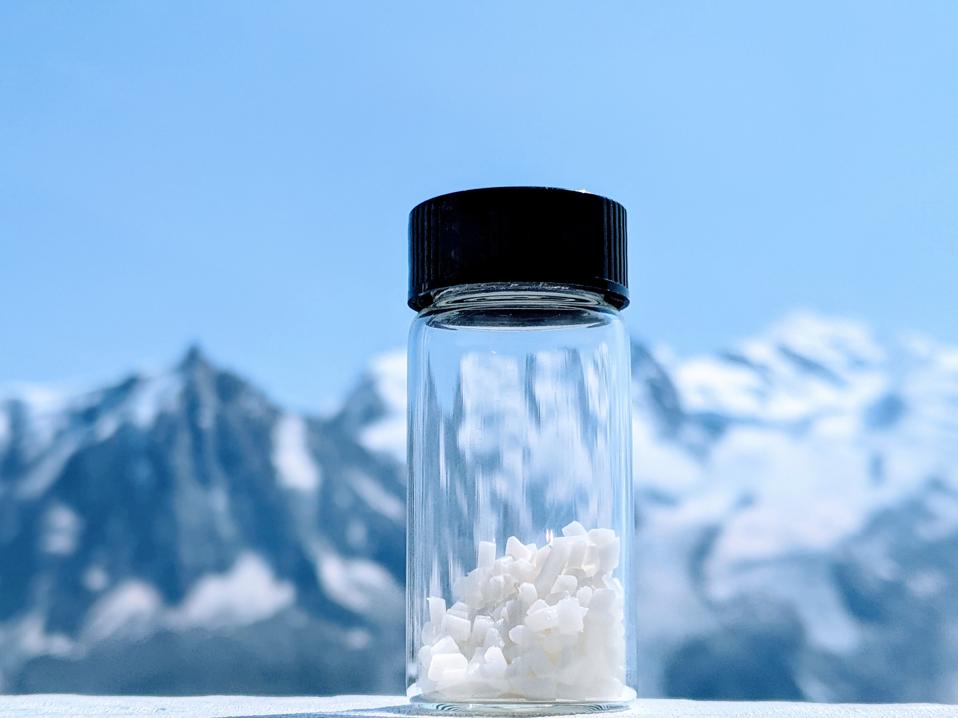
Synthetic materials, including polyester and polyamide (nylon), should be considered the ‘sharp end’ of the textile industry’s urgent need for next-gen materials. Synthetics account for around 62% of the global fiber market: that’s 80 million metric tonnes (MT) in 2020, projected to reach around 100 million by 2030. It is by far the fastest-growing fiber category, and that is a serious concern in environmental, social, and, if you’re a fashion brand, economic terms (which I’ll come to in a minute).
Synthetic fibers are mostly made from finite fossil fuels, whose environmental damage begins during the extraction process and continues for hundreds or thousands of years. For polyester, crude oil is chemically processed into polyethylene terephthalate (PET) pellets, which can be formed into plastic bottles or extruded into yarns for textiles.
Polyester textiles have an estimated footprint of around 30kg of CO2e per kilogram over their lifetime; with some 27.2kg of this attributable to fiber and fabric production. While these numbers might seem ‘immaterial’ to us directly, they reveal a fundamental truth: that circularity isn't a viable route to ‘sustainable synthetics’ and recycled PET (rPET) is not the answer. Why? Because the processing of polyester into yarns and textiles devours most of the energy–not the raw material phase that recycling replaces. I never thought I’d say this, but recycling, in this context, is unsustainable.
Polyester’s dark ‘triple-threat’ from extraction, production, and microfiber shedding during use and at end-of-life is reflected in the expanding regulations on plastic use, recycling and disposal. Synthetic materials are, indeed, at the sharp end of the urgent search for next-gen solutions, and not addressing them will also be a financial burden as regulation increases and crude oil prices rise with the transition to renewable energy sources.
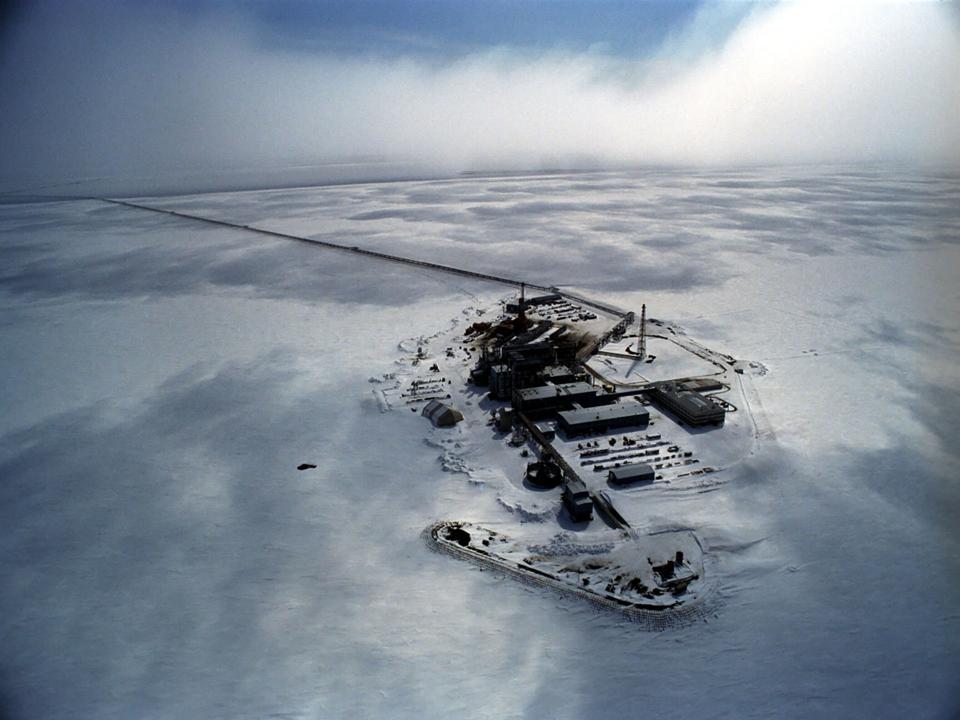
If not fossil fuel, what?
But what are the viable alternatives to fossil fuel raw materials? And can fibers and fabrics made from renewable and non-polluting sources perform like the polyester and polyamide we’ve grown dependent on? If so, how?
Fortunately, a cluster of material innovators are probing these questions, and a range of hope-filled answers exist. The first answer is in nature’s most abundant polymer: cellulose. It’s practically everywhere: coffee grounds? (12-30% cellulose); banana skins? (50-60% cellulose); cigarette butts? (95% cellulose acetate). But right now, most cellulose ‘waste’ is burned. “There is 50 times more cellulose waste burned every year than there is polyester produced,” Carlo Centonze told me during a video interview. He’s the co-founder and CEO of Heiq, a company turning cellulose into a direct replacement for polyester and nylon.
Heiq’s Cellulose ‘synthetics’
Heiq, founded in Switzerland in 2005, is an ‘IP creator for novel materials’ founded by Centonze and chemical engineer Dr. Murray Height. Recently, they launched Heiq Aeoniq - a cellulose yarn rivaling polyester and polyamide (nylon), with a chunk of investment from Hugo Boss to advance their pilot production, plus exclusive distribution of the yarn through The Lycra Company, which sounds like a valuable endorsement. But how does this supercharged cellulose work like polyester?
The factors in Heiq Aeoniq’s low impact and high performance are threefold, say Centonze says: atypical feedstocks, a newly designed spinning process, and the use of bacterial cellulose. During our interview, he revealed that Renewcell recycled textile pulp (a cellulose pulp) is one of their feedstocks, too, but the Aeoniq spinning and use of bacterial cellulose (also called nanocellulose) significantly diverges from the regenerated cellulose methods covered in my previous article. Where the next-gen solutions of Spinnova and IFC develop cellulose into cotton-like fibers,
New spinning and continuous fibers
Instead, Heiq is using PH-neutral chemistry that is far gentler than the solvents traditionally used for fiber spinning that homogenize the cellulose according to molecular weight. The next critical difference is that the spinning process creates a continuous filament yarn–a kind of cellulose 'spaghetti'. Centonze describes this process as “an art, rather than a science”. This is a vital differentiation from cellulose fiber production because usually it is cut into short lengths and twisted into yarns. But such cutting and twisting result in a yarn with structural weaknesses that reduce performance. According to Heiq’s CEO, their continuous filament cellulose has the elongation and tenacity to match polyester and none of the weaknesses of traditionally spun cellulosic yarns.
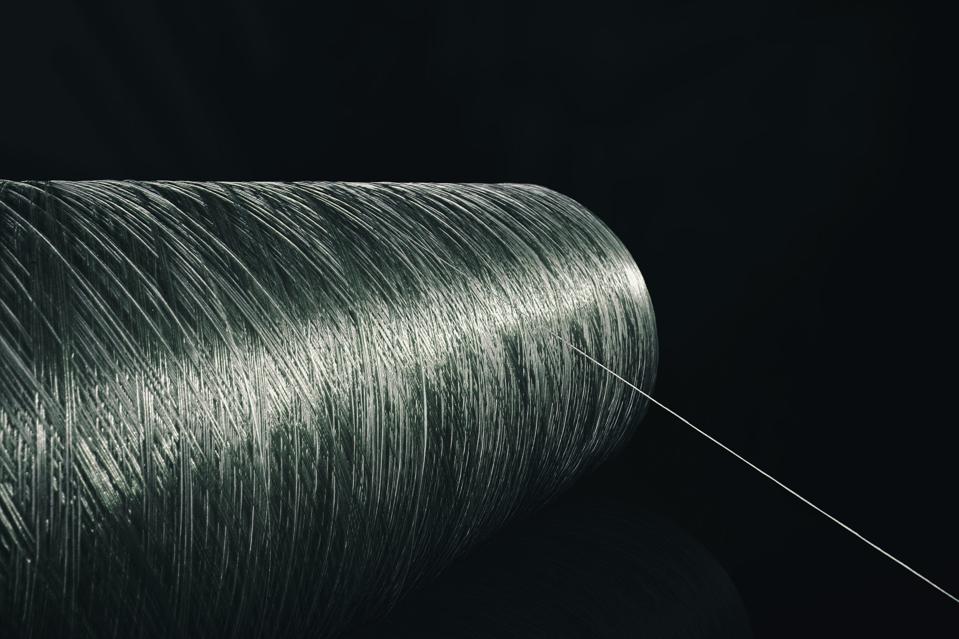
Cigarettes butts to performance textiles
On the renewable feedstock side of things, Aeoniq’s feedstock comes mostly from waste: algae, sugar cane, straw, hemp, nutshells, cigarette butts, and coffee grounds. Their secondary feedstock is recycled textile pulp (including from Renewcell) and thirdly, they use “bacterial cellulose made in our fermentation reactors”, says Centonze. The third input is the standout (although cigarette butts were a welcome surprise, too) because it marks a ‘new era’ of cellulose creation for this industry that takes us back 3.5 billion years. Bacteria are one of the oldest lifeforms on earth and some species have been making cellulose as a part of their natural metabolic functions for that long–biochemically and perfectly in a refined nanostructure–and this seems to be the perfect antidote to the synthetic mess we’re in right now.
Heiq Aeoniq LLC just received a $5M investment from Hugo Boss to scale their pilot commercialization facility scheduled for Q2 2022. Its first commercial Giga factory in Central Europe will be ready in 2024, at which point 30,000 metric tonnes per year (around 0.04% of current market share) will be achieved, requiring a total of around $200M investment. This adds color to the financial clout needed to scale sufficiently to nibble at the synthetics’ stronghold, let alone bite a chunk out of it.
“We need 2500 Aeoniq plants to replace the polyester [currently in production], or 3000 to account for growing demand” Centonze added. The technology “needs to be adopted worldwide” and will be opened up through licensing agreements.
Who are the other companies working on incumbent synthetics and nearing commercialization? Next, Natural Fiber Welding, whose cotton yarns are also made of cellulose, but ‘welded’ to extend its performance profile.
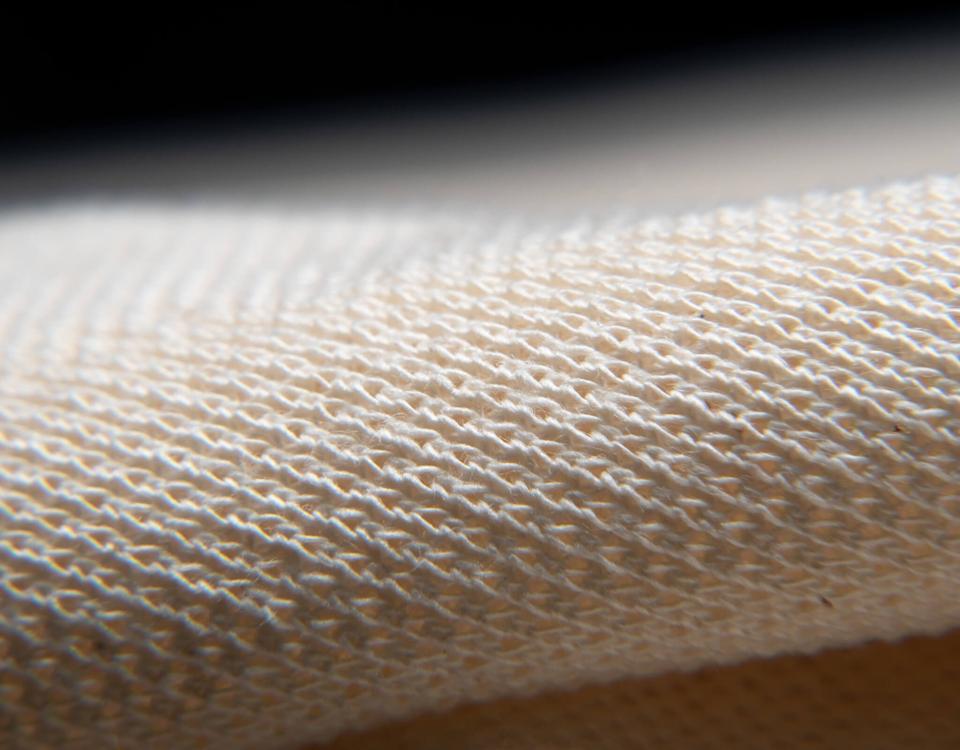
Natural Fiber Welding
Also pursuing the ‘performance cellulose’ route is Natural Fiber Welding (NFW). They have developed CLARUS®: a proprietary technology platform with 11 patent families. The tech toolkit spans chemical engineering and automation solutions, designed to re-engineer and ‘fine tune’ natural fibers to perform like synthetic ones.
As mentioned above, ‘natural’ fibers including cotton lint and shorn wool are in short lengths that are twisted together to make long yarns (as opposed to smooth, continuous filament yarns) for knitting and weaving Going deeper into the pitfalls with twisted yarns from natural fibers, CEO of NFW, Luke Haverhaps explained “The twisting of the fibers creates empty space [and] by controlling this space it is [possible to] create durable, low pilling and low breakage yarn”; And this is what CLARUS® technology does.
This is how it works: The ‘twisted’ yarns are placed in an ionic solution that partially dissolves the outer layer, which is then “welded” back together to create a smoother yarn surface with geometry more similar to continuous filament yarn. After welding, “the yarn geometry is such that moisture can be shuttled across the fabric, so you have more cooling and evaporation” Haverhals explains, resulting in technical yarns made from cellulose and protein-based fibers, not plastic.
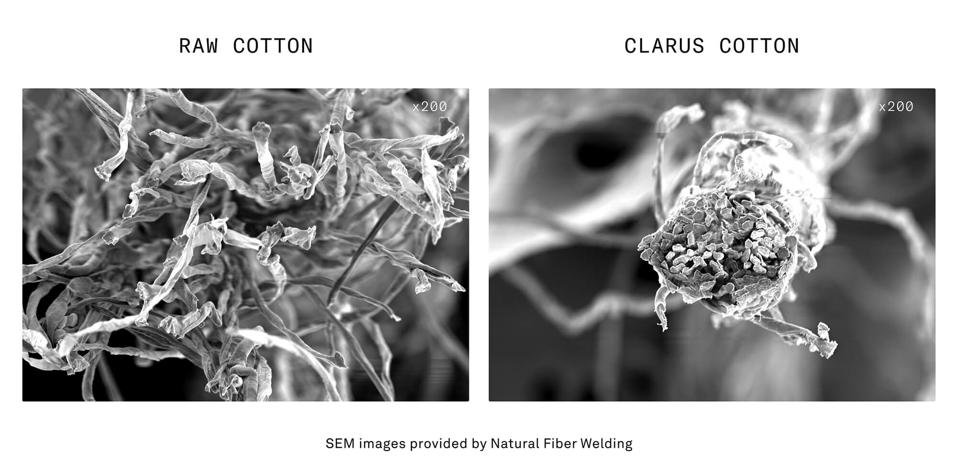
But is CLARUS® creating an alternative to polyester and polyamide, or simply upgraded cotton (amongst other natural fibers)? It’s both, explained the CEO, who shared the startling tally of brands approaching NFW asking for materials solutions: “more than 700” at the latest count.
Some brands, like Ralph Lauren, want ‘natural technical’ products, for such products as their RLX CLARUS® polo shirt (made of 50% virgin and 50% recycled cotton). Others want to replace synthetic materials with natural ones that can perform much more robustly, like Chaco’s use of CLARUS® in a tough, durable shoe upper. On another shoe note, Allbirds invested in NFW last year after making a public commitment to drastically reduce the carbon footprint of their products.
Impact reduction
How does their innovation reduce textile impacts, I asked Haverhals? In a few ways, he explains, but primarily, but utilizing fibers that are considered ‘waste’ because of their short staple length. Large quantities of cotton lint, mechanically recycled cotton and wool are currently excluded from spinning, but Natural Fiber Welding’s technology makes those fibers viable by ‘welding’ them into performance yarns with added value.
Apart from utilizing ‘waste’, the welding process uses non-toxic and minimal chemical and water inputs, along with integrated dyeing (including their patented closed-loop recycled indigo process). The cumulative impact reduction is not easily quantifiable at current quantities and with the variable use-cases, so indicative numbers will have to follow as the solutions achieve scale.
On that front, mills will be able to license the CLARUS® technology to enable them to ‘weld’ the yarns on-site in their facilities, and disrupt the synthetic textile market, says Haverhals. “We think of ourselves as a disruptor to plastic, but you can’t disrupt plastic by planting cotton–you have to use cotton that’s already been grown.”
In terms of capacity, NFW is processing around 50 metric tonnes of yarn per year, but they recently took investment from a leading textile mill and are implementing CLARUS® technology with them. Their target output of 10-20 metric tonnes per day would equate to as much as 7300 metric tonnes per year, (or 0.009% of today’s synthetic fiber market).
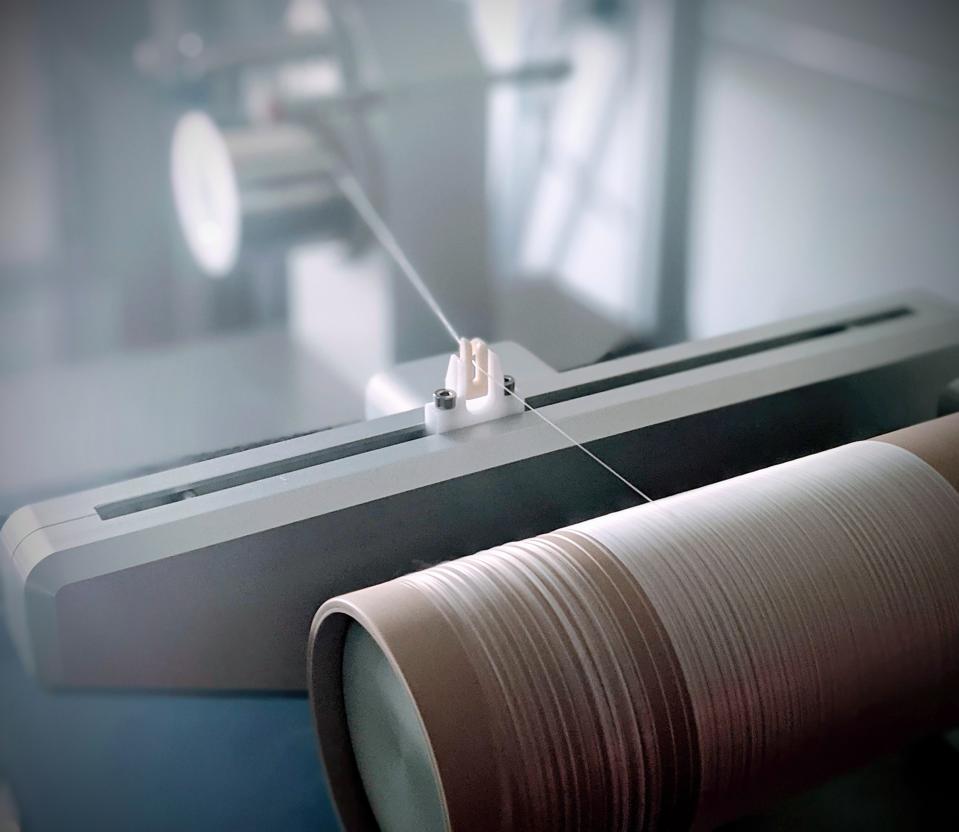
Kintra
Like Aeoniq, New York-based startup Kintra is extruding a continuous filament yarn, but from a polyester resin called Polybutylene succinate (PBS). PBS (which biodegrades into water and CO2 with the help of microorganisms) is not a new polyester, but Kintra’s IP-protected formulation is. By adding additional bio-based materials to the traditional monomer feedstock for PBS they are enhancing (and refining) the performance characteristics and biodegradability of the extruded yarn. And they’re avoiding fossil feedstocks in the process.
At their lab space in Brooklyn, they receive already processed monomer feedstock (originating from corn) and chemically engineer this into their unique PBS formulation. I reported on Kintra’s first steps 15 months ago, when they had just one spool of yarn. During my conversation with co-founder and COO Alissa Baier-Lentz, she updates me on the fabrics now being produced in partnership with a mill, seeing them approach pilot quantities.
How does Kintra differ in proposition to its cellulose-engineering counterparts? Crucially, it fits into existing industry infrastructure, because what they are creating is a new resin for extrusion into yarns in the same facilities that already make polyester and nylon. This is the proverbial plug-and-play situation, in which they can scale quickly and competitively with recycled polyester on cost.
The challenges Kintra face now are not market disruption like Aeoniq and Clarus, but rather ensuring that their PBS nanocomposite can be spun at the same rate as PET, and optimizing the formula to reduce dyeing temperatures and thereby energy usage. In addition, can they facilitate radically improved chemistry for dyeing this new polyester, to further reduce impact and add value?
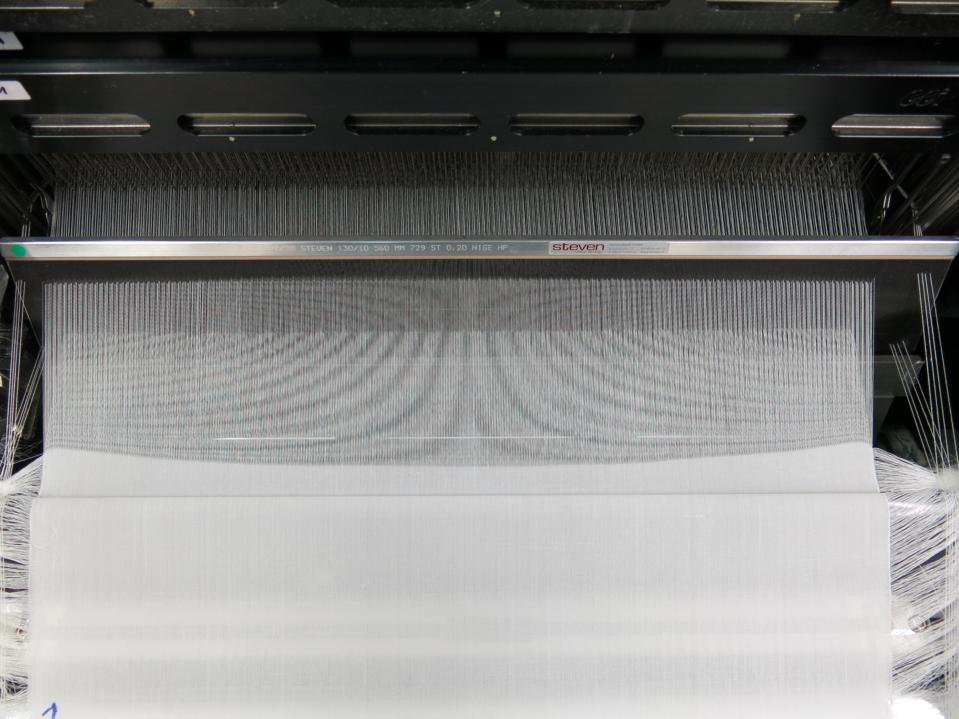
Right now, their R&D lab in Brooklyn is producing “a kg at a time” says Baier-Lentz, but Kintra’s pilot with their mill partner scaled to 100kg in 2020. The startup will “pursue a hybrid business model of resin sales and licensing the formula” she added. Their targets are ambitious: replacing rPET is their first goal, and they expect commercial availability of Kintra by 2024.
A huge opportunity
It would seem false to refer to the three innovators in this article as competitors when their combined displacement of the synthetic fiber market over the next few years amounts to a single-digit percentage (notwithstanding the potential to rapidly scale from there, given the right financial and market conditions). And there are many more innovators working in this space, however, this very top-level crunching of numbers demonstrates the still enormous scope for cost-effective and environmentally sound innovations to replace synthetic fibers. This remains as big an opportunity as it is a challenge.
Stay tuned for the next instalments in my next-gen materials series, when I dig into the potential of synthetic biology, next-gen animal fibre replacements and more.