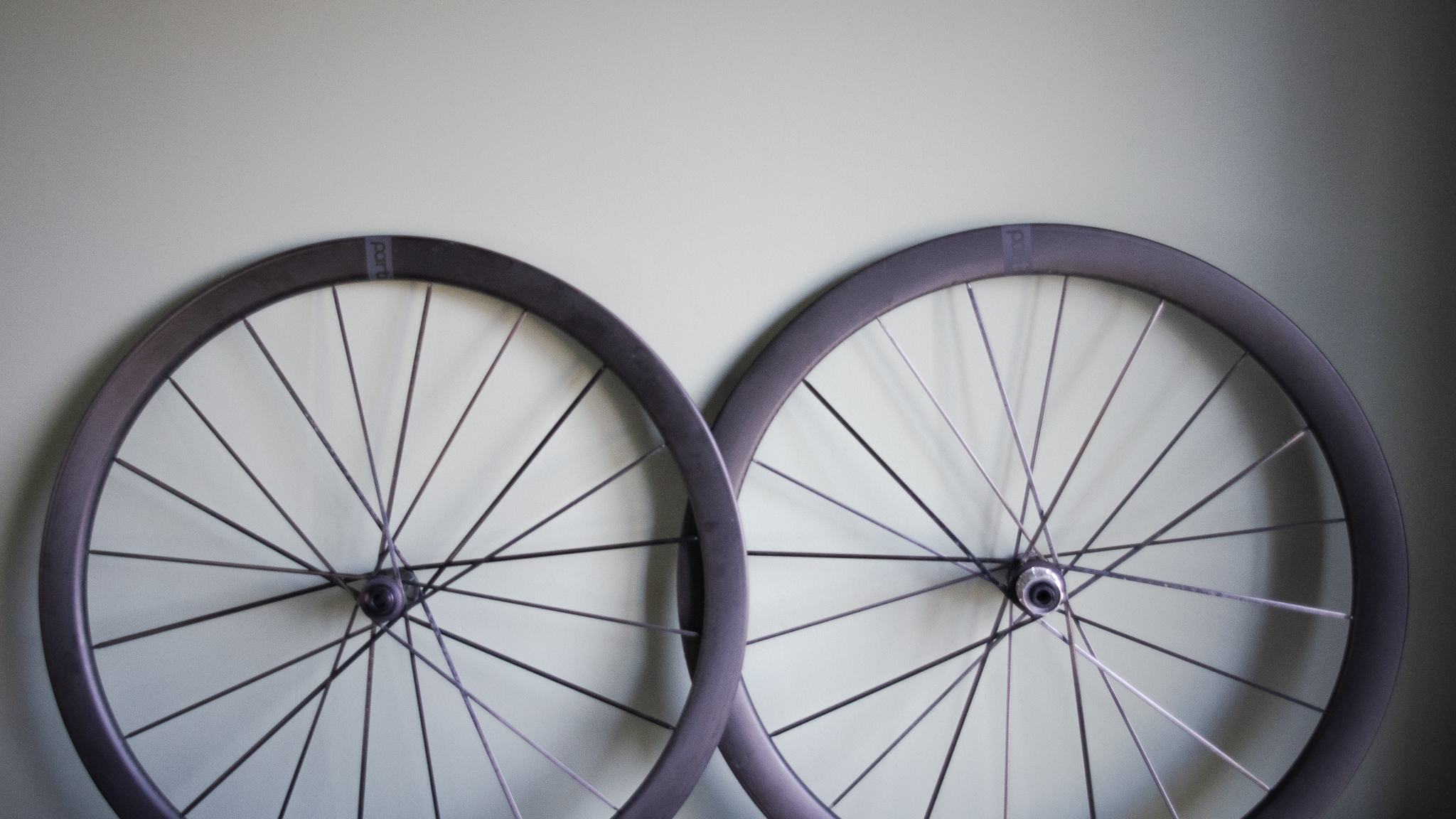
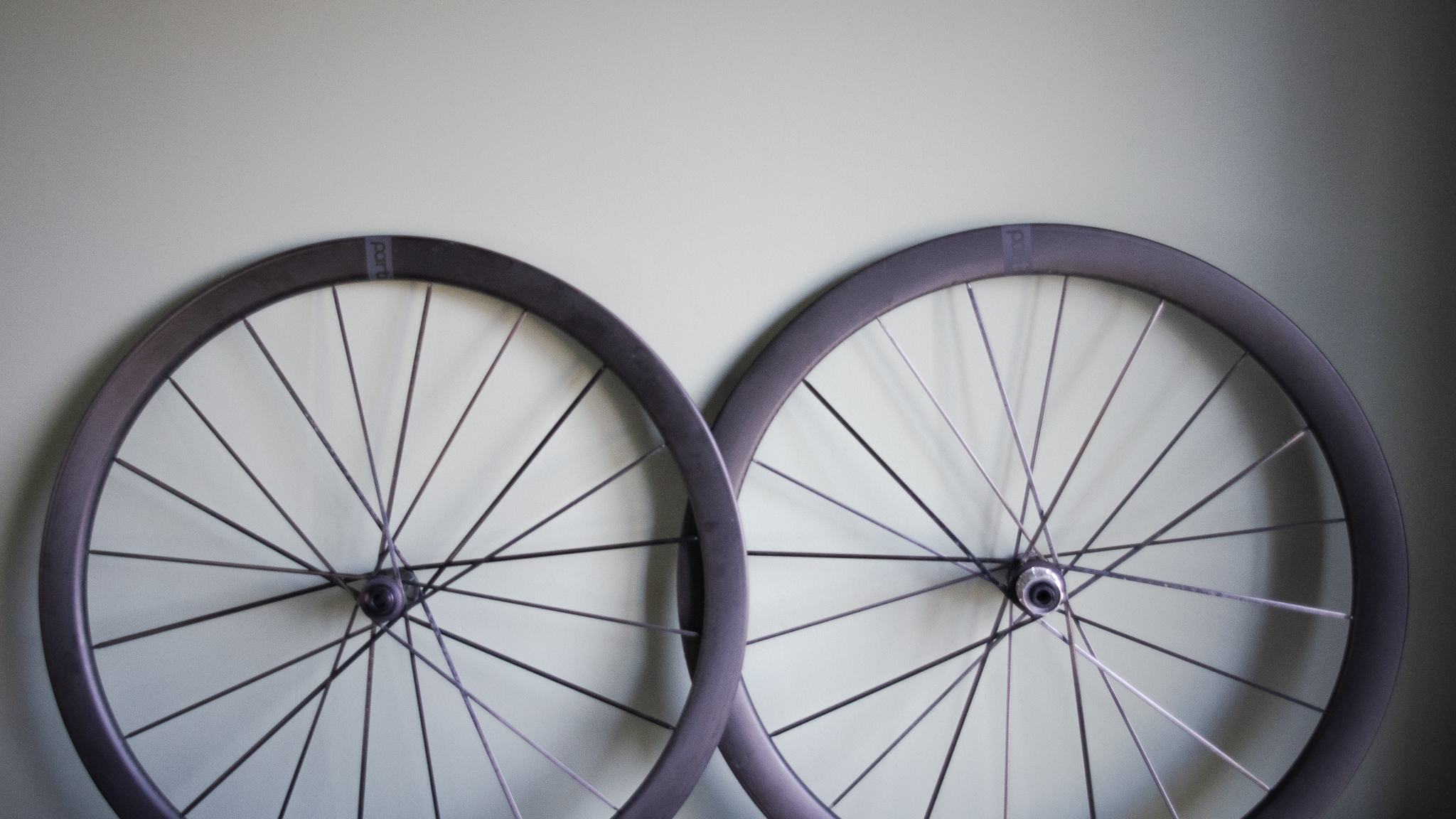
Price: £5,499.00
Weight: F: 538g / R: 635g Pair: 1173g as tested.
Rim Dimensions: F:39mm R:44mm
Rim Widths: Int. 21mm Ext: 26.5mm
Spoke Count: F: 20 / R: 20
Rim Type: Hooked
Tubeless / Tubes: Both
More Information: partington.cc
The Partington R-Series MKII R39/44 wheelset is one of the lightest and most expensive disc clincher wheelsets in the world. Manufactured in Victoria, Australia the wheels are the brainchild of company founder and engineer Jon Partington, who moved to Oz around 13 years ago but hails from the UK and has a background in the motorsport and automotive industries.
The R series MK II R39/44 wheels, or just 'Partingtons' as I have taken to calling them for want of a snappier description, sit at the very sharp end of the cycling wheelset pyramid alongside the likes of Lightweight, Syncros, and Princeton Carbonworks. They feature carbon fibre rims, bonded carbon spokes and carbon fibre hub shells, with all of the bearings coming from brand technical partner CeramicSpeed. Cadel Evans is also a brand ambassador and has provided feedback on the wheels.
The wheelset features a hooked rim, can be used with tubes or tubeless, and weighs a claimed 1160 grams. I don't think there are many hooked, off-the-peg disc clincher wheelsets that come close to that weight at the moment.
To quote Partington on the product and its philosophy, they are "aimed to be the best-performing products on the market, for people who want the most desirable high-performing cycling componentry."
I've been able to test the wheels over several months and with two different bikes during this summer and autumn to see how they performed and if the performance justified the very high price tag.
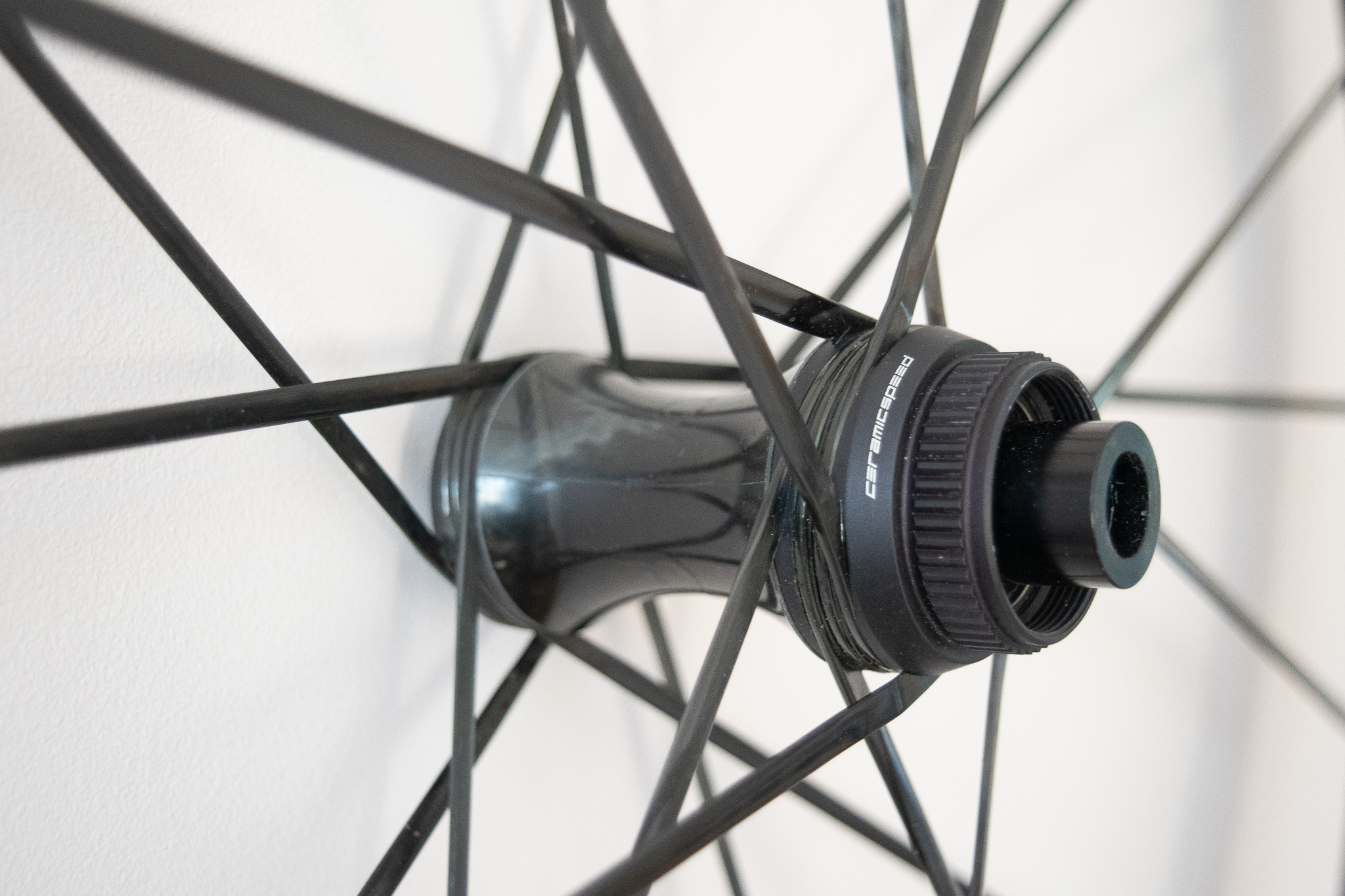
Design and Aesthetics
Aesthetics-wise, the R series wheels have a subtle, un-fussy finish and look. The rims themselves have an understated matte finish, with a single, simple grey band with a black 'Partington' logo on the rim opposite the valve hole, and that's it. No huge logos, or inspirational quotes here.
From a distance of a few metres, you could be forgiven for not particularly noticing them at first glance when fitted to a bike. The rims look similar in finish to a myriad of other matte carbon rims. It's probably the wider, glossy carbon spokes however that initially give the game away and lend a more aggressive look to the wheels. Move in closer and your eyes are drawn to the glossy spokes and gleaming carbon fibre hub shells that again carry a single, subtle Partington logo. Next, you notice the single 'Ceramicspeed' logo on the non-drive side of each hub shell and the unique arrangement of the spokes at the hub flanges.
I like the subtle styling choices. It feels like the brand and wheels themselves are saying 'We don't need to shout'. These are very expensive wheels that sit at the top end of the market, they look purposeful and fast when installed in a bike but it's only upon second glance or when you move in for a closer look that you start to notice there's a little bit more going on.
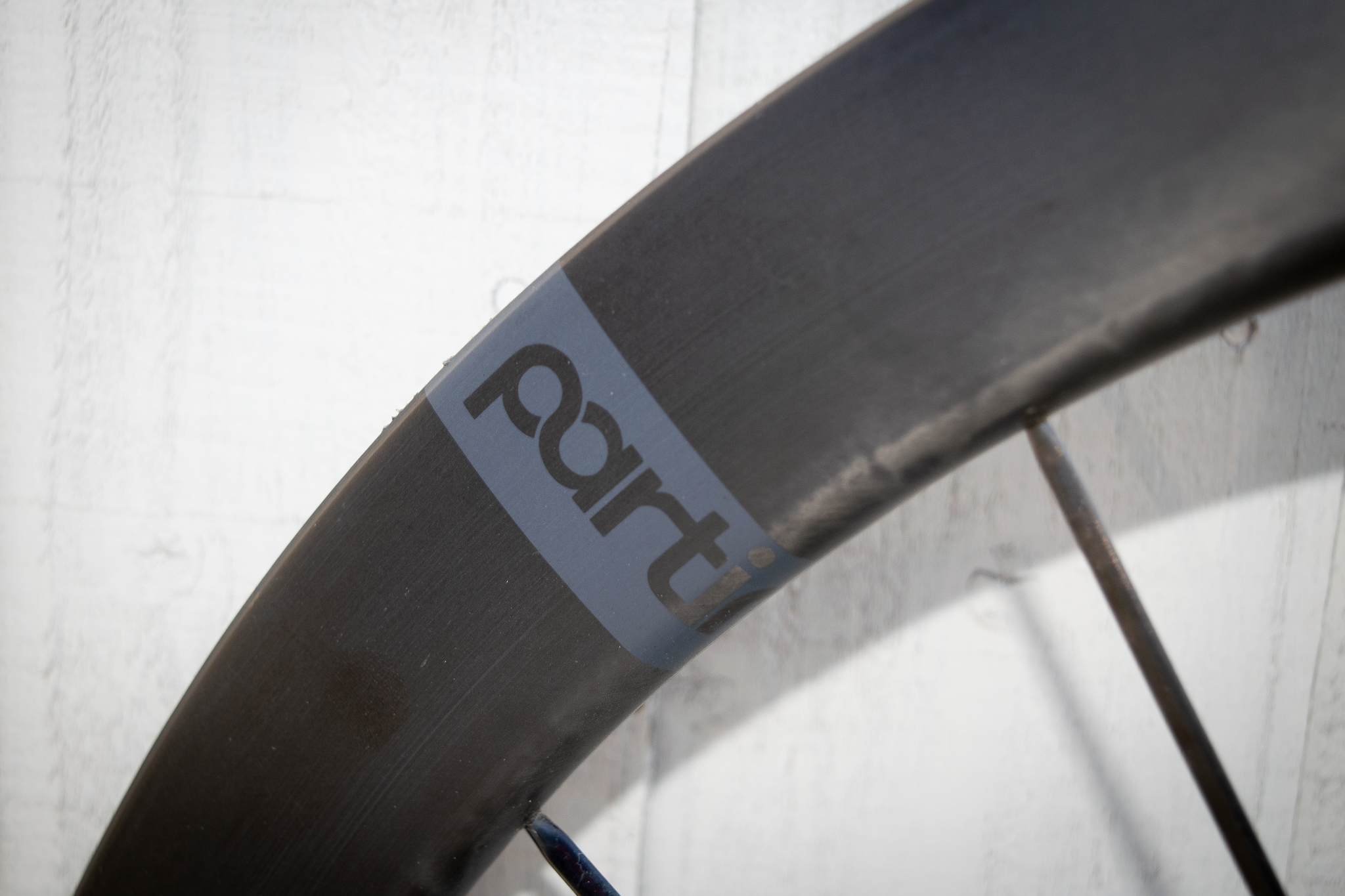
The R series MKII wheels feature specific rim depths and profiles. The front wheel is 39mm deep and the rear 44mm, the rims also feature an aerospace foam core, said to aid stiffness - it certainly doesn't add much extra weight.
Partington makes no specific aero claims about the wheels, and there are no 'X watts faster at...' claims to read or share. The wheels do have front and rear-specific rim profiles though. The front rim is more rounded than the rear, which is deeper and has a broad 'V' shape. The rim depth has been selected for its versatility and the shape was largely focused on handling characteristics.
The carbon fibre hubs themselves are designed and manufactured by Partington in partnership with CeramicSpeed which supplies bearings to Partington's spec for the wheels. The MK I version of the wheels used an aluminium hub shell and DT Swiss internals but Partington has overhauled and re-designed its own hubs for the MKII.
Spokes are bonded from hub to rim in pairs, and you can see some of the resin at the point where the spokes meet the rim. Partington wouldn't divulge all the information regarding the manufacturing process here, specifically on the tensioning procedure when I asked. The rim and spokes are produced and bonded together under tension on a fixture, or jig if you like. Partington claims the highest lateral stiffness for the wheels in their class which is 55 N/mm (Newton millimetres). What does this mean? If I understood correctly, hang a 5kg weight of the rim and it will move by 2mm, to give you an idea. All UCI and ISO standards have apparently been exceeded for the wheels in testing and they have met 2x the UCI impact testing standard without failures.
You could cite the fact you can't true the wheels as a negative, but they shouldn't in theory ever come out of true, thus negating the issue. Crash or accidental damage is another thing, which would involve a more involved repair or wheel replacement (there is a crash replacement scheme and a 2-year warranty) but the wheels should never need truing. The wheels will never be as true as a conventional wheel, with no chance to make fine adjustments in the same way you normally would. There's 3/4mm of runout. This is negligible and once a tyre was on if I really looked I could detect a slight bit of runout.
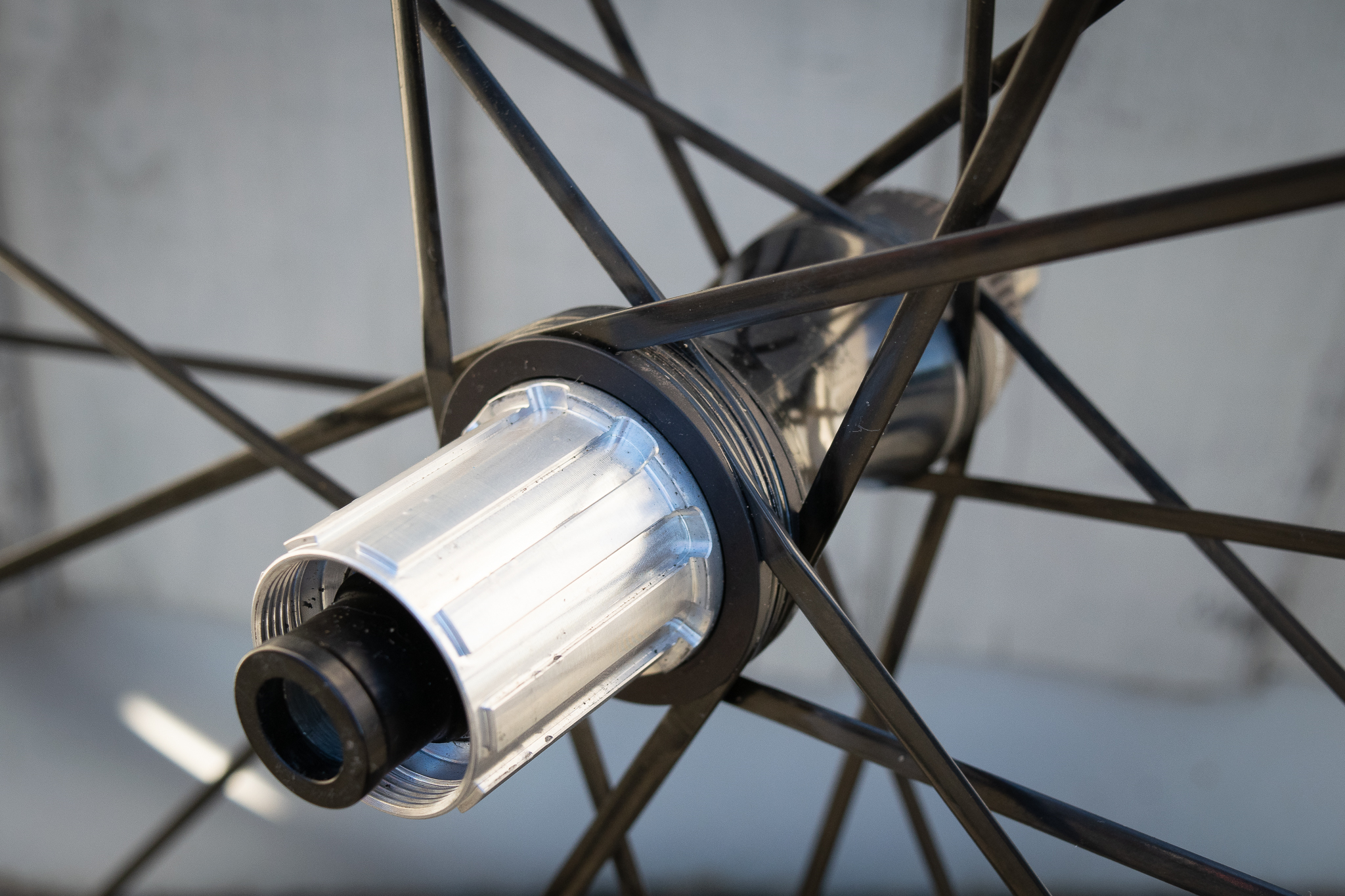
I encountered something completely new when installing the wheels and living with them. There is about 2/3mm of play in each wheel when installed in a frame. I thought it was perhaps an assembly issue at first. I've always aimed to eliminate play in a wheel when working on my bikes or customers and have always seen it as a negative.
The MK II wheels are designed to have this play in the hubs. It's a product of an intentional piece of the design the brand calls 'dynamic bearing architecture'; I was even sent a white paper on it. Jon from Partington summed things up for me: "We don't over constrain the bearing arrangement, is the best way of phrasing it." The hub design deliberately ensures the bearings are not adversely loaded. Partington says if there's no detectable free play at the rim, you've gone too far.
I've struggled to simplify this section of the review, it's the most interesting to me but I'll try my best. Ever tried to achieve the least amount of bearing pre-load in your hubs while achieving no side-to-side play so they spin most freely? Or remember leaving a sliver of play in your cup and cone bearings until you did the quick-release axle up? This design takes that to the next level.
Due to a combination of high-quality bearings with very close internal clearances, exacting manufacturing tolerances and a hub design to avoid adversely pre-loading the bearing races, Partington has achieved exceptionally smooth, resistance-free hubs that should provide a very long life for the wheel bearings. As a simple example, you can pull the front axle out of the front hub effortlessly, it's obvious not much is loading or affecting the bearings. I've worked on low-end hubs where it's been difficult to even press the cartridge bearings in straight due to poor tolerances.
To provide a quick take-home here from all of this, the hubs are incredibly smooth. The front in particular with its more simple design than the rear spins forever, probably the smoothest running front hub I've ever felt, it's just effortless. Though an unloaded spin test isn't the be-all and end-all it's still something we all do to check our wheels and was mightily impressive on the R Series front wheel.
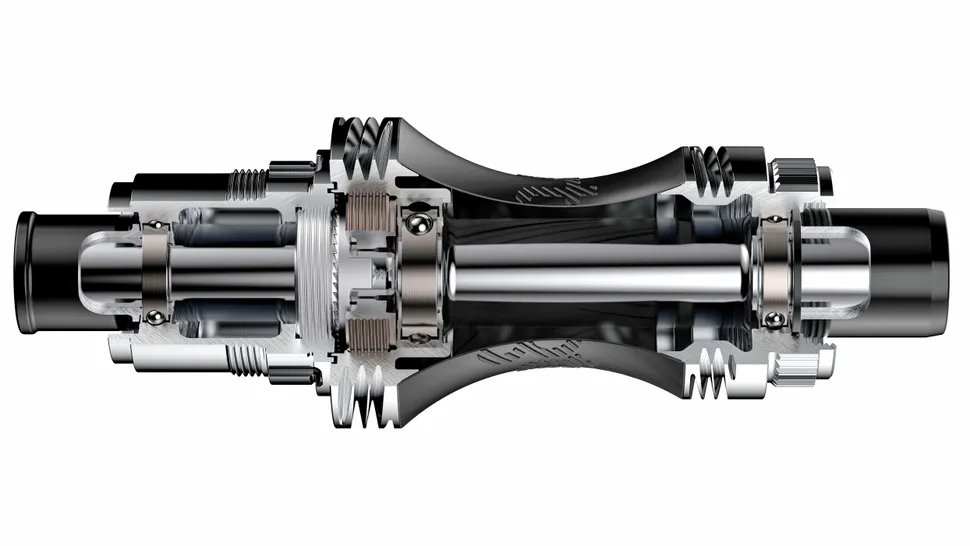
CeramicSpeed has been involved in the development of bearings for the wheels, providing advice on appropriate bearings seals, amount of grease fill in each bearing etc. The bearings all use non-contact seals which reduce drag except the larger drive-side rear hub bearing which has contact seals. The rest of the bearings should be serviceable in situ by removing the seals, cleaning and regreasing etc. The larger bearing needs a specific tool to access but the brand says all bearings should have a long lifespan due to in a nutshell manufacturing tolerances and bearing quality.
The last thing to touch on is the freehub body and drive system. The engagement system uses a spring-loaded ratchet design that needs to be lightly oiled, not greased. This reduces drag, provides faster engagement, distributes around moving parts more easily and aids reapplication according to Partington. Six small springs help the ratchets engage; they are very small but stay in place which makes maintenance easy. The freehub body can be removed, swapped and cleaned in minutes. The freehub body noise isn't super loud either, which is just fine by me.
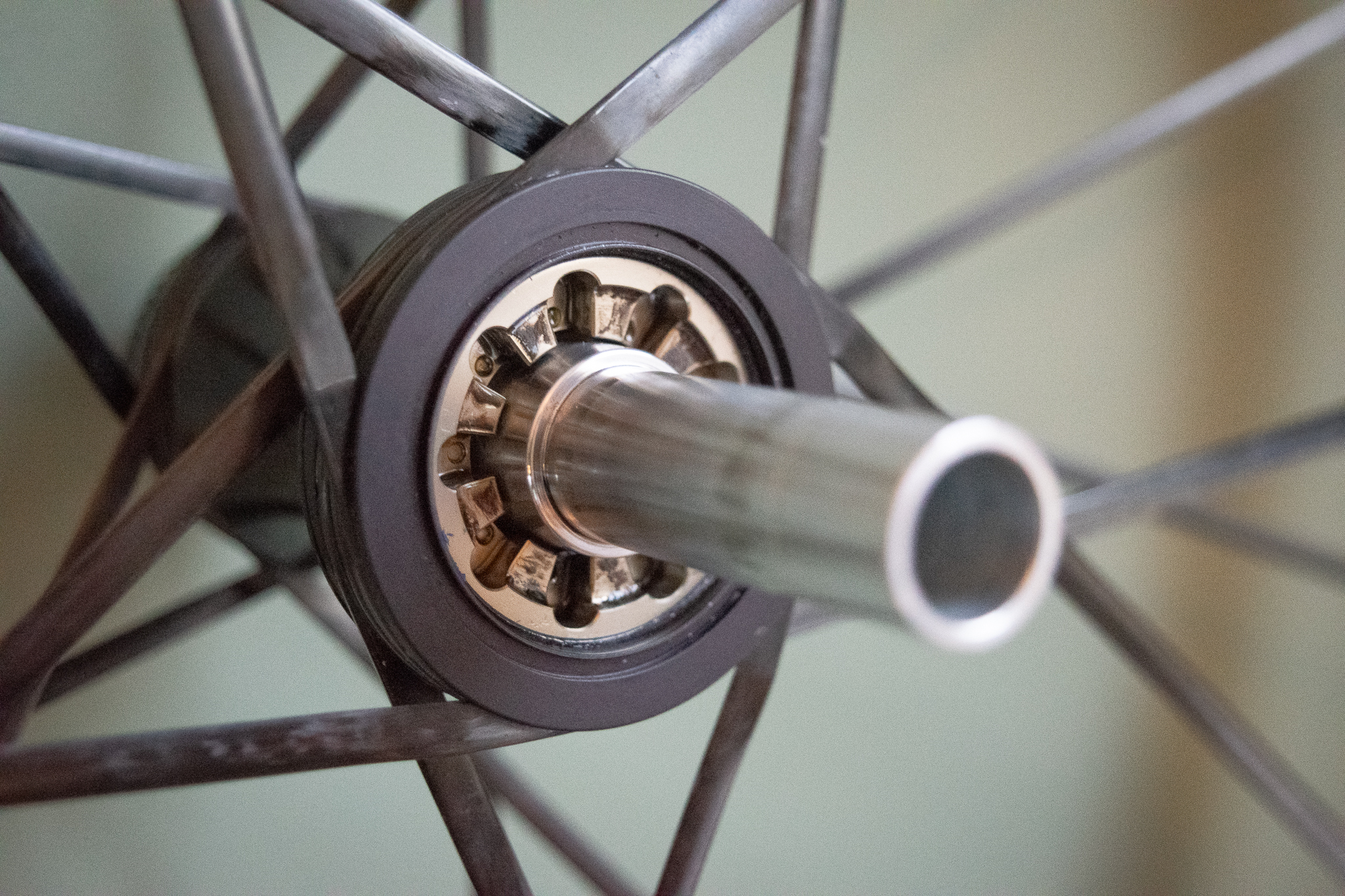
Performance
The R Series MK II is for the moment the only wheelset I've ridden with completely bonded carbon fibre spokes and an all-in-one carbon design. They are also the lightest wheels I've ever used at 1173 grams per pair on my own scales.
The Partingtons are clearly by most metrics very high-end, performance-focused wheels. Given the stiffness claims, carbon-spoked construction, very low weight and CeramicSpeed bearing package, before actually riding them I felt my initial impressions would go one of two ways. That I'd either hop on the bike and be absolutely blown away by what I felt or it would be slower, working out of everything. It did turn out to be a slower working out of things, and I can't honestly say there was the earth-shattering moment during the first few rides that I half expected.
Slowly but surely though I began to get a feel for the wheels. Over the first few rides, I would just have moments here and there, riding a section of road, or accelerating over the top of a climb and I'd have a "hang on, I I felt something a bit special there" moment. Acceleration was noticeably improved, especially at slower speeds, on a climb for instance, when getting back on the power and it was this feeling of 'zip' which grabbed me at first.
Only after more riding and once I swapped back onto other bikes or wheels did I realise the Partingtons just make everything feel that little bit better. In my notes, I'd written that it almost feels like you are always on a good day when riding them. The stiffness is noticeable, particularly for me at low speeds out of the saddle. I did back-to-back tests and other high-end carbon wheels felt sluggish and slow when riding the same way, almost like riding with a slow puncture.
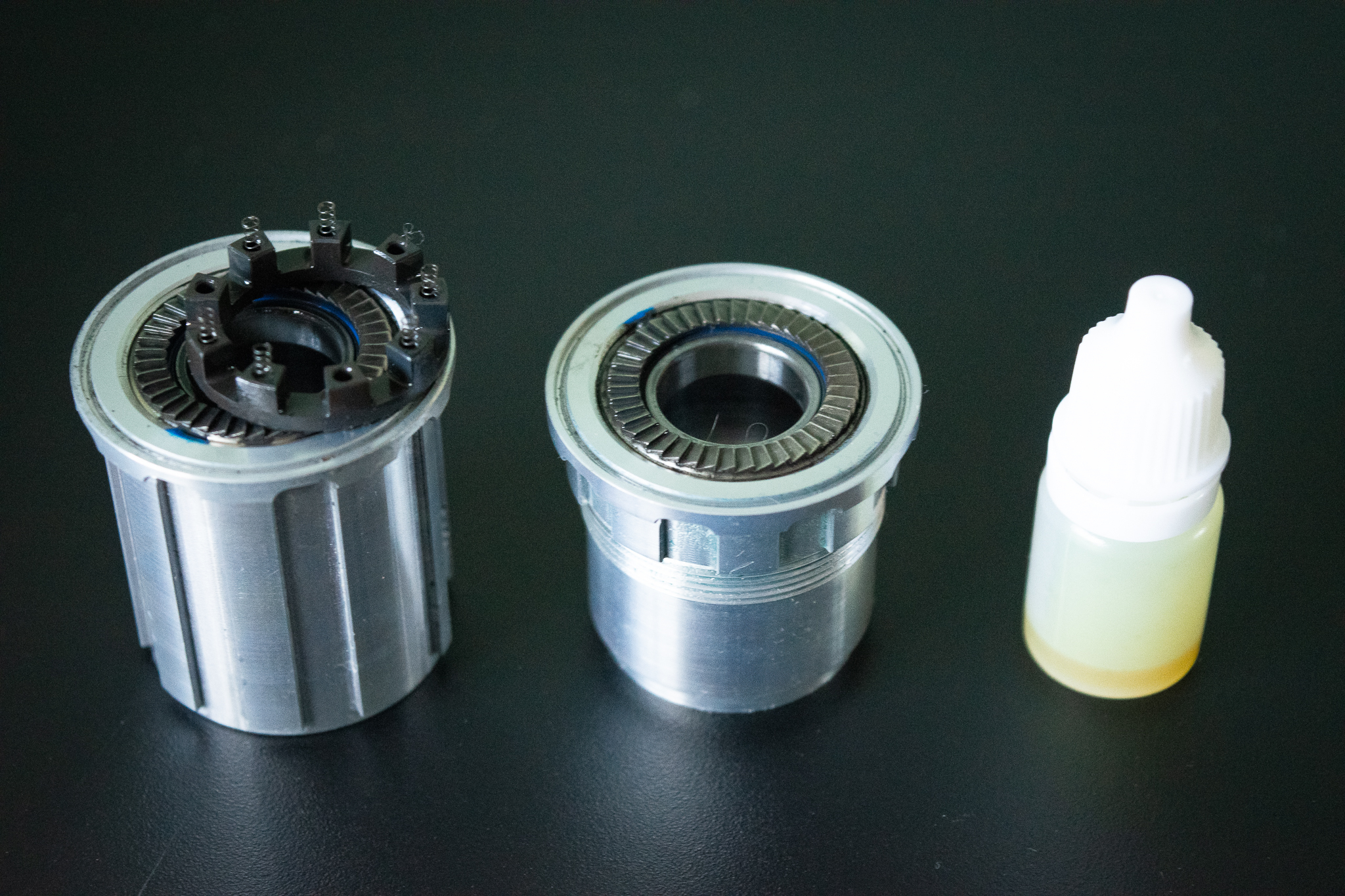
I've tested the wheels on two different bikes over the past several months - the Ridley Falcn RS and the Canyon Endura CFR - and have ridden others for more comparison. I used the wheels with two sets of different tyres during my time with them. A set of 32mm Vittoria Corsa Pros and 28mm Schwalbe Pro ONE TLE tyres. Partington has a useful tyre size and pressure guide included in their user manual which I used as a guide.
Overall it was probably the easiest tubeless setup experience I've had yet. I added Stans's sealant, inflated the tyres with a track pump and that was it. I've set a lot of tubeless tyres up for customers in the past on a range of wheels and know what it's like when it's a pain, not so here. The Vittorias in particular were very easy and I installed them by hand without effort. I'd probably just run them with latex tubes were they my own but tested them tubelessly as I think that's probably what the majority of users want to hear about. I had zero flats and from what I could make out no sealant splatter over my months of use. The R series rims are hooked and compatible with inner tubes and tubeless tyres, and the rim bed is sealed, there's no need for spoke holes here it's just one smooth section of carbon fibre. This means you don't have to worry about the tubeless tape and getting your setup perfect, which is a huge plus point in my book.
During my chat with Partington, after remarking on the effortless tubeless install we touched upon a fascinating insight regarding rim diameters. Tyre pressure affects spoke tension and high spoke tension can affect rim diameter. On traditional wheels, this can lead to a slightly smaller wheel diameter, potentially leading to tubeless issues. Partington knows with complete confidence their wheels are 621.95mm in diameter + / - less than .1mm due to their all-carbon construction. My understanding here is that the only element in the equation that could affect tubeless setup regarding the MKII wheels are the tyres themselves, the rim is always going to be the same, which should ensure better tubeless performance due to consistent and unaffected rim diameter.
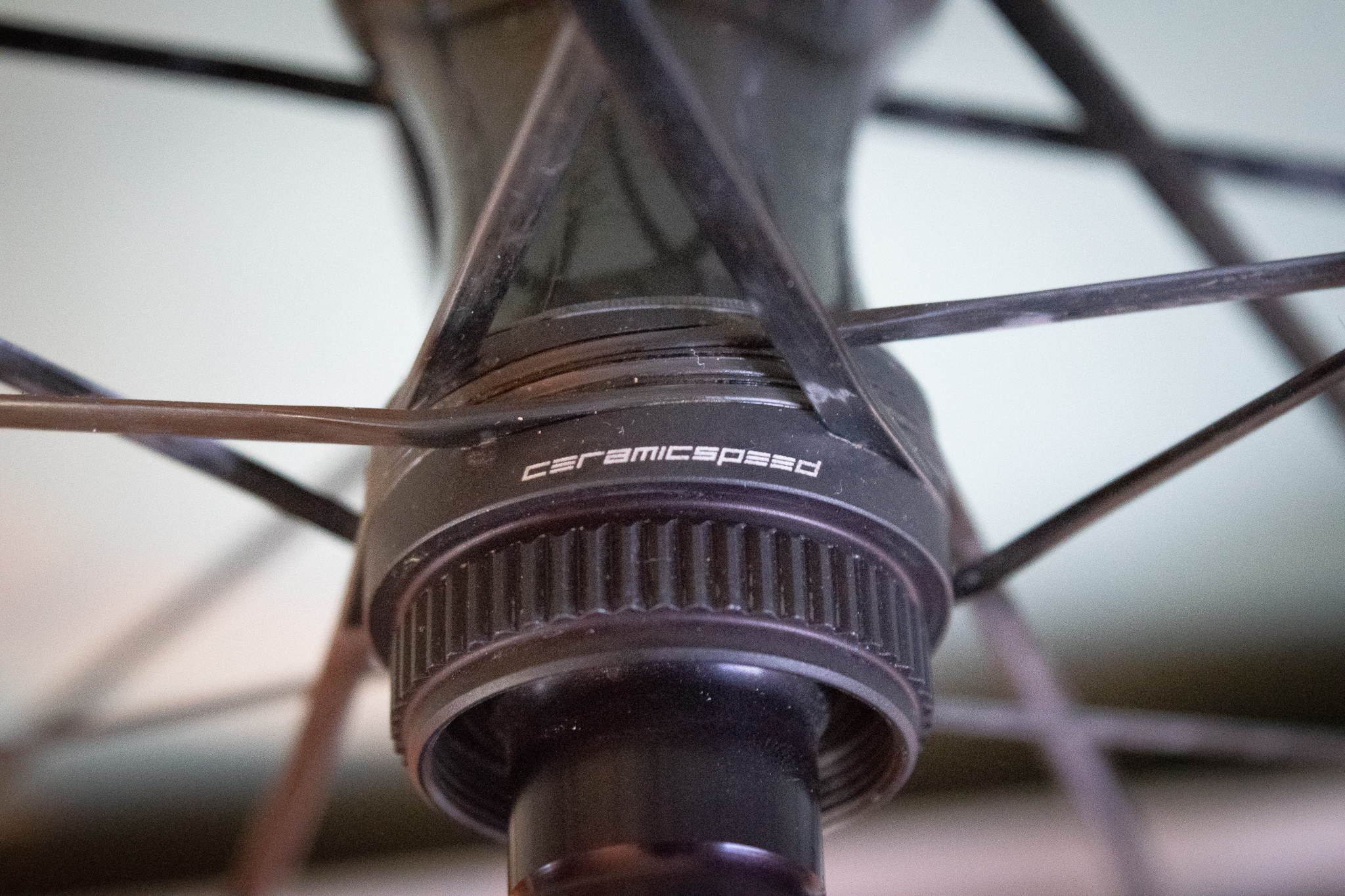
Value
There's no getting around the fact these are very expensive wheels that sit at the top end of the market. RRP is listed at £5,499 / $6,400 / €6,000 / AU$ 9,898.
Looking at other competitor wheelsets on the market puts the Partington's second only to some Lightweight wheel models in terms of price from what I can make out. They are around £1000 more expensive than the top-spec Princeton Carbonworks wheels with £1000 Tactic hubs, and over £1000 more than the wheelset that people may cite as a direct competitor, the Syncros Capital SL. The Reynolds RZR series wheels also came very close to this mark several years ago but I'm not sure they are still in production.
The wheels are designed and manufactured in-house by Partington in Victoria, AU. It's clear the brand wants complete control of its product and manufacturing processes. Even down to the resin used in the spoke bonding process which is their own. Partington cited just a few mould tools that aren't made in-house, that's not even wheel components but the actual tooling used to produce them, these are manufactured within a 100km radius. However, I assume the CeramicSpeed bearings are coming from Denmark.
There are premium, no-compromise products in every sector, not just the bike world. Not everyone will be able to afford these wheels, I know I can't. But if customers or teams with the cash want a top-end, custom-made wheelset that prioritises engineering and performance the Partington vision will fit the bill.
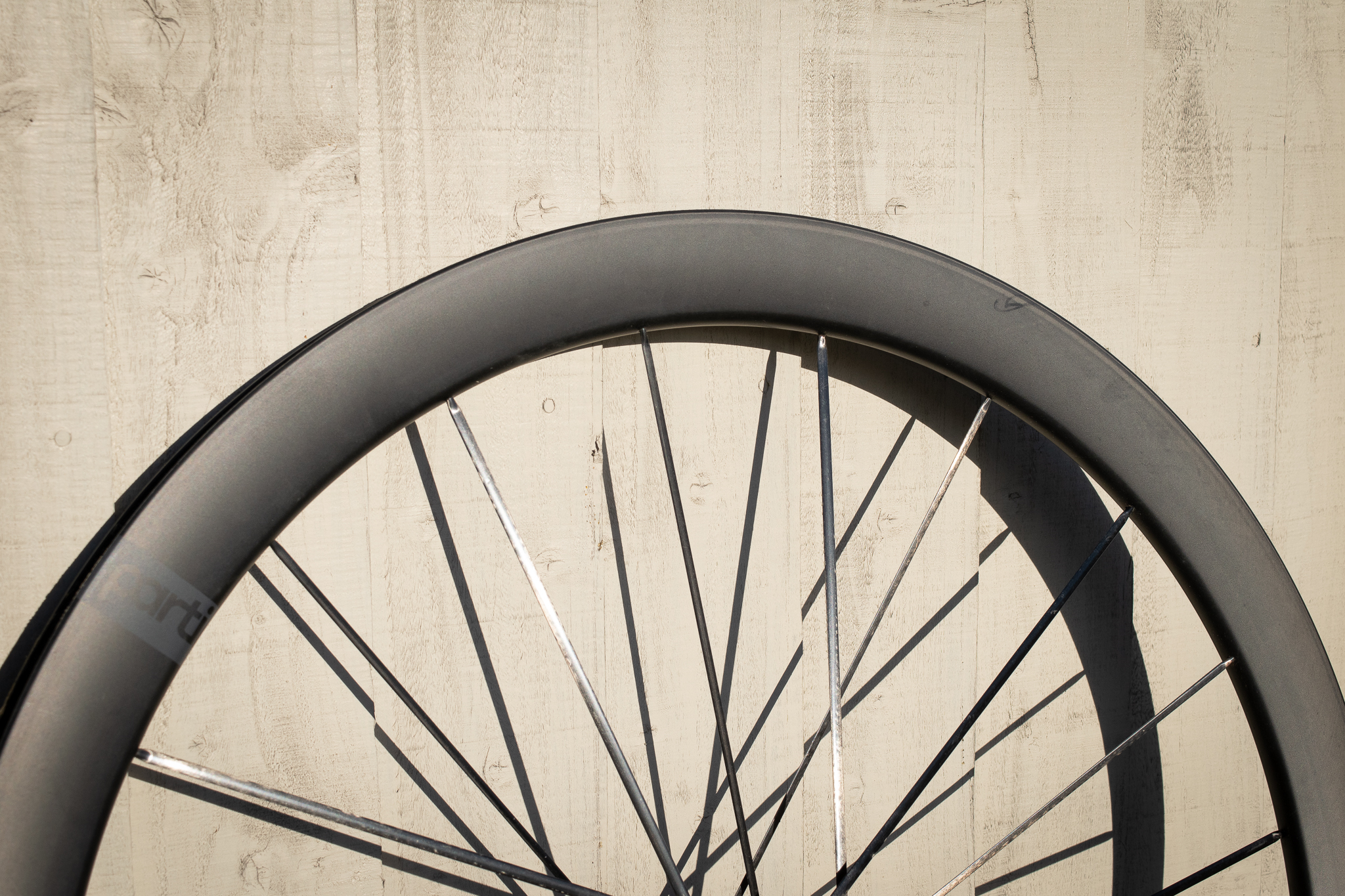
Verdict
The performance of the R Series MKII wheels has been excellent across the board. The wheels feel really fast over any terrain, and handling and descending were all also spot on. I can't say I felt any harshness from such a stiff wheelset, I relished what the extra stiffness brought to the table if anything. I feel tyre size and pressure contribute far more to this. It's not something that tends to trouble me but I didn't have any issues in crosswinds from the rim profiles etc.
I found myself not really wanting to use anything else whilst I've had them, and I felt I would be at a disadvantage if I did. I rode them on our Saturday morning chain gang which in summer features plenty of fast wheels and aero socks etc and they performed really well here on a circuit I ride hard regularly as well as in a couple of 100-lap road bike races at my local outdoor velodrome.
They are special wheels that provide elevated performance across the board. Perhaps this is why nothing smacked me in the face when riding immediately, everything just felt that little bit better, like always having a tailwind or good legs. Going back to other wheelsets highlighted the difference for me. I wonder if this has provided an insight into how good wheels could be when unshackled from financial price point constrictions.
Not everyone can afford these wheels and I'm sure many will find the price slightly outrageous; they are amongst the most expensive available for bicycles right now. They do however offer fantastic performance and you can rest assured a great deal of care and attention has gone into their construction.