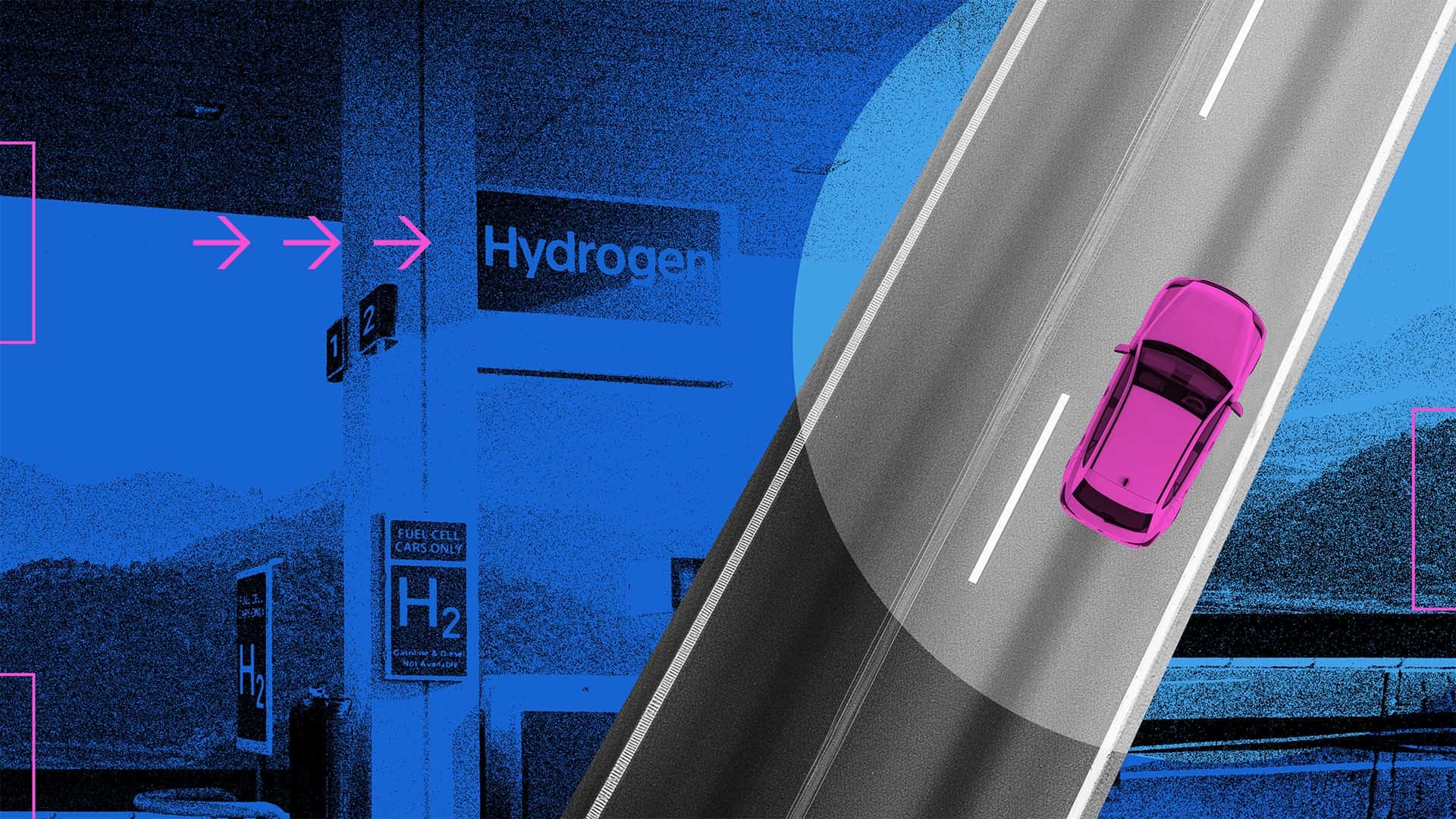
In 2021, Congress approved a $7.5-billion plan under the Biden Administration to build thousands of new electric vehicle charging stations around the country. Fewer than 10 stations have actually been built.
In the three years since the bill passed, EV enthusiasm has severely waned. Countries have started to roll back calls for ICE engine bans, some EV owners are switching back to gas, and automakers like General Motors and Ford—two of the largest EV producers in the US—are diverting more money to hybrids and plug-in hybrids.
The problem is that gas engines still spew emissions while the Earth gets warmer. The National Oceanic and Atmospheric Administration (NOAA) says there's a 60% chance 2024 will be the warmest year ever and a 100% percent chance it will rank in the top five.
So where do we go from here?
The solution may have been in front of us the whole time: Hydrogen. Although it hasn't been well received historically, hydrogen—much like electricity—has powered vehicles since before the turn of the century. Belgian inventor Etienne Lenoir built the first hydrogen-powered “Hippomobile” back in 1860.
Environmental concerns in the 1970s marked the first time modern auto manufacturers experimented with the technology in their vehicles. And in the 1980s, that expanded to military use. But hydrogen took a back seat in the US in the 1990s and was nearly obsolete by the early 2000s.
It wasn't until 2008—lightly coerced by the Japanese government—that Honda and Toyota developed their FCHV and Clarity models (respectively), the first hydrogen cars available to consumers at scale. Today, those two companies are still bullish on the technology while General Motors, Hyundai, and yes, even Ferrari are all dipping their toes in.
The problem is: How do we make hydrogen work on a mass scale?

Producing hydrogen on a mass scale certainly isn't as simple as flipping a switch. First and most importantly, it requires a ton of cash. General Motors threw down $35 billion for hydrogen fuel-cell, EV, and autonomy development through 2025, with $85 million coming via a joint investment from Honda. That partnership included a 70,000-square-foot fuel-cell development facility in Michigan, with a chunk of that cash going toward the Ultium EV platform, which currently underpins every Chevy EV and the Honda Prologue.
For consumers, only Honda’s CR-V e:FCEV—the company's first modern hydrogen SUV—is proof of that massive investment in hydrogen research. It goes on sale in California later this year. Honda plans to sell about 300 units annually, as the market for hydrogen vehicles remains limited. And the company will cover $15,000 worth of refueling costs in an effort to get more people through the door.
But the reality is, consumer-facing hydrogen isn't a top priority for Honda at the moment.
“Our primary activity in hydrogen, frankly, is not FCEV right now,” says Chris Martin, the Group Lead of Technical, Safety, and Regulatory PR for Honda. “It's more about growing the overall hydrogen economy. And ultimately, we do see FCEV as a bigger part of personal transportation later, but we need to grow the hydrogen economy to a point where it can already be in place to support the consumers and the regular drivers.”
That hydrogen economy starts on the commercial side. Alongside the hydrogen CR-V, Honda recently introduced a new hydrogen-powered Class 8 semi-truck that can drive up to 400 miles on a single tank. It’s the first of what Honda hopes will be many hydrogen-powered commercial vehicles.
“The broader strategy is to move into heavy equipment,” Martin says. “Battery electric is not necessarily a great solution for construction equipment, mining equipment, or Class 8 trucks that do long-haul trucking. Those sorts of things are primarily diesel-powered right now, which obviously is carbon-intensive, but also particulate emission intensive.”

Industries that rely on diesel have corporate targets to reduce emissions and greenhouse gasses, Martin says. Hydrogen offers a solution those industries crave. Once hydrogen is established on the industrial level, Honda believes the technology will trickle down to consumers.
“Once that happens, when there's an industrial level production of hydrogen nationwide, that opens up the possibility to produce FCEVs at an affordable scale,” Martin says. “And if it makes sense, then a wider range of fuel-cell powered vehicles will make it into consumer hands.”
There are still so many hurdles before we get to that point, though.
One of the biggest issues is at the source. Extracting hydrogen isn’t exactly a clean process—at least, not yet. As of 2021, more than half of all hydrogen production in the US was done via natural gas and coal. Excess energy from solar and wind could help curb those consumption challenges, with the National Renewable Energy Lab suggesting that 1 billion metric tons of hydrogen could be produced annually using renewable resources. But that type of clean hydrogen production on a mass scale is still years off.
Extracting hydrogen isn’t exactly a clean process—at least, not yet.
Splitting water into hydrogen and oxygen molecules is also immensely energy-consuming. About 60% percent of the energy used during the electrolysis process is lost. And many would argue that using electricity as a middle-man to hydrogen production is a waste of energy (literally) when battery electric vehicles themselves exist.
It’s also extremely cost-prohibitive. Estimates suggest hydrogen is as pricey as $12 per kilogram to produce, whereas fossil fuels come in at around $1.7 per kilogram and renewable electricity is $8 on the high side. And that ultimately means higher prices at the pump.
Hydrogen costs skyrocketed to as much as $36 per kilogram early this year. That means it would cost you more than $200 to fill up your Toyota Mirai's 5.6-kg tank. With an estimated driving range of 402 miles, the Mirai costs about $0.50 per mile to operate—give or take a few cents. Traditional hybrids like the Toyota Prius operate at anywhere from $0.15 to $0.18 per mile (depending on fuel prices), and a Tesla Model 3 only costs about $0.10 per mile. Naturally, consumers aren't seeing any cost benefits by switching to hydrogen.
Hydrogen stations aren’t cheap to produce, either. The State of California Energy Commission quotes an all-in price of at least $6.5 million per hydrogen fueling station. The numbers vary wildly depending on who you ask, but when the cost of an EV charging station is roughly $110,000, hydrogen is still a huge investment comparatively.
Right now, there are only 53 hydrogen fueling stations for consumers in the US—52 in California and one in Hawaii. There are also a handful in Canada. Shell recently closed its seven hydrogen fueling stations in California for light-duty vehicles citing “hydrogen supply complications and other external market factors.” You can probably construe “external market factors” as not enough of a need; Fewer than 3,000 hydrogen cars were sold in the entire US in 2023.
Martin says it’s a classic case of chicken and egg. Would more hydrogen stations lead to more hydrogen cars? Or is it the inverse? It’s unclear, and at this point, no one is willing to budge.
“We've tried making the FCEV vehicles the first step and then letting the refueling infrastructure and the hydrogen supply come later,” Martin says. “Unfortunately, that just hasn't worked so well in expanding the acceptance of the vehicles and getting a larger refueling infrastructure.”

Then there are the safety concerns associated with driving around with a hydrogen fuel cell under your hood. The Internal Consortium for Fire Safety, Health, & The Environment says “the danger of electric shock is great” with fuel-cell vehicles and that the “flammability concern[s] of the fuel translates into the design needs for the vehicle itself.” Simply put: Hydrogen cars need to be built safer than gas cars.
Honda takes those safety concerns seriously. The company's fourth-generation fuel cell is stronger and more corrosion-resistant. The aluminum shell is wrapped in carbon fiber, and instead of silicone rubber, Honda now uses two high-strength metal plates precisely welded for increased durability while still allowing coolant to flow between them.
“We've had fuel vehicles on the market for years and I don't believe that we've ever had a consumer experience of fire,” Martin tells me. “So we do know what we're doing in that respect. The tanks are extremely well designed and extremely shielded against crashes.”
That level of special engineering and precision manufacturing requires an equally special building process. Rather than building the e:FCEV alongside garden-variety CR-Vs, the hydrogen SUV is built at Honda’s Performance Manufacturing Center (PMC) in Ohio, where Honda produced its NSX supercar.
At PMC, Honda can take extreme measures to ensure fuel-cell safety and viability.
“It's a good place to build this sort of specialty vehicle that requires a little bit more precision,” notes Martin. “It's pretty important to us to make each one of these right.”
Would more hydrogen stations lead to more hydrogen cars? Or is it the inverse?
Assuming we can overcome these seemingly impossible obstacles, the benefits on the consumer side are too great to ignore.
Filling up a hydrogen car takes five minutes at the pump, roughly the same time as a normal fuel stop; Even the fastest electric cars take about 20 minutes to recharge these days. The only thing spewing out of a hydrogen-powered car’s tailpipes is water vapor. And many modern hydrogen fuel cells are rarely affected by extreme heat and cold. BMW says its iX5 is completely “unaffected by weather conditions.”
That's a five-minute fill-up getting you 300 miles of a completely clean-burning fuel source, again, in theory. Assuming the correct steps are taken to ensure safety and availability, there are almost no downsides.
“We want to give consumers things that work for them,” says Martin. “But at the same time, we have these huge carbon reduction goals. So if we were solely focused on what we could sell right now, immediately, we wouldn’t be investing in all this future research. But we're looking much longer term, and it just makes too much sense. Hydrogen makes too much sense to leave it off the table.”

On the governmental side, while most of the headlines focus on the Biden Administration’s huge EV push—that so far hasn’t produced a ton of fruit—the US government is also quietly working on hydrogen transportation technology in the background.
Just this March, the Department of Energy (DEO) put $750 million toward 52 hydrogen projects across the US under the Bipartisan Infrastructure Law. That cash will go toward improving electrolysis technologies, reducing costs, and helping hydrogen manufacturing overall. It should also create 1,500 new jobs in the process, particularly in areas affected by growing energy-related job losses like Appalachia and the Great Plains.
A big facet of that investment includes defining exactly how hydrogen will be produced in the US. There still isn't a clear outline yet, but the DOE does offer a deeper dive on its website that lays out some of its clean hydrogen requirements for new facilities. That plan also includes up to 10 years of tax credits for older facilities that are willing to make the switch to renewables (Section 48).
Still, as with Honda, the bulk of hydrogen production—at least initially—won’t be for light-duty vehicles. Hydrogen has to work in shipping first; semi-trucks, cargo ships, cargo planes, etc. The idea is that, once hydrogen becomes viable for shipping, it could (in theory) also be viable for consumer use.
But that brings us back to the beginning of the story.
A $750 Million investment in clean hydrogen production is great in theory, but it needs to be put into action. As we saw with the Biden Administration’s $7.5-billion EV plan, there’s been barely any movement on a bill passed more than three years ago. The law could be scrapped entirely in November if Donald Trump returns to office, who plans to roll back many of the Biden Administration’s proposed clean energy solutions.

Of course, there are still so many hurdles to climb before hydrogen can become a viable source of energy; environmental impact, lack of fueling stations, costs, safety concerns, and government regulations. But as the market shift to electrification proved, it’s not impossible.
The first Nissan Leaf only started production in 2010, while most charging companies only popped up in the last 15 years. In a relatively short time, we saw EVs rise to a level once thought unprecedented. They still only make up about 16% of the total market share, but compare that to 2010—when that figure was just 0.01%—and they’ve come a long way.
Assuming we’re willing to invest as heavily in hydrogen over the next decade as we did in electrification—financially and environmentally—there’s a very real chance that mass-produced hydrogen vehicles could become a thing within the next 15 years. The benefits—like refueling, reduced range anxiety, and little to no environmental impact—would make it easier for even the most EV-averse customers to make the switch.
Hydrogen can work. We just have to be willing to make it work.
Update: An earlier version of this story noted a $35-billion investment by General Motors and Honda for hydrogen development. That $35-billion figure represents the total investment by GM for multiple projects (including hydrogen); Honda and General Motors have only spent $85 million in joint hydrogen development.