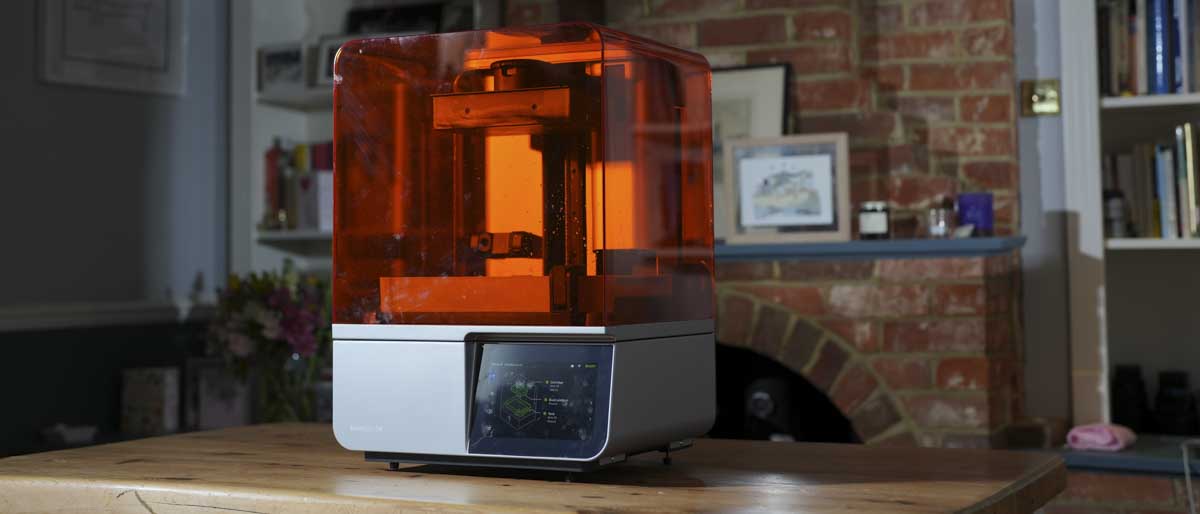
Formlabs has earned a reputation as the go-to machine for businesses needing a cost-effective and reliable 3D printer for a wide array of applications, from prototyping to medical and mechanical uses.
The vast selection of specialist materials and a high-quality ecosystem that includes wash and cure machines as well as a finishing station make this one of the most complete and user-friendly options on the market. Form 3+ and Form 4 occupy a niche with few direct competitors; many professional-level machines cost tens of thousands of dollars, while the best 3D printers at cheaper end of the market is great for hobbies but often lacks the consistency and reliability for heavy professional use.
First and foremost, Form 4, with the PreForm software and dashboard, makes preparing and uploading work easy, whether it's a new iteration of a prototype or a small product production run. The flexibility of the range of materials allows you to go from quick printing with general-purpose V5 materials to silicone, elastic, and biocompatible materials, providing a solution for almost any intended end-use.
In this review, we've focused on the standard and most affordable V5 materials to see what this printer is capable of, and from the outset, the Form 4 impresses with some of the speediest, most accurate, and detailed prints we've seen from any 3D printer yet.
Formlabs Form 4: Design
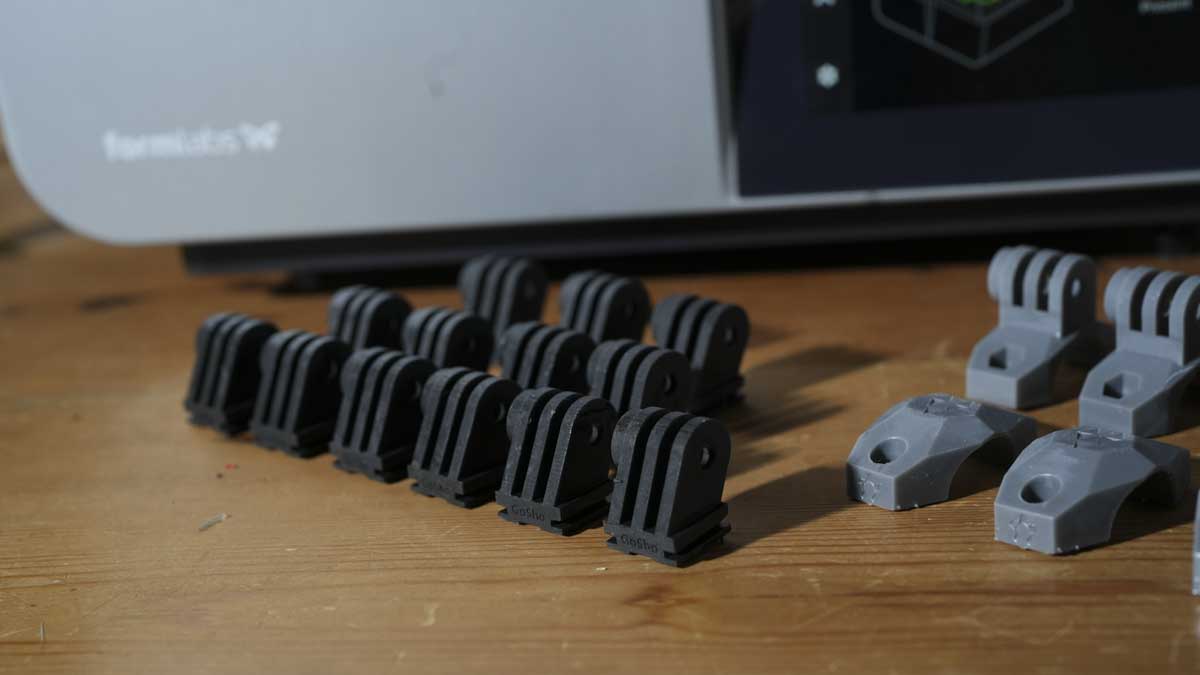
It's worth noting from the outset that while the Form 4 hints at the Formlabs design of previous printers, it is a completely different machine with a host of new features and technology. The overall design still features the flip-up orange protective lid and a build platform on the Z-axis with a quick release, very similar to the Form 3+. At the back, there is a slot for the resin cartridge. These cartridges look smaller but still contain a litre of material but in a more compact design than those seen with the Form 3+.
These resin cartridges function in the same way once dropped into the machine with a rubber bung at the bottom that is squeezed by the machine to release the resin. This time, however, the resin cartridges’ contents can be easily seen through a transparent window in the machine—a small design touch that can make a big difference in the workplace. The resin tank has also been redesigned with an improved mixer that clicks into place.
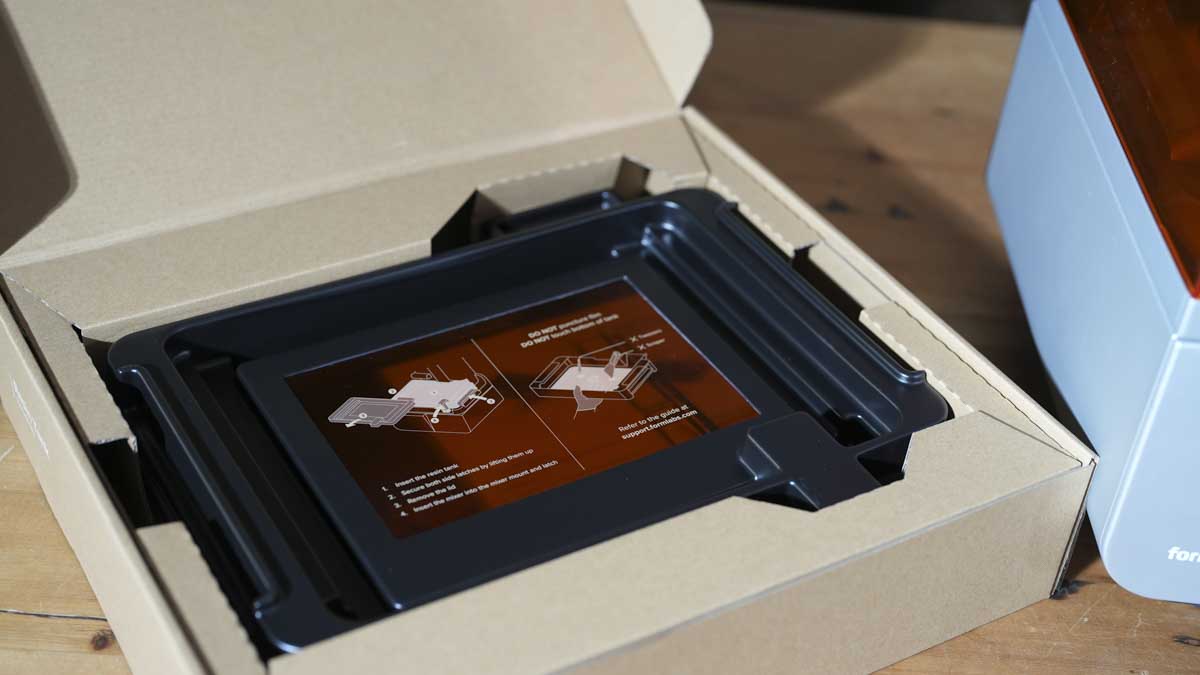
Like Form 3+, the front of the machine has a large touchscreen interface that enables users to adjust settings, run maintenance procedures, and re-run past prints, among other tasks.
The biggest design difference for the Form 4 is the switch from Low Force Stereolithography (LFS) used by Form 3+ to Masked SLA (MSLA) technology. This new method leverages a custom LCD and LED-based backlight to cure entire layers of resin at once, significantly improving both speed and accuracy.
Formlabs Form 4: Features
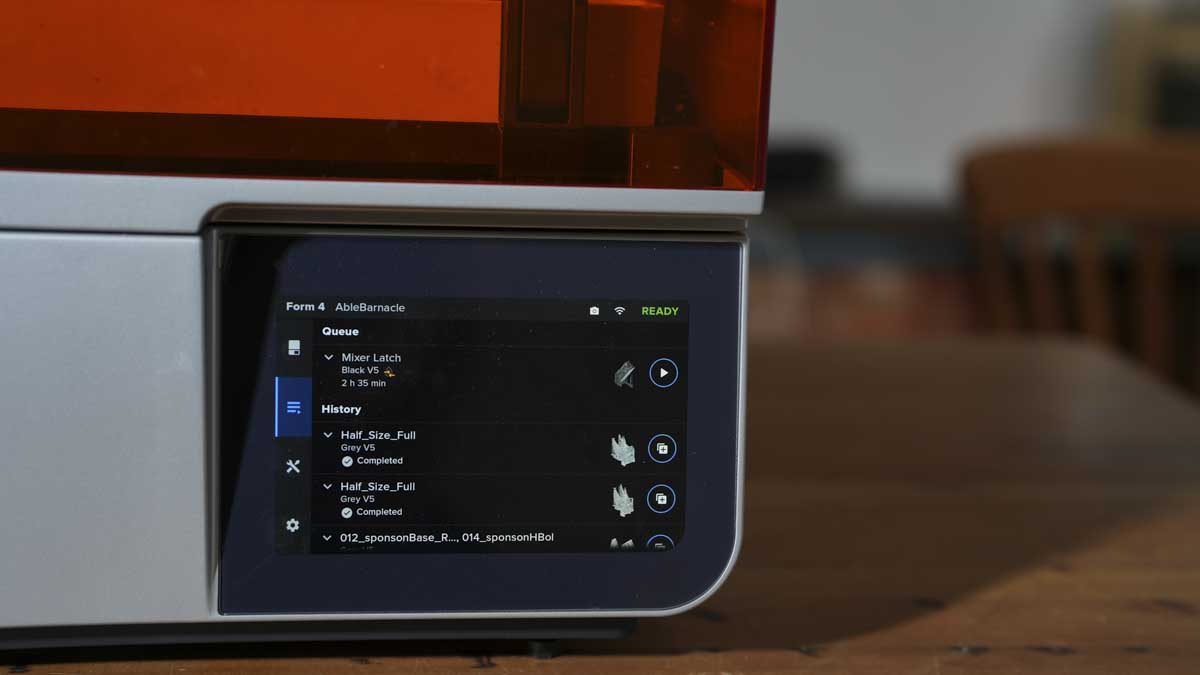
Formlabs has developed the technology used in the latest model of the Form printer to meet technological advancements. As such, the machine has moved away from Low Force Stereolithography (LFS)—a technology that previously gave the company's machines an edge in accuracy. However, that accuracy can now be matched by the latest LCDs, and the Form 4 introduces a new Low-Force Display (LFD) Print Engine that utilizes a custom LCD and LED backlight system. This system strikes a balance between high speed and high precision.
The integration of Masked Stereolithography (MSLA) technology in this new machine enables faster curing of entire resin layers rather than just pinpoint areas, significantly boosting print speeds compared to the method used by the Form 3+ SLA printer.
One of the major advances enabled by this new system is high dimensional accuracy, achieving a 50 µm XY resolution similar to the Form 3+. This ensures detailed and accurate prints with smooth surface finishes suitable for functional part production runs.
Although initially appearing similar to its predecessor’s resin tank, the new version incorporates several changes to aid printing speed. One of the main features is the release texture of the film, which helps to minimize adhesion forces, improve compatibility with various resins, and reduce print failures.
All resin printers can make handling resin messy; to facilitate workflow and ease of use, Form 4 includes smart sensors for automatic resin dispensing, which should lead to fewer failures.
Print Technology: Masked Stereolithography (MSLA) with Low Force Display (LFD) print engine
Build Area: 145 × 145 × 185 mm (5.7 × 5.7 × 7.3 in)
Minimum Layer Resolution: 25 µm
Maximum Layer Resolution: 300 µm
Dimensions: 405 × 375 × 530 mm (15.9 × 14.8 × 20.9 in)
Weight: 17.5 kg (38.6 lbs)
Bed: Removable Build Platform
Print Surface: Flexible Resin Tank with Release Texture
Software: Formlabs PreForm Software and Dashboard
Materials: Compatible with over 23 Formlabs resins, including new high-speed resins like Grey Resin V5, White Resin V5, Black Resin V5, and Clear Resin V5
Print Speed: Up to 4x faster than the Form 3+, capable of printing full build volumes in approximately 2 hours
The setup process for previous Form printers has been designed to be as straightforward as possible. Even the least experienced user should be able to get the machine up and running within 15 minutes, requiring only the printer, resin, computer, Wi-Fi, and installed software, with the rest managed by the machine.
When it comes to materials, Formlabs has invested heavily in developing a wide range of specialist materials for various uses and applications. Currently, this range for Form 4 covers over 23 different Formlabs resins, including new high-speed resins for diverse applications.
As this machine is designed for professional markets, reliability and longevity are key features. The Light Processing Unit (LPU) and other components are designed for long service life and high-volume use, with robust construction and smart sensors used to monitor and maintain print consistency, stopping printing if anything appears to be out of place to help save on failures and damage to the machine.
Finally, the change in technology enables print speeds that are up to five times faster than the previous iteration of the machine. This also boosts print efficiency, with the cost per print dropping by around a quoted 40%.
Formlabs Form 4: Performance
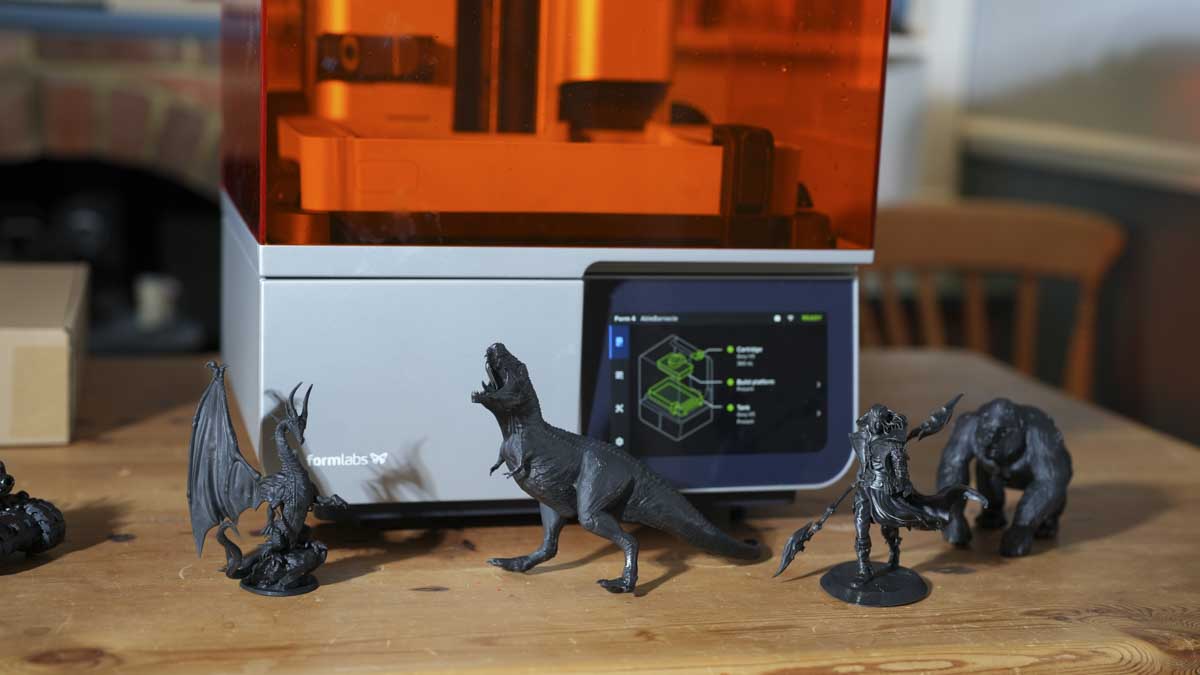
Unpacking the Formlabs Form 4 immediately showcases the significant upgrades this machine offers. Its size and weight are roughly equivalent to those of Form 3+, so it occupies a similar workspace area. The machine arrives fully assembled, requiring only a few minor setup steps before it's operational. First, you install the new-design resin tank, which, like the Form 3+, incorporates a mixer arm that also needs to be fitted and locked into place.
The resin tank clicks into place with ease, and the scoop fits back into the machine to catch the resin once the cartridge is installed and primed. The resin mixer design is more robust than that of the Form 3+ and features a locking mechanism. This new design is not only sturdier but also easier to clean between resin swaps. However, given that each tank costs over $100/£100, they are not considered disposable.
Formlabs has simplified the tank cleaning process; the mixer arm fits into the Form Wash easily, and the cleaning sheet option allows you to peel out most of the excess resin before it's wiped clean.
When it comes to loading the resin, a resin cartridge is dropped into a slot at the back of the machine, then the lid is flipped open to allow airflow to enable the release of resin. Once printing is complete or if the machine is to be left idle for some time, the lid is closed, and the resin is stored for future use.
Resin swapping follows a specific procedure: remove and clean the build platform, close and remove the resin cartridge, then swap out the resin tank. Install a clean resin tank, then the build platform and insert a new resin cartridge. This process is relatively quick and straightforward.
An advantageous feature for frequent resin changes, as in this test, is that tanks with resin residue can be covered and stored flat without a full clean. It is crucial to perform this procedure away from sunlight, as the resins will cure very quickly. Ideally, this should be done in an artificially lit room or with the curtains or blinds drawn.
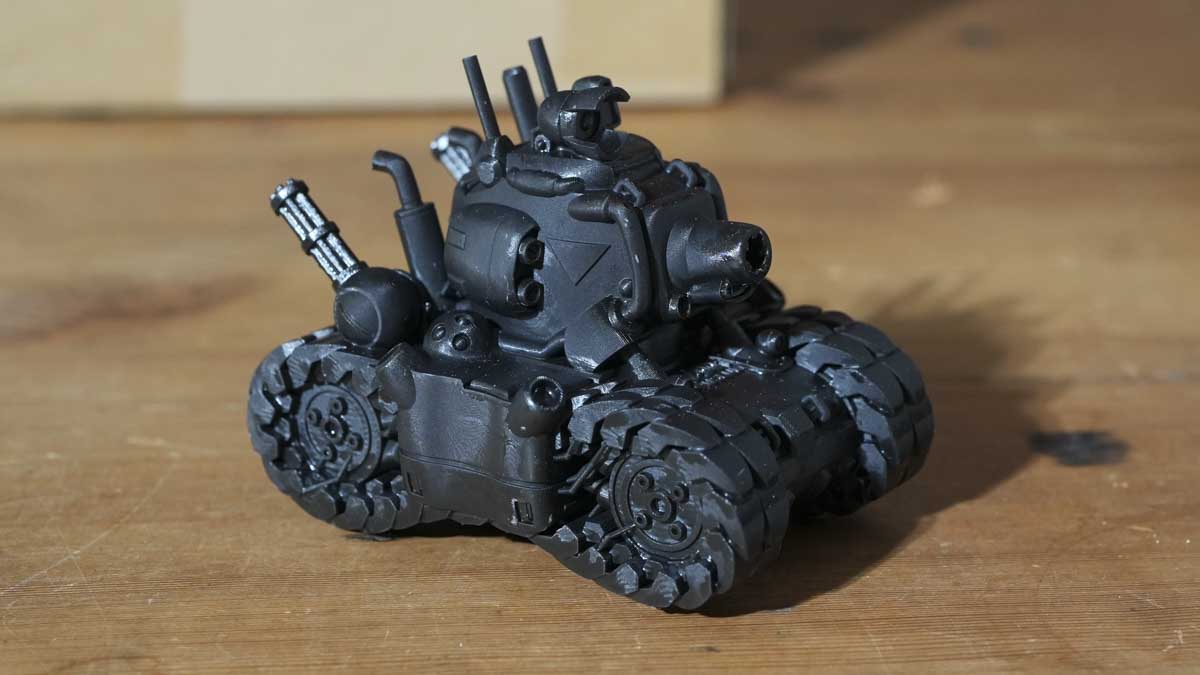
PreForm software
Once Form 4 is primed and connected to the local area network, you can connect to the machine via the PreForm software and dashboard. This software allows you to prepare your models and upload them directly to the machine without needing to transfer them via USB or another method. Formlabs has designed this system to be streamlined and intuitive, focusing on professional environments without distractions from manufacturer offers or "models of the day."
An issue we encountered during testing was that many larger pre-supported models could not withstand the machine's high-speed operations. However, when this issue has been encountered with other high-speed machines we've tested, when a print falls from its supports, it often spells disaster for the resin tank and, in one instance, the LCD. However, Form 4, with its advanced monitoring, is well-prepared for such obstructions. The mixer arm detects when something has fallen into the resin, and the print process automatically pauses until the obstruction is removed. During our tests, it was generally possible to retrieve dropped pieces of hardened resin relatively easily, run a cleaning sheet, and restart printing. This occurred about five times and exclusively with pre-supported models. Switching to supports generated with PreForm achieved a 100% print success rate and after a short time of getting to know the printer the switch to using the PreForm supports at all times makes sense.
Formlabs advertises that Form 4 is up to five times faster than its predecessor for certain types of prints. Although a few prints approached the four to five-hour mark, the majority were completed within two hours—considerably faster than many other resin 3D printers. The quality of these prints is notably high, with a finish comparable to injection-molded designs.
In standard mode or print speed of 0.100, prints from Form 4 appeared clear and accurate, with superb surface quality. When switching to high-quality mode 0.050, print times naturally extended. For instance, the 3DBenchy model in PreForm is estimated to take 1 hour and 14 minutes with support or 59 minutes without. In fine quality mode at 0.050, the print time extends to 2 hours or 1 hour and 39 minutes unsupported. For comparison, the Creality K1C can produce the same model in 55 minutes or 1 hour and 45 minutes with supports using standard settings.
Initially the print speeds might seem slightly slower than those from a COREXY FFF printer, however for small production runs, Form 4 dramatically reduces printing times. It can produce nine 3DBenchy models in 1 hour and 12 minutes with supports or 1 hour and 25 minutes without. Conversely, using the Creality K1C for the same task would take approximately 7 hours and 10 minutes or 15 hours and 47 minutes with supports—a significant difference in efficiency.
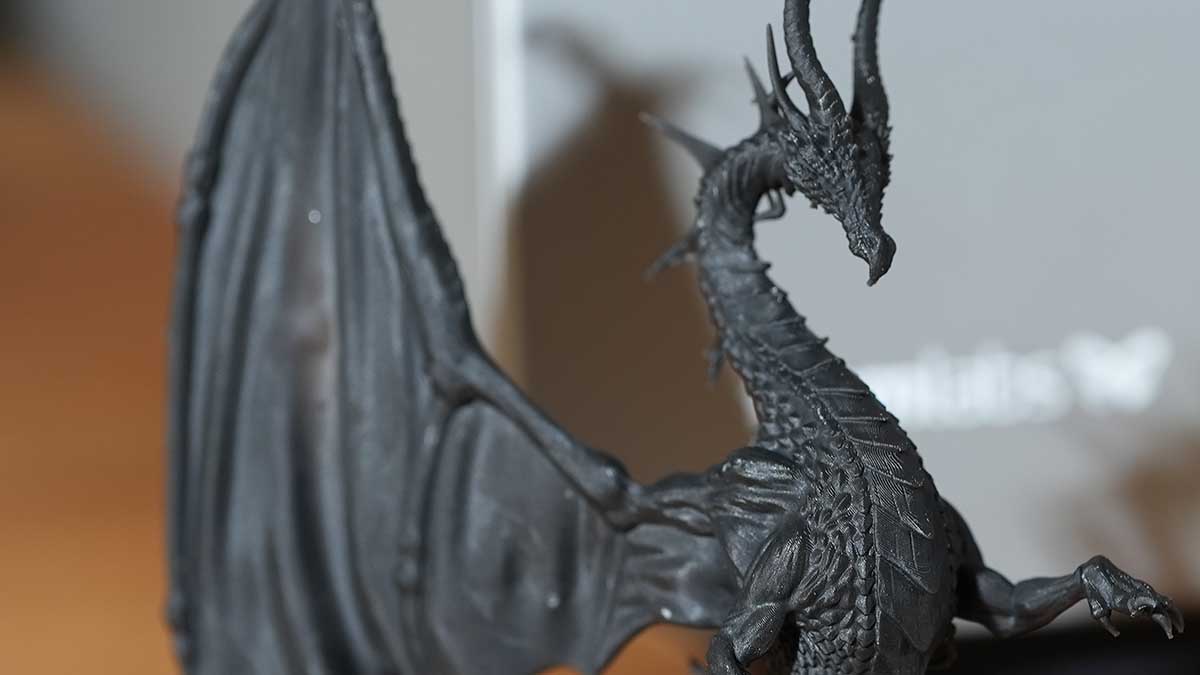
In a design studio where multiple iterations of a design are common, Form 4 enables fast processing of all designs simultaneously. Although the print platform may seem small, it generally suffices for most print jobs. For example, while the 3D Benchy model is relatively simple by today's standards, as the complexity and detail of the prints increase, the distinction between the quality and speed of an FFF printer and the Form 4 becomes more pronounced. Printing a detailed model like the Blue Young Dragon illustrates this well, showing that Form 4 finishes the print in 2 hours 53 minutes while the Creality K1C takes 9 hours and 45 minutes. It's not only the print speed but also the removal of the supports, on the resin model all supports were removed in a round a minute on the FFF print more like ten and some of the more delicate details around the claws were lost despite the high quality of the print.
The cleanup process of resin prints is a major consideration, and with Form 4, this aspect remains significant. The Wash and Cure machines, while optional, are nearly essential for achieving the best results and are among the best in their class. The second-generation Form Wash allows the use of either IPA or TPM as the washing agent, and we've chosen IPA for continuity and ease of air drying in our tests. The Cure machine then hardens the prints post-wash using 405 nm light and heat to evenly dry and cure the models. Although these machines are excellent, their cost is comparable to many other resin 3D printers on the market and then there's the cost of the IPA which to fill to a decent level is going to set you back a good £50/$50. For those looking to economise after investing in Form 4, there are less expensive wash and cure machines available.
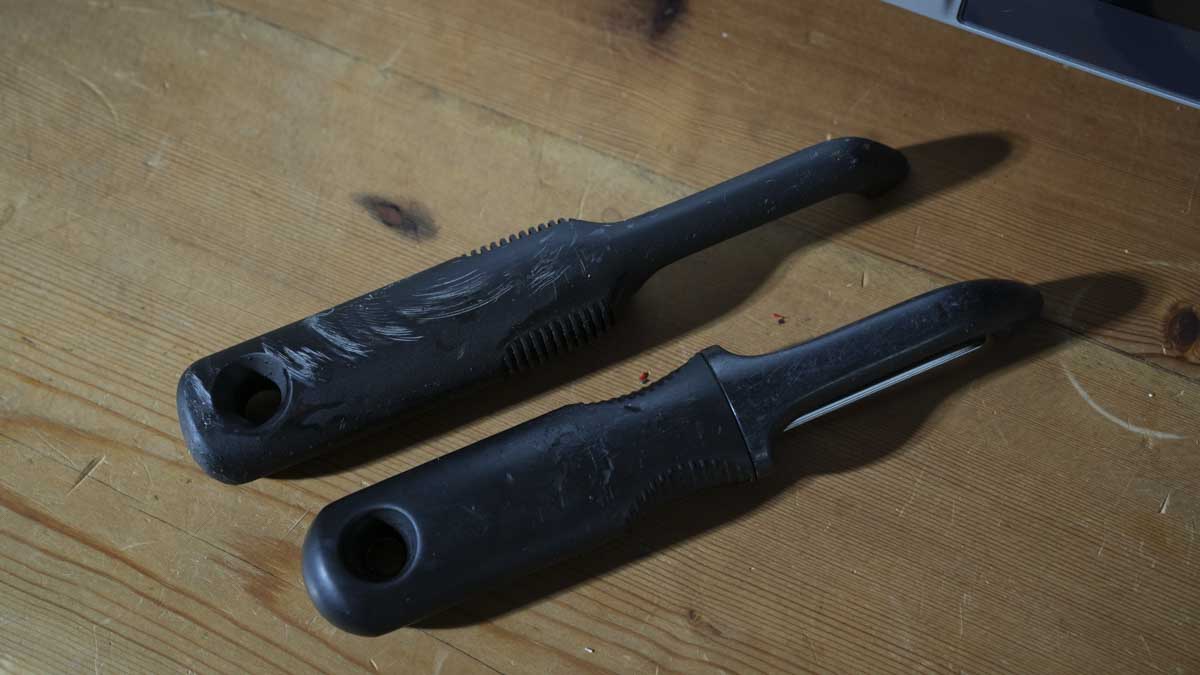
Cleaning the prints
When it comes to finishing the prints Formlabs have streamlined the process of washing, curing, and removing supports making sure it's as straightforward as possible: print the model, remove the build platform from the printer, place it into the wash, and start the machine. After washing, use snips to detach the print from the build platform, remove the supports, and then place the print into the Cure machine. Once the curing is complete, any final touches can be applied to finish the print. The support structures are designed such that a quick rub between washing and curing usually results in a clean surface. For optimal results, it's best to ensure all residual supports are removed before curing.
Print quality and accuracy is the main reason you would levitate towards the Form 4 over cheaper resin printers and at no point does the machines print quality disappoint. Using standard settings and V5 materials, the surface finish is exceptionally smooth, with only minor visible layering on some contours. By increasing the quality settings in the PreForm software, these layer lines become nearly invisible, though the print times will be longer.
In terms of quality, the output from Form 4 is comparable to that of Form 3+, with differences only discernible at the micro-detail level. However, the enhanced user experience and additional features make the Form 4 a worthwhile upgrade from the Form 3+.
Beyond standard resin
In this test we've looked at the standard V5 resins, but it's worth highlighting that this is just the edge of what this machine has to offer. The resin materials that will work with this machine enable all sorts of uses, from functional parts, Ceramic, Biomedical and moulding with each of these materials fine tuned for their intended usage.
More on an enthusiast level it's also possible to use non Formlabs' resin which will prove to be a cheaper option for many. More details of this can be found on the formlabs website https://formlabs.com.
Formlabs Form 4: Final verdict
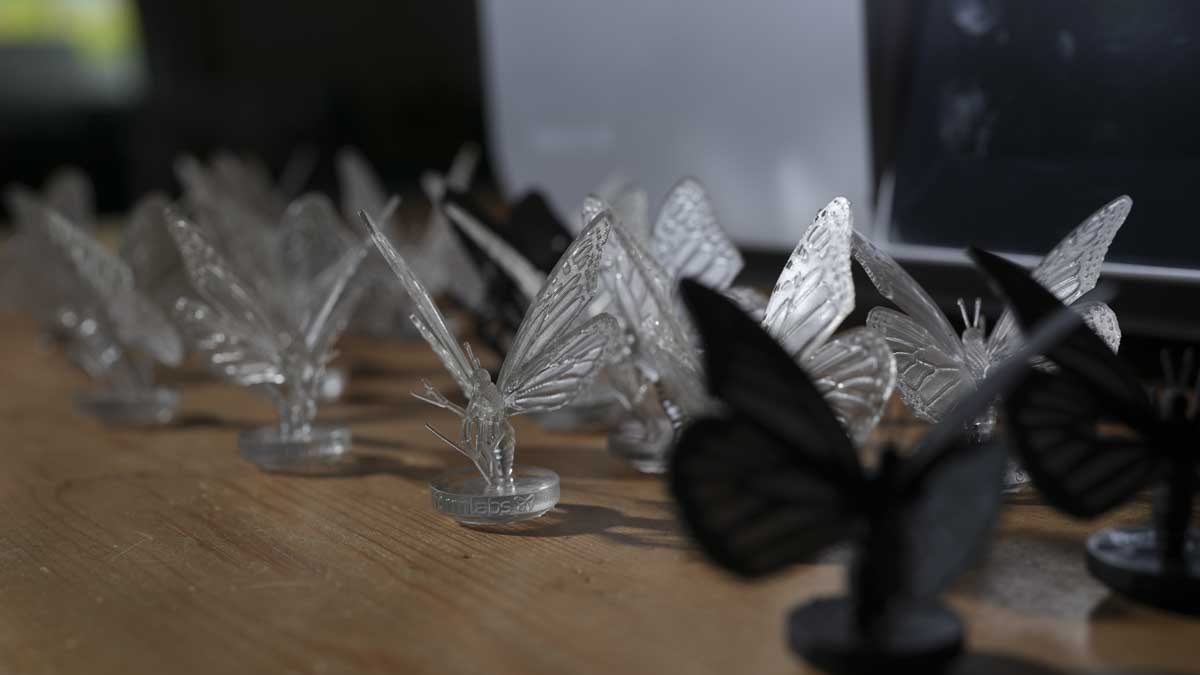
If you're in the market for a resin 3D printer that surpasses the print quality of all FFF 3D printers and offers a cost-effective professional solution, then Form 4 is among only a few that deliver such high standards in this price range. Right from the start, the machine impresses with its easy setup and intuitive workflow, which is straightforward enough for even those completely new to the technology to grasp.
While dealing with resin is typically a messy affair, Formlabs has made this process as manageable as possible with auto-feed and easy-to-dispense resin cartridges. The tanks are also easy to remove, safe to store, and use on a daily basis, with little to no fault.
For more sporadic use, where cleaning the machine or, more specifically, the tank is necessary, the process can be a bit more time-consuming. While the mixer arm can be easily cleaned in Form Wash, the tank requires a more manual approach. Despite the advanced design and the helpful cleaning sheet, it's more complex than some of its competitors.
Aside from cleaning, most other aspects of the workflow are straightforward, including swapping out resins. Maintaining cleanliness and methodical practices ensures smooth operation without issues. Form 4 stands out in two particular areas: its accuracy, quality, and reliability for intricate details and complex objects, which make it an ideal choice for jewellers and model makers, offering unmatched ease of consistency. Throughout testing, 8 litres of resin—clear, grey, and black—were used without a single issue, a stark contrast to some of the best, cheaper printers that often encounter failures.
The second area where Form 4 excels is in prototyping and small to medium production runs. Formlabs provided a test print file that demonstrated the machine's capability to produce small production runs of parts for their resin tank mixer, achieving quick and incredibly high-quality results. In our test we switched to printing a GoPro handlebar mount product, and successive runs produced fast and accurate prints without fault.
For those looking for one of the most reliable, high-quality, and least messy resin 3D printers on the market, the Form 4 has little competition at this price point.
Should You Buy the Formlabs Form 4?
The Formlabs Form 4 is ideal for professionals requiring high precision and reliability in industries such as prototyping, jewelry-making, modelling and small production runs. Its superior print quality, capable of handling intricate details and complex designs, makes it standout. The intuitive setup and workflow make it accessible, even for those new to 3D printing. Despite its higher upfront cost, its efficiency in managing resin and the minimal occurrence of print failures provide long-term value. Suitable for both frequent and occasional users, the Form 4 excels in rapid prototyping and small production runs, making it a top choice for businesses aiming for outstanding results without constant technical challenges.
Buy if...
Don't buy if..
For more tech tools for crafting, we've tested the best laser engravers