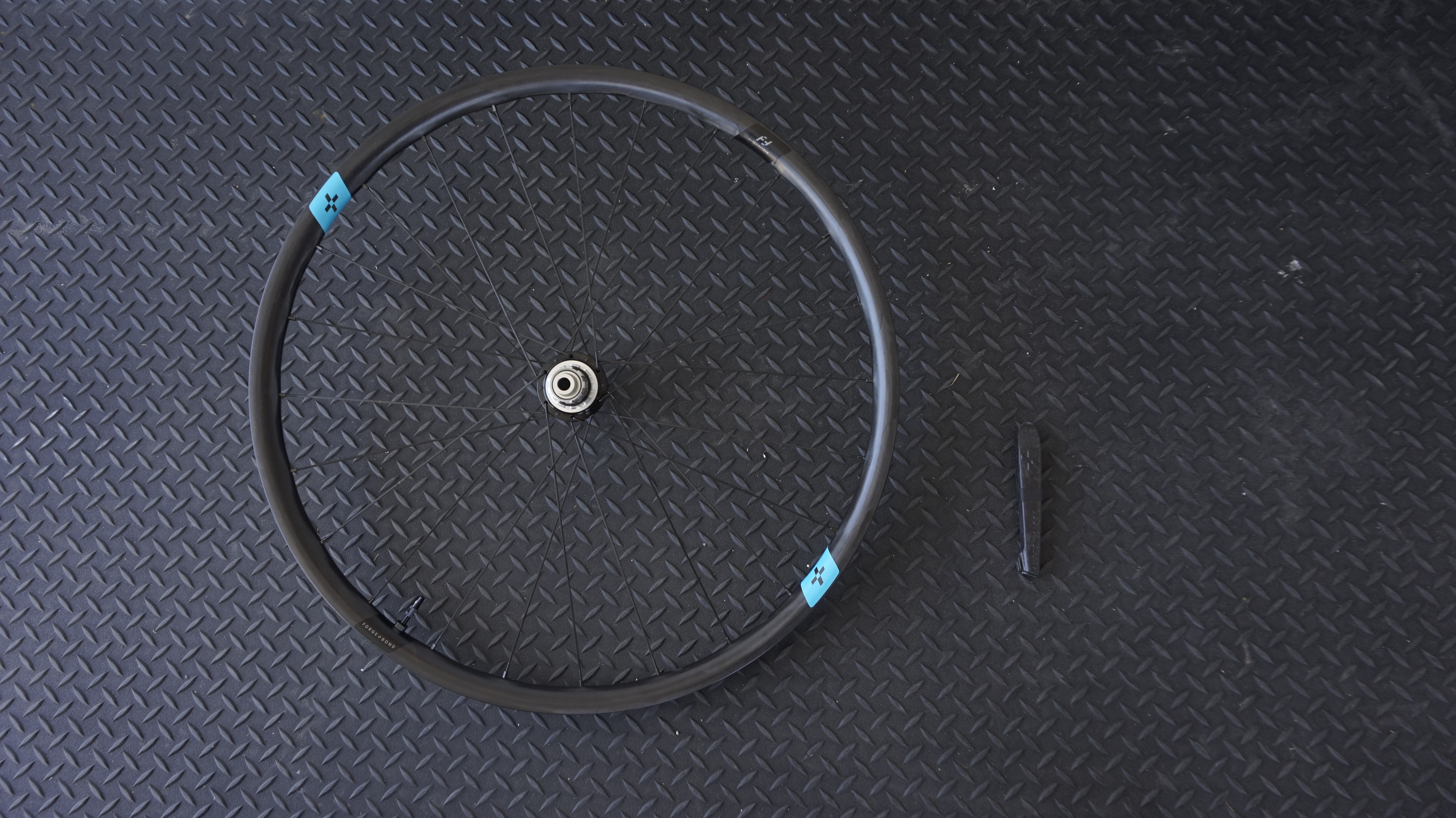
When CSS first launched its wheels, the company was hesitant to share the exact sequencing and techniques being utilized to produce them. Since then, however, it has become more open about the process. The reason for this, according to Brett Stahl, VP of Brand and Marketing at Forge + Bond, is that as the inventors of this process, the people within the company know precisely how many resources were required to develop the machinery and techniques needed to manufacture these products. As a result, they know how difficult it would be to replicate.
The first stop on the tour was visiting the ACT Aerospace production facilities. We were ushered through several doors into loud industrial spaces busy with people cutting raw material, laying up carbon fiber sheets by hand and doing the messy finish work that is necessary for these large scale thermoset composite pieces. ACT manufacturers parts for satellites, specialized aerospace applications, and more. We walked past giant autoclaves, an impressive machine shop, and the hulking carapaces of helicopter and other aircraft parts stacked up to the ceiling. ACT and affiliated businesses under the same roof employ several hundred people from Gunnison and the surrounding area, and it’s clear these people are very good at what they do.
Surprisingly clean, efficient and astonishingly fast: a CSS-made wheel can go from raw materials to being ridden in less than two hours!
Next we visited CSS’s wheel building facility. Instead of giant freezers stocked with different mixtures of pre-impregnated resins, there were a few pallets of boxed fiber spools sitting on the floor, at room temperature. The raw material, manufactured by Toray, comes to CSS in several polymer mixes, which are utilized in different ways to optimize each wheel design. It was still loud here, but instead of dozens of people hard at work, there was just one: a single technician runs the first two machines that begin the process of making FusionFiber rims.
The contrast between the two composites techniques could not be more stark: building wheels using thermoplastics means no refrigerator, no autoclave, and instead of many hands, a few (large, noisy, imposing) robots. Despite all of the work that went into developing these techniques, the process is easily digestible.
The Process
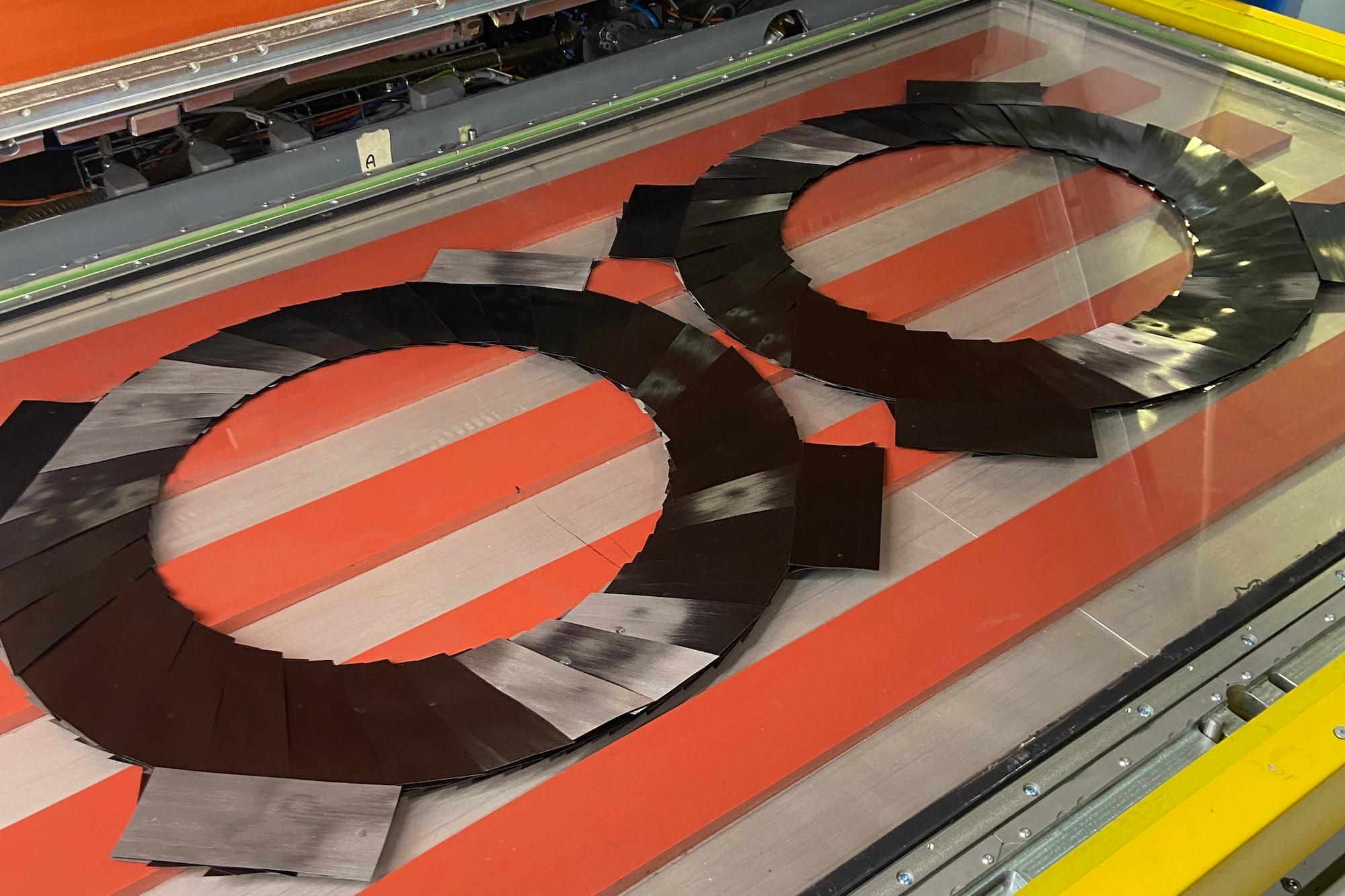
First, unidirectional tape is wound onto special spools, much like winding thread onto a bobbin. It is then loaded onto a Dieffenbacher machine called the Fiberforge, which CSS co-developed with the German machinery manufacturing company (cost: many millions of dollars).
The Fiberforge cuts the tape into short sections at robotically precise lengths and angles, then ultrasonically tacks them together in the shape of a wheel. Each model that CSS manufactures (there are several different Forge + Bond rim shapes, as well as rims for Chris King, Trek and others) utilizes different mixtures of polymer-infused tape depending on the desired riding characteristics. Four to six minutes later, a flat, multi-piece carbon wreath is spit out on a tray, without the same violence, but in a similar way to a cash register drawer opening. The speed the machine is tuned to is determined by the tape being used and the tension of the spool.
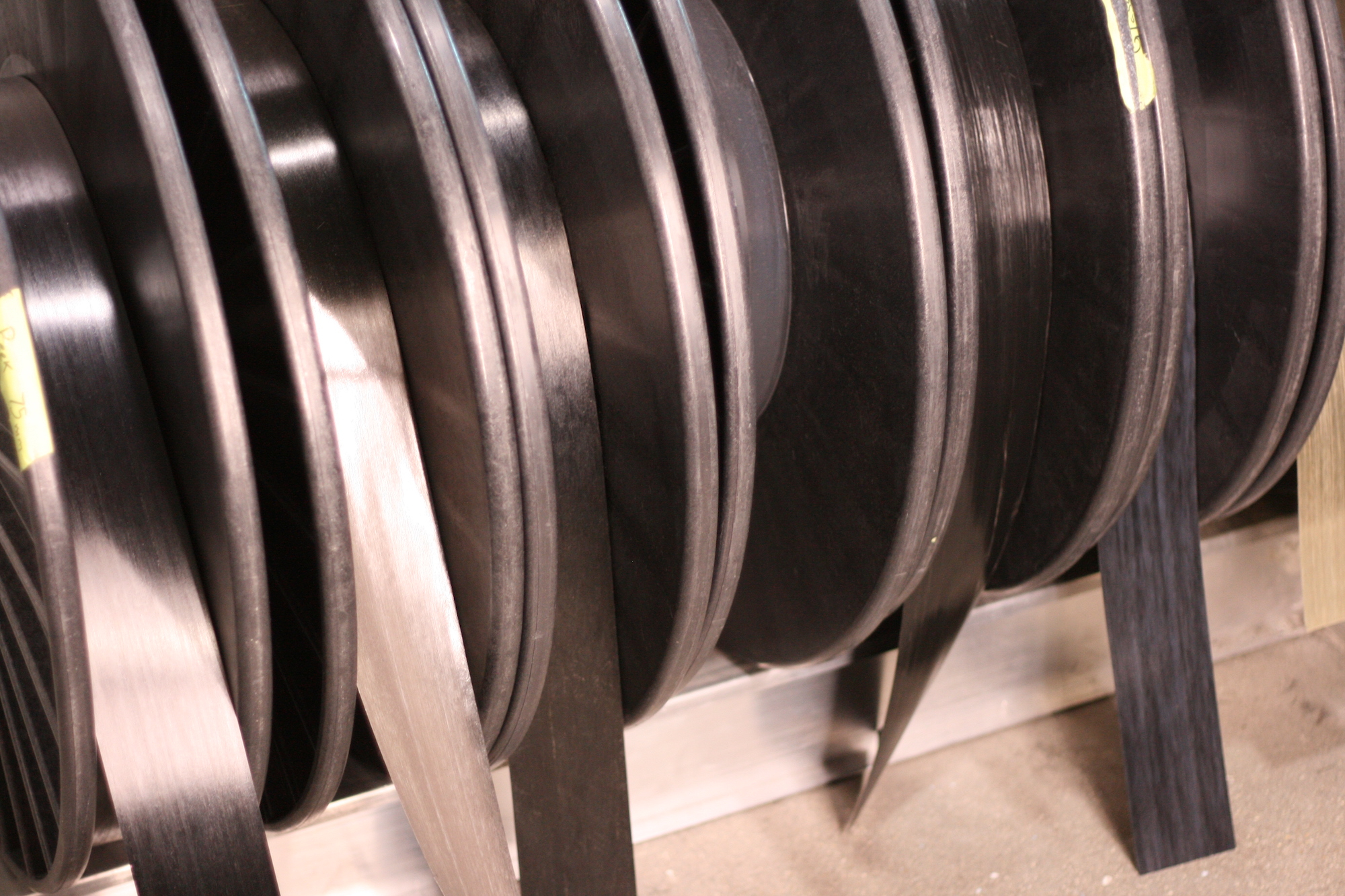
The technician then moves each flat multi-piece wreath over to the consolidation machine, called the Fibercon, another Dieffenbacher creation (and again costing many millions of dollars), which vacuum compresses the individual sections of tape into one single piece. The Fibercon is designed to hold two tack-welded pre-rims at a time, side by side, and moves them around for each stage of the process at exactly the right time without human input. It first heats them up using infrared, then slides them over to be water-cooled, at which point the two pieces (half of a rim, each) emerge, warm to the touch. This entire process only takes a few minutes.
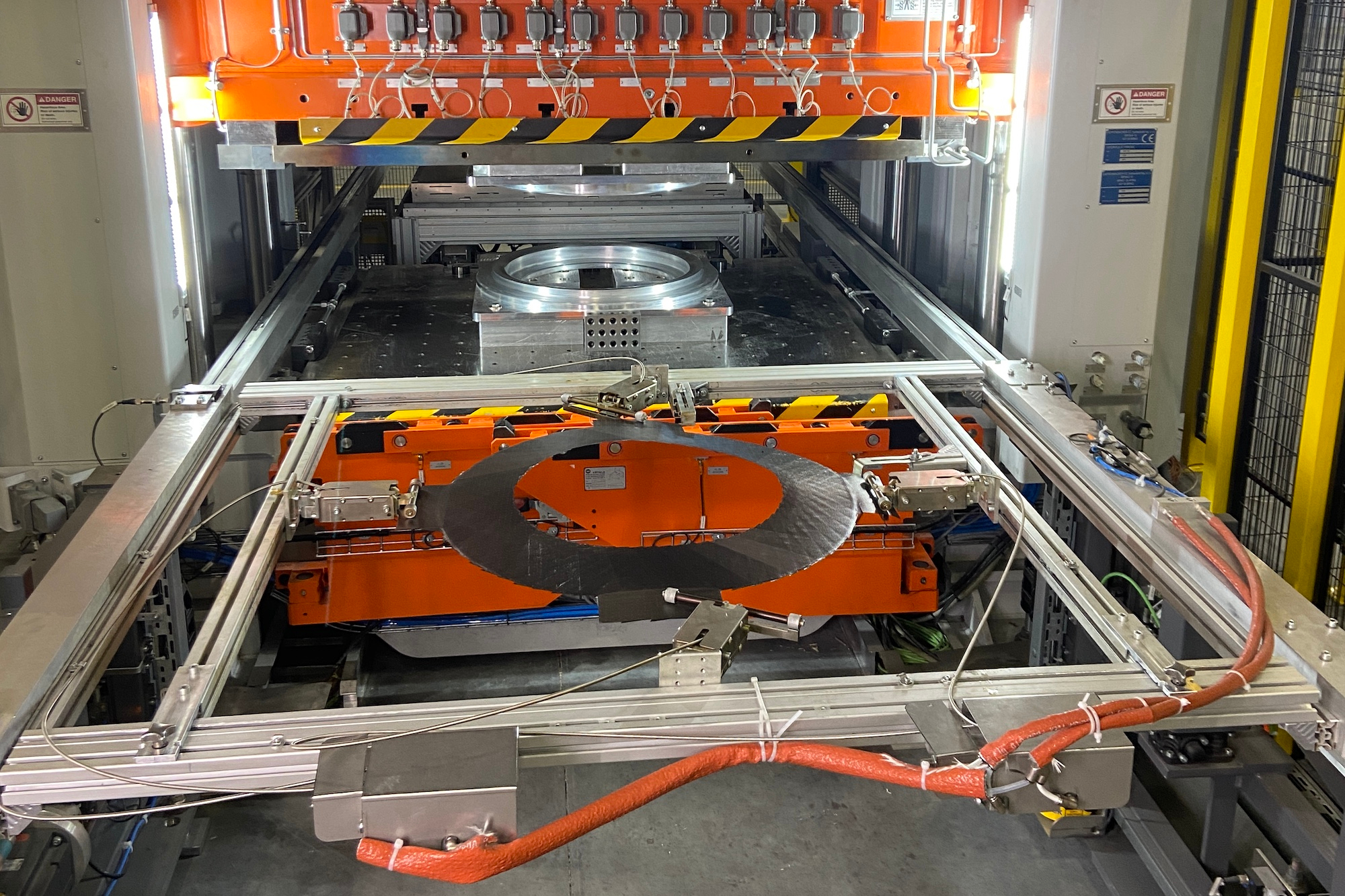
Thermoset composites, as the name implies, set up once and then cannot be reheated and remolded. The FusionFiber system, in contrast, uses the repeated heating and cooling technique as the basis of its manufacturing technique. This is one of the many ways the two processes differ. The implications of this make the Forge + Bond’s rims much easier to manufacture: being heated and cooled over and over again without changing chemical makeup means things can be batched. If the rim pieces need to sit for a while, it’s not a problem; each step of the process can stop and start as needed and workflow can be adjusted to suit specific needs.
The next step is moving to yet another Dieffenbacher machine for pressing. This is how the individual pieces, which hitherto are completely flat, get molded into the shape of a bicycle rim. Each wreath-shaped piece is mounted one at a time into a suspended rack, held in place by tabs made expressly for this purpose. It first moves into an infrared heating chamber, then is dropped onto an aluminum mold and pressed into the shape of a rim sidewall. This takes only a few minutes, and pieces come out smooth, with a finished surface requiring no additional treatments.
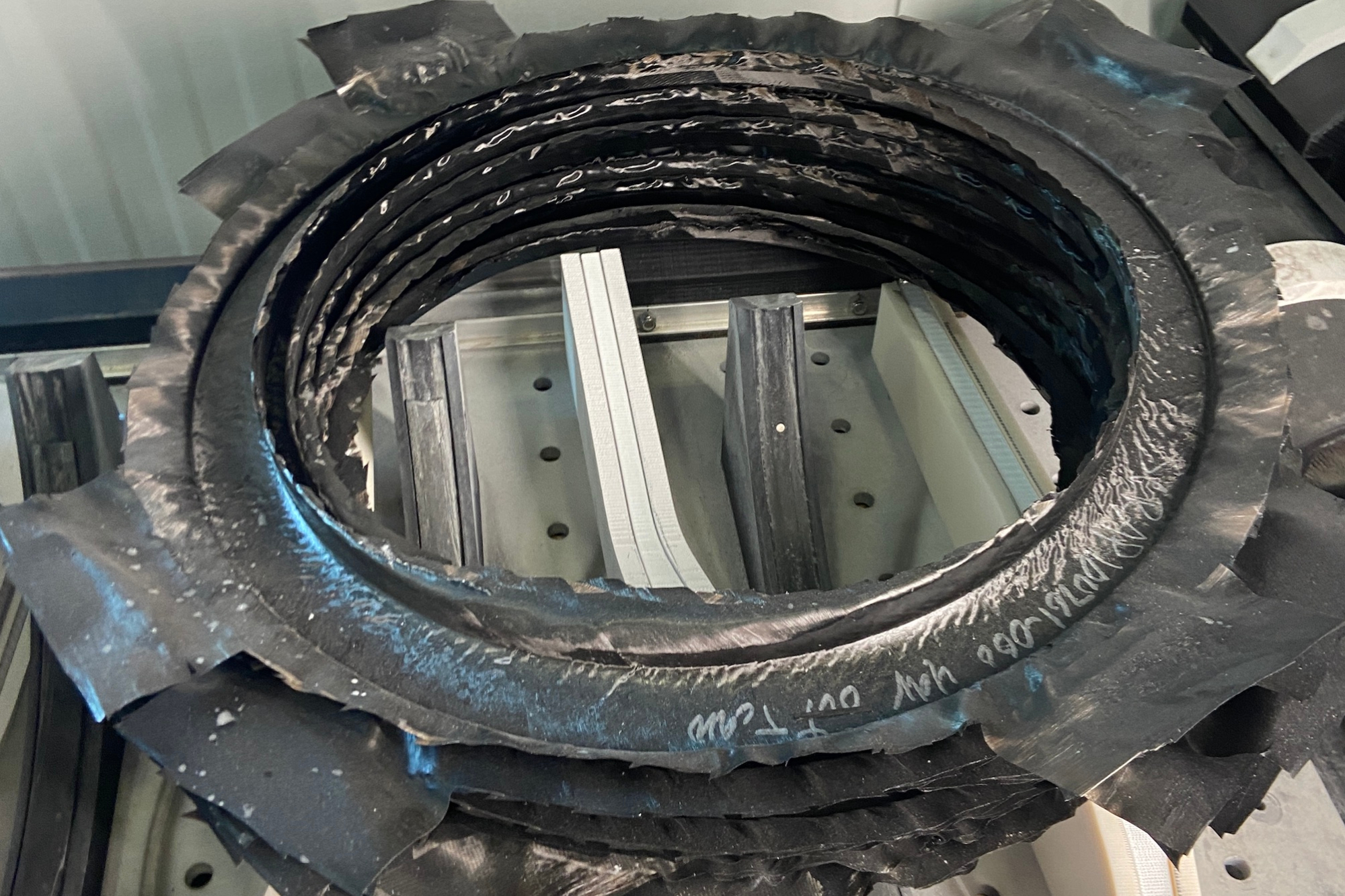
Next, the pieces are taken to a water jet that trims off excess material. This is completed in a matter of seconds. Trimmings come off as one piece outers and inners, and these are saved to be repurposed into other things (more on that later).
The final molding step of the process takes the two formed sidewalls and places them into an aluminum mold along with a channel piece (this the rim bed, which is manufactured separately using the same techniques) with a latex bladder inside all three pieces. This step requires the most humans; three different technicians work together to efficiently assemble and disassemble molds and insert the carbon pieces and latex bladder.
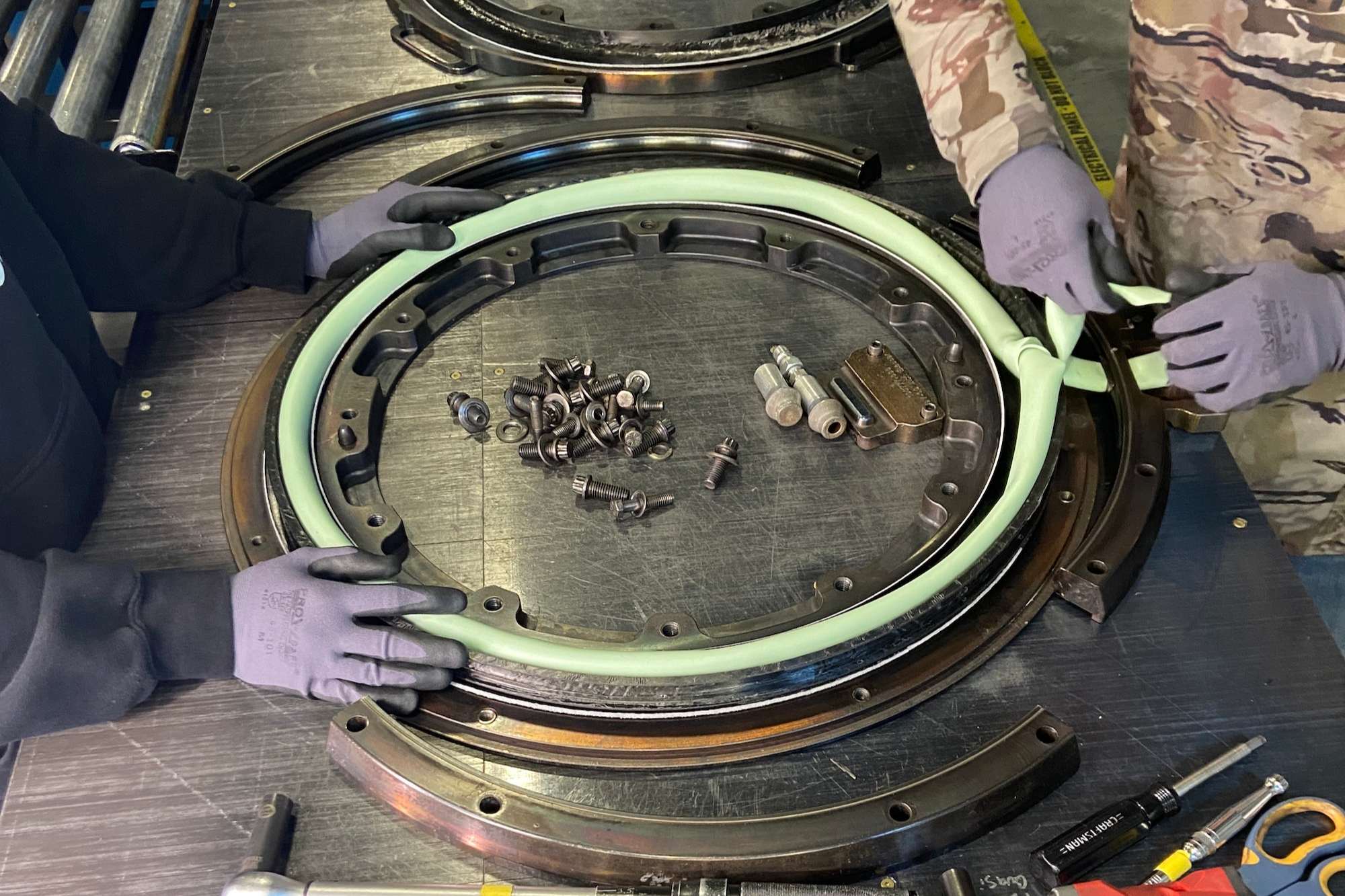
Once the mold is bolted together it slides into a Wabash vacuum press, where the mold is subjected to significant heat and pressure in order to bond the rim pieces together into a completed product. It stays in the press for about six minutes. When the completed rim comes out of the mold, it gets its latex bladder removed and is then cleaned of excess nylon/polymer while the edges are given a light sanding. It gets inspected after this stage, but is essentially done. The tiny slivers of excess polymer that are scraped off the edges of the rim are the only tangible waste throughout the entire process.
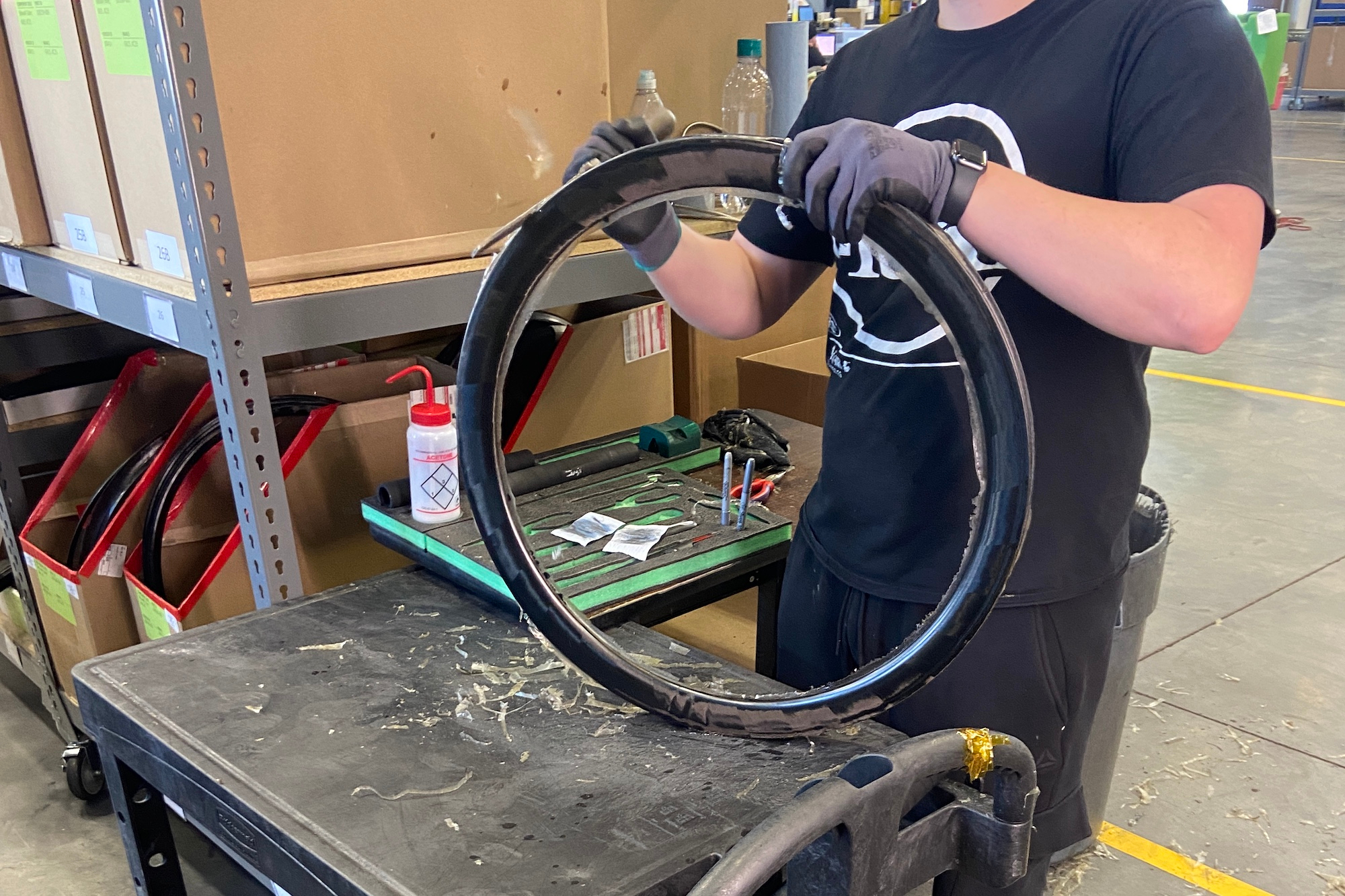
After this step, rims are ready to be made into wheels. Yet another machine is responsible for spoke hole drilling, followed by a lacing machine, at which point the completed wheel gets hand-trued, stickered, and has rim-tape installed. The completed wheel is now ready for tires to be mounted.
Final step: go for a ride.
Curious about the ride quality? So were we! Check out our review of the Forge + Bond GR45 gravel wheels and the CSS-made Chris King GRD23 R45D wheels.
What about the scraps and leftover material?
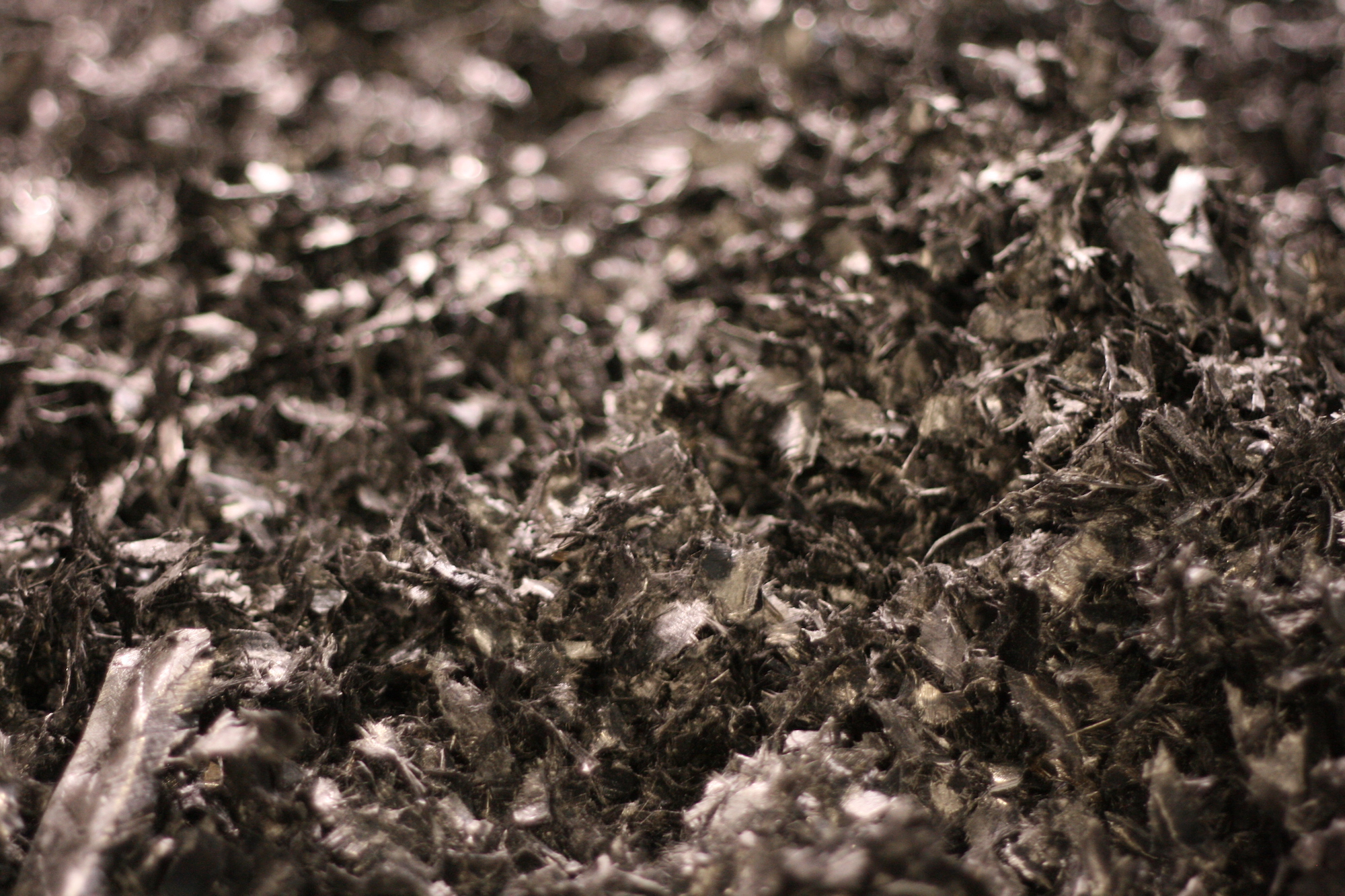
One of the selling points of thermoplastics is that since the material doesn’t get altered through repeated heating and cooling cycles, broken or extra pieces can be ground up and reused. In fact, Toray sells raw material, whether in tape form or chipped, for the same retail price. For this specific process, these ground up bits cannot be remade into rims—that requires longer sections of material, but all manner of other products are possible, from bikes parts like pedals and stems to saddles for equestrian use, ATV applications, tractor parts, hydrofoil components, body armor, etc. The list is endless. CSS is rapidly connecting with interested partners to develop these things.
This is the key to CSS’s ultimate mission. Yes, the company has developed an incredibly environmentally friendly manufacturing process, but it’s also one that has the potential to make high value parts, then reuse and sell that same exact material over and over again. It’s just a matter of scale—once the raw material is being utilized in sufficient quantities, it will be increasingly inexpensive to perpetuate the cycle. Realistically, the bike industry makes up a pretty small part of the overall pie when it comes to manufacturing products.
One of the best parts of the job, says Stahl, is coming in to work each day and asking “what can we make today?” The options are essentially unlimited.
Tire Levers?
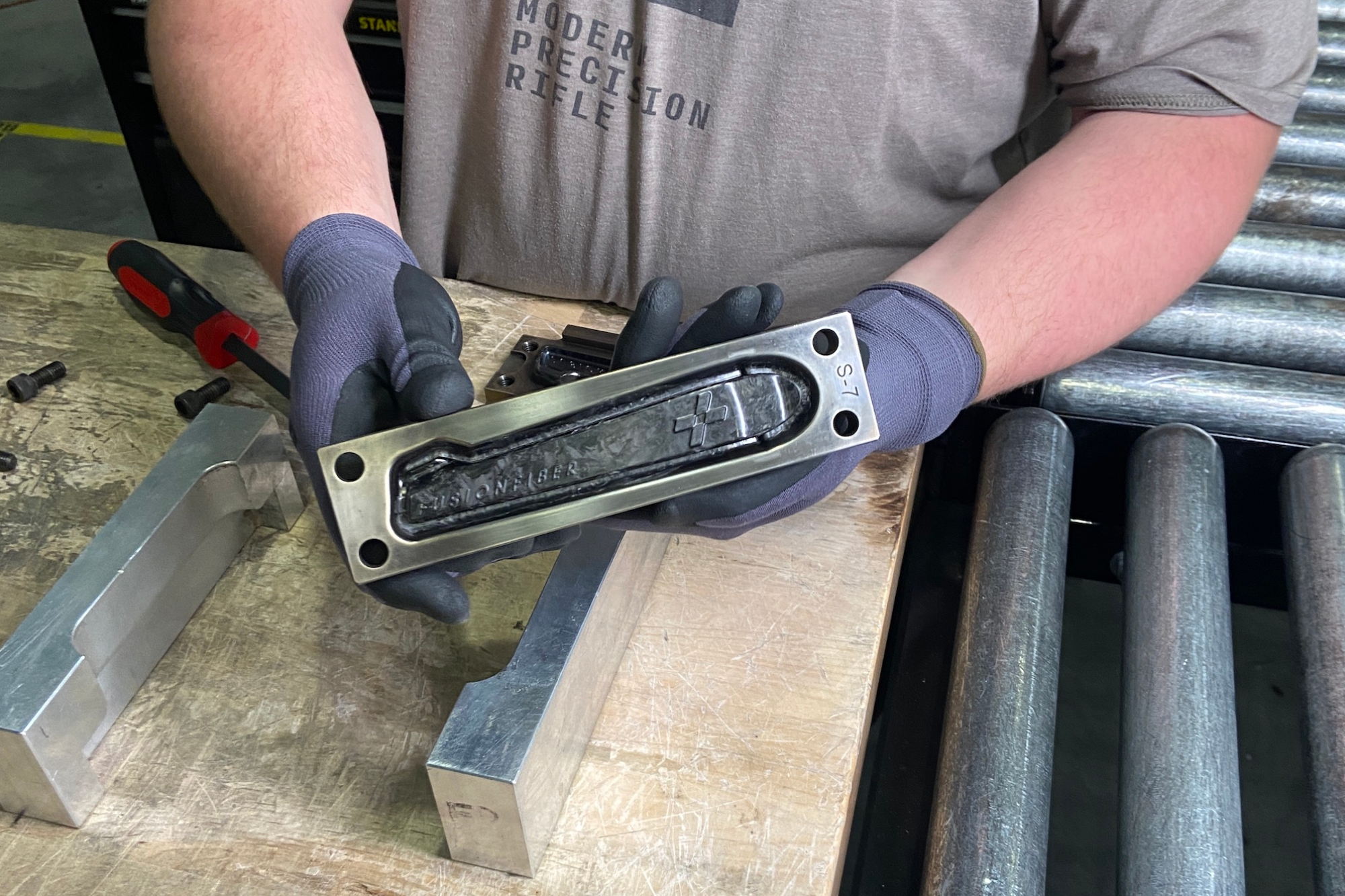
The first product Forge + Bond released with chipped thermoplastic material was a tire lever, retailing for $50 (a set is also included with each wheelset the company sells). This hard-to-stomach price caused some internet backlash, though Stahl says the levers sell surprisingly well.
The point, however, is not the levers: they’re just a proof of concept (though a very highly engineered proof of concept). Taking waste, offcuts, and busted up parts and turning them into new items is the real aim here, and developing the levers demonstrates how it can be done. Other bike products, like pedal bodies, stems, saddle rails, crank arms and the like may be available in the future.
People may criticize the touted recyclability benefits of thermoplastics as greenwashing, but the process is already under way. And at scale, it could really shake things up.
We were able to see the lever making process as part of my tour. A small portion of chipped material first gets weighed out, then added by hand into a small mold. The mold then goes into one of the same Wabash presses used for the wheel mold where it sits for a few minutes to come up to temperature, then gets compressed down before being moved to another press for cooling. The lever is then removed from the mold but needs to have the rough edges trimmed off before use. Apparently it’s common for Forge + Bond to hand out these levers and tradeshows and bike shops and offer people the opportunity to try to break them: so far no one has succeeded.
The chipping process is more or less as straightforward as turning trees into mulch; material goes into a hopper, gets ground up and spit out in precisely the same way, without clouds of toxic dust or anything. Chipped material sits in bins and garbage cans throughout the facility, ready to be made into new things.
Arguably, what CSS is doing when turning rims into other things is downcycling, not recycling. But it’s not theoretical, the company is actively doing this. People may criticize the touted recyclability benefits of thermoplastics as greenwashing, but the process is already under way. And at scale, it could really shake things up.
Building wheels for other brands
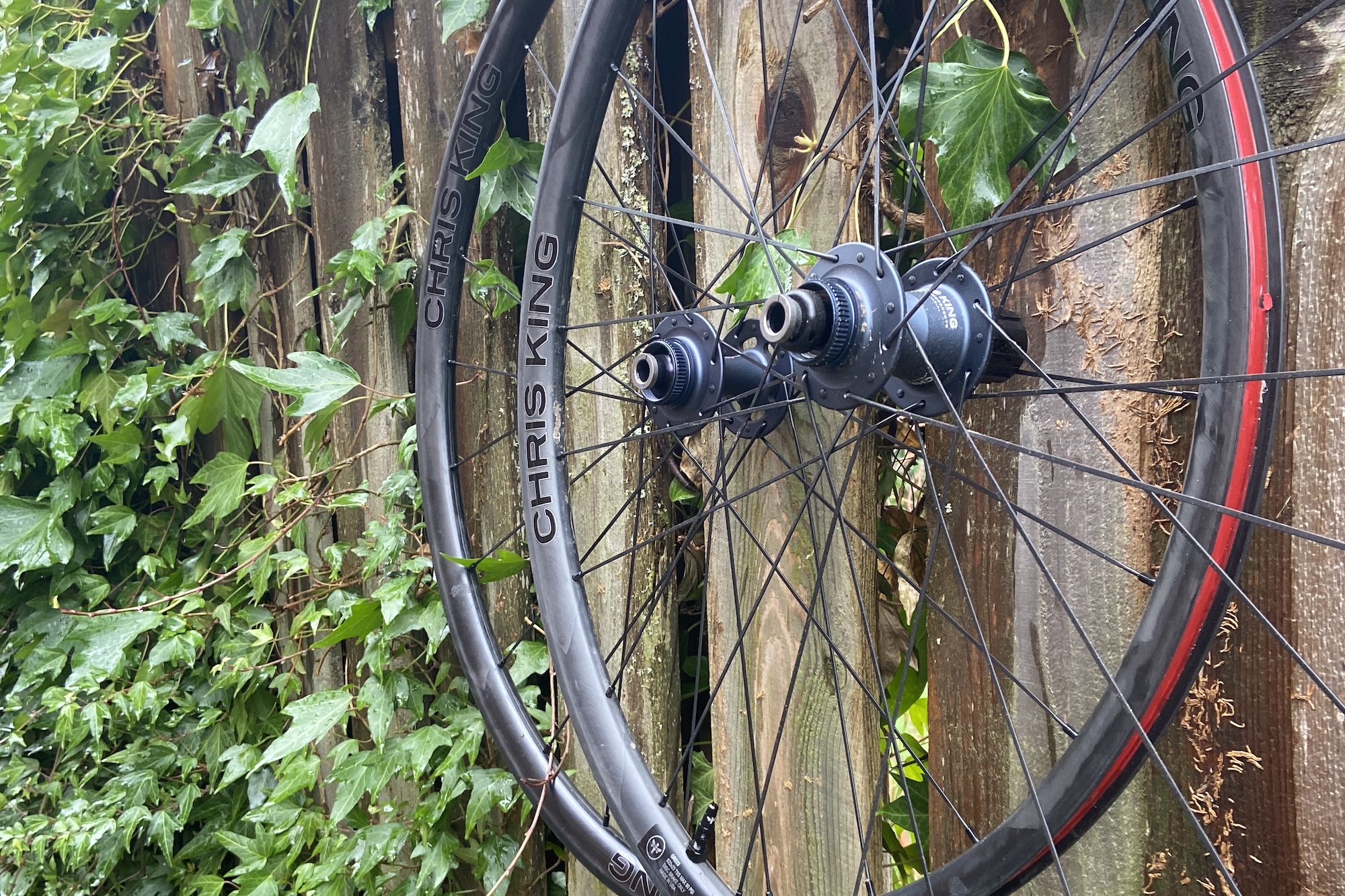
We asked why CSS had launched Forge + Bond while simultaneously making rims for other brands, which seems as though it would put CSS in direct competition with its manufacturing customers.
Stahl explained that after initially developing the process and manufacturing rims for others, CSS wanted the freedom to design rims without outside influence. Forge + Bond provides a means to push the envelope on the technologies being used, and as the experts, put to use the things it has learned to make the very best product available. Though the rims Trek and Chris King offer are similar to Forge + Bond’s offerings, each rim has its own mold and own recipe of carbon sheets with different polymer/nylon types. They may be similar, but each one is designed jointly to the specifications of each brand.
Thermoset vs. Thermoplastic
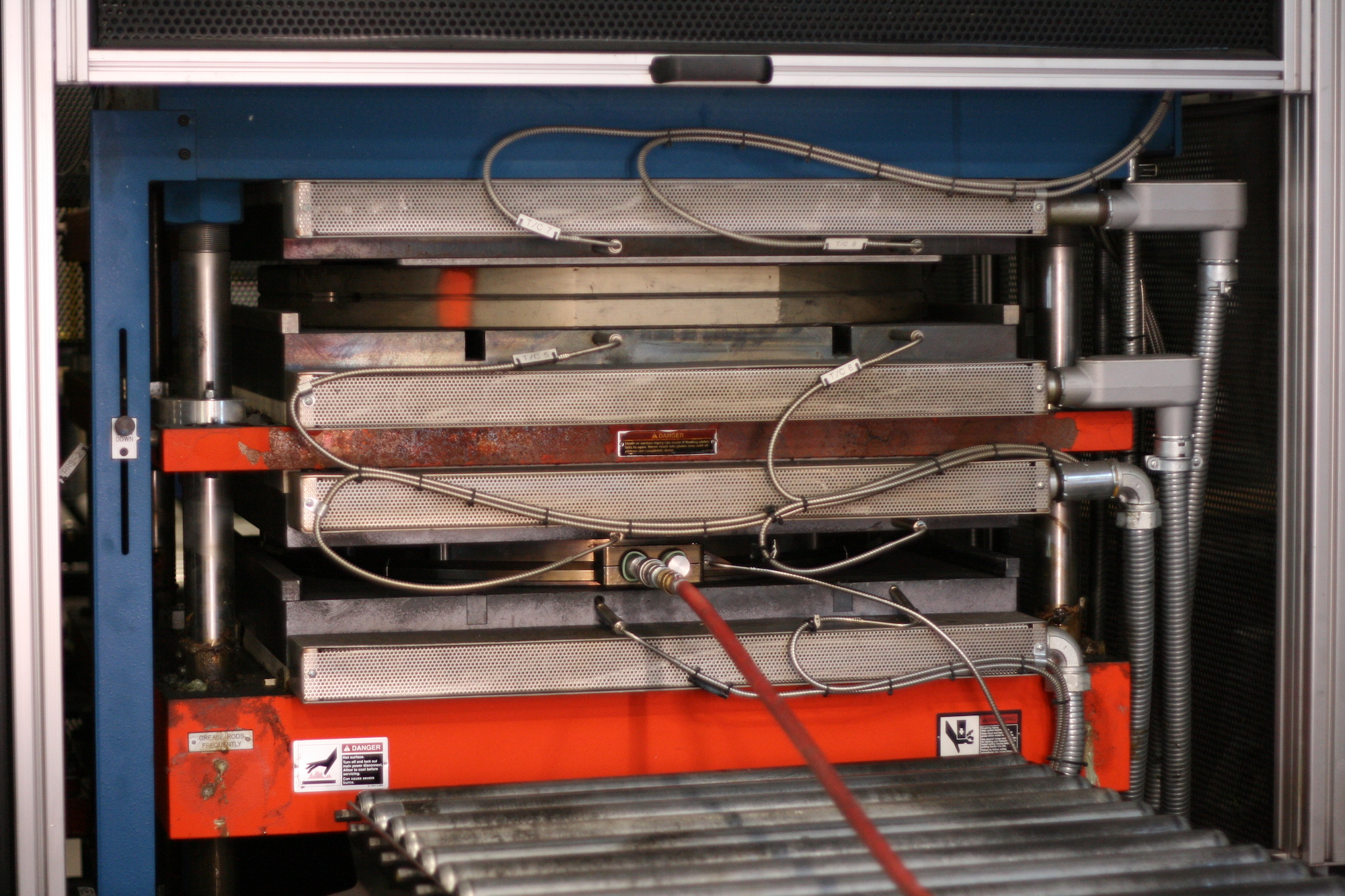
Despite advantages in terms of energy cost, labor cost, waste produced and diminished toxicity, thermoplastics do have drawbacks. In terms of pure mechanical performance (strength to weight), thermoplastics cannot match high performance thermoset composites. This is why we are not likely to see many bicycle frames made with these techniques.
Thermoset frames, especially in the current era ruled by aerodynamics, will continue to rule the roost. At the moment, there is no better material for building racing bicycles than epoxy-based thermoset composites. In terms of other applications, thermoset materials can also withstand much higher temperatures, making them a better option for anything that gets very hot (or very cold) i.e. aerospace uses.
But bicycle rims are a place where mechanical performance isn’t based solely on strength to weight. Damping, especially for off-road riding, is much more critical. As is fatigue resistance over time and how it is that the materials fail. Because of the inherent give in the polymers that hold the fibers together, thermoplastic wheels do much better over repeated impact and can often remain rideable even after cracking—making it that much more likely you can make it to the finish line, or at least back to your front door.