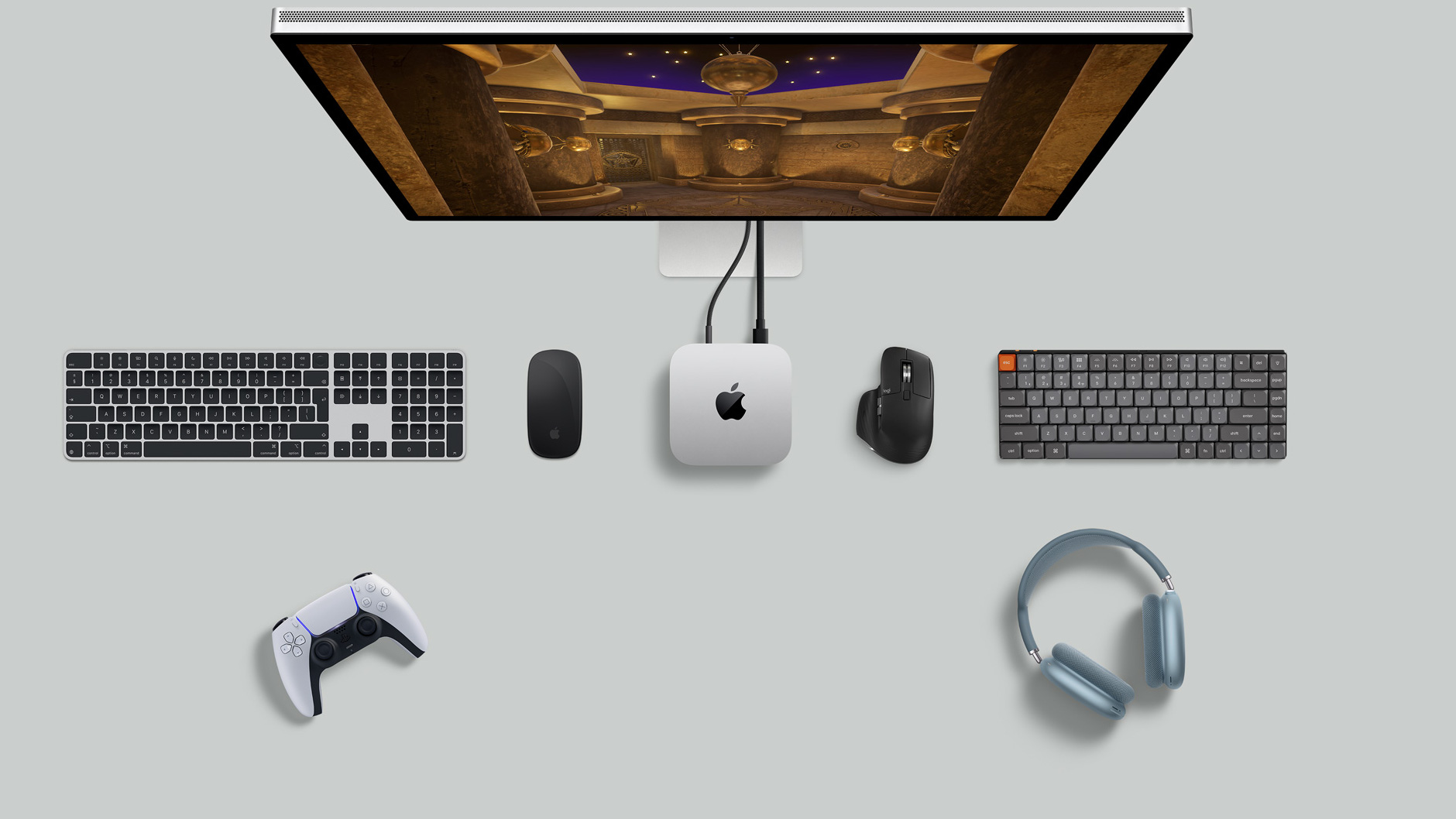
Apple can’t ship its new Mac mini fast enough. Launched in October 2024, this new ultra-compact version of its popular desktop model is now equipped with the M4 and M4 Pro chipset for the first time. Apple silicon, first introduced in November 2020 is now on its fourth iteration. What benefits does it bring to the new mini form factor?
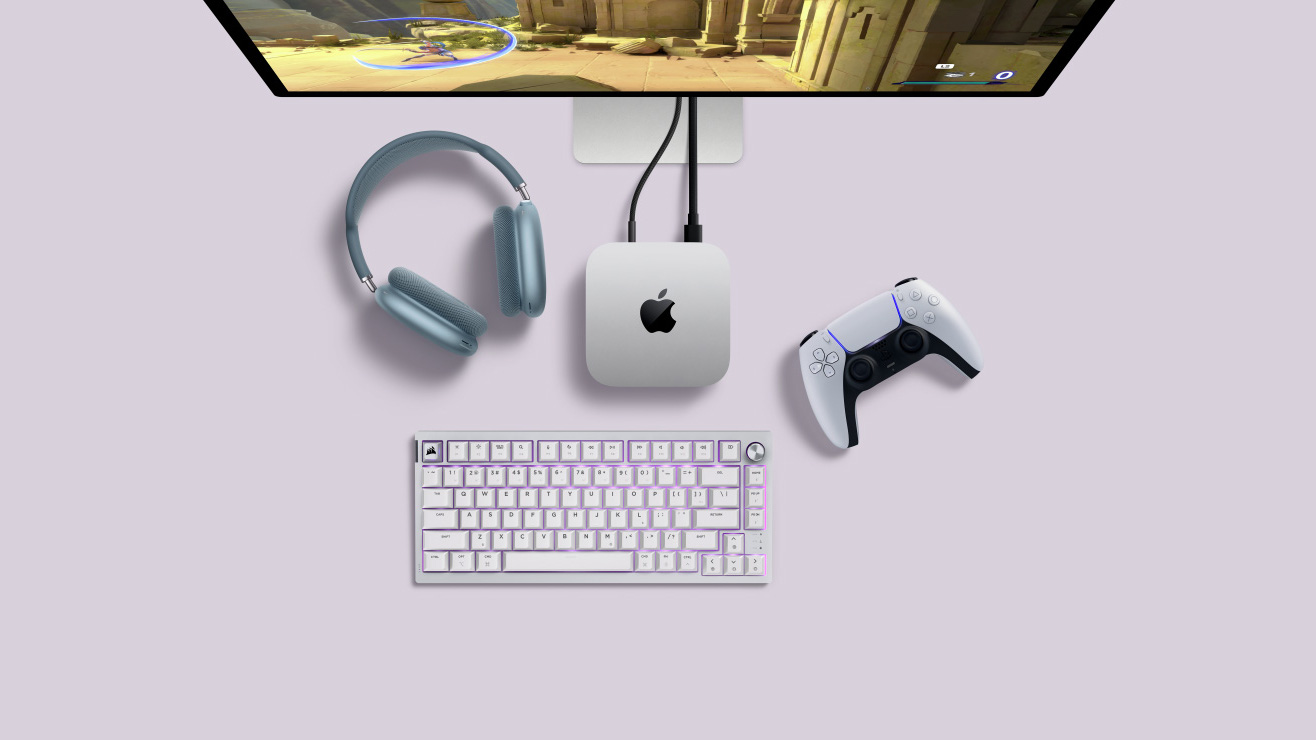
The new mini is a remarkable machine. At just 5 inches by 5 inches, it’s substantially smaller than the outgoing model, and the new processors double and even triple the processing power of its predecessor. The M4 Pro model can have up to 64GB of memory and an 8TB SSD drive, making it a highly effective machine for video, image and sound editing. The packaging is also impressively compact, thanks to the computer’s small scale, although there’s still no way of shipping a Studio Display around the world without a great deal of protection.
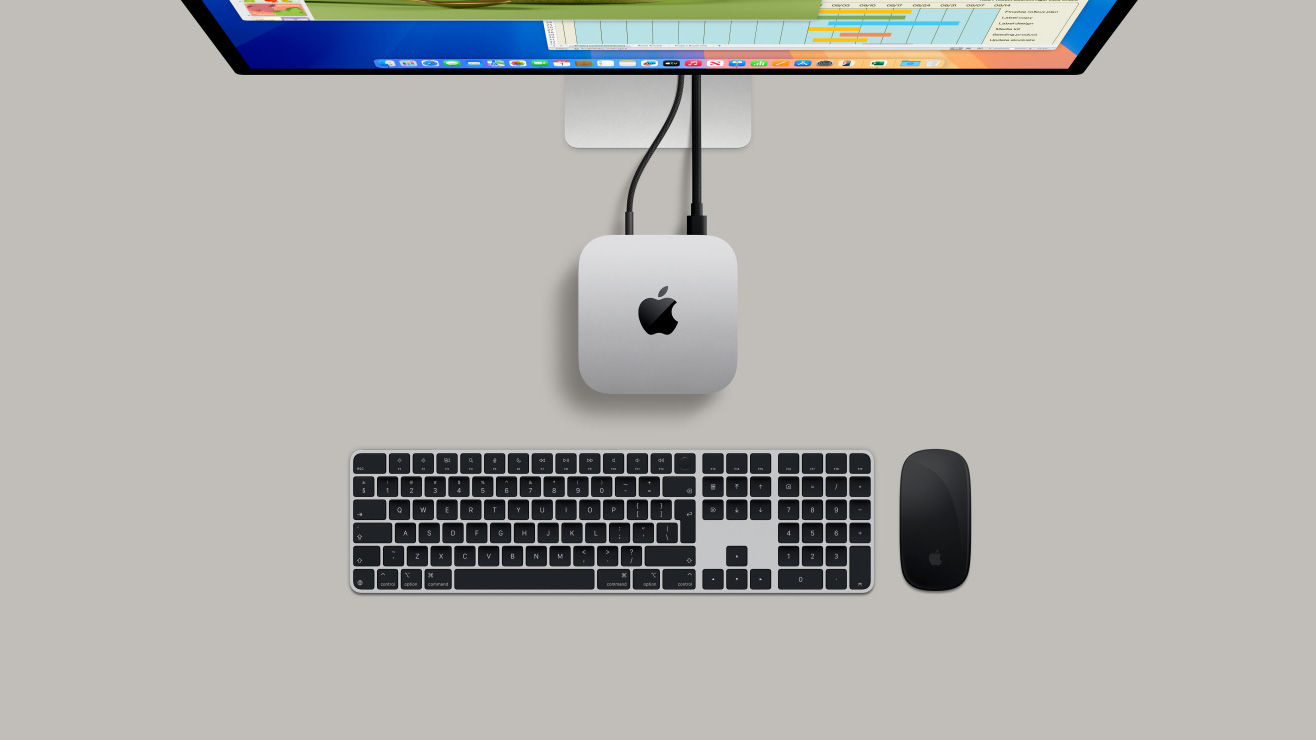
Apple is now well advanced on its roadmap to 2030, by which point it hopes to have a fully carbon-neutral product line-up. The mini represents a big step towards this goal, requiring in-depth work and research across the entire supply chain to create the first ever carbon neutral Mac. Other targets are coming sooner, such as the removal of all plastic from packaging by 2025.
Apple insiders on shrinking the new Mac mini
To find out how the company came to integrate its very own silicon into this mainstay of modern computing, we spoke to Apple’s Kate Bergeron, Vice President, Hardware Engineering, and Thomas Boger, a Senior Director of Mac and iPad Product Marketing, to get the low-down on the mini.
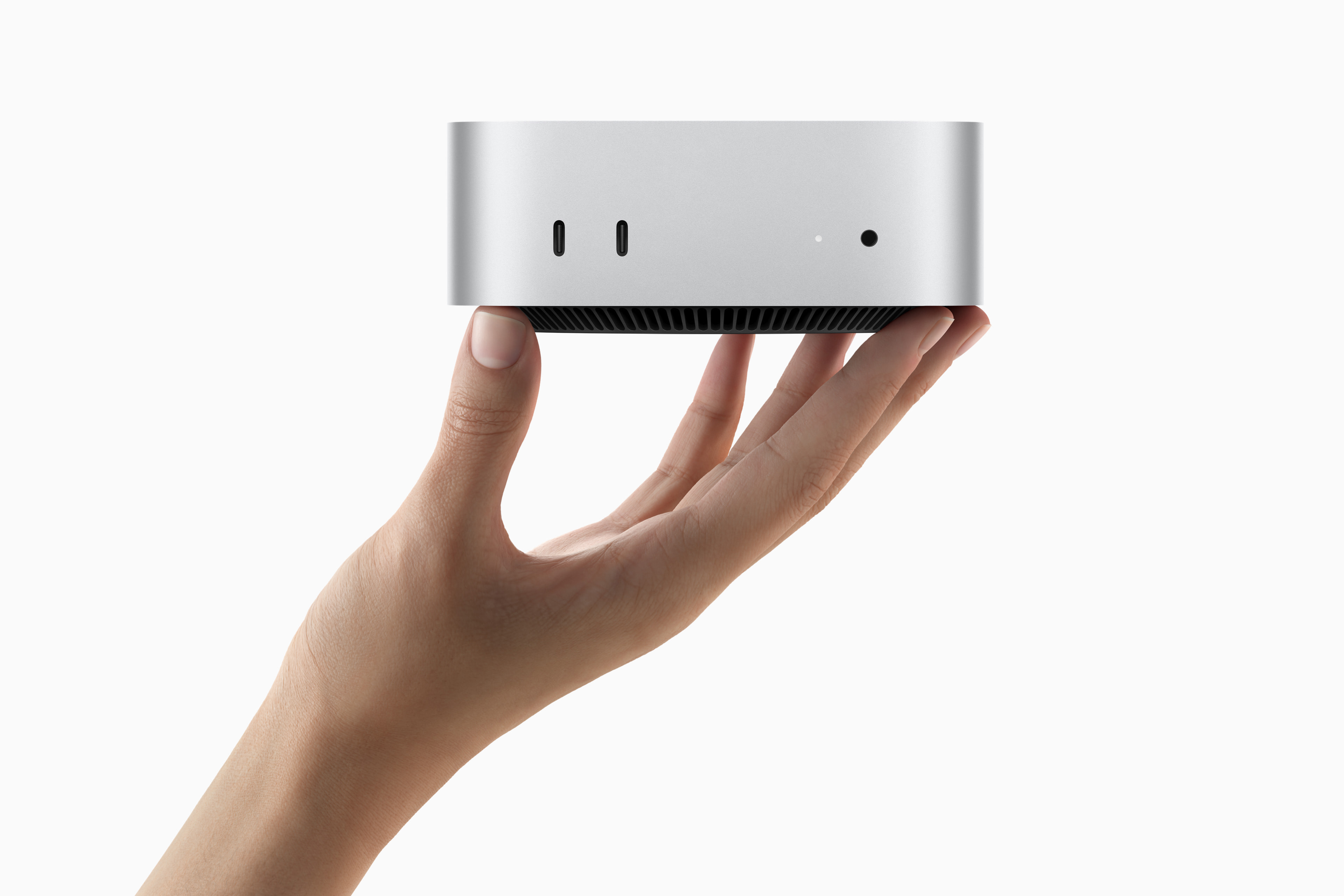
Wallpaper*: Tell us about the importance of the new Mac mini
Thomas Boger: It’s got quite the reception from our customers. Mac mini is our most versatile Mac, because of its size. It’s used at home, on desks but also all over the house – as a server, connected to a television, or part of a photography, music or video set-up. It has great connectivity as well. Outside the home, the mini is popular with small businesses, for everything from admin to creative work.
It’s also a product that’s popular with large institutions – it fits in well and is very energy efficient, especially in mission-critical use like healthcare, which benefits from Mac OS’s incredible reliability. With this launch, we’ve got a new product that hadn’t yet been redesigned around Apple silicon.
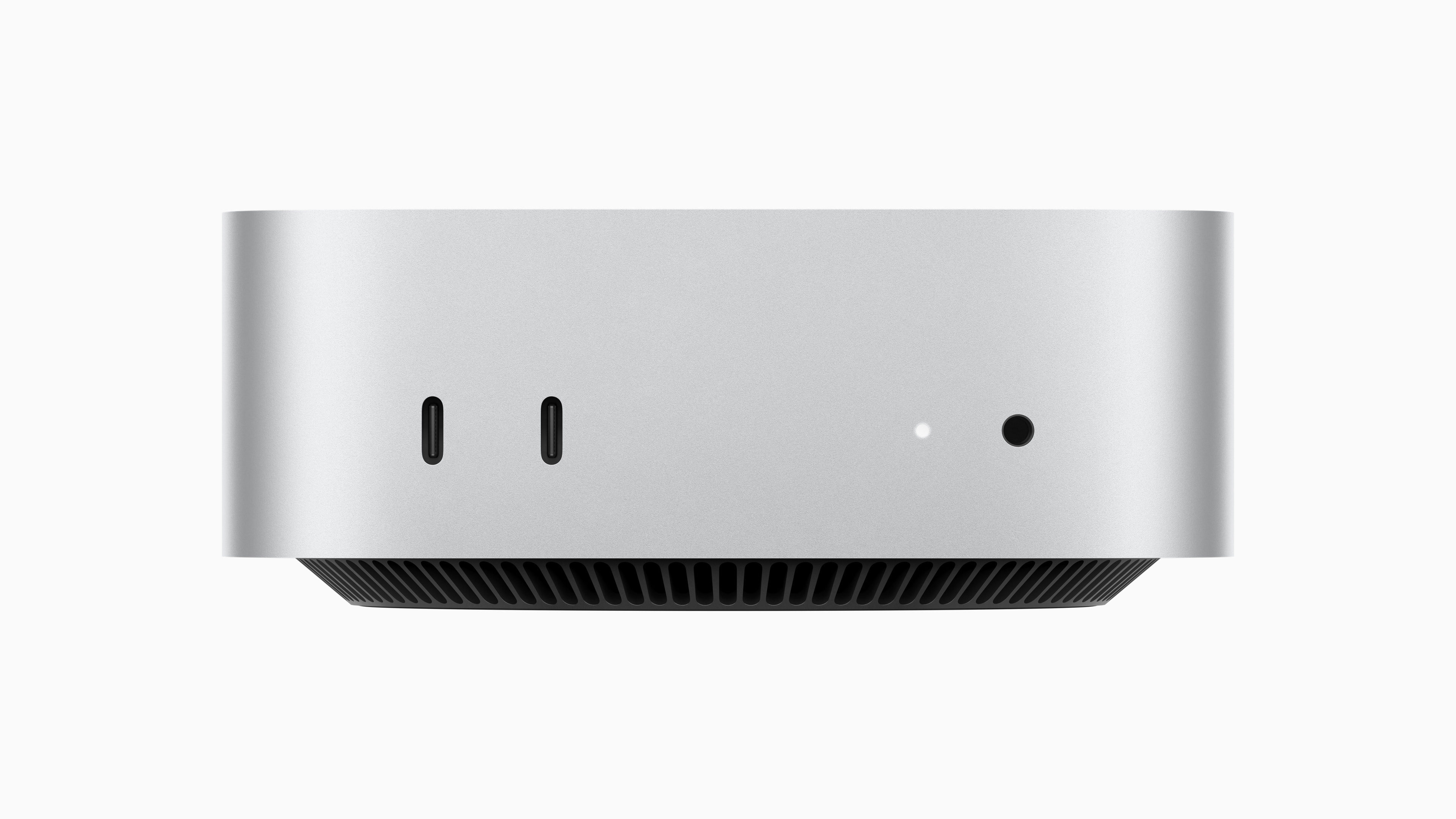
W*: How has the Mac mini evolved over time?
Kate Bergeron: We’re almost at the 20th anniversary of the Mac mini – it was first introduced in January 2005. We hadn’t had a chance to sink our teeth into the possibilities of Apple silicon for the mini. It’s always been our most compact Mac, but with this iteration we’ve taken quite a journey with our CNC technology. With our first extruded aluminium cases we had to cut off quite a bit of waste [material] to make them work. We’ve got more and more efficient.
The Mac Studio pioneered our efficient extrusion process – ‘impact extrusion’ – where we used as much of the material as possible. We did this by switching to a special nylon wire with diamond plating to cut the aluminium, as opposed to a conventional saw. This saved 3mm of wastage for each unit. We also changed the profile of the extrusion itself from round to square to save even more material – it shows how we obsess about things.
‘We set out the goal of making this our first carbon neutral Mac’
Thomas Boger
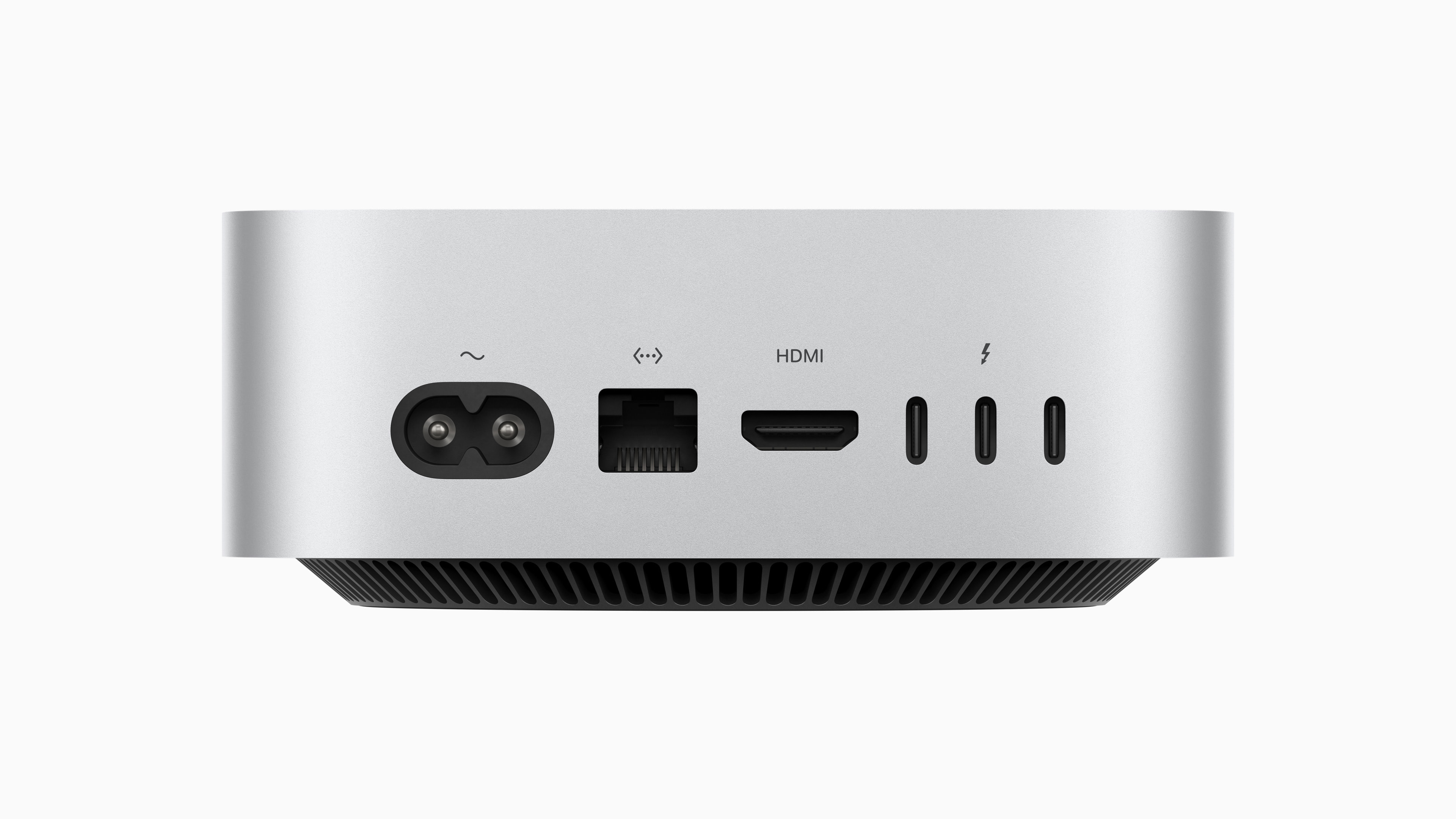
W*: Did the physical size of the new mini constrain the design team?
KB: There’s always this great tension between the design team and the engineering team. We did a lot of thermal simulation work, so we could model how to construct the system and whether it needed to be wider or taller. Pretty early on we locked down the system size, scaled so it could accommodate the M4 Pro chip. We want to find a nice balance – it seems we only do the Mac mini every ten years.
TB: We also set out the goal of making this our first carbon neutral Mac. We have 100 per cent recycled aluminium, recycled copper, zinc and even steel, including in our logo.
KB: A single ingredient won’t necessarily get you to that destination. We also have to calculate the manufacturing electricity, which is the largest source of emissions for the mini. Then there’s the energy footprint of the user, as well as spending time putting the systems into low-carbon shipping.
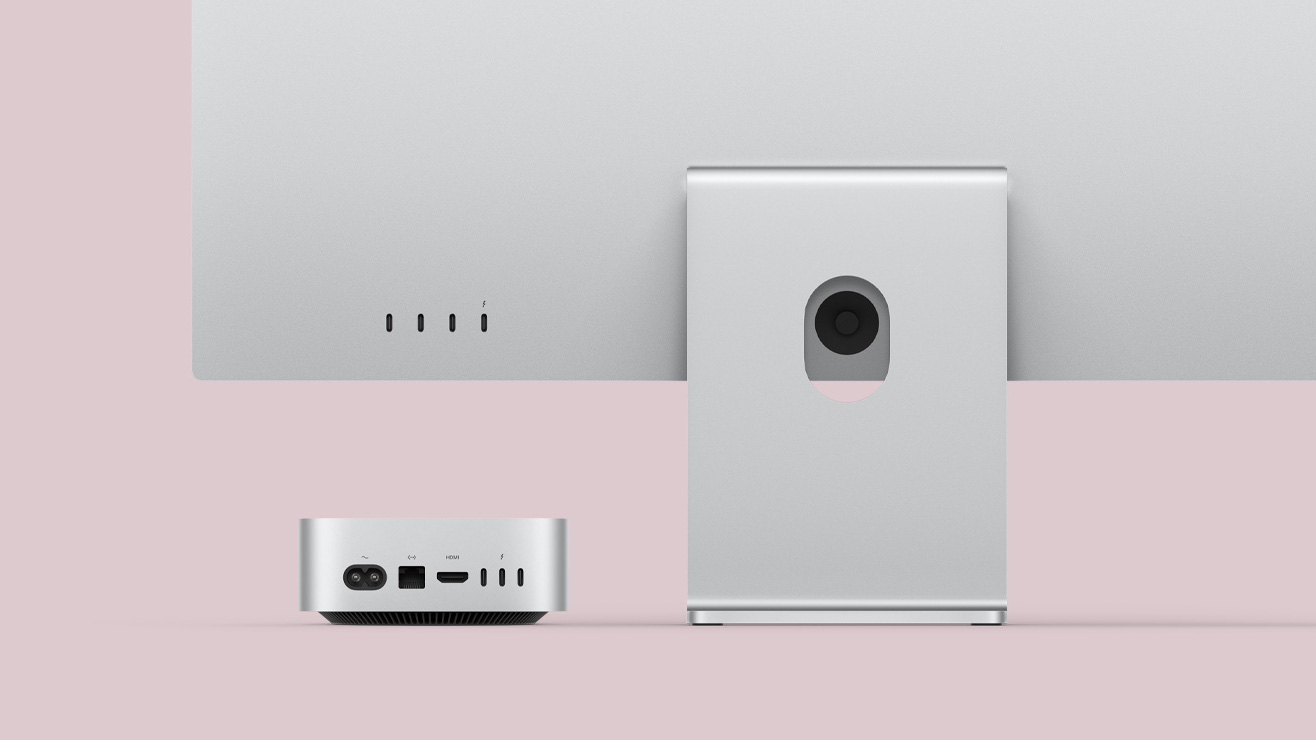
W*: How does this impact on your supply chain?
KB: It's dependant on the material. We’re working with all our suppliers. We also have a very capable set of engineers, including a materials team, that’s very focused on working towards these goals.
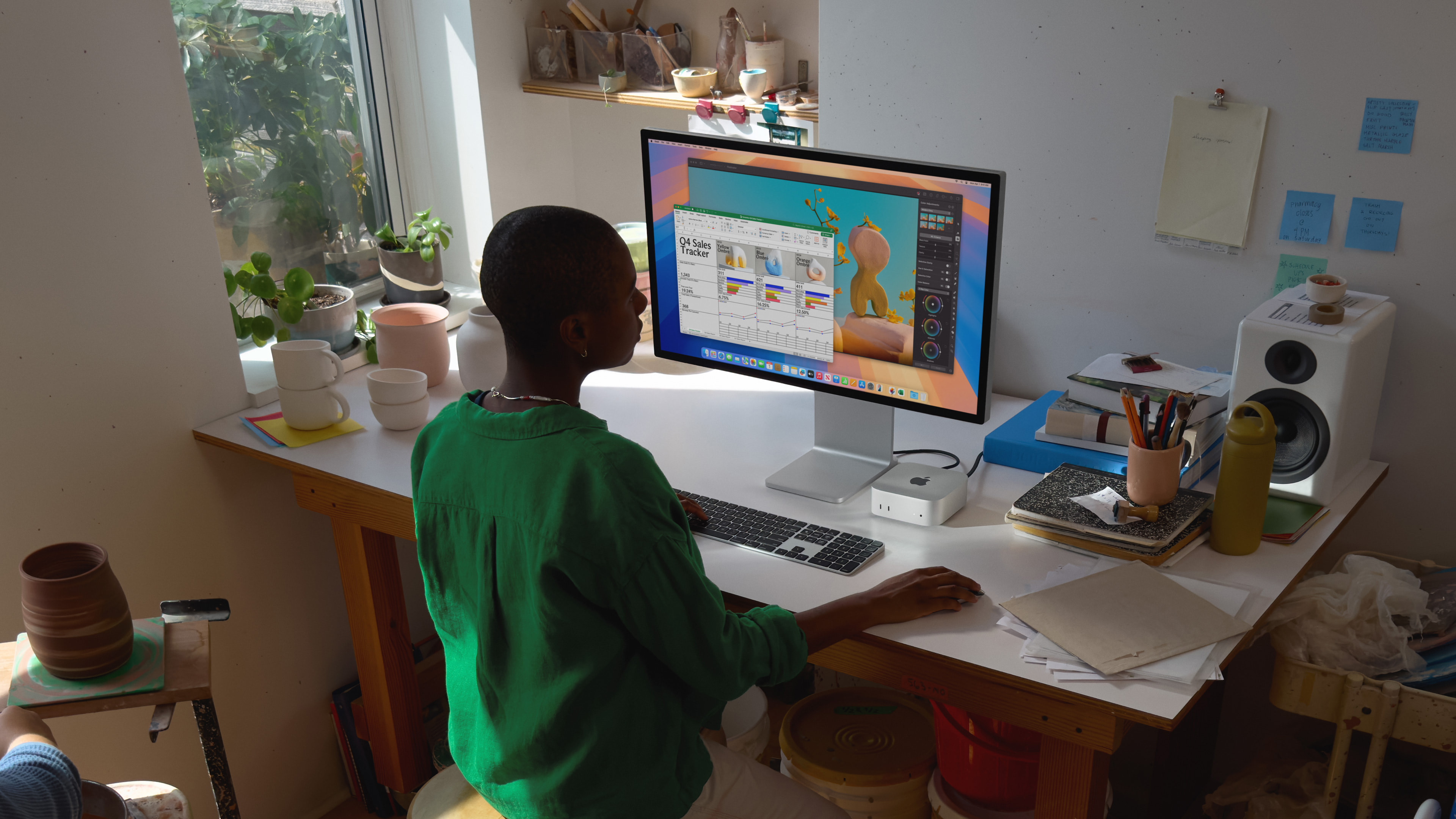
W*: Does that mean you’re sourcing manufacturing power from renewable sources?
KB: Yes. It’s about working with vendors and local governments, trying to find ways to make that feasible.
TB: You can see it’s quite the comprehensive effort, all the way from the source materials we use to all the way through the whole design and manufacturing process, all the way to getting the product to the customer, and then off-setting their energy use.
KB: We felt good about using the Mac mini as a first carbon neutral product – it does represent a good look at the Mac line in its entirety to make sure all this work translates well into future products.
TB: I think the combination of the redesign itself around Apple silicon, and the achievement of carbon neutrality, is a testament to how Apple approaches all of its products. We’re always trying to make the best product we can possibly make in every dimension, and I think this new Mac mini really embodies that philosophy.
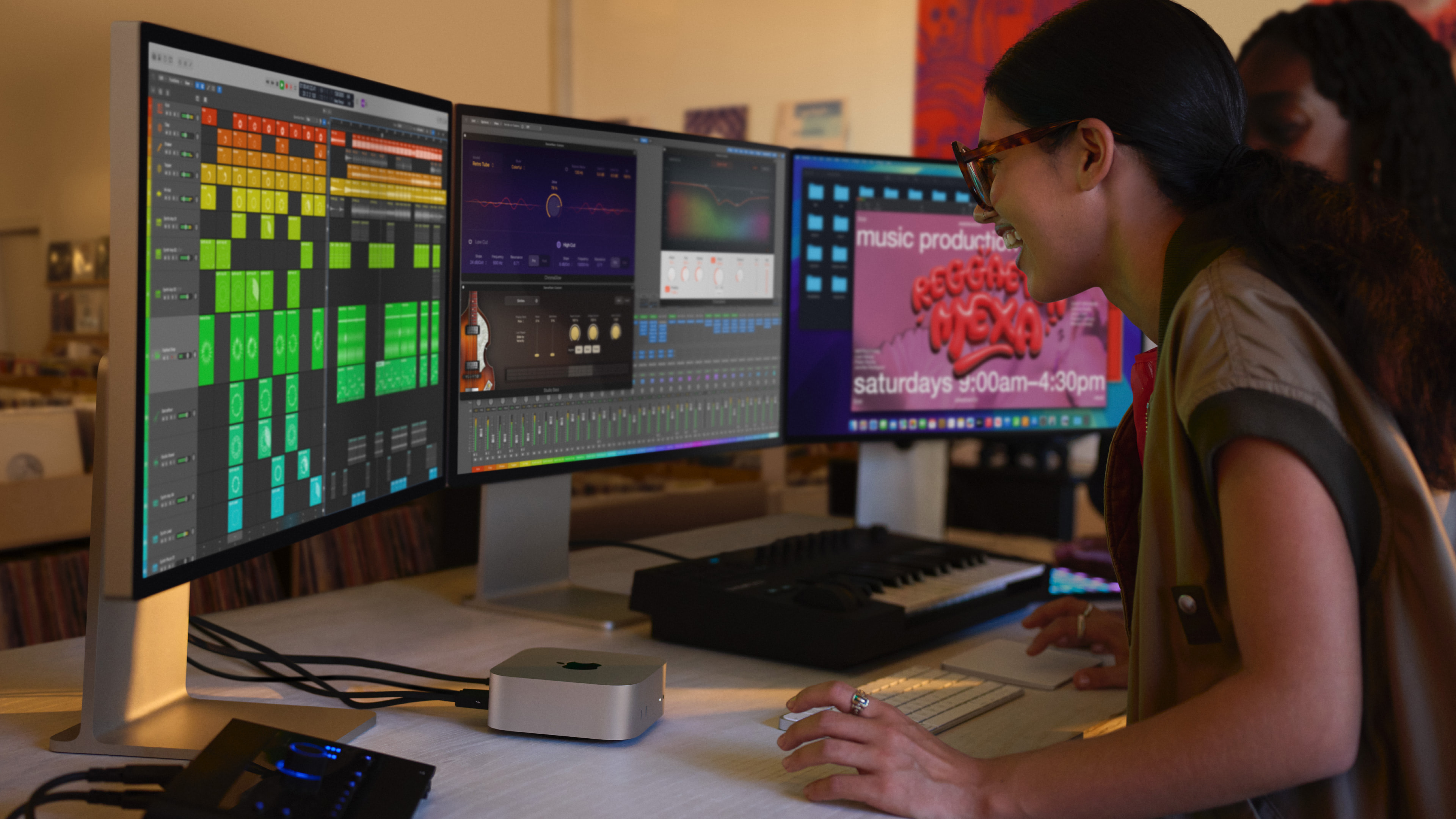
W*: What are the benefits of Apple silicon?
KB: Working so closely with our engineers gives us a new freedom, it’s truly the essence of Apple.
TB: What's so important to understand is that unlike the rest of the industry, where you have merchant chip vendors creating a bunch of chips and other vendors taking those chips and trying to design products around them, we do the exact opposite. We know what our product road map looks like. Our chips are designed specifically for our products. This is radically different to the rest of the industry, so we have a tremendous advantage.
Apple silicon was born with iPhone in 2020. What’s great about it is that it’s a very scalable architecture – we scaled it up for iPad, then for Mac, and we’re now on our fourth generation. Every M-series chip and Mac that we’ve made since 2020 runs Apple Intelligence, which is also a key aspect of the Mac mini. It’s a great system for AI.
‘We never talk about performance without talking about how much power it requires. It’s a relentless focus’
Thomas Boger
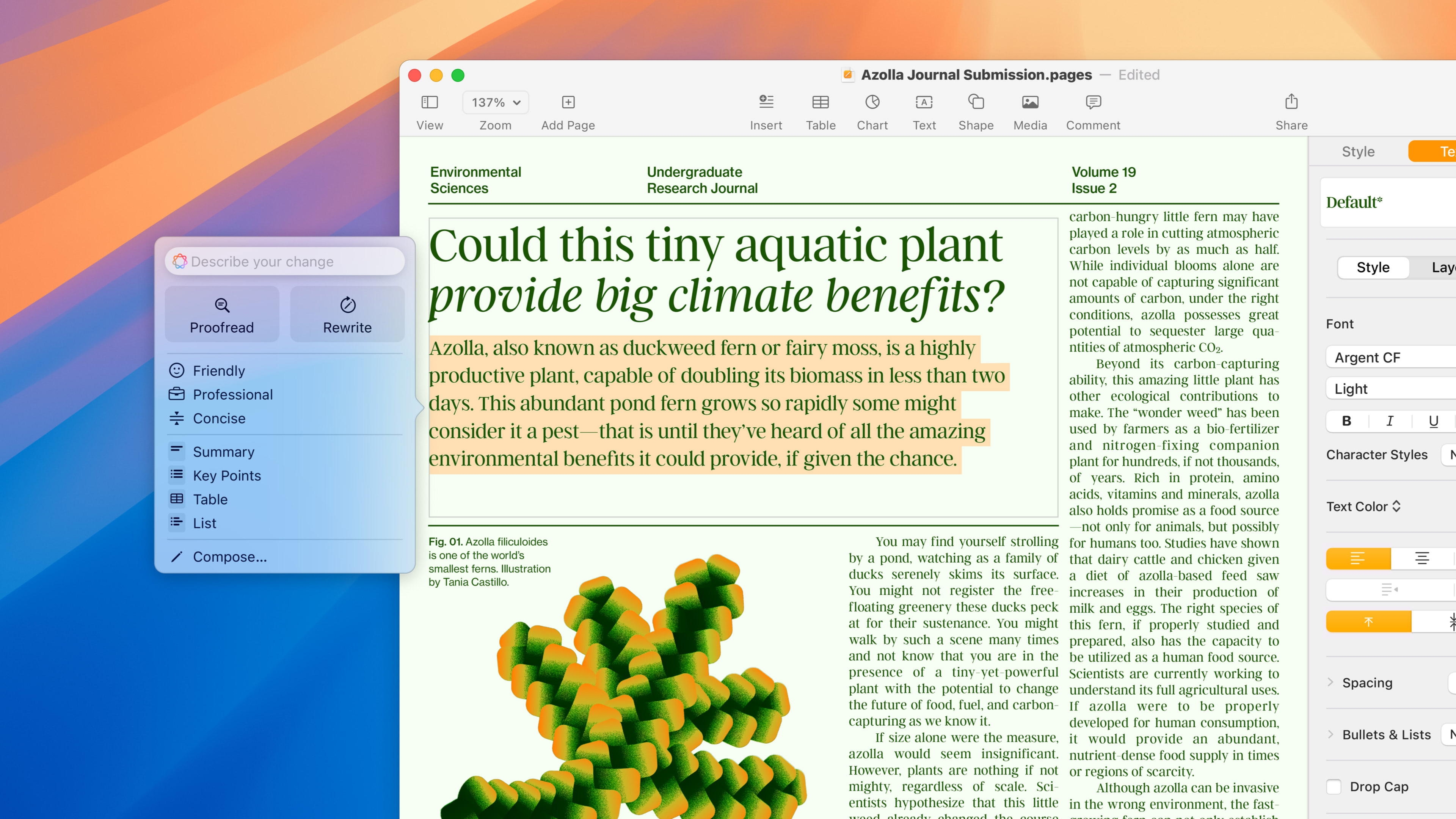
W*: Is aluminium still the best material for your purposes?
KB: At this point in time, I would say yes. There’s thermal performance and structure – in a device like a laptop, it’s very important.
TB: Then there’s the intangible part, how our products feel in your hand. How beautiful aluminium feels – this is very important to our customers. Their Macs are such a vital part of their lives, they rely on Mac.
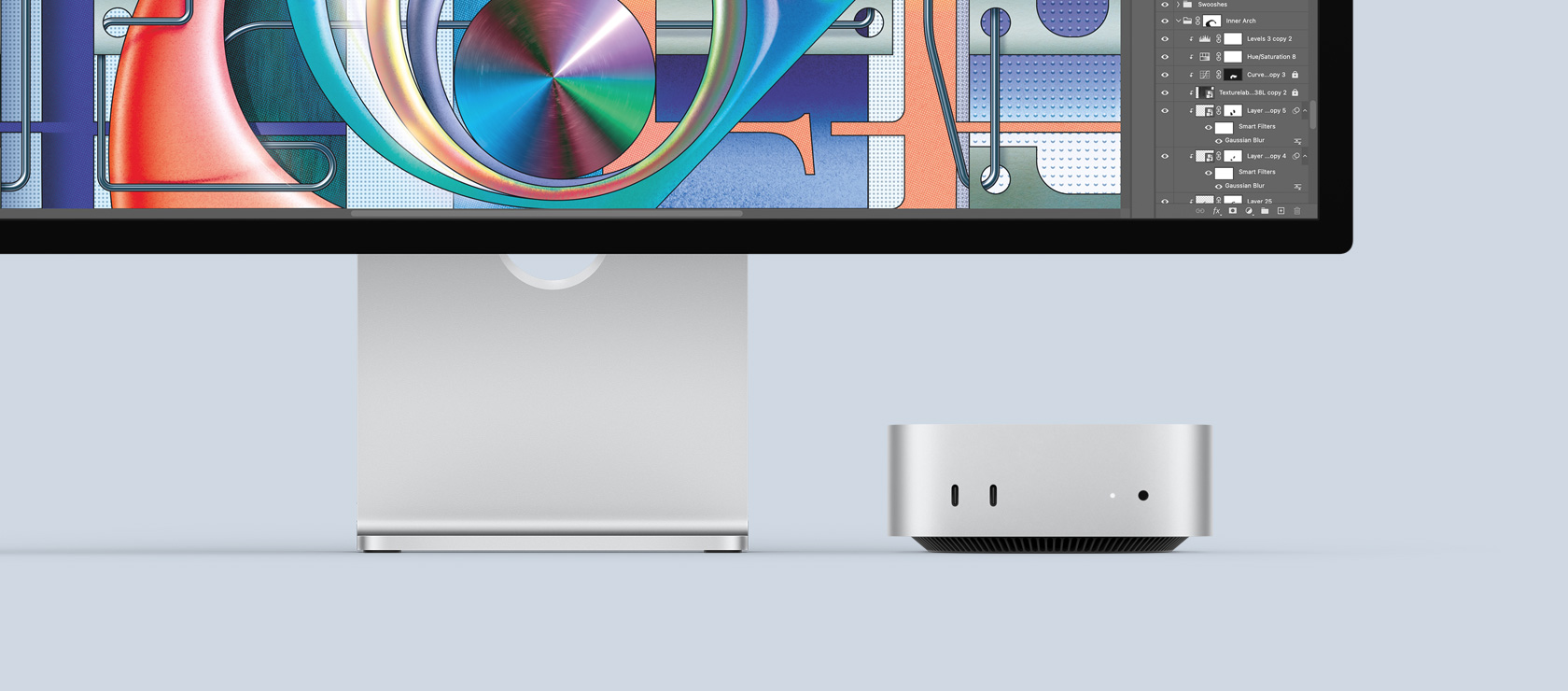
W*: Do you think AI will alter the form factor of computers and start making them more discrete and invisible?
KB: We don’t speculate on where we’re going. But Apple silicon gives us a toolkit of capabilities at Apple which makes it a very exciting time.
TB: The Silicon Team is excited to remove constraints on the design team to make products like the Mac mini possible, with a relentless focus on performance per watt. That’s the fundamental name of the game. We never talk about performance without talking about how much power it requires. It’s a relentless focus.
One of the reasons Apple silicon is so special is that it started on the iPhone, a device so small that you have to have a maniacal focus on performance per watt. This discipline is what makes these amazing new products.
Apple Mac mini, from £599, Apple.com